Currently in pre-proof in the journal Materials Letters, a study has been published which has reported chromium-based coatings with remarkable tribological properties, even in repeated-wear conditions.
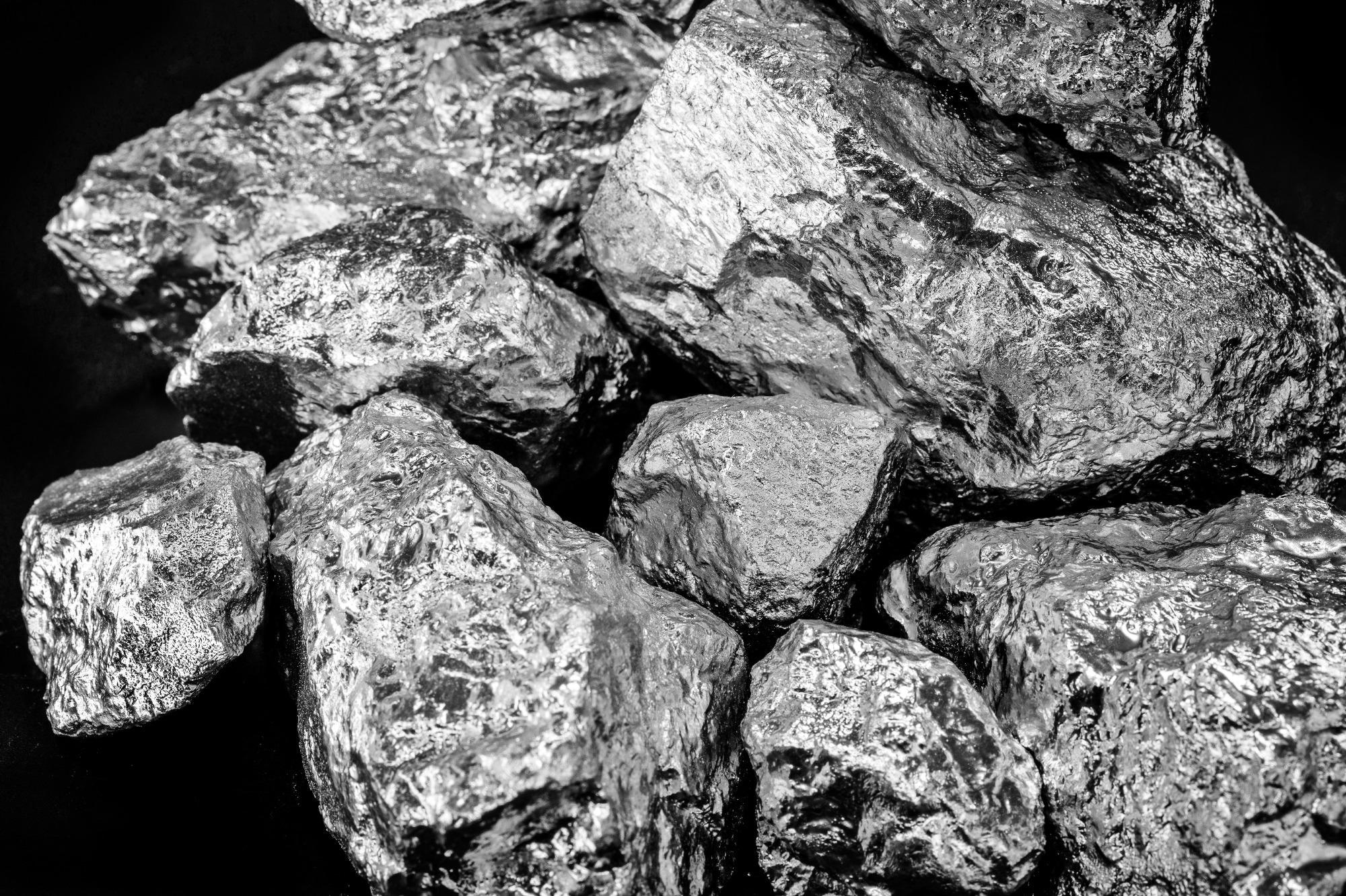
Study: Fantastic behavior of near-zero wear of Cr-based coatings. Image Credit: RHJPhtotos/Shutterstock.com
Super-Lubricity
Manufacturing materials with super-lubricity is a key concern for scientists working in fields such as material science and surface engineering. Coatings which can withstand repeated wear and still perform under extreme conditions are essential for numerous applications.
However, in these fields, research has been lacking on ultra-low or near-zero wear. This area of research is important as it could help to improve the reliability and service life of components and coatings under motion, which is important for engineering applications. Manufacturing coatings that can withstand physical motion and perform well for a long period of time is vital for the engineering industry.
Chromium-Based Coatings
Chromium is used in coatings for a wide variety of industrial applications. Coatings that include chromium as an ingredient have self-healing and protective properties. When water enters coatings after damage, for instance, chromium ions interact with it and form Cr2O3, preventing further damage and oxidation of the coated material.
Chromium-based coatings have been used to protect aluminum aircraft components, pipelines, storage tanks, offshore infrastructure, hulls on seafaring vessels, public transportation such as buses and trains, and civil infrastructures such as dams and bridges. These coatings confer superior corrosion resistance. Due to their superior properties, they have been proposed as coatings for components that undergo significant mechanical wear.
The Study
The study has explored the resistance of chromium coatings to repeated wear conditions. Three different coatings were investigated. Two CR(III) electrolyte and one CR(VI) electrolyte coatings were evaluated by the authors. Analytical grade reagents were used in the research. Subsequent heat treatment was employed.
The wear characteristics and short and long-term tribological properties of the three coatings were analyzed in the study. For electrodeposition of the coatings onto a steel substrate, the authors employed a graphite anode and a stainless steel disk cathode. Temperature and pH of the electrodeposition process were controlled (at 25 oC and ~1.5, respectively.)
A thick coating of chromium was deposited onto the substrate and then heat-treated at 180 oC for 2 hours. A microhardness tester was used to determine the Vickers hardness of the three coatings. A fretting friction tester was used by the authors to examine the tribological properties of the coatings. Oil was used as lubrication. This tester can simulate friction close to operating conditions.
More from AZoM: What is X-Ray Emission Spectroscopy?
After testing, a non-contact 3D surface profiler was used to evaluate the wear of the coatings, and SEM was used to analyze their worn surfaces. Volume-time curves revealed that there was sharp wear in the initial stages of friction for all coatings, with the curve flattening over time, demonstrating that all coatings during the later stages of testing exhibited near-zero wear. Therefore, the coatings exhibited superior wear resistance over time.
Previous work by the authors established the phase structures of chromium-based coatings. Even though the microstructure of each coating differs, sometimes to a significant degree, all three coatings analyzed in the study possess significant wear resistance. Very low wear and zero wear behaviors were observed in all samples.
Wear tracks were analyzed with scanning electron microscopy to further understand the wear characteristics of all three coatings. For each coating, the wear tracks displayed a similar uniform and flat morphology after entering the zero wear stage. All coatings displayed slight abrasive wear in the zero wear phase, which could be connected with the zero wear behaviors. Adhesive strength and bonding state for the three coatings were different, but the authors concluded that this did not affect the coating's zero wear behavior.
Conclusions of the Study
All three chromium-based coatings in the research displayed near-zero wear under tested conditions. The performance of the coatings was the same regardless of the preparation process and steps. In the zero wear stage, mild abrasive wear appears to be the dominant wear mechanism. Differences between the coatings were observed in both short-term and long-term wear conditions, with some coatings performing better, but this did not affect their behavior and performance.
The authors have concluded that near-zero wear is likely an intrinsic characteristic of chromium-based coatings, making them ideal for use in applications where wear resistance is a critical factor, such as engineering applications. They have stated that fully elucidating the mechanisms of this characteristic will require further research. The comparative analysis of different chromium-based coatings performed in the study provides a vital knowledge base for future research in the area.
Further Reading
Liang, A et al. (2022) Fantastic behavior of near zero wear of Cr-based coatings [online, pre-proof] Materials Letters 132228 | sciencedirect.com. Available at: https://www.sciencedirect.com/science/article/abs/pii/S0167577X2200581X
Disclaimer: The views expressed here are those of the author expressed in their private capacity and do not necessarily represent the views of AZoM.com Limited T/A AZoNetwork the owner and operator of this website. This disclaimer forms part of the Terms and conditions of use of this website.