A paper recently published in the journal Additive Manufacturing demonstrated topology optimization (TO) of three-dimensional (3D) printed concrete for construction.
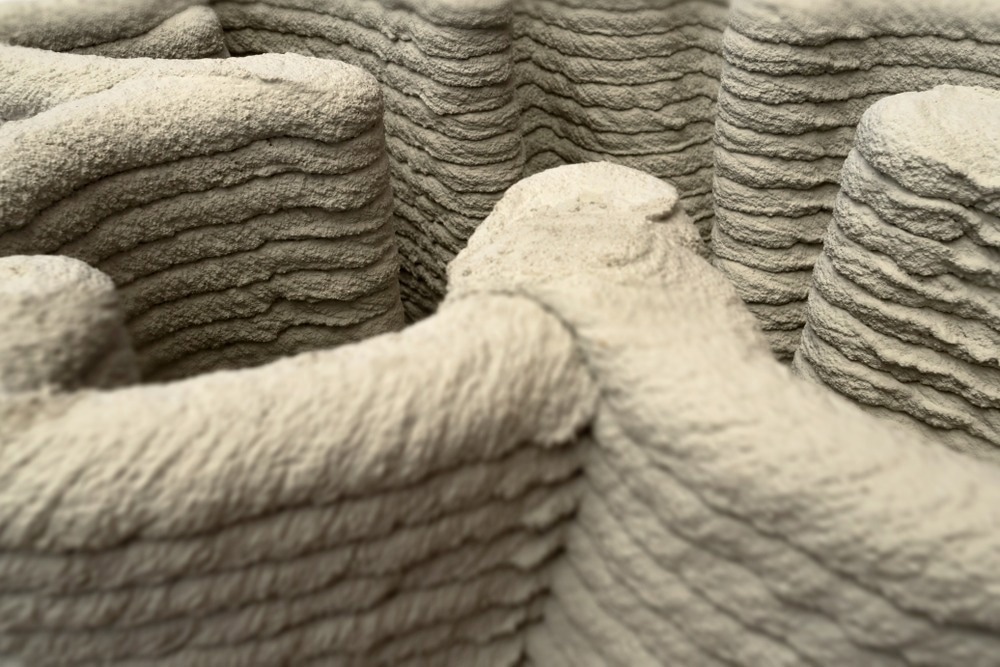
Study: Topology Optimization for 3D Concrete Printing with Various Manufacturing Constraints. Image Credit: Zapp2Photo/Shutterstock.com
Background
Additive manufacturing (AM) / 3D printing allows the manufacturing of complex designs in a layer-by-layer process with greater design flexibility in geometry. AM is used in different industrial applications, such as automotive, biomedicine, and aerospace.
Recently, AM has gained considerable attention for enabling free-form designs and automation in the architecture, engineering, and construction (AEC) industry. Among various AM strategies, 3D concrete printing (3DCP) is rapidly gaining prominence in the AEC industry for the construction of large-scale structures by extruding cement-based materials. For instance, 3DCP was used to construct 3D concrete printed walls, truss-shaped pillars, and bespoke columns.
TO optimizes the structural layout under prescribed design conditions. Structurally inefficient areas in a design are gradually eliminated using an iterative procedure to refine the design. Different methods, including solid isotropic material with penalization (SIMP) method, homogenization method, bi-directional ESO (BESO) method, level set method, moving morphable component (MMC) method, and evolutionary structural optimization (ESO) method, are currently used for the TO of structures.
The design freedom allowed by AM is compatible with the TO concept. Thus, the integration between TO and 3DCP can help in fabricating structurally efficient and spatially intriguing structures for large-scale construction. However, 3DCP-TO integration also possesses several challenges, which must be addressed before its implementation.
For instance, the cantilevering structures can lose their self-supporting capacity due to the gravitational force if their overhang angle, which typically ranges from 70o to 90o depending on the application, exceeds the maximum limit. Similarly, the printed structures display an anisotropic structural behavior, and their surfaces are vulnerable to cracks due to shrinkage owing to the nature of 3DCP.
Additionally, compatible reinforcement strategies, including micro-cable and fiber reinforcement, mesh reinforcement, and bar penetration must be explored to incorporate reinforcements in tensile zones. Moreover, 3DCP requires continuous printing to prevent nozzle blockage owing to material solidification as the simultaneous stop-and-start operation is extremely difficult in printers with separate nozzle movement systems and material feeding systems.
These manufacturing constraints are typically resolved during the post-processing stage, requiring additional design efforts and significant modifications, which affect the structural efficiency of the topology-optimized design. Thus, an explicit TO framework incorporating different 3DCP manufacturing constraints are required to successfully facilitate the integration between these fields.
The Study
In this study, an integrated TO framework was proposed to address different 3DCP manufacturing constraints. A self-supporting design was generated by introducing a layer-wise sensitivity scheme to replicate the layer-by-layer printing process.
The BESO procedure was utilized in this study due to its compatibility with image-processing strategies using good computational efficiency and binary variables. Numerical studies were performed to evaluate the effectiveness and robustness of the proposed algorithm based on the benchmark cantilever example used extensively in TO studies. In the experiment section, the feasibility of the algorithm in practical applications was tested by fabricating a TO chair using 3DCP.
Various printing designs were specified, and the generated designs were kept continuous and vertically aligned in every iteration. The geometrical continuity of every layer was ensured by implementing an innovative continuous extrusion constraint, which led to uninterrupted extrusion and movement of the nozzle during the 3DCP fabrication process.
Domain segmentation of the TO structure, which is analogous to the modular construction concept, was proposed to allow favorable print direction in every segment and modular construction. The 3DCP anisotropic behavior was also simulated in the TO framework by considering a transverse isotropic material model in the finite element analysis (FEA).
Observations
An innovative BESO TO framework was demonstrated that addresses several 3DCP manufacturing constraints. The 3DCP overhang angle limit was satisfied by the layer-wise sensitivity scheme. The vertical alignment of the optimized design was guaranteed along the print direction, leading to a self-supporting structure in the user-defined orientation. Alternative solutions with a similar performance were obtained using the self-support constraint.
The overhang limit was bypassed by domain segmentation. The 3DCP process anisotropy was simulated effectively in the optimization process using the transverse isotropic material model. Although 3DCP printing anisotropy led to variations in the optimized designs, the main structural elements remain unchanged.
The implementation of a novel continuous extrusion constraint in the TO framework facilitated continuous printing operation. The shortest possible routes were located depending on the minimum distance principle and connected component labeling algorithm.
The optimized design achieved a global geometrical continuity with the interconnected two-dimensional (2D) geometry in every layer. The continuous extrusion constraint successfully linked the isolated areas in every layer without considerably affecting the structural performance of the designs.
The combination of continuous toolpath algorithm and continuous extrusion constraint allowed the fabrication of a topology-optimized design with good efficiency and print quality. However, designs at a low volume fraction were modified during post-processing to address the nozzle size constraint.
The topology-optimized chair was printed successfully based on the proposed algorithm, which demonstrated the robustness of the algorithm in addressing different 3D manufacturing constraints in a real-design environment.
To summarize, the findings of this study effectively demonstrated TO for 3DCP with different manufacturing constraints. A stress constraint can be integrated into the TO framework in future studies to obtain a more accurate simulation.
More from AZoM: Reviewing the Use of Computational NIR Spectroscopy
Disclaimer: The views expressed here are those of the author expressed in their private capacity and do not necessarily represent the views of AZoM.com Limited T/A AZoNetwork the owner and operator of this website. This disclaimer forms part of the Terms and conditions of use of this website.
Source:
Bi, M., Xia, L., Tran, P. et al. Topology Optimization for 3D Concrete Printing with Various Manufacturing Constraints. Additive Manufacturing 2022. https://www.sciencedirect.com/science/article/pii/S221486042200375X?via%3Dihub