In a paper published in the journal Energies, researchers reviewed the various cooling systems in semiconductor devices. The study discussed the classification of classical as well as modern cooling systems of devices and integrated circuits, including the construction and operation principles of the said systems. The effect of different factors on the efficiency of the components operating on the cooling functions was measured and the results were presented and discussed.
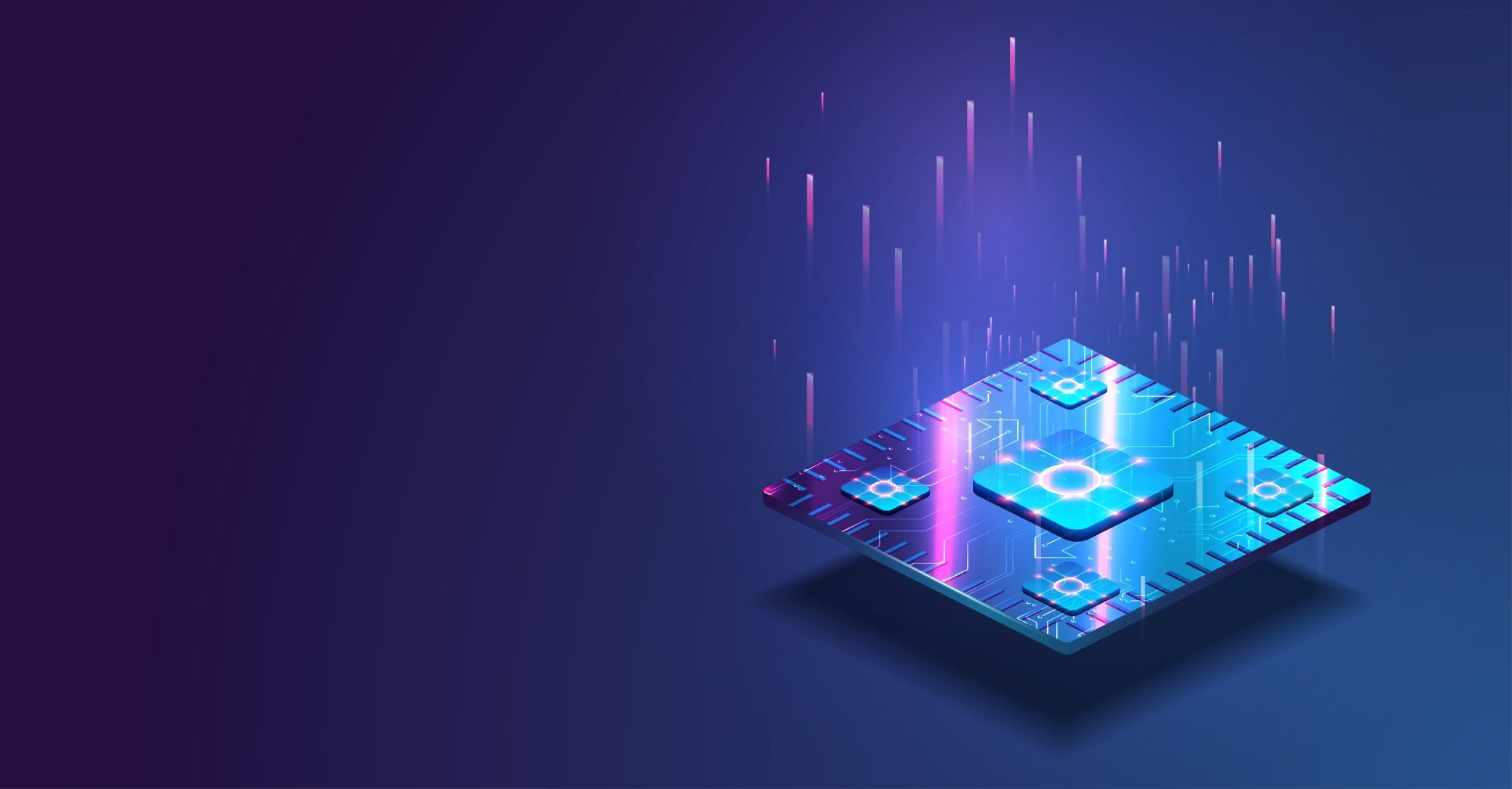
Study: Cooling Systems of Power Semiconductor Devices—A Review. Image Credit: ZinetroN/Shutterstock.com
Background
With the increase in the power generated from contemporary electronic devices, cooling becomes a vital problem. High heat flux values render traditional cooling methods using metal heat sinks insufficient. The device packaging constructors and the electronic circuit designers also need to be investigated in order to solve the problem of effective cooling.
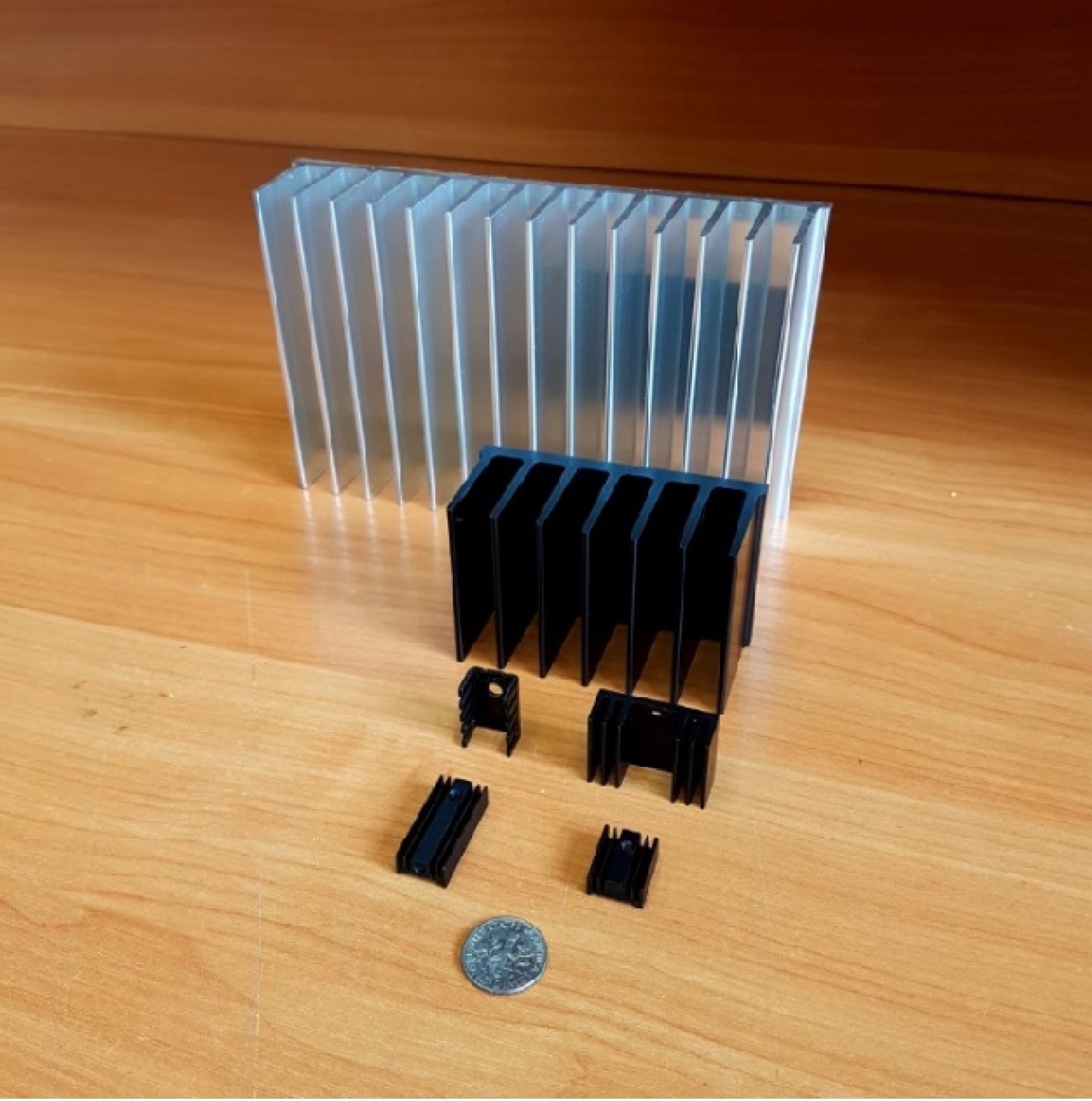
Examples of a passive heat sink. Image Credit: Górecki, K et al., Energies
Research in this area is focused on selecting new materials to be utilized in cooling systems and on instruments based on physical phenomena to enhance the cooling of the devices discussed.
The materials utilized to cool electronic devices include graphene, diamond, and pyrolytic graphite along with metal and ceramic composites, among others. Modern solutions comprise vapor and liquid chambers, liquid cooling, and thermoelectric modules. Advances in contemporary science have led to materials with enhanced properties. Thus, a trend was observed by the team in the search for new materials and solutions to improve heat dissipation in electronic devices.
Commonly Used Cooling Systems
This review showed that all the components located between the device package and its surroundings constitute its cooling system, which maintains the temperature of the device under a specified maximum temperature. Cooling systems are divided into active and passive systems. Active systems require an external energy supply to function, while passive systems do not.
The components of the cooling systems reviewed included passive heat sinks, which function by dispersing the heat in the sink material, commonly aluminum. Axial fans and blowers are active cooling systems that create an airflow to dissipate heat from one side to the other. Heat pipes are two-phase passive devices that are filled up with a cooling liquid, usually deionized water. The heat from the device vaporizes the liquid, which travels to the condenser section and cools down. The condensed liquid returns to the vapor section by gravitational and capillary action.
High conduction metal plates (HCMPs) can also work with multiple heat sources and spread the heat on the entire plate surface through in-built heat pipes and thus are useful as device enclosures. Vapor chambers and thermosiphons work similarly in operation to heat pipes, except thermosiphons lack the wick structures. Encapsulated conductive plates (ECPs) contain sheets of annealed pyrolytic graphite and are used in high-quality electronic devices. Liquid cooling systems remove heat from the components through a coolant without changing its aggregate state. Other cooling systems reviewed in this study include immersion cooling, phase change material (PCM) heat sinks, interface materials, and thermoelectric modules.
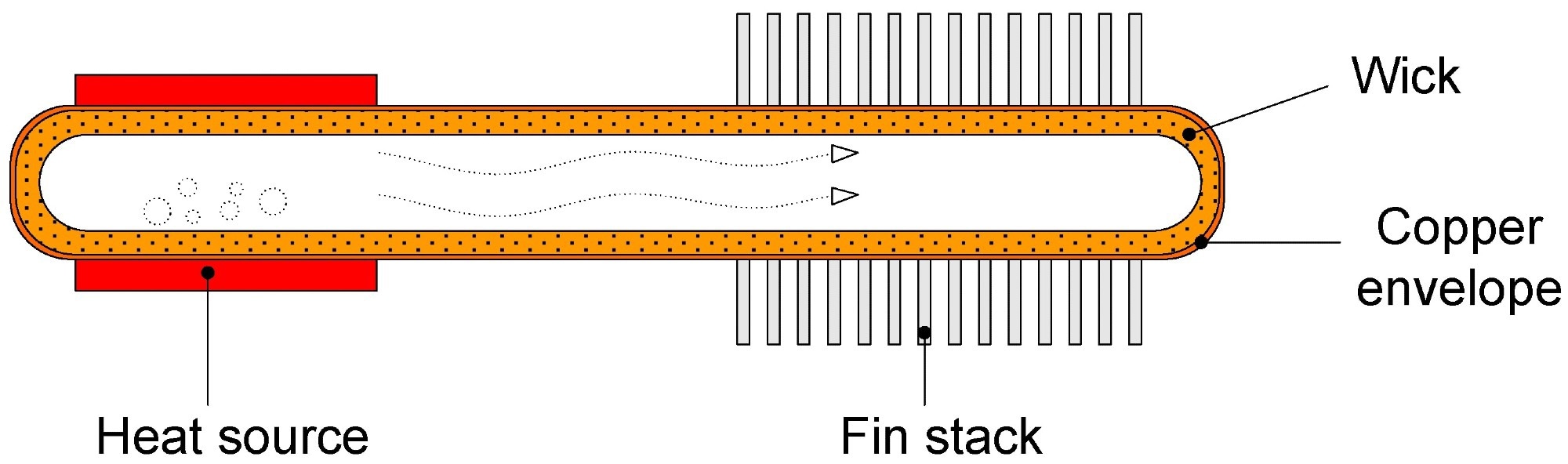
The construction and principle of operation of a heat pipe. Image Credit: Górecki, K et al., Energies
Measuring Cooling Parameters
Designing cooling systems requires calculation tools for active heat sinks. Such online calculators can be found on websites such as Advanced Cooling Technologies (ACT), MyHeatSinks (MHS), and Celsia. Precise determination of cooling parameters demands the use of computational fluid dynamics (CFD) methods. Using these tools, the effect of selected parameters on heat pipes and air-cooled active heat sinks was calculated.
It was observed that the thermal conductivity of a heat pipe depended on its diameter in a non-monotonic and greatly nonlinear function, with optimum thermal conductivity achieved by heat pipes 4 mm and 5 mm in diameter. The heat pipe was most efficient with the evaporator located right above the heat source. The thermal resistance exhibited a decreasing nonlinear function of the pipe diameter. However, the thermal resistance of the heatsink decreased with the extension of the base of the heat sink, when aluminum was selected as the heat sink material.
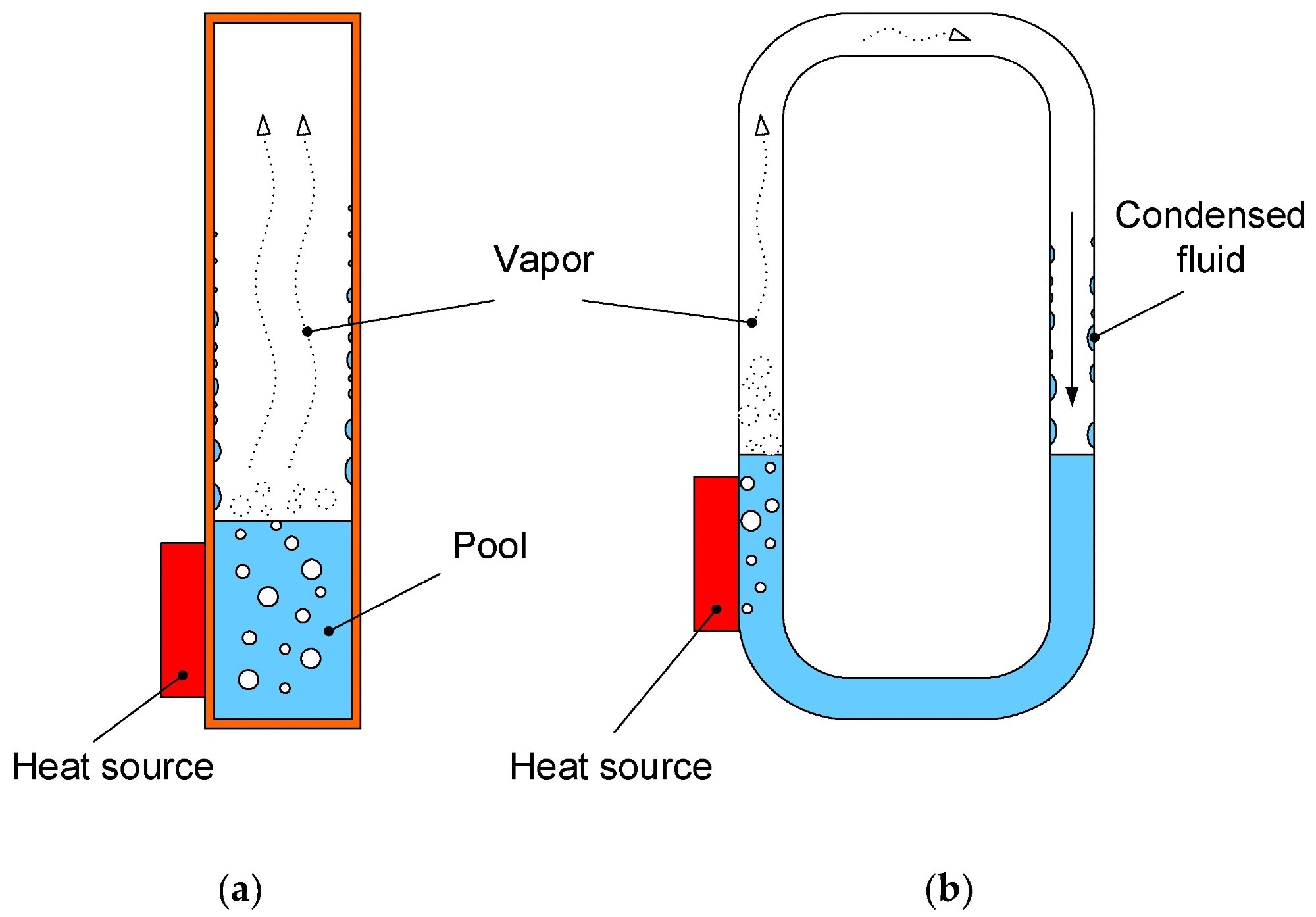
Schematic representation of (a) counter-flow thermosiphon and (b) loop thermosiphon. Image Credit: Górecki, K et al., Energies
Conclusions
Overall, this review demonstrated that aluminum and a spot heat pipe were the cheapest cooling solutions, while encapsulated conduction was the most expensive. The vapor chamber released maximum power density in the cooled element. Immersion cooling exhibited effective heat removal but had the least system dependency. The cheapest, as well as low-efficiency cooling systems, were the air-cooled fin heat sinks. Two-phase cooling system, although expensive was the most effective cooling system with the added advantage of easy expansion.
Thus, the efficiency of cooling components in semiconductor devices depends on the design, power dissipation, the dimensions of the heat pipe and the heat sink, and the airflow velocity around the heat sink. According to the authors, more solutions for the cooling systems are being developed intensively, and new designs of systems operating at higher power densities enabling efficient heat removal can soon be expected.
Disclaimer: The views expressed here are those of the author expressed in their private capacity and do not necessarily represent the views of AZoM.com Limited T/A AZoNetwork the owner and operator of this website. This disclaimer forms part of the Terms and conditions of use of this website.
Source:
Górecki, K.; Posobkiewicz, K. Cooling Systems of Power Semiconductor Devices—A Review. Energies 2022, 15, 4566. https://www.mdpi.com/1996-1073/15/13/4566