Bioethanol production has the potential to replace petrochemical-derived fuels for sectors such as the automotive industry. A new paper appearing in the journal Energies has explored the production of this alternative fuel from bacteria and fungi. Researchers from the Department of Chemical Engineering at Ariel University in Israel have contributed to the paper.
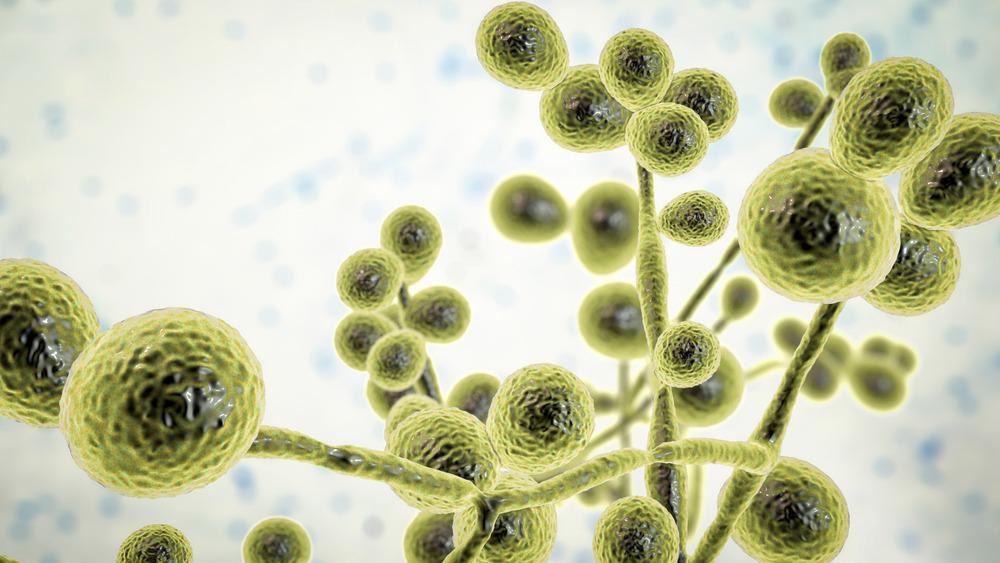
Study: Continuous Bioethanol Production by Fungi and Bacteria Working in Tandem. Image Credit: Kateryna Kon/Shutterstock.com
Bioethanol: A Green Alternative to Traditional Petrochemical Fuels
The harm that fossil fuel exploitation causes to the environment has been well documented in recent years. Along with the carbon emissions that are produced during manufacture and subsequent use, fossil fuel reserves are becoming depleted, facilitating the search for alternative fuels. Petrochemical production is struggling to keep up with demand as the world rapidly industrializes.
Bioethanol has been widely touted as a green, sustainable alternative to traditional petrochemical-derived fuels. This fuel can be produced from a multitude of natural, renewable resources such as crops and agricultural and food waste. However, producing biofuels such as bioethanol from food crops is not sustainable, as it depends on seasonal production and uses land that can be better purposed for food crops.
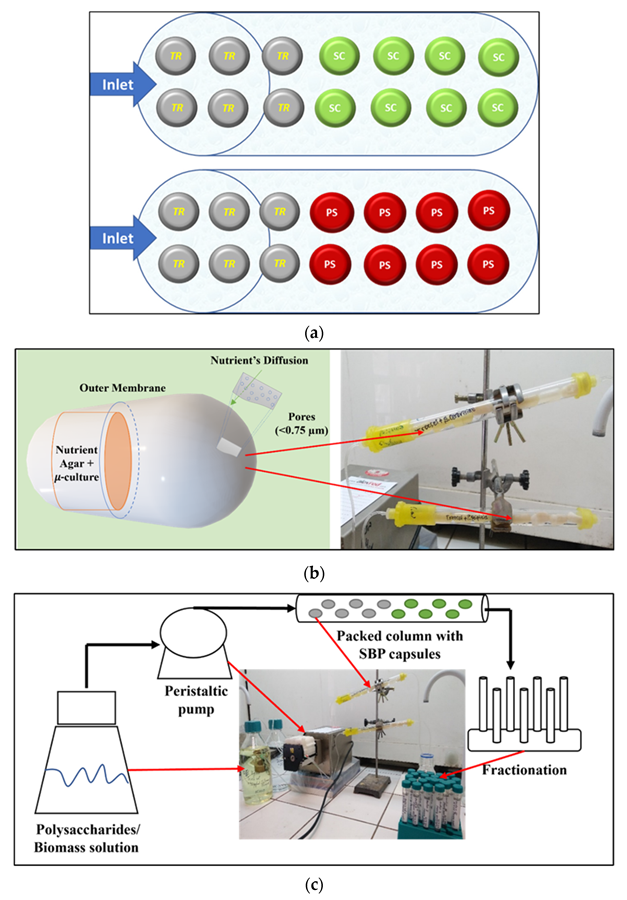
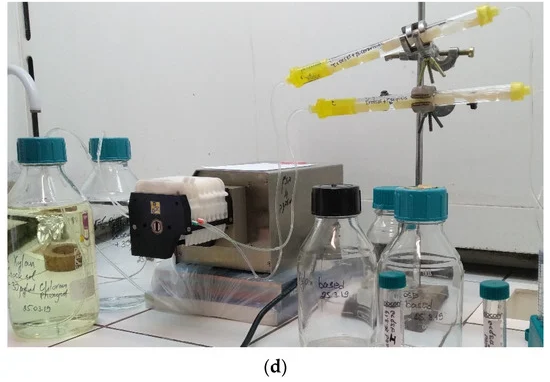
Schematic diagram of the continuous simultaneous reactor with SBP capsules: (a) Two columns packed with SBP capsules. Two colors in the columns depicted in the scheme represent two different encapsulated organisms. Each column contains encapsulated micro-organisms for saccharification and fermentation processes. The upper column was packed with T. reesei (TR) cells and the consecutive—with encapsulated S. cerevisiae (SC) cells. The bottom column was packed with encapsulated T. reesei cells and the consecutive column with P. stipitis (PS) cells. (b) The capsule (left panel) consists of an external membrane that encases the aquatic exogenous micro-inoculum and nutrient supplemental specific growth medium. The porous membrane allowed for free the diffusion of oxygen and nutrients to the internal micro-culture. Columns packed with capsules are shown on the right panel. (c) The reactor consisted of a feed container with a specific substrate stock solution, a peristaltic pump and pipes, glass columns packed with SBP capsules containing micro-organisms, and the fractions collection system. (d)—an image of a designed reactor. Image Credit: Rahamim, V et al., Energies
Traditional bioethanol production also faces problems with water consumption. Many international bodies have highlighted the critical issue of water poverty in several developing nations, and the consumption of this vital resource for bioethanol production is exacerbating this key social issue.
Bioethanol produced from waste lignocellulosic materials and other non-edible resources circumvents these issues. Fuel can be produced from a wide variety of waste products such as straw, forestry residues, and sawdust. These materials have the advantages of not competing with food crops, renewability, circularity, abundance, and seasonal independence.
There are drawbacks associated with using waste materials for bioethanol production, however. Biomass typically must be pre-treated, and conversion processes are costly and complex. To address the technical issues with utilizing food crops and waste materials, research has focused on utilizing microorganism biomass in recent years.
Producing Bioethanol from Microbial Biomass
Microbial biomass has several advantages for the manufacture of bioethanol. Biomass derived from these organisms can be produced cheaply in a short period of time, producing abundant amounts of recoverable materials. One of the main sources of biomass for biorefineries is microalgae.
There are, however, some challenges still to overcome with these processes. It is still a novel field of research, is expensive, has scalability issues, and requires significant amounts of carbon dioxide to produce raw materials. Additionally, there are unresolved environmental, social, and contamination issues.
Biomass pretreatment is an essential step in bioethanol production. Physical treatment and microbial biodegradation are widely employed methods that are considered eco-friendly and can efficiently retrieve valuable products such as polysaccharides. Pretreatment of biomass can also reduce rigidity and crystallinity.
Trichoderma reesei is a widely used fungal species that secretes hemicellulose and cellulase enzymes. This commercial-scale fungus breaks down biomass and produces fermentable monosaccharides which can be metabolized by other micro-organisms such as S. cerevisiae. Using microorganisms such as these can produce high volumes of bioethanol via simple and scalable processes in biorefineries.
To improve the efficiency of bioethanol production from microbial biomass and enhance the stability of processes, several immobilization and bioencapsulation strategies have been explored. However, challenges occur with these techniques such as cell leaks, excessive costs, and limited product and substrate diffusion.
Recently, an innovative process called the Small Bioreactor Platform technology has been developed. Microbial cells are encapsulated without the need for immobilization or absorption on gelatinous matrices. Inside the capsules, the microbes are held in a free suspended state. Capsules are constructed from microfiltration membranes, which have benefits such as higher permeability rates compared to traditional polymeric beads.
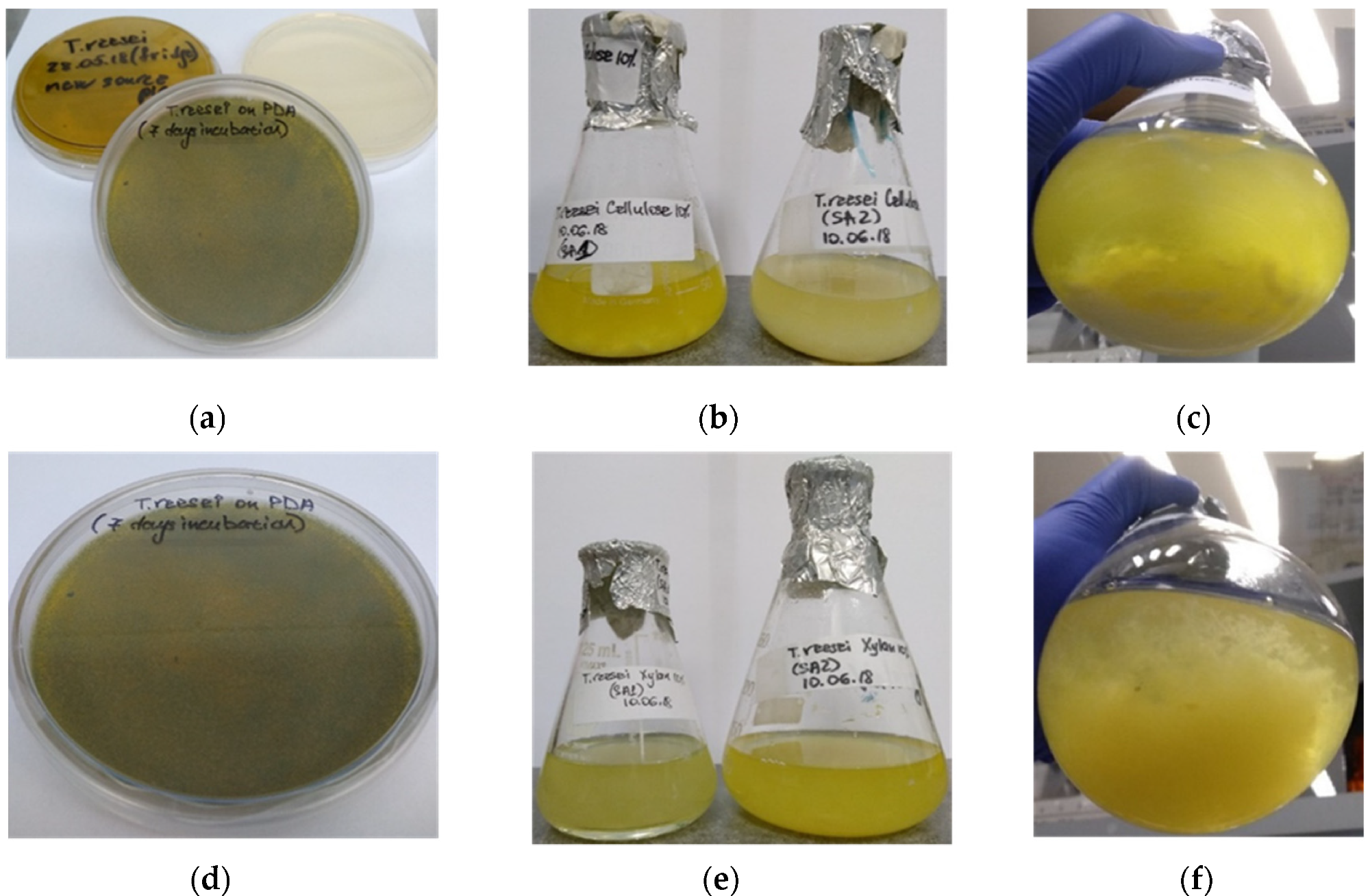
Shake-flask cultivation of T. reesei on cellulose-based (a–c) and xylan-based (d–f) culture media. (a,d)—PDA plates with fungal mycelium after 7 days incubation at 30 °C; (b,c)—biomass production of T. reesei cultured in the growth medium with cellulose added as carbon source, after 14 days incubation at 30 °C; (e,f)—biomass production of T. reesei cultured in the growth medium with xylan added as carbon source system, after 14 days incubation at 30 °C. Image Credit: Rahamim, V et al., Energies
The Study
The team behind the paper in Energies has developed a Small Bioreactor Platform process that uses encapsulation of T. reesei, P. stipitis, and S. cerevisiae to continuously produce bioethanol from cellobiose and xylan. Corn core was used as the raw material for xylan production.
Post-encapsulation viability, biological activity, and bioethanol production were evaluated in the paper. Moreover, the authors evaluated the longevity of the process over a period of three months. The authors evaluated two process configurations. The first configuration involved columns of all three encapsulated microorganisms. In the second configuration, separate columns of yeast and fungal cells were used in series.
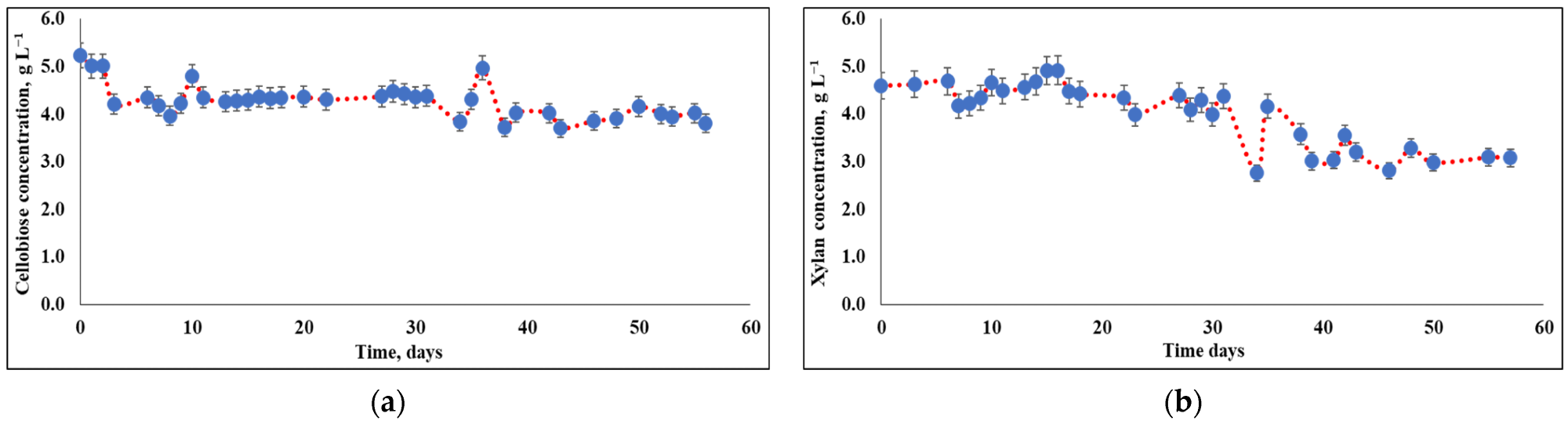
Cellobiose and xylan concentrations during consumption by T. reesei cells. The cultivation was based on: (a) cellobiose as the carbon source; (b) xylan as the carbon source. Image Credit: Rahamim, V et al., Energies
Study Findings
Physical encapsulation of microorganisms in the process’s medium with abundant nutrients enhances the proliferation of micro-cultures over several weeks. Another benefit of the proposed system is the simultaneous fermentation and saccharification without the need for cell or matrix renewal. A 60-70% system efficiency was achieved, with the goal of continuous production achieved.
The process used low concentrations of substrate materials; therefore, bioethanol yields were low. The authors have stated that future experiments using higher substrate concentrations are needed. Increased residence time leads to prolonged microorganism exposure to substrates and tuning this residence time can lead to controlled process yields. Further studies are needed on other substrates.
At the end of the study, there was no significant change in the structure of the capsules. Furthermore, no changes to microbial cultures were observed. Additionally, the simultaneous nature of the process and prolonged micro-organism viability provides benefits in terms of capital costs and significant improvements in the conversion of sugars to bioethanol.
Whilst further studies are needed, the process demonstrated in the paper is highly promising for the production of sustainable, green bioethanol.
Further Reading
Rahamim, V et al. (2022) Continuous Bioethanol Production by Fungi and Bacteria Working in Tandem Energies 15(12) 4338 [online] mdpi.com. Available at: https://www.mdpi.com/1996-1073/15/12/4338
Disclaimer: The views expressed here are those of the author expressed in their private capacity and do not necessarily represent the views of AZoM.com Limited T/A AZoNetwork the owner and operator of this website. This disclaimer forms part of the Terms and conditions of use of this website.