By Surbhi JainReviewed by Susha Cheriyedath, M.Sc.Jul 8 2022
In an article recently published in the journal Additive Manufacturing, researchers discussed the development of complex lattice materials through additive manufacturing to fully utilize the design possibilities and provide reliable strut additive continuity.
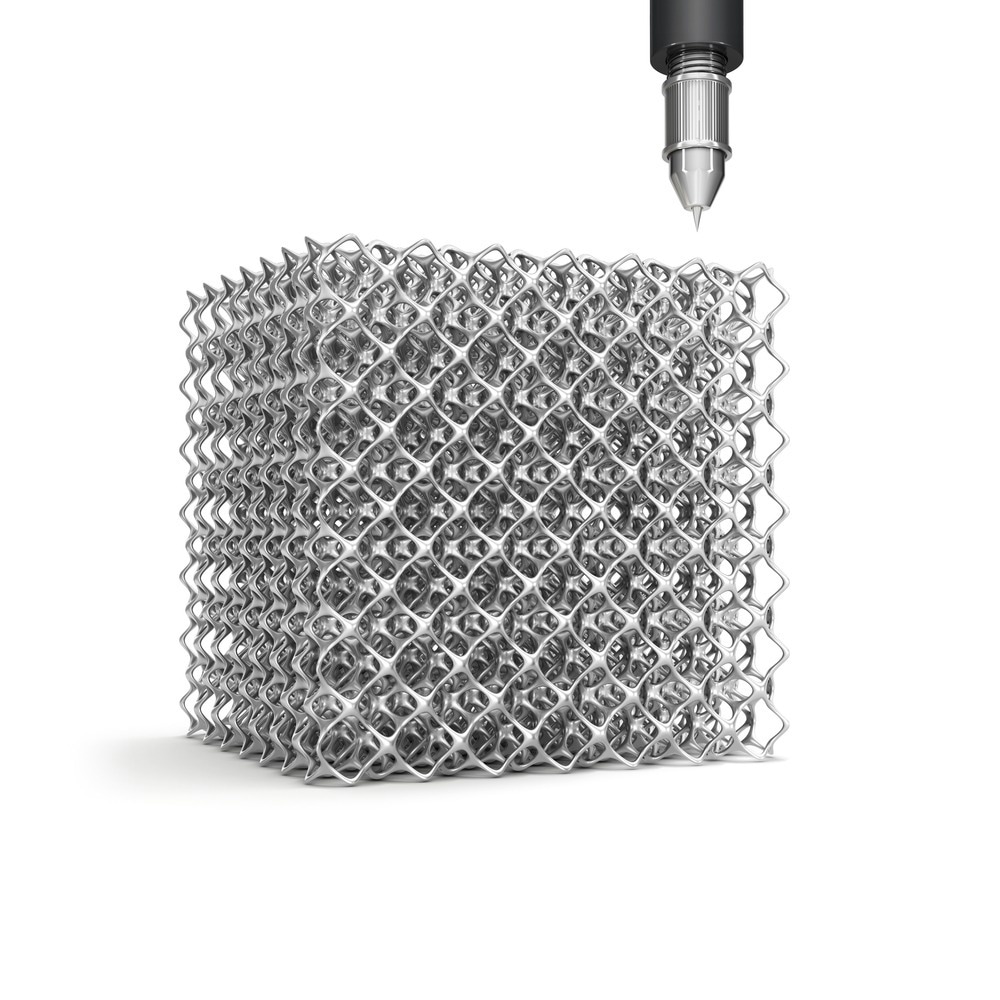
Study: Additive manufacturing of intricate lattice materials: Ensuring robust strut additive continuity to realize the design potential. Image Credit: Iaremenko Sergii/Shutterstock.com
Background
Powder bed fusion (PBF) additive manufacturing (AM) enables complex lattice materials that are topologically organized, three-dimensional (3D) open-cell structures. As a result, they have swiftly become a class of innovative materials with a wide range of applications, most notably in the form of lattice structures. A wide range of metal lattice structures has been created, fabricated additively, and evaluated up to this point.
However, Finite Element (FE) based estimates of metal lattice properties frequently noticeably differ from experimental observations due to improper consideration of lattice strut defects and geometric errors.
As a result, efforts have been undertaken to incorporate the impact of strut geometry flaws into the FE modeling of lattice characteristics. Overall, metal AM using either electron beam PBF (EB-PBF) or laser PBF (L-PBF) is able to consistently create highly dense sections with uniform surface finishes after years of intensive development.
Furthermore, the interior flaws in lattice struts can be successfully repaired by hot isostatic pressing (HIP). However, each tiny strut's short cross-section means that any significant surface imperfections or geometrical flaws could significantly affect the strut or lattice qualities. According to studies, the base material, strut diameter, inclination angle, strut length, powder properties, and PBF parameters all have an impact on a lattice strut's PBF additive manufacturability.
About the Study
In this study, the authors discussed the development of an interlocked strut additive continuity model for PBF and applied it to the whole range of Ti-6Al-4V strut designs. Based on this, a strut additive continuity threshold value of 0.9 was proposed and tested using 23,100 inclined struts made by electron beam PBF in Ti-6Al-4V lattices. Further, design maps for lattice material EB-PBF were created. Additionally, a baseline beginning layer thickness for each type of powder and a minimum powder-bed density for powder selection was suggested.
The team created the fundamental foundation for EB-PBF to design and produce durable lattice materials, including graded lattices. The setting of a minimal threshold parameter for strut additive continuity was determined. The complex lattice designs were then informed or verified using the criterion for systematic validation. On the basis of this, all-inclusive additive continuity maps for PBF AM of the metal lattices were built. Their extensive ramifications were examined for both graded and uniform lattice materials, with the identification of a minimal powder-bed density (PBD) for powder selection as well as a fundamental layer thickness setting equation particular to powder (h0-specific).
The researchers addressed the problem of the lack of a general design criterion for PBF of lattice struts that were informed by manufacturability. To quantify the impact of both explicit and latent design and manufacturing parameters on lattice strut additive continuity, a thorough additive continuity model for PBF AM of lattice struts was developed.
Observations
In the case of Ti-6Al-4V with ρPBD = 0.65ρTD, additive continuity was only a concern for lattice struts thinner than 310 µm at h0 = 20 µm, regardless of strut orientation. All Ti-6Al-4V struts thicker than 155 µm could be robustly produced for all inclination angles if h0 was further decreased to 10 µm. It was difficult to satisfy the min-threshold of 0.90 if a powder feedstock displayed ρPBD < 0.6ρTD.
The lattice strut additive continuity was significantly impacted by the starting layer thickness setting (h0). For EB-PBF of lattices having reliable strut additive continuity, a small h0 was always chosen when it was practical. A powder-specific h0 was defined as Dv(90) x (ρPBD/ρTD), which could be used as a benchmark.
Lattice strut additive could be considerably affected by the powder-bed layer density continuity. Powder selection for PBF of the lattice materials should have a minimum ρPBD of 0.6TD, where PBD was affected by the powder recoating mechanism, and the particle size distribution. The maps of lattice strut additive continuity created by EB-PBF served as a thorough manual for the designing and production of lattice materials with reliable strut additive continuity. The cut-off layer number could be adjusted to 10 for all the powder feedstock materials having ρPBD > 0.5ρTD.
Conclusions
In conclusion, this study elucidated the development of a φ parameter that quantified the effects of the starting layer thickness setting (h0), the strut inclination angle (θ), the strut diameter (d), and the powder-bed density (ρPBD) on the lattice strut additive continuity. In order to design and produce lattice materials with reliable strut additive continuity via EB-PBF using the default Arcam EB-PBF parameters, a minimal strut additive continuity threshold value, min-threshold = 0.9, was defined.
The relationship of powder-bed layer thickness on layer number (n) for PBF AM was analytically determined.
Disclaimer: The views expressed here are those of the author expressed in their private capacity and do not necessarily represent the views of AZoM.com Limited T/A AZoNetwork the owner and operator of this website. This disclaimer forms part of the Terms and conditions of use of this website.
Sources:
Zhang, X. Z., Tang, H. P., Wang, J., et al. Additive manufacturing of intricate lattice materials: Ensuring robust strut additive continuity to realize the design potential. Additive Manufacturing 103022 (2022).
https://www.sciencedirect.com/science/article/abs/pii/S2214860422004146