By Surbhi JainReviewed by Susha Cheriyedath, M.Sc.Mar 23 2022
In an article recently published in the journal ACS Applied Polymer Materials, researchers discussed the preparation of ultra-stiff 3D-printed molds with ultraviolet (UV)-curable and low-viscosity resin having a high silica filler content.
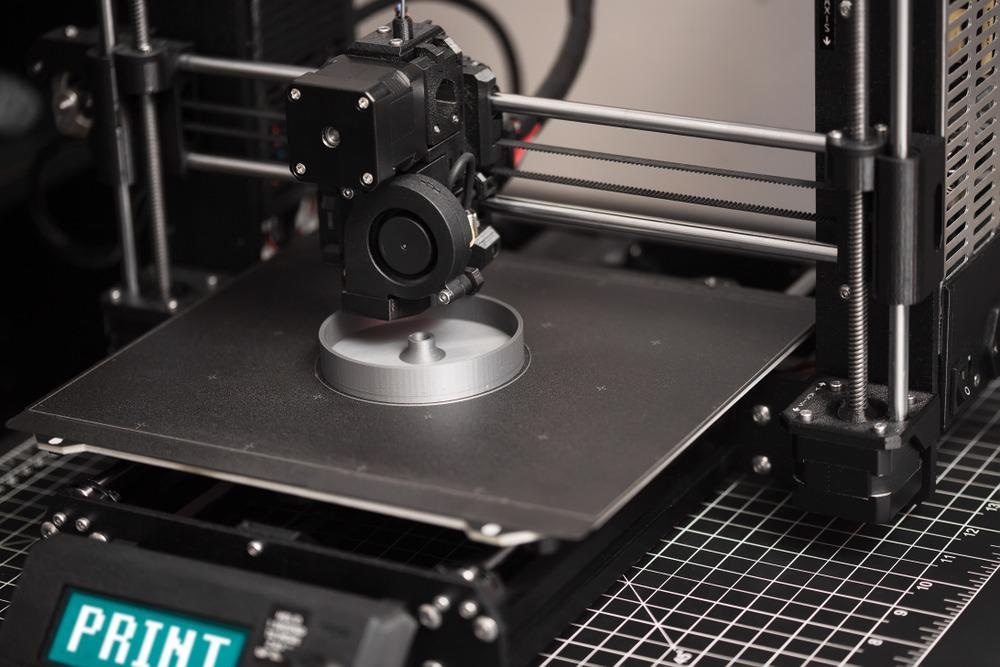
Study: Low-Viscosity Resin with a High Silica Filler Content for Preparing Ultra-stiff, 3D-Printed Molds. Image Credit: Marlon Lopez MMG1 Design/Shutterstock.com
Background
Due to its high accuracy and fast throughput, mold forming is one of the most valuable ways of plastic processing and engineering. Traditional subtractive processes for preparing molds are time-consuming and expensive. Researchers have actively sought the implementation of the concept of the conformal cooling channel into the preparation of molds with suitable cooling efficiency.
Sintering-based 3D printing has been utilized to build the rigid parts of 3D-printed molds successfully; however, the long-wave infrared laser and size of resin powders used in this technology produce molds with a coarse surface, which necessitates time-consuming post-processing such as sanding and wire-cutting.
Stereolithography (SL), an emerging three-dimensional (3D) printing process, has the potential to dramatically reduce mold manufacturing costs while still achieving mold accuracy standards. Nonetheless, the poor mechanical and thermal qualities of suitable resins limit the service life of printed molds, prohibiting their broad usage in industrial applications. In order to generate viable composite resins for 3D printing injection molds, silicon-based inorganic fillers such as silica dioxide, silicon carbide, and montmorillonite have been added into the polymer resin matrix.
Earlier research has shown that adding inorganic fillers to as-prepared resin composites enhances their viscosity exponentially. Moreover, the viscosity of composite resins has been shown to be strongly affected by the surface characteristics of the filler.
About the Study
In this study, the authors presented the utility of vaporized metal combustion (VMC) approach for the preparation of a UV-epoxy/micro-silica with high solid content and low viscosity, to make it acceptable for SL 3D printing. In addition, silica produced using sol-gel was used as a comparative. The stiffness (Young’s modulus) and thermal tolerance (heat deflection temperature) of the as-prepared samples from a laboratory-scaled SL 3D printer were determined.
The researchers used the VMC methodology to manufacture micro-sized silica with an exceptionally low specific surface area in order to overcome rheological problems. Both forms of the filler were investigated for their contributions to the efficacy of UV-curable resins in 3D printing. All of the test samples were created using a laboratory-scale SL 3D printer. Finally, as-prepared resin composites were used to prepare molds for injection molding and vacuum casting, and their service life and heat dissipation were thoroughly investigated.
The team utilized poly(ethylene terephthalate) (PET) film as a raw substance to create desired structures using vacuum thermoforming equipment and the molds made from the as-prepared resin. Since PET softens at around 80 °C, the mold was heated up to 140 °C to facilitate filling and enhance accuracy.
Observations
The prepared UV-epoxy/micro-silica had 60 wt% solid content and 1072 cps viscosity. It's Young's modulus and heat deflection temperature were estimated to be 9.72 GPa and 188 °C, respectively. The resin composites' high solid component ensured excellent rigidity. The produced teeth model was able to keep dimensional precision after being subjected to high-pressure and temperature conditions for 2 minutes, which allowed for easier and more exact preparation of a transparent teeth aligner.
More from AZoM: What is Localization Atomic Force Microscopy?
The resin composite was strengthened with 60% silica powder and had a low viscosity value of 1076 cps and good fluidity, which made it suitable for use with a commercial SL 3D printer. Among vat polymerization processes, the composite parts of cured resin had a high thermal conductivity value of 0.44 W m-1 K-1. As-prepared high rigidity composites could meet the material's precision requirements and service life for successful injection mold performance.
After 1000 continuous injection cycles, the fabricated mold maintained a stable structure, and injected parts maintained good precision, according to service life testing.
Conclusions
In conclusion, this study devised a method for fabricating customized molds using SL 3D printing of a modified UV-curable epoxy resin/silica composite. SL was found to be appropriate for the creation of a mold with an inside conformal cooling channel, which resulted in enhanced cooling efficiency.
The authors demonstrated that by combining materials and mold design, the service life of the as-prepared injection and vacuum casting mold could be significantly increased. The authors emphasized that this technique overcomes constraints in the characteristics of 3D-printed parts, allowing direct stereolithography printing of molds for use in both academic and industrial applications. They also believe that the approaches described in this study can allow a marketed stereolithography technology to be used to direct print the mold.
Disclaimer: The views expressed here are those of the author expressed in their private capacity and do not necessarily represent the views of AZoM.com Limited T/A AZoNetwork the owner and operator of this website. This disclaimer forms part of the Terms and conditions of use of this website.
Source:
Yang, Z., Peng, S., Wang, Z., et al. UV-Curable, Low-Viscosity Resin with a High Silica Filler Content for Preparing Ultra-stiff, 3D-Printed Molds. ACS Applied Polymer Materials (2022). https://pubs.acs.org/doi/10.1021/acsapm.1c01920