Latvian scientists have reported the findings of structural integrity tests on aircraft parts produced using additive manufacturing. Writing in the journal Polymers, they have evaluated different structures, with their findings providing useful information for the future manufacture of parts used in the interior of aircraft.
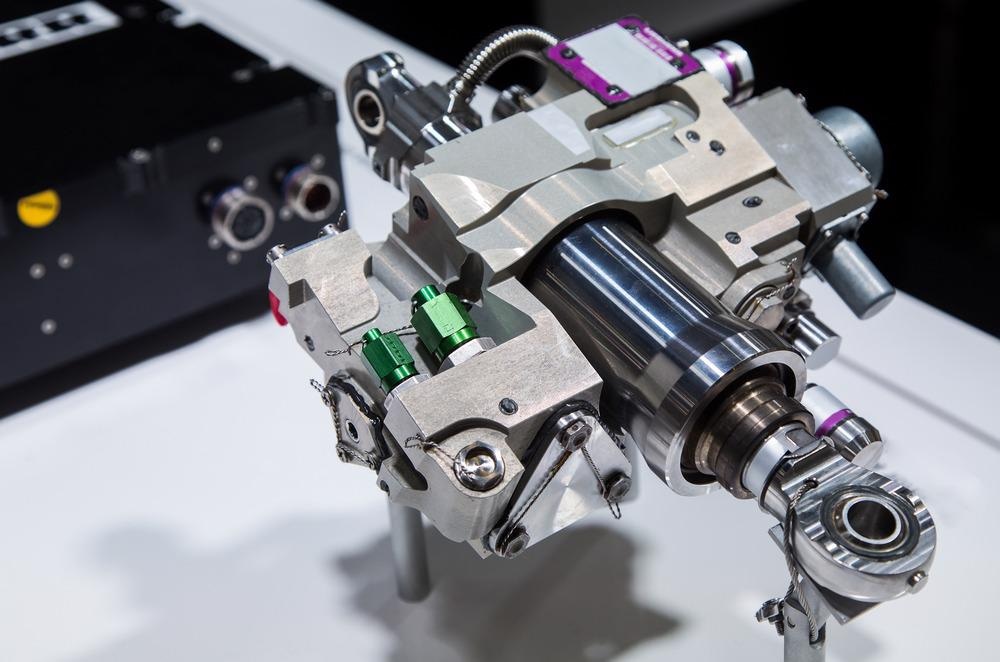
Study: Structural Integrity of the Aircraft Interior Spare Parts Produced by Additive Manufacturing. Image Credit: magicinfoto/Shutterstock.com
Developing Improved Aircraft Interiors
Air travel is a key transportation sector. Safety and efficiency are paramount concerns for aircraft companies, and for this reason, new components and materials are constantly being researched by scientists working in the aerospace industry and materials science.
Investment in cabin interiors, as well as retrofitting old aircraft, is an efficient and cost-effective strategy for airline companies to improve the consumer experience. Moreover, replacing conventional metallic materials with advanced polymers and composite materials offers the opportunity for weight reduction, improved fuel efficiency, and improved flight range of aircraft. Cost savings can be made by companies and safety during emergencies can be improved.
Printing directions for the class divider (a) and seat folding table (b). Image Credit: Kobenko, S et al., Polymers
To be considered for aircraft interiors, materials must not only meet aesthetic needs and reduce weight, but they must possess characteristics that meet stringent safety regulations. For instance, they must be fireproof and non-toxic and possess suitable mechanical properties. Amongst polymeric materials, thermoplastics such as PEI and PEEK have attracted interest due to flame, toxicity, and smoke resistance, their durability, and their easy manufacture.
The Paper
The paper’s aim is to demonstrate the feasibility of replacing conventional metallic parts with lighter, polymeric materials in aircraft interior applications. The suitability of additive manufacturing for the production of these materials is widely explored in the paper, and the authors have demonstrated that these materials keep the high strength to weight ratios demanded by aircraft interior applications.
The authors have noted that all materials used in aircraft interiors must meet stringent requirements for the specific aircraft type, and the minimum requirements depend on the aircraft’s airworthiness category and the standard applicable when the design was first certificated. The aircraft certification basis defines the minimum standard.
Ultem 9085, which is manufactured using fused deposition modeling, was analyzed in the research. This thermoplastic blend of PEEK and PEI has high thermal and chemical resistance, is flame resistant, and emits low levels of smoke when ignited. These properties make it a safe option for parts used in cabins. Two examples of aircraft interior components constructed out of this material were evaluated by the authors.
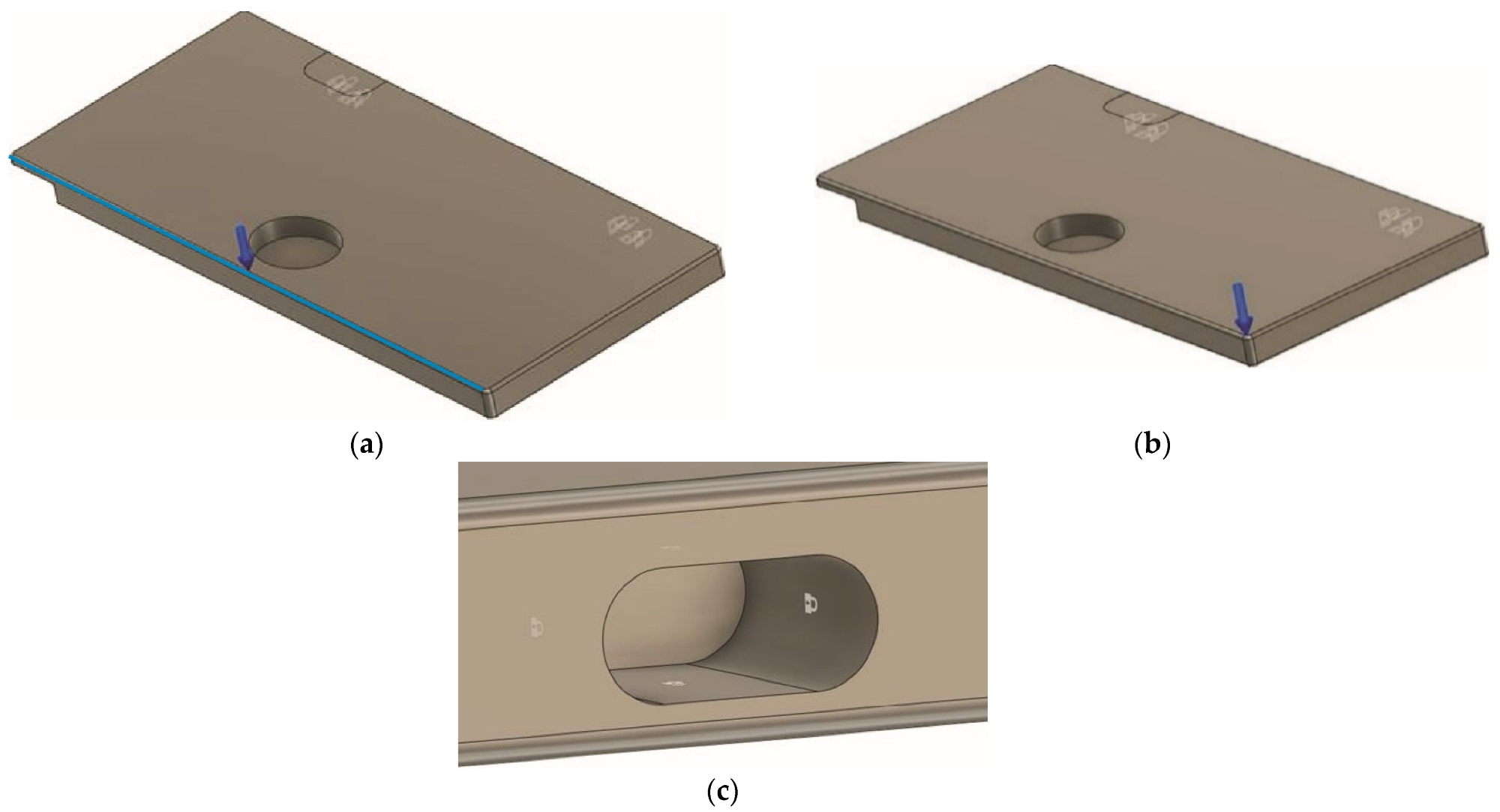
Load case 1 (a), 2 (b), and boundary conditions for the seat folding table (c). Image Credit: Kobenko, S et al., Polymers
Parts constructed from Ultem 9085 were evaluated alongside traditional aircraft interior components. Conventional parts were constructed using traditional manufacturing methods, whilst the proposed replacement parts were manufactured using fused deposition modeling. Minor design adjustments were conducted to meet current mechanical load requirements for certification.
Currently, the authors have stated, there are no similar studies on the structural integrity of parts produced from Ultem materials using additive manufacturing, which makes this research highly original. The two component designs evaluated in the research were class dividers and seat folding tables.
Results of the Research
Structural integrity and mechanical tests and numerical modeling were employed by the authors in order to evaluate the properties and performance of the FDM-printed Ultem components. Further design modifications of the components were made, which demonstrated a 17% weight reduction compared to the original design proposal. However, the authors noted that using FDM to manufacture this lighter design would be challenging, requiring further design iterations, but it does demonstrate there is room for improvement.
The authors have stated that using a simple, idealistic modeling approach can estimate the structural integrity of these parts. Results of the numerical modeling can be used for future physical tests on the printed aircraft interior parts.
Testing the class divider revealed the adequate performance of the printed part, with a lack of failure even under critical loads. The part can withstand maximal load without breaking, with a lack of residual deformations after horizontal and vertical tests.
The printed seat folding table can withstand loads of 900 N at the tip, and vertical pull-down tests demonstrated that the part could withstand maximal load without breaking, with a lack of deformation afterward. Furthermore, the authors identified that there was an opportunity for further optimization of the printed part.
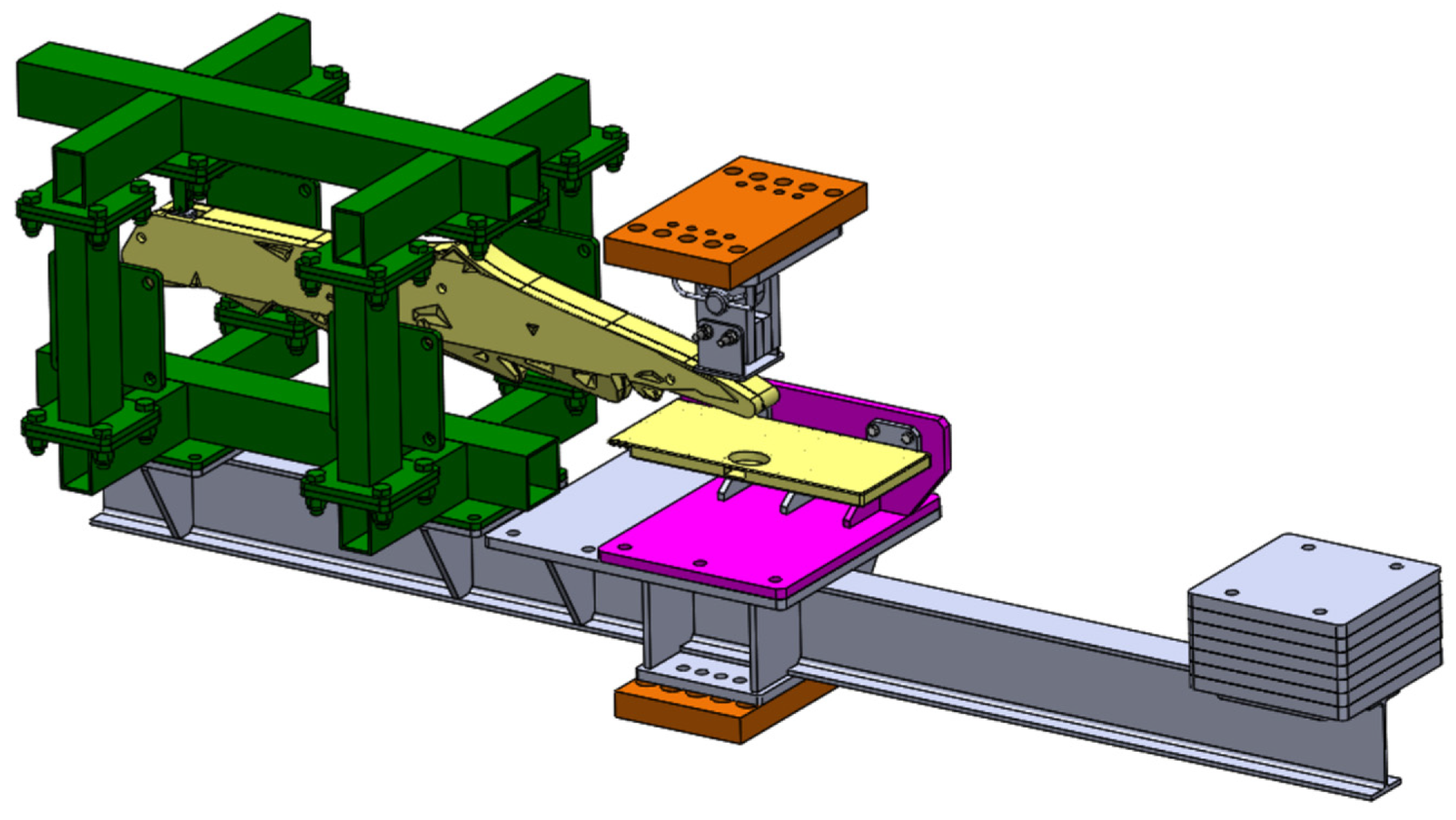
3D model for the manufactured test stand. Image Credit: Kobenko, S et al., Polymers
Whilst the authors have identified that further structural elements may be necessary for these non-engineering structures, the test results have demonstrated that additive manufacturing is suitable for replacing current manufacturing methods. This reduces the steps involved in constructing aircraft interior parts and, consequently, provides cost savings. Moreover, additive manufacturing reduces waste and allows a freer design form.
Overall, this paper has demonstrated that replacing conventional metal parts with FDM-manufactured polymer materials meets the stringent requirements of aircraft interior parts, and provides opportunities for weight reduction, increasing fuel efficiency, and reducing the CO2 emissions which the aerospace industry is responsible for.
Further Reading
Kobenko, S et al. (2022) Structural Integrity of the Aircraft Interior Spare Parts Produced by Additive Manufacturing [online] Polymers 14(8) 1538 | mdpi.com. Available at: https://www.mdpi.com/2073-4360/14/8/1538
Disclaimer: The views expressed here are those of the author expressed in their private capacity and do not necessarily represent the views of AZoM.com Limited T/A AZoNetwork the owner and operator of this website. This disclaimer forms part of the Terms and conditions of use of this website.