Scientists from the University of Kwazulu-Natal, the University of Witwatersrand, and Icarus Avionics in South Africa have collaborated on a new paper published online in the journal Energies investigating strategies for reducing the starting current in motors.
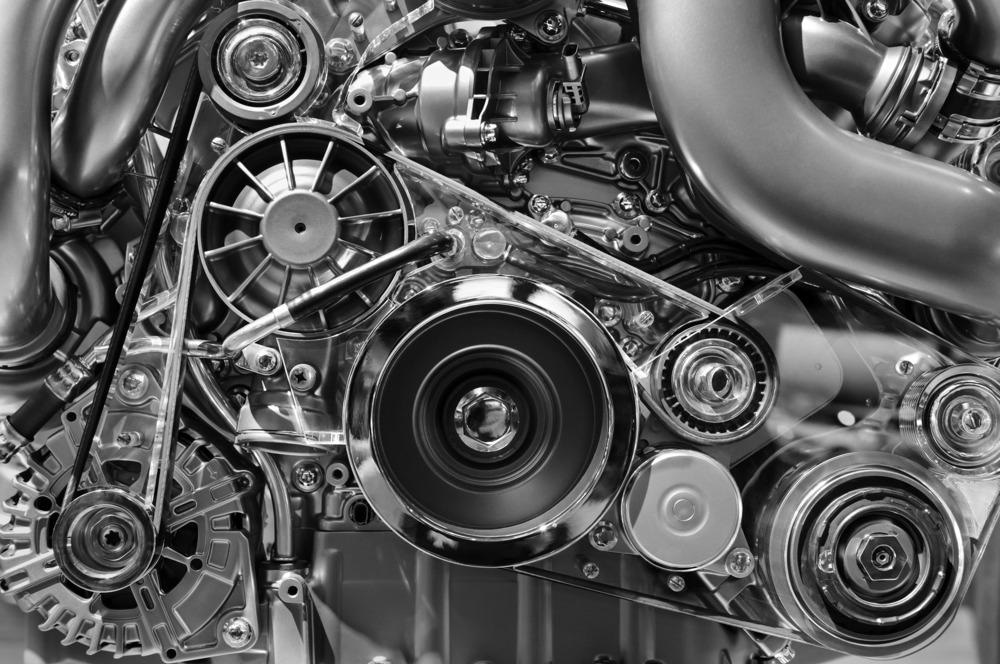
Study: Reduction of Starting Current in Large Induction Motors. Image Credit: AMatveev/Shutterstock.com
Motor Starting Currents
High inrush and run-up currents during starting is a challenge when designing large induction motors. High start-up currents can cause problems such as voltage dipping below acceptable levels and system stability issues in weak supplies. Capacity can be pulled down below the maximum levels in islanded systems.
Excessive current can be drawn during switch-on surges. Unnecessary tripping can occur in protection relays, other connected components can malfunction, and weak grids can become destabilized. Large inrush currents occur in several devices such as induction motors and transformers. Moreover, surges occur in large electromagnetic devices when they are switched on to induce the magnetic field.
In directly connected induction motors, a magnetic field is formed when voltage is applied on start-up. After this initial magnetization surge, a high run-up current occurs. When machines are running up to speed, between five and ten times the full-load current can be drawn. If this is not mitigated, overloading can occur in extreme cases, leading to the system tripping.
DSTATCOM induction motor starting. Image Credit: Habyarimana, M et al., Energies
Improving the Performance of Induction Motors
Induction motors are analogous to transformers. Because they are electromagnetic devices, induction motors draw both active and reactive power. If there is a high inductive loading, this can lead to power quality issues. One common strategy to mitigate poor power factors is to use capacitor compensation. This is achieved by connecting parallel capacitors to compensate for power loads.
Using capacitors is not a new practice. For decades, they have been utilized in single-phase induction motors. When in series with auxiliary winding, capacitors can be used during both start-up and when the device is running. Studies have reported boosted starting voltage outputs using electronic control both in parallel and in series. However, potential over-voltage can be caused, which has implications for system performance.
Parallel capacitor compensation during start-up has not been widely investigated in the current literature. Large induction motors are extremely inductive during start-up, and supplying reactive power to these systems may be more effective than supplying energy from the grid.
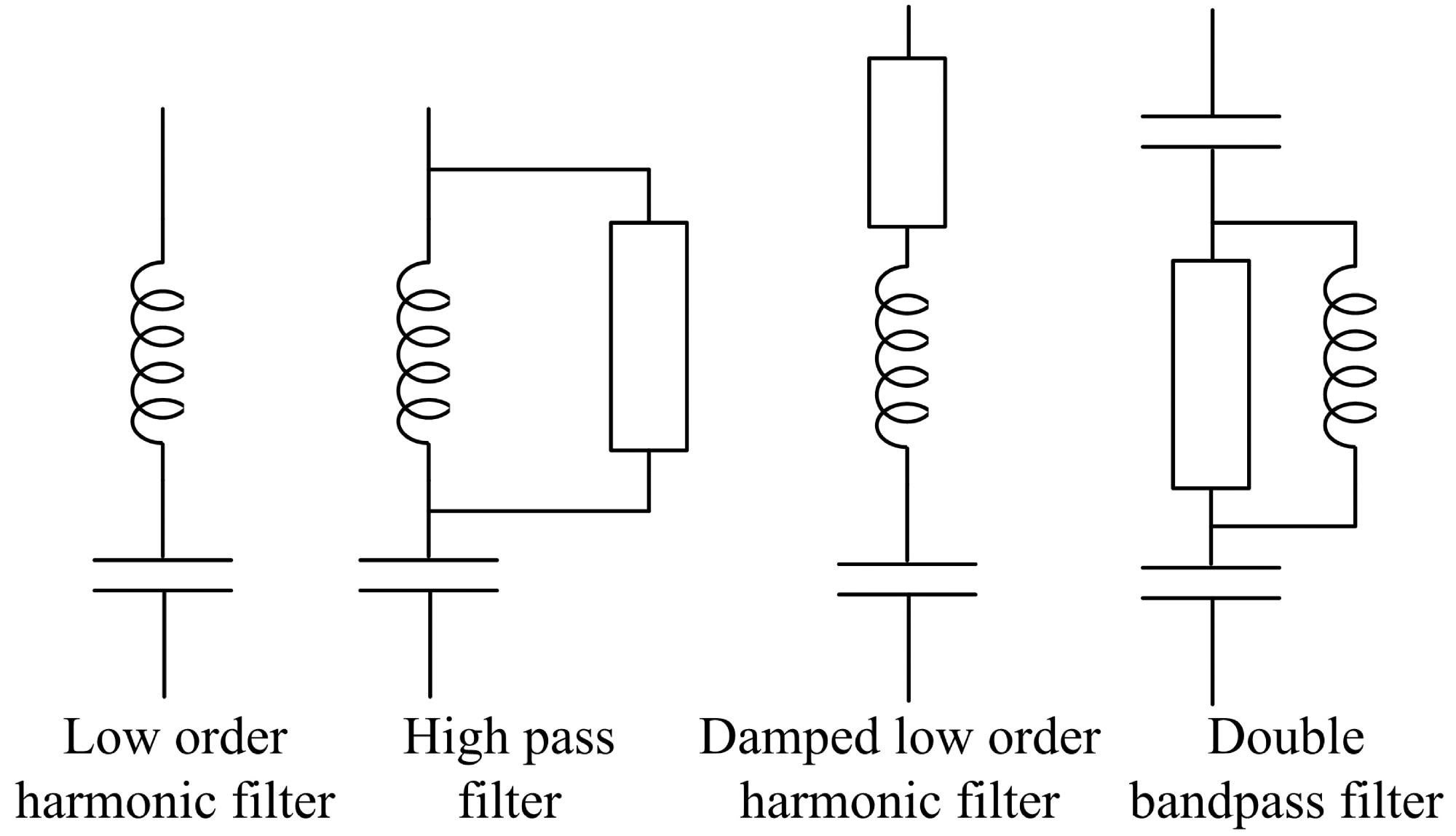
Possible filter arrangements—low pass filter most suitable in this application. Image Credit: Habyarimana, M et al., Energies
The Study
The paper in Energies has evaluated the use of parallel capacitors for reducing starting currents in induction motors. Several motors of increasing size have been assessed for their compensation requirements in terms of reactive power requirements during start-up.
The authors have highlighted that inverters can be used in smaller devices, converting them to variable speed drives and reducing the starting current. Unfortunately, this strategy can be too expensive for larger induction motors.
Increasing complexity and power demands leads to rapidly increasing costs that do not correlate with power ratings in a linear fashion, making them prohibitive for devices that operate in megawatts. The dominance of reactive power absorption in larger induction motor starting cycles means it is possible to compensate for starting currents using capacitors that generate reactive power.
Private discussions with an electrical contractor highlighted the practical problem of temporary voltage drops caused by sudden high currents during start-up in induction motors in large systems such as air-conditioning fans, water pumping stations, and motors at the end of long feed lines. The problem occurs not just at motor terminals, but over the entire power bus which feeds the starter motor.
Results of the author’s investigation of several induction motors demonstrated that as they become larger, they become more inductive. Simulations were employed to analyze the current reduction capabilities of connecting capacitors to these systems.
To test the concept, the authors employed a small experimental motor during their experiments. To increase its induction and mimic a much larger system, several series inductors were incorporated into the test system. The research’s proposed method was confirmed using experimental analysis.
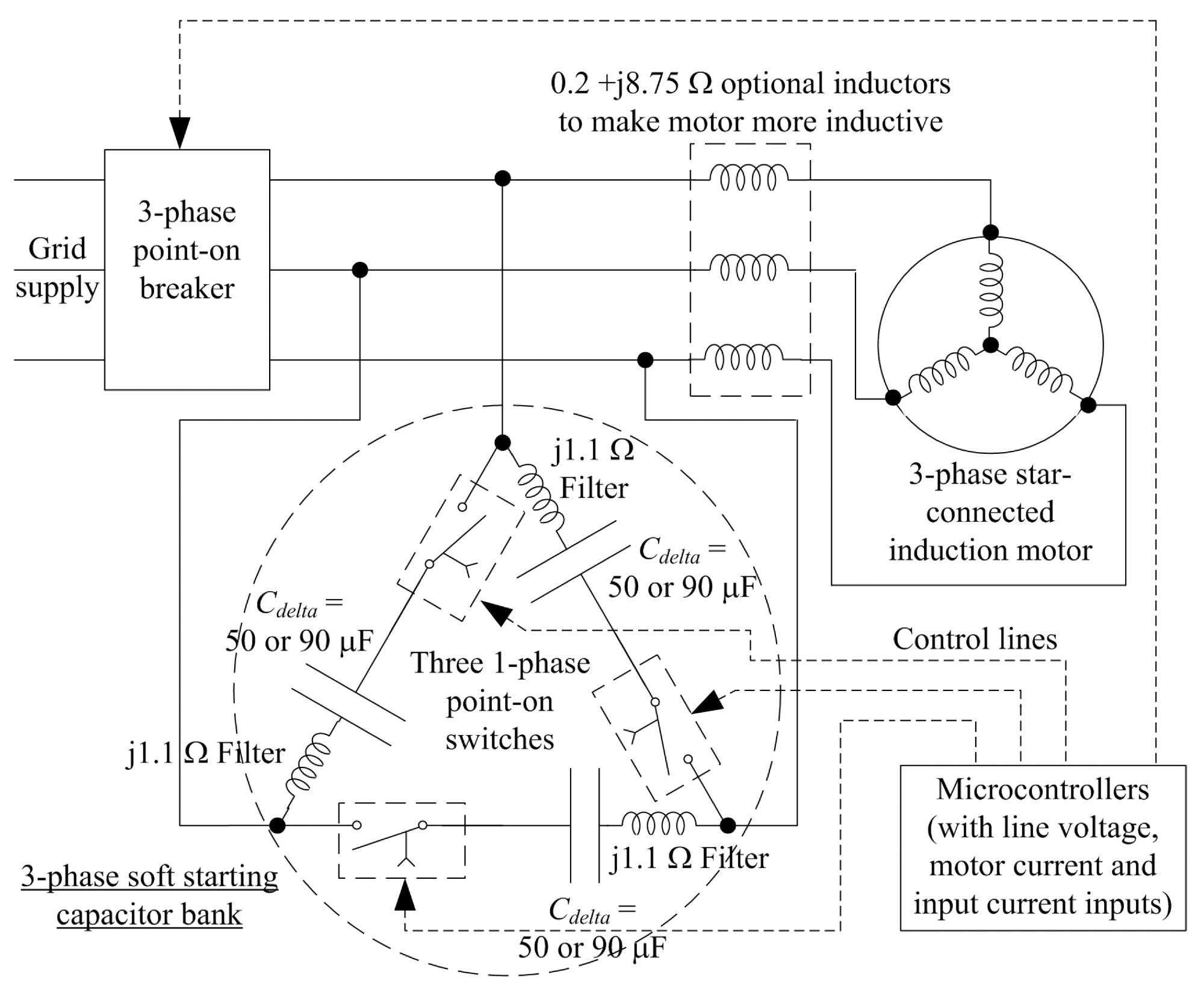
Complete system power circuit. Image Credit: Habyarimana, M et al., Energies
Reducing the harmonics of systems was also investigated in the research. Systems can be susceptible to low-frequency harmonics, requiring the use of filters. The authors proposed using in-line inductors in conjunction with capacitors. It was demonstrated experimentally that this considerably reduced run-up current harmonics, in line with simulations.
Another strategy explored in the paper was point-on switching. It was demonstrated that utilizing this approach reduces transient effects during turn-on. This method possesses the advantage of allowing soft connection of equipment.
The authors have stated that future work will investigate the possibility of constructing commercial devices which possess full capacitor turn-on and turn-off capabilities.
Further Reading
Habyarimana, M, Dorrell, D.G & Musumpuka, R (2022) Reduction of Starting Current in Large Induction Motors Energies 15(10) 3848 [online] mdpi.com. Available at: https://www.mdpi.com/1996-1073/15/10/3848
Disclaimer: The views expressed here are those of the author expressed in their private capacity and do not necessarily represent the views of AZoM.com Limited T/A AZoNetwork the owner and operator of this website. This disclaimer forms part of the Terms and conditions of use of this website.