By Surbhi JainReviewed by Susha Cheriyedath, M.Sc.May 31 2022
In an article recently published in the journal Additive Manufacturing, researchers presented a simulation of shrinkage during the sintering of additively manufactured silica green bodies.
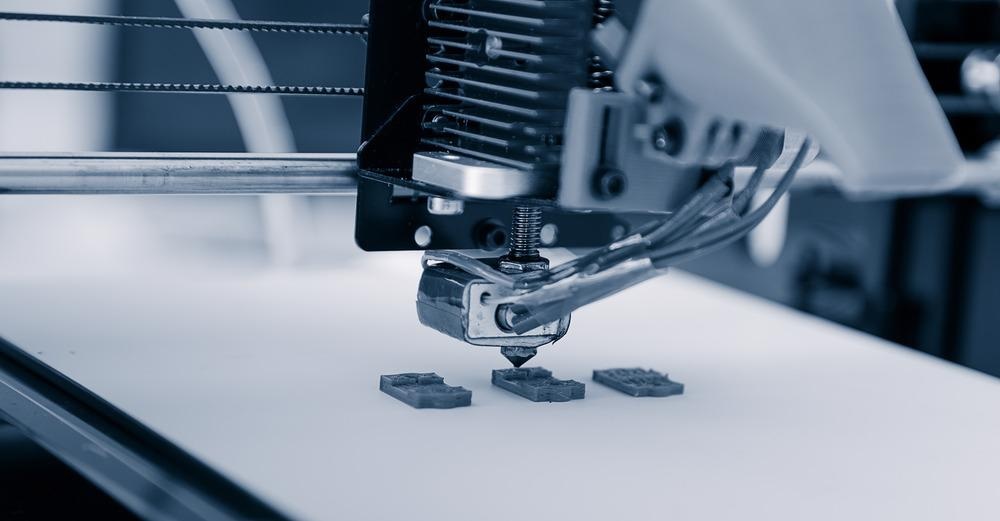
Study: Simulation of Shrinkage during Sintering of Additively Manufactured Silica Green Bodies. Image Credit: Alex_Traksel/Shutterstock.com
Background
Due to the limits and costs of mold tools, as well as time-consuming shaping procedures, the design of complicated high-temperature components with ceramics is constrained. These constraints are overcome by additive manufacturing (AM), often known as three-dimensional (3D) printing. The microstructure and mechanical properties of the final ceramic part are determined by the shape and densification of a green body.
Estimating shrinkage and distortion that occurs during the densification process can aid in planning the green body geometry precisely and decreasing post-processing of the corresponding parts to bring them to required dimensional tolerances. For metals and ceramics, the Skorohod-Olevsky phenomenological model of viscous sintering (SOVS) is extensively employed. For all AM feedstocks, no sintering model parameters have been determined.
To aid in the design and development of green bodies that could lead to dimensionally precise ceramic parts, computational methods for calculating relative density, shrinkage coefficients, and stresses associated with sintering for complex geometries need to be further developed. The three-dimensional finite element method (FEM) can simulate and anticipate process-dependent geometry changes.
Currently, the green bodies are sized using empirical scale factors that are responsible for projected shrinking during the steps of the process. Accurate process models and simulations open the path for the automated production of any final part design using green body shape/size synthesis.
About the Study
In this study, the authors implemented the SOVS model as a user-defined creep model in a 3D finite element program. The SOVS model's parameters, such as surface energy and viscosity, were calibrated by reducing the difference between experimental and anticipated relative densities. The parameters were determined by defining an error measure and utilizing the differential evolution global optimization to minimize the error.
The team investigated the dimensional changes of additively built green bodies during the sintering and polymer burn-off processes. The time-temperature cycles often employed to manufacture ceramic pieces from their green bodies were utilized to track density changes. The distortion and volumetric change during the sintering of the 3D printed ceramics were predicted by the SOVS sintering model, which allowed engineers to design geometries of the final parts and derive automatically produced green bodies.
The researchers designed a cylinder with a height and radius of 5 mm which was subjected to gravity and thermal loads to calibrate the material constants for the SOVS free sintering model. The relative changes in the density were simulated using the commercial FEA software, Simulia, and the axisymmetric finite element model. The SOVS model was implemented using a user-defined creep subroutine, and the time-dependent displacement fields were generated using viscoplastic analysis. The volumetric shrinkage was calculated by measuring the component dimensions.
Observations
When the temperature exceeded 1000 °C, the shrinkage strains predicted by the sintering model facilitated the evolution of the stresses. At the part's outer radius, the Von-mises stress was estimated to be in the range between 4.2 and 12.28 MPa. For the circular disc and rectangular plate specimen geometries, linear shrinkages of 21.7% in the x-direction and 25.91% in the y-direction were calculated.
During the heating process of the green body, the overall weight loss was roughly 34%. The phase change of silica from quartz to cristobalite induced cracking as the sintering temperature increased over 1250 °C.
Due to the decreased concentration of ceramic particles between layers and across print roadways, 3D-printed components were shrunk more along the printing axis than in other directions. As a result, proper shape deformation fields must be applied, and the print direction should also be considered along with the topology of the part, such as internal stress distributions. Green body geometries that yielded the necessary final sintered ceramic geometries could be produced by utilizing inverse optimization problem solution techniques that employed the proposed model.
Conclusions
In conclusion, this study elucidated the development of a method for calibrating sintering model parameters utilizing global optimization techniques, finite element simulations, and experimental data. The evolution of shrinkage and relative density during the sintering of arbitrarily shaped 3D printed silica specimens was estimated using a numerical simulation with the SOVS sintering model.
The global minimization of error in dilatometry data of an experimental specimen and the model predictions were used to calibrate the constants necessary for the sintering model. The shrinkage behavior of arbitrarily shaped 3D parts during sintering was modeled using finite element analysis and compared to experimental data using the calibrated constants.
The proposed methodology considered orthotropy in shrinkages, the mechanics of internal stiffness related to the body's topology, and internal stresses that affect the part's apparent strength.
More from AZoM: Photovoltaic Efficiency of BiY(1-x)MnxO3 Ceramics
Disclaimer: The views expressed here are those of the author expressed in their private capacity and do not necessarily represent the views of AZoM.com Limited T/A AZoNetwork the owner and operator of this website. This disclaimer forms part of the Terms and conditions of use of this website.
Source:
Kakanuru, P., Pochiraju, K., Simulation of Shrinkage during Sintering of Additively Manufactured Silica Green Bodies. Additive Manufacturing 102908 (2022). https://www.sciencedirect.com/science/article/abs/pii/S2214860422003050