By Surbhi JainReviewed by Susha Cheriyedath, M.Sc.May 30 2022
In an article recently published in the journal Additive Manufacturing, researchers discussed analytical thermoelastic solutions for additive manufacturing processes.
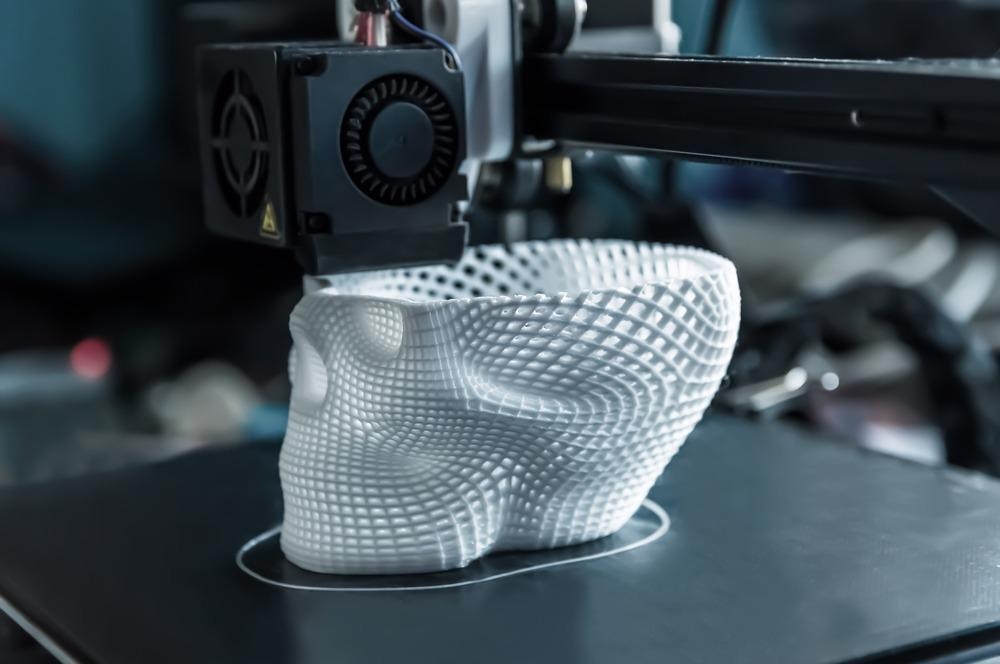
Study: Analytical thermoelastic solutions for additive manufacturing processes. Image Credit: Olga Ilina/Shutterstock.com
Background
The ability to precisely and efficiently model and manage many parts of the process is a crucial component of the characterization, design, and certification of components produced by additive manufacturing (AM) techniques. Analytical solution modeling is appealing because of its great computational efficiency and ease of use, as well as the ability to build a direct analytical relationship between input and output parameters.
Parallel to the advancement of various AM processes, great progress has been made in computational modeling of the multiphysics associated with them at various scales. The vast bulk of study has concentrated on finite element approaches (FEM) and particle-based methods due to the complexity of both the multiphysics problem and the relevant domains.
Under the assumption of minimal inertial terms, the thermo-mechanical response of elastic solids can be described by the solution of two coupled partial differential equations (PDEs). Extensive tabulated sets of accurate Green's function for the heat conduction equation may be found in several bibliographic sources. The enriched analytical solution method (EASM) has recently been offered as a way to create a generic thermal analytical solution that can eliminate several of its core assumptions.
The use of analytical solutions to tackle quasi-static thermomechanical issues involving moving heat sources has been the subject of extensive research. Eigenstrains, which are defined as any non-elastic stresses such as inelastic deformation, thermal expansion, or phase transformation strains, are one of the most well-known techniques.
About the Study
In this study, the authors presented an analytical model for computing time-dependent three-dimensional (3D) thermo-mechanical field distributions for heat deposition and AM challenges. The strain, displacement, and stress fields produced by a moving heat flux in the thermally conducting and mechanically deforming objects were determined. The problem was solved by using a one-way coupled technique, in which temperature fields calculated analytically by solving the heat transport problem were used as inputs for solving the solid mechanics problem analytically.
The team handled the heat transfer problem by using the recently created EASM, which was used to evaluate the spatiotemporal distribution of temperature fields created during AM operations. A non-uniform thermal eigenstrain field was utilized in conjunction with Green's function for the half-space to derive the corresponding elastic fields. For the case of a single-track laser powder bed fusion application, the analytical results of the elastic fields were compared to those produced via finite element analysis.
The researchers discussed three different methods for the evaluation of the elastic fields. The first method was used to solve the heat transmission differential equation and used thermal eigenstrains to add temperature effects on elastic fields. The second and third techniques were based on stationary thermoelasticity extensions of the work reciprocity theorem.
The second approach, in particular, was based on the reciprocity of work theorem for dynamic situations. The third method used a generalization of Maysel's technique based on Poisson-type integral formulas to solve the Lamé equations directly. The primary goal was to combine the thermal EASM with an elastic analytical model in order to calculate strain, 3D displacement, and stress fields in thermally conducting structures due to a moving heat flux.
Observations
Except for t = 0, when the two models had zero values, the analytical model replicated the FEM result, which resulted in a high relative difference error. The relative difference error was substantial during the time span of 0.25 seconds because the third displacement component (u3) had an asymptotic variation up to 0.15 seconds.
The results show that the proposed analytical model accurately matched the structural response computed using finite elements. Because the analytical model predicted the structural response of semi-infinite finite domains, it was inferred that the proposed model could be utilized to estimate the structural response of semi-infinite finite domains.
Conclusions
In conclusion, this study presented an analytical model for calculating strain, 3D displacement, and stress fields in thermally conducting objects due to a moving heat source. The heat transfer was first solved using EASM, which offered the thermal field due to a moving heat source. The temperature field was used as an input, and the 3D elastic fields were evaluated using three methodologies. For the case of a single-track laser powder bed fusion application, the analytical predictions of the elastic fields were compared to those produced via finite element analysis.
The authors emphasized that more work is needed to improve the applicability of the solution for scenarios with finite boundaries and severe nonlinear fluctuations in material properties due to temperature dependency. They believe that plasticity and phase transition along with more complex material models will be researched in the future.
More from AZoM: Use and Applications of Flame Atomic Absorption Spectroscopy
Disclaimer: The views expressed here are those of the author expressed in their private capacity and do not necessarily represent the views of AZoM.com Limited T/A AZoNetwork the owner and operator of this website. This disclaimer forms part of the Terms and conditions of use of this website.
Source:
Apetre, N. A., Michopoulos, J. G., Steuben, J. C., et al. Analytical thermoelastic solutions for additive manufacturing processes. Additive Manufacturing 102892 (2022). https://www.sciencedirect.com/science/article/abs/pii/S2214860422002901