By Surbhi JainReviewed by Susha Cheriyedath, M.Sc.Apr 18 2022
In a review recently published in the open-access journal Materials, researchers discussed the reinforcement of waste alkaline battery epoxy composites with zinc oxide (ZnO).
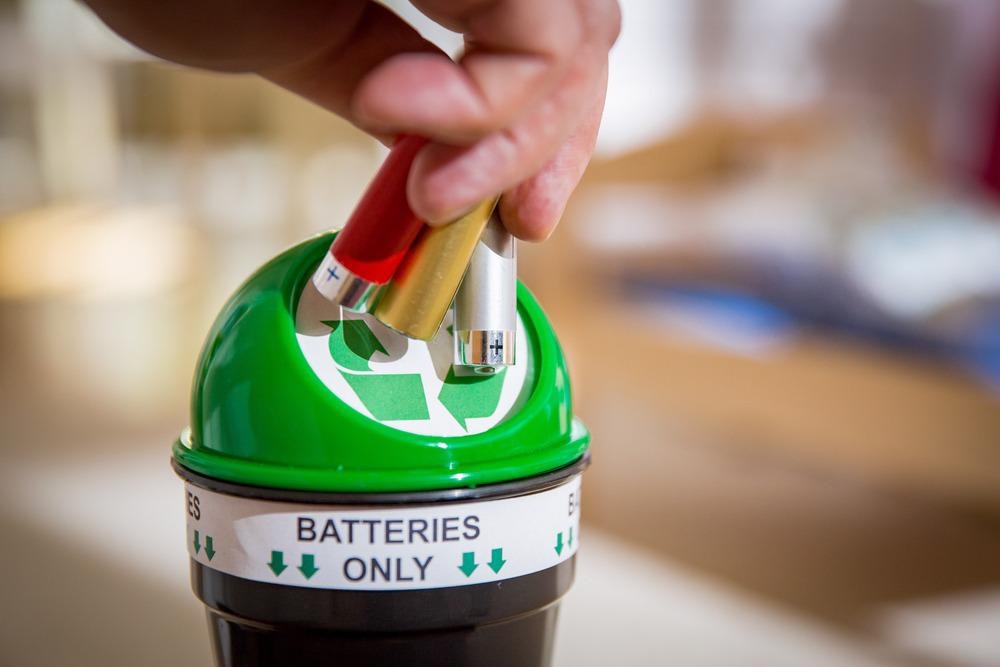
Study: Epoxy Composites Reinforced with ZnO from Waste Alkaline Batteries. Image Credit: Aleksandra Suzi/Shutterstock.com
Background
In today's world, battery recycling is a significant challenge. In addition to studying more effective recycling procedures for waste batteries, the use of their recycled materials for the manufacture of batteries and other new uses should be encouraged. ZnO is a fascinating material with a wide range of applications.
However, due to the closure of numerous mines and a lack of toxic and raw procedures to synthesize it, the production of ZnO particles is costly. As a result, making ZnO microparticles from waste is an intriguing and long-term option.
The use of fillers has a number of drawbacks, the most significant of which is the difficulty in dispersing them. The concept of producing nanoparticles in situ has recently been investigated, with promising findings in terms of dispersion. Nanocomposites with suitable properties can be made by incorporating ZnO fillers into a thermosetting matrix. Ceramic particle/epoxy composites are being used as coatings on the surface of neat epoxy thermosets and composites to reduce water absorption and improve surface mechanical performance in civil and defense buildings.
FEG-SEM micrographs of ceramic particles: (a) commercial TiO2, (b) commercial ZnO and (c) recycled ZnO. Image Credit: Lorero, I et al., Materials
About the Study
In this study, the authors proposed the utility of ZnO microparticles recovered from worn-out batteries as epoxy resin fillers. These nanocomposites were employed as pigments, protective coatings, and thermally stable structural composites. Several nanocomposites supplemented with recycled ZnO and commercial ZnO and TiO2 nanoparticles were created with various nanofiller proportions.
The researchers presented the development of ZnO particles by recycling old alkaline batteries and their application as fillers in epoxy coatings. The acquired results were compared to two other commercial ceramic oxide nanoparticles i.e., TiO2 and ZnO, in order to assess their effectiveness. The geometry and size of the ZnO particles were investigated. ZnO particles were mixed into epoxy thermosetting resins to achieve good thermal and mechanical performance.
The team filled various ceramic micro and nanoparticles based on ZnO and TiO2 into an aeronautical epoxy thermosetting resin. One of the ZnO particles was recycled from depleted alkaline batteries. Field Emission Gun Scanning Electron Microscopy (FEG-SEM) and Fourier Transform Infrared Spectroscopy (FTIR) were used to characterize the prepared nanoparticles. The potential benefits of recycled ZnO as fillers of an epoxy thermosetting resin, which was used as a matrix of composites manufactured by resin infusion techniques for aeronautical structures or as protective coatings were identified, and the performance of recycled ZnO in comparison to other expensive commercial ceramic nanoparticles was investigated.
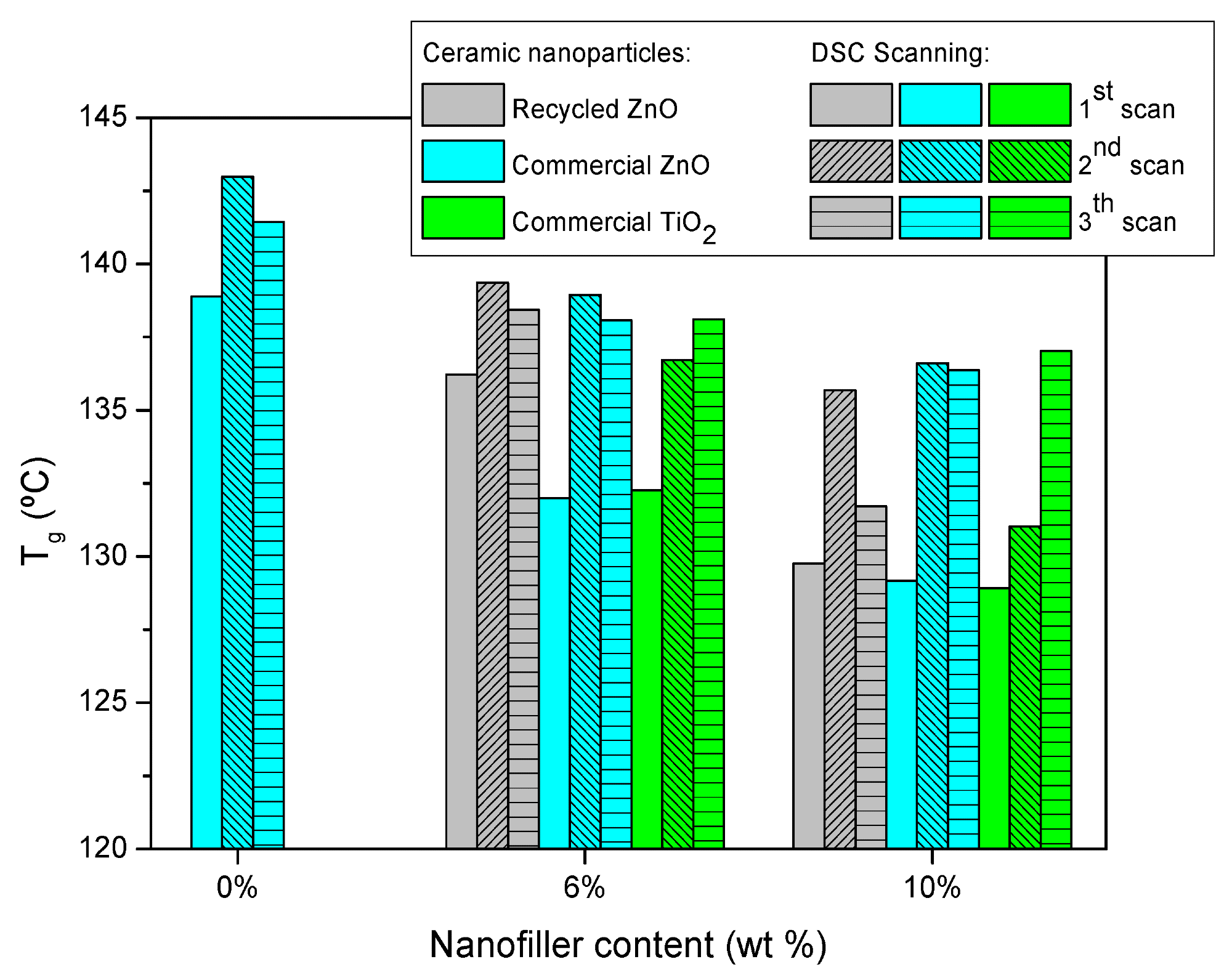
Glass transition temperature, measured by three consecutive DSC scans, for the studied epoxy composites reinforced with ceramic nanoparticles. Image Credit: Lorero, I et al., Materials
Observations
Non-treated epoxy thermoset had an average roughness of 1.30 ± 0.16 µm. In the region of 1.4–1.6 µm, the roughness increased slightly with the addition of ceramic particles. When the chemical etching treatment was performed on the composites' surface, their roughness increased dramatically in the region of 3.2–4.2 µm. Due to the improved effectiveness of scanning thermal curing, the initial Tg of neat epoxy resin was 139 °C and gradually climbed to 142°C for subsequent scans. Commercial ZnO nanoparticles were rectangular parallelepipeds with square base sides of less than 100 nm and a height of up to 500 nm.
Adding ceramic nanofillers, such as ZnO or/and TiO2, to epoxy resins improved their mechanical and thermal properties as well as their hydrophobicity and hardness, which were also dependent on a variety of circumstances. The morphology and size of fillers varied in addition to the various ceramic oxides.
Commercial TiO2 nanoparticles were smaller spherical nanoparticles. Recycled ZnO were "desert roses" such as microparticles. The use of ceramic fillers resulted in a minor rise in the glass transition temperature of <2%, as well as an improvement in the epoxy resin's barrier effect, resulting in a lowering of the water diffusion coefficient by <21% and simultaneously maintained the maximum water uptake. After the heat treatment, the nanocomposite water absorption was entirely reversible and restored its original thermomechanical behavior.
The water angle contact (WCA) increased by 12% when ceramic particles were present, but the highest hydrophobicity (35%) was achieved when the epoxy resin reinforced with recycled flowerlike ZnO microparticles was etched with acid stearic and acetic acid, which caused ZnO corrosion on the surface and thus an increase in surface roughness. The de lotus effect was enhanced by the presence of desert rose ZnO particles.
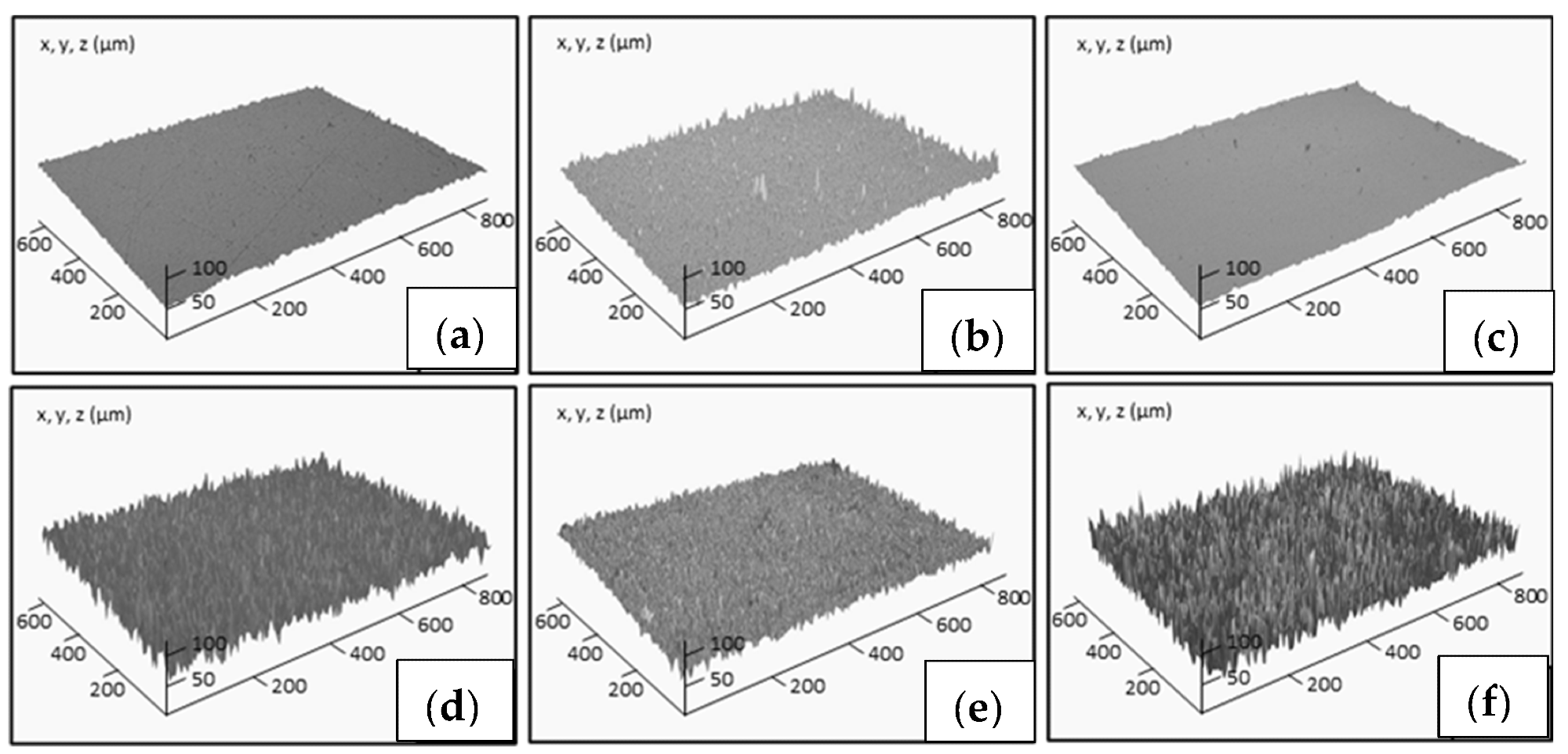
Surface profiles of non-treated surfaces of neat epoxy thermoset (a) and composites reinforced with 10 wt% commercial TiO2 (b) and commercial ZnO (c), and etched surfaces of nanocomposites with 6 wt% commercial TiO2 (d), commercial ZnO (e) and recycled ZnO (f). Image Credit: Lorero, I et al., Materials
Conclusions
In conclusion, this study elucidated that the use of the proposed ceramic fillers had a negligible impact on the thermoset's thermal strength and mechanical stiffness, as evaluated by Tg and storage modulus. Furthermore, the epoxy composites were found to have the same hydrothermal resilience as the neat epoxy thermoset.
The water diffusion coefficient was slightly reduced by the incorporation of ceramic oxide particles. The oxide ceramic particles enhanced the contact angle of a water drop, which allowed the examination of the surface hydrophobicity. This increase was more noticeable when the surface was chemically treated with stearic and acetic acids. Due to its maximum roughness, which was generated by the lotus effect and oxidation with acids related to its desert rose form, the composite reinforced with recycled ZnO particles had the highest WCA and, thus, hydrophobicity.
Disclaimer: The views expressed here are those of the author expressed in their private capacity and do not necessarily represent the views of AZoM.com Limited T/A AZoNetwork the owner and operator of this website. This disclaimer forms part of the Terms and conditions of use of this website.
Source:
Lorero, I., Campo, M., Arribas, C., et al. Epoxy Composites Reinforced with ZnO from Waste Alkaline Batteries. Materials 15(8) 2842 (2022). https://www.mdpi.com/1996-1944/15/8/2842