Researchers from India and Poland have investigated the improvements lightweight materials can bring to electric motors. Their research findings have appeared in the journal Energies.
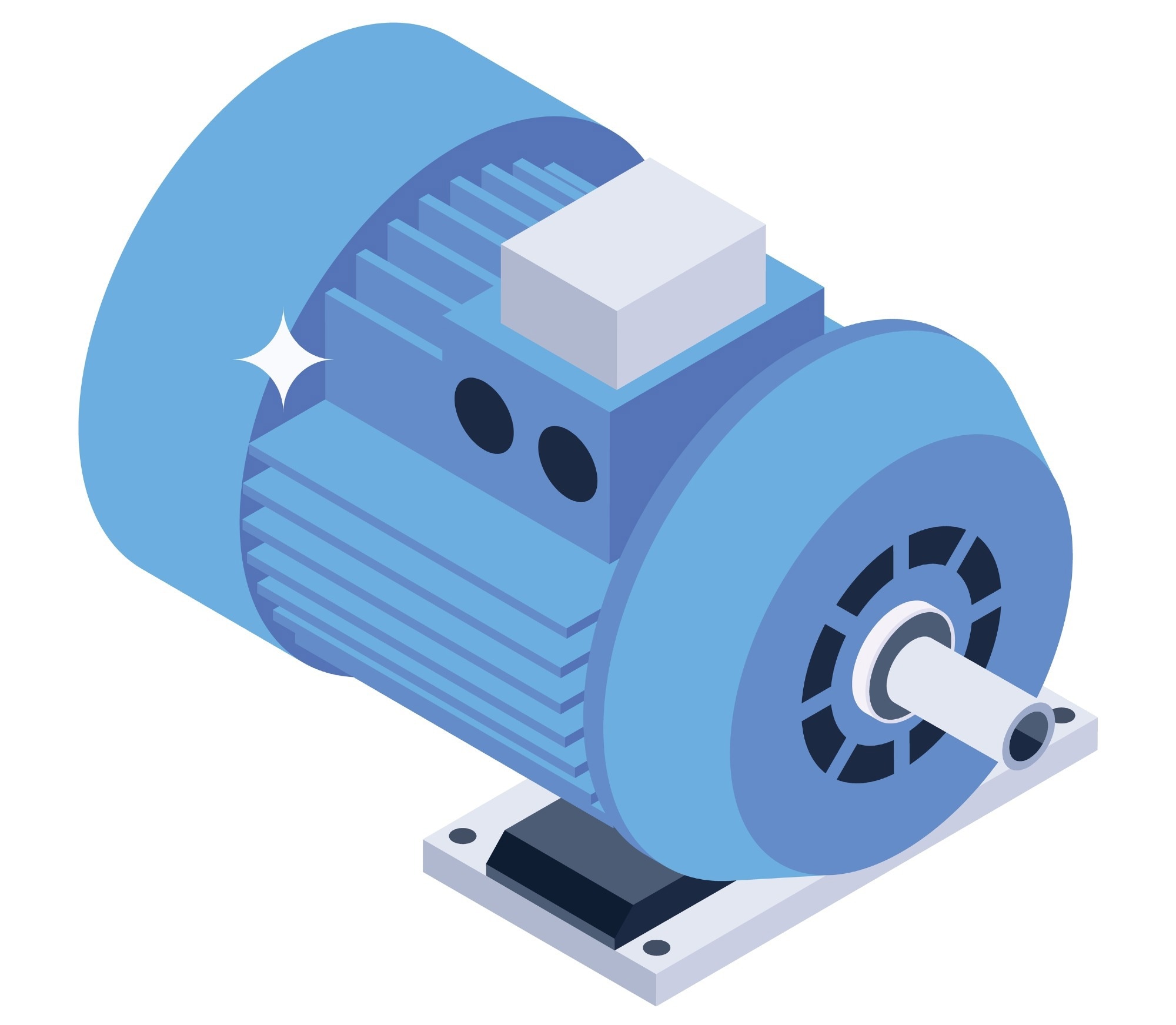
Study: Modeling and Simulation of Electric Motors Using Lightweight Materials. Image Credit: smashingstocks/Shutterstock.com
Electric Motors
Electric motors are a key technology in the fight against climate change and achieving global net zero carbon goals.
In electric vehicles, especially, the need to maintain power and efficiency while reducing the weight of vehicles is of paramount importance to designers. While challenges still exist with the design of electric motors and, in particular, the materials used in their construction, the urgent need for rapid decarbonization has increased research focus on designing efficient, powerful, and lightweight devices.
Typical AC induction motor. Image Credit: Boopathi, N.G et al, Energies
Applying Electric Motors in Motor Vehicles
The electric and hybrid vehicle markets have grown significantly in recent years. Companies such as Tesla, Porsche, and BMW have been at the forefront of innovation in this commercial space in the past decade or two. Electric motor design is at the heart of this industry, and several challenges exist with designing suitable technologies.
High-performance electric vehicles currently employ different cooling systems for electric motors, with water-cooled systems being widely employed instead of conventional fan-cooling systems, which are both bulky and heavy. This keeps the electric motor cool and at peak efficiency without sacrificing vehicle weight and performance.
However, water cooling systems experience their own set of issues which limits the optimal design of electric motors. Firstly, leaks can occur within these systems, in pipes, and so forth, which can reduce the overall efficiency of motors, leading to potential overheating and furthermore, causing safety issues from both overheating and water damage. Proper design and maintenance are crucial.
Furthermore, challenges arise with the need for complex machinery in these systems, such as pumps, pipes, and radiators. This makes them more difficult to maintain than conventional fan-cooled systems.
Utilizing Lightweight Materials in Electric Motor Systems
To overcome weight issues and maintain optimal efficiency in electric motors, research has focused on the use of lightweight advanced materials in components such as water-cooling systems.
Studies have investigated many different materials in recent years, including carbon fiber and polymer-based composites. Improving the design of components and evaluating the use of advanced materials in electric motors overcomes many of the issues with current technologies.
For instance, one of the major components of an induction motor is the start coil. These are usually constructed from metallic materials such as copper, aluminum, and silicon steel. Changing the material used in the outer casing, for example, and using fiber-reinforced polymers instead reduces the weight of these components and therefore improves the overall efficiency of motors.
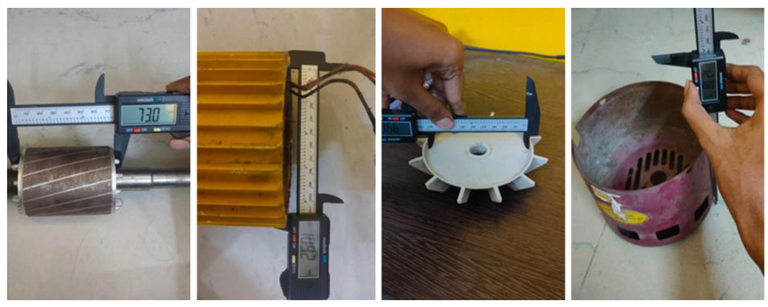
Measuring the dimensions of various parts of the motor. Image Credit: Boopathi, N.G et al, Energies
The Study
The authors have explored different possibilities for reducing the overall weight of electric motors using various lightweight advanced materials without sacrificing the overall power efficiency and performance of these crucial green devices. Specifically, the authors have focused on a fluid-cooled motor. Several studies and concepts have been explored in the paper.
For the research, a 0.5 HP motor was selected by the authors. This is a conventional fan-cooled induction motor. The authors chose this motor to demonstrate how a water-cooled system could improve its efficiency. Using this motor as a reference, a fan-cooled motor was designed using CAD methods. The reference motor was stripped, and the dimensions and weight of components were measured.
Thermal analysis demonstrated the increased efficiency of using an axial housing water jacket to provide cooling compared to the conventional, completely enclosed fan-cooled motor.
FEM analysis was employed in the research to evaluate the difference in temperature ranges and gradients. The water-cooled motor possessed a lower temperature range than its fan-cooled counterpart. PA6GF30, a glass fiber-reinforced polymer composite was evaluated. The ability of this material to reduce the highest temperature of the system was nearly comparable to aluminum, which is a conventionally used material for this purpose.
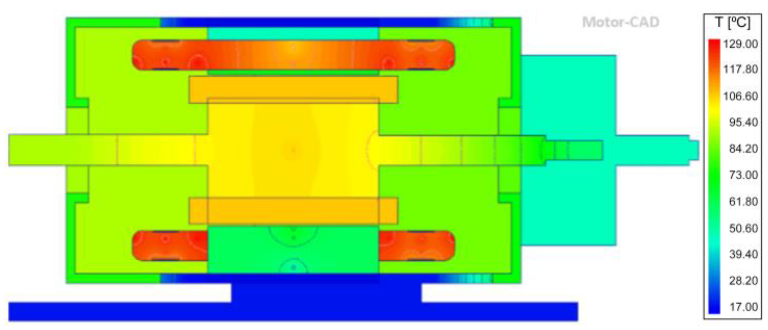
Axial view of water-cooled motor with PA6GF30 casing after FEM analysis. Image Credit: Boopathi, N.G et al, Energies
Future Research
Whilst this study has demonstrated the use of lightweight materials (specifically PA6GF30) in electric motor design (specifically water-cooled systems) to reduce weight whilst retaining similar efficiency and performance, there exists several future research opportunities. The significant weight reduction using the material in the research demonstrates the promising nature of this research field.
The authors have stated that a next step in the research into improving electric motors is to evaluate lightweight and low-density materials for use in motor casings. Selecting appropriate materials which are compatible with the cooling system will be a key area of focus. Whilst there are still challenges to overcome, this study has provided an important contribution to this field of materials science and design.
Further Reading
Boopathi, N.G et al. (2022) Modeling and Simulation of Electric Motors Using Lightweight Materials Energies 15(14) 5183 [online] mdpi.com. Available at: https://www.mdpi.com/1996-1073/15/14/5183
Disclaimer: The views expressed here are those of the author expressed in their private capacity and do not necessarily represent the views of AZoM.com Limited T/A AZoNetwork the owner and operator of this website. This disclaimer forms part of the Terms and conditions of use of this website.