By Surbhi JainReviewed by Susha Cheriyedath, M.Sc.May 24 2022
In an article recently published in the journal Additive Manufacturing Letters, researchers discussed the utility of chemical etching stainless-steel spatters in extending powder lifetime in additive manufacturing.
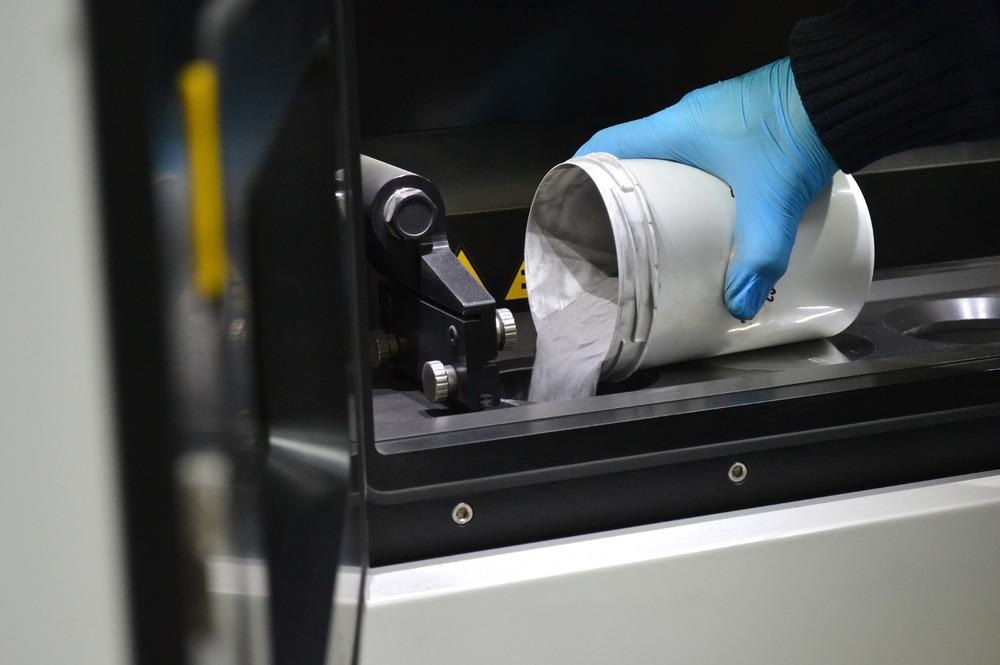
Study: Extending powder lifetime in additive manufacturing: chemical etching of stainless steel spatter. Image Credit: MarinaGrigorivna/Shutterstock.com
Background
Metal laser powder bed fusion (LPBF) produces spatter particles from molten droplets expelled from the melt pool or powder particles heated to near or beyond the melting point when they pass through the laser beam.
Despite the use of an inert environment, the high reactivity of metals near their melt temperature promotes oxidation. Although the ejected spatter particles are molten at least at the surface for a brief duration during LPBF, it is probable that diffusion of volatile elements toward the surface occurs, and these elements with a high affinity for oxygen create thick oxide layers.
Because the partial pressures of oxygen in LPBF are often higher than in gas atomization, the possibility of bonding with oxygen is increased.
Stainless steel and nickel-based alloy spatter is well known for oxidizing quickly, forming islands with a thickness of up to a few meters. Furthermore, stainless steels and nickel-based alloys, such as those that produce island-type oxide spatters, are far more commonly processed materials in LPBF, and it is critical that this approach be applied to more typical LPBF metal spatters to demonstrate the chemical renewal of powder in a generic manner.
(a) SEM image of stainless steel spatter particle, (b) experimental approach of heated chemical etching, (c) LPBF processing of de-oxidised spatter particles. Image Credit: Murray, J. W et al., Additive Manufacturing Letters
About the Study
In this study, the authors employed a novel chemical etching technique to remove oxides from the surface of oxidized stainless steel spatter powder. The dissolving of the metal surrounding and beneath oxide islands on the powder was used as the primary mechanism for oxide removal, which allowed for more aggressive oxide removal. Spatter, etched, and virgin powders were sieved to the same powder size range for LPBF processing.
The team showed how to remove oxides from stainless steel spatter particles, specifically those that segregate to create Si- and Mn-rich oxide islands on the powder surface by using a chemical technique. 316L spatter was collected from the powder bed of LPBF prints and chemically etched by submersion. After sifting all of the particles to the same size range, LPBF treated them in single tracks, along with the optimally etched splatter and virgin stainless steel.
The researchers studied temperature as well as two different stainless-steel etchants. After sifting to an equal size range, LPBF single tracks were created by utilizing an analogous virgin powder, spatter powder, and effectively etched spatter powder.
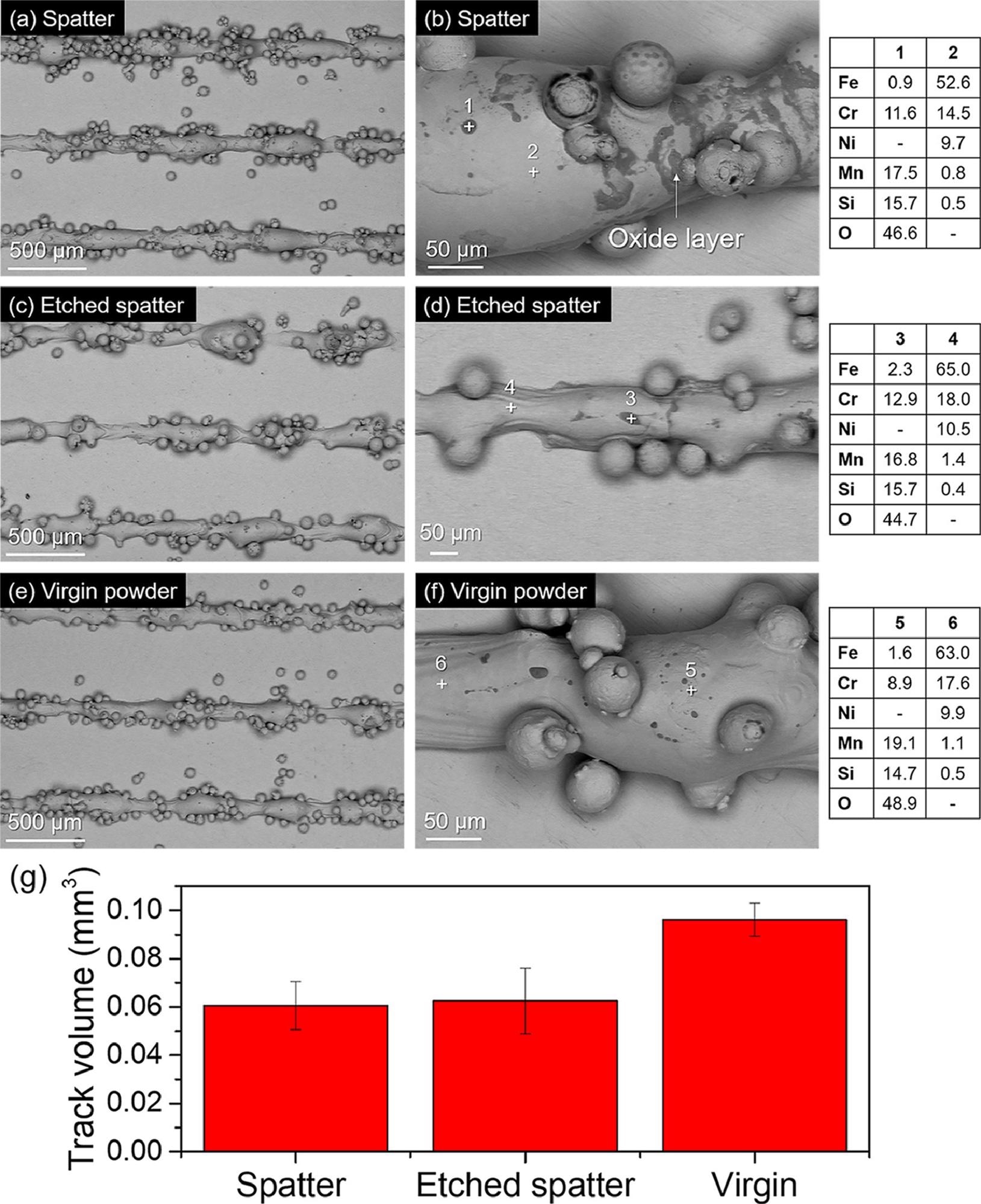
Single LPBF tracks generated from spatter, etched spatter and virgin powder. High magnification images reveal oxide layer prevalent on spatter tracks is somewhat eliminated on the etched spatter tracks. Virgin powder is shown to still exhibit some oxide presence. Image Credit: Murray, J. W et al., Additive Manufacturing Letters
Observations
Ralph's reagent, heated to 65 °C in a water bath for 1 hour, resulted in a 10-fold reduction in area coverage of the oxides on the 316L stainless steel spatter powder, from 7% to 0.7%. Through large-area mapping, EDX data revealed a reduction in the presence of oxygen from 13.5% to 4.5%.
When compared to spatter, etched spatter had a lower oxide slag coating on track surfaces. Furthermore, the chemical etching of the powder increased the powder's assimilation onto tracks. Chemical etching had the potential to boost the reusability and durability of spatter or heavily used powder made from widely used and corrosion-resistant stainless-steel powder.
The remaining agglomeration particles among both the etched and unetched spatter powders throughout the 45-63 µm sieved size range explained why track volumes of both etched spatter powder and spatter were similar, whereas virgin powder was about 50% greater by volume. Powders that were agglomerated or satellited were observed to affect packing density and thus track volume.
When compared to spatter, etched spatter had a lower oxide slag coating on track surfaces. When oxides were chemically removed, semi-incorporated, and denuded powder demonstrated evidence of better incorporation of reduced oxides, which was attributed to better wetting.
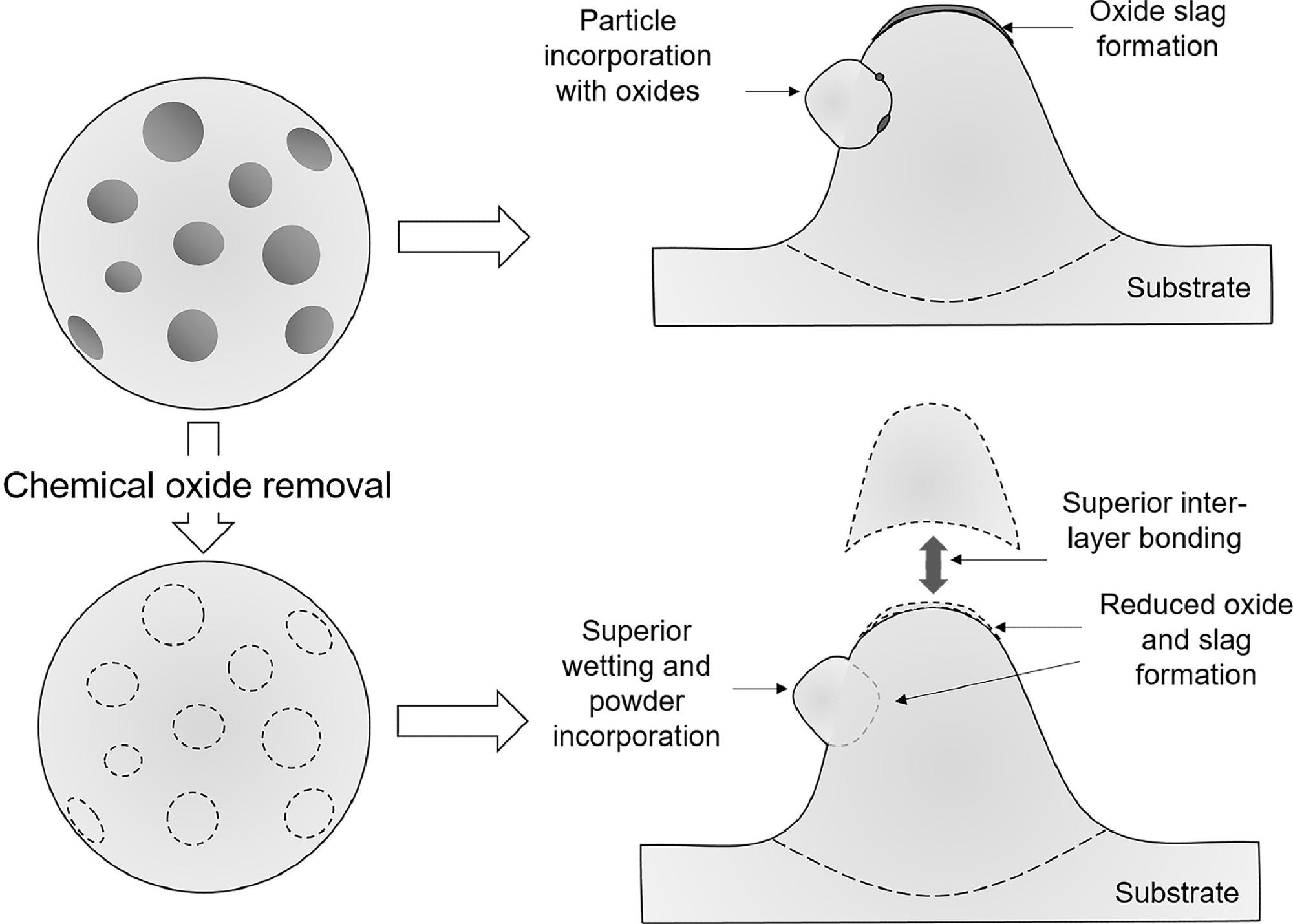
Schematic showing benefits to LPBF processing when oxides are chemically removed from spatter powder for the stainless steel system. Superior wetting is enabled via oxide elimination. Image Credit: Murray, J. W et al., Additive Manufacturing Letters
Conclusions
In conclusion, this study used a chemical etching procedure to chemically rejuvenate highly oxidized stainless steel spatter powder with submersion in Ralph's reagent, which is a solution of iron and copper chlorides in hydrochloric acid. Submersion in a solution of heated Ralph's etchant for one hour was observed to result in a 10-fold reduction in oxide area coverage on spatter powder.
The authors believe that chemical etching has the potential to be improved and employed on a wider scale to refresh spatter particles or LPBF powder that has been reused numerous times, hence increasing the value of the expensive powder-type materials.
Disclaimer: The views expressed here are those of the author expressed in their private capacity and do not necessarily represent the views of AZoM.com Limited T/A AZoNetwork the owner and operator of this website. This disclaimer forms part of the Terms and conditions of use of this website.
Source:
Murray, J. W., Speidel, A., Spierings, A., et al. Extending powder lifetime in additive manufacturing: chemical etching of stainless steel spatter. Additive Manufacturing Letters 100057 (2022). https://www.sciencedirect.com/science/article/pii/S2772369022000317