By Surbhi JainReviewed by Susha Cheriyedath, M.Sc.May 3 2022
In an article recently published in the journal Additive Manufacturing, researchers discussed the development of 3D printed poly (ether ether ketone) pieces with improved interlayer strength.
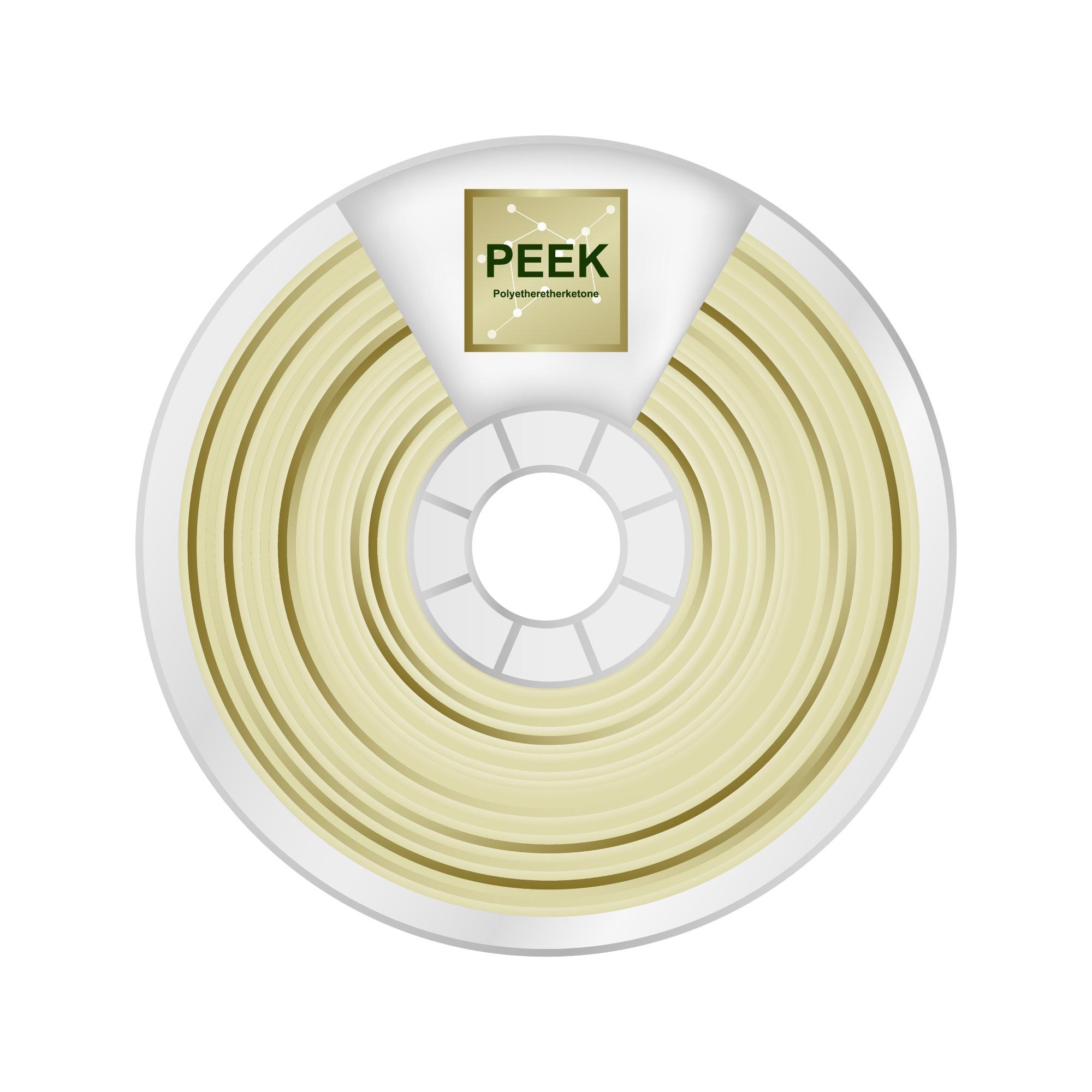
Study: Enhanced interlayer strength in 3D printed poly (ether ether ketone) parts. Image Credit: petrroudny43/Shutterstock.com
Background
3D printing, commonly known as additive manufacturing (AM), is a new type of manufacturing technology that is based on the notion of fast prototyping and has been widely used in a variety of fields. PEEK (polyether ether ketone) is a semi-crystalline thermoplastic material that has sparked great interest in 3D printing.
The direction with weak mechanical qualities determines the strength of the entire 3D printed part, severely limiting the parts' performance. Improving the Z-axis performance is the key to improving the performance of 3D printed items. In recent years, researchers have been attempting to boost interlayer strength.
Polymer blending, which has been widely utilized in industry and scientific research, has the advantages of large-scale manufacturing, ready-made industrial equipment and methods, and manageable development costs. Rarely has the mixing method of manufacturing PEEK filaments been documented in order to improve interlayer strength and reduce anisotropy.
About the Study
In this study, the authors discussed the utility of amorphous poly (aryl ether ketone) (aPAEK) as an interlayer reinforcement modification in 3D printed PEEK parts to improve the corresponding interlayer strength and reduce the mechanical anisotropy.
The researchers showed that the diffusion and entanglement of aPAEK between the layers were responsible for its enhanced performance characteristics. The obtained results vastly increased the mechanical characteristics of 3D printed PEEK parts and expanded their high-performance applications. By combining an amorphous polymer with semi-crystalline PEEK, a scalable and successful method for new filaments was developed.
The inter-layer strength was greatly enhanced with reduced mechanical anisotropy by incorporating the amorphous molecular chain's migration and diffusion. A variety of amorphous poly (aryl ether ketone) (aPAEK) with varied glass transition temperatures and strong compatibility with PEEK were synthesized, and melt blending was used to create aPAEK/PEEK mix filaments. The impact of various types of molecular weight, amorphous polymers, and amorphous polymer percentage on the performance of 3D printed objects was compared.
The team investigated the crystallization behavior, interlayer strength, rheological characteristics, and interlayer micromorphology of 3D printed aPAEK/PEEK blends to reveal the mechanism of interlayer enhancement in PEEK blends.
Observations
The tensile strength increased from 85.4 ± 3.3 MPa corresponding to 3D printed PEEK specimen to 88.1 ± 4.1 MPa corresponding to 3D printed 7 wt.% -DPAPEEK1/PEEK blends, which indicated that amorphous DPAPEEK1 facilitated filament bonding. The addition of a considerable amount of aPAEK reduced the inherent strength, which lowered the tensile strength of 3D printed 20 wt.% -DPAPEEK1/PEEK blends to 80.3 ± 2.2 MPa.
With the increment in the loading of DPAPEEK1 from 0 wt.% to 20 wt.%, the tensile strength corresponding to the X-axis of 3D printed DPAPEEK1/PEEK blends reduced from 95.4 ± 3.2 MPa to 87.3 ± 4.1 MPa, and the strain at the break incremented from 31.33 ± 3.45% to 102.11 ± 3.22%, which achieved a significant increment in the strain at break and simultaneously maintained a slight reduction in the strength.
The interlayer strength of 3D printed DPAPEEK1/PEEK blends improved from 13.4 ± 1.3 MPa to 35.2 ± 1.1 MPa, which was 2.7 times that of the 3D printed PEEK parts, and the strain at break was increased to 5.99 ± 0.1% compared to 1.75 ± 0.18%, which achieved simultaneous interlayer strength and toughness improvements. The interlayer strength of 3D printed 5 wt.% -DPAPEEK/PEEK blends increased from 13.3 ± 2.1 MPa to 23.4 ± 1.5 MPa and then declined to 19.2 ± 0.5 MPa as the molecular weight of DPAPEEK increased, while strain at break decreased from 5.36 ± 0.31% to 2.58 ± 0.33%.
The interlayer strength in 3D printed items incremented 130% from pure PEEK to aPAEK/PEEK blends when 7wt% aPAEK was added to PEEK filaments. The mechanical anisotropy in the XY plane was reduced to 1.1%, whereas the tensile strength in the X- and Y-axes was still 89.2 ± 3.3 MPa and 88.1 ± 4.1 MPa, respectively.
Conclusions
In conclusion, this study elucidated that the use of amorphous PAEK improves the interlayer strength and mechanical anisotropy of the 3D printed PEEK parts. When compared to pristine PEEK, aPAEK diffused between layers more easily during printing, which boosted interlayer strength. Because DPAPEEK1 had a reduced transition temperature and molecular weight, it had strong diffusivity while maintaining molecular chain entanglement strength between interlayers.
In addition, DPAPEEK1 improved the interlayer strength of the 3D printed DPAPEEK1/PEEK blends while lowering mechanical anisotropy in the X-Y plane. The shape of the tensile fracture cross-section corresponding to the Z-axis further confirmed the effective enhancement of interlayer fusion.
The authors emphasized that aPAEK can help improve the interlayer strength of the 3D printed PEEK pieces. Furthermore, they mentioned that aPAEK might be easily manufactured on a large scale using low-cost materials. They also believe that this study will provide new insight into the blending-based development strategy for additive manufacturing materials.
More from AZoM: What Multi-Analytical Techniques are Used to Assess Paintings?
Disclaimer: The views expressed here are those of the author expressed in their private capacity and do not necessarily represent the views of AZoM.com Limited T/A AZoNetwork the owner and operator of this website. This disclaimer forms part of the Terms and conditions of use of this website.
Source:
Xu, Q., Xu, W., Yang, Y., et al. Enhanced interlayer strength in 3D printed poly (ether ether ketone) parts. Additive Manufacturing 102852 (2022). https://www.sciencedirect.com/science/article/abs/pii/S2214860422002512