Lightweight concrete (density less than 1000 kg/m3) is often achieved by incorporating a substantial amount of foamy substance into fresh concrete. The latest study in the journal Cement and Concrete Composites looks into combining lightweight particles with prepared foam in foamy concrete to achieve a density of less than 1000 kg/m3 for 3D printing.
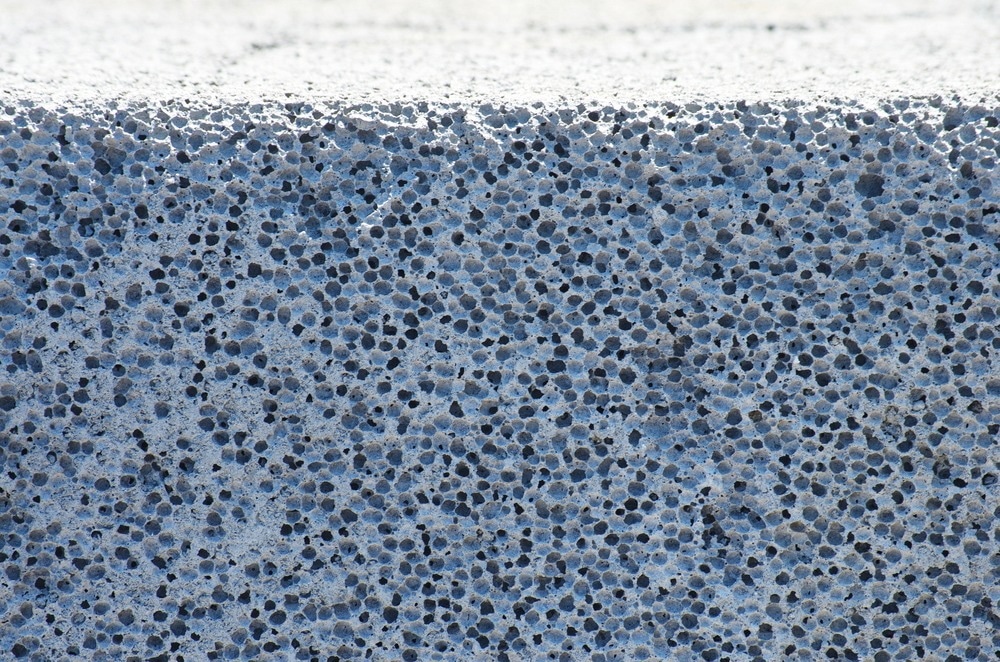
Study: Enhancing the properties of foam concrete 3D printing using porous aggregate, Cement and Concrete Composites. Image Credit: olpo/Shutterstock.com
Advantages of 3D Concrete Printing
3D concrete printing (3DCP) is a new technology altering the construction sector by combining construction automation and intelligent manufacturing. Compared to traditional building methods, 3DCP offers considerable reductions in waste generation, labor costs, time, and construction-related disasters, as well as the structural flexibility to design aesthetically complicated structures.
Extrusion-Based 3D Concrete Modeling
Extrusion-based 3DCP can be utilized for building large-scale buildings. Its popularity is mostly owing to the inherent benefits of the extrusion approach, which include the ease of application in large-scale 3D printing, the accessibility of specialized manufacturing machines or gantry platforms, the speedy fabrication method, and so on.
3D printed buildings are produced using the extrusion process by extruding and positioning a thin layer of new concrete strands following the geometry of the extrusion head.
The most frequent method for manufacturing ultralight concrete buildings using 3DCP is to utilize a compact concrete mix. Extrusion-based or powder bed 3D printing processes are used with a lightweight concrete mix comprised of permeable particles.
Introduction to Foam Concrete
Foam concrete is a type of concrete mixture that is made by incorporating a significant number of air cavities into the new cementitious matrix. Air gaps can be generated using either manual foaming (pre-foaming technique) or chemically induced foaming.
While the former approach incorporates pre-made foam at a predetermined ratio into the new cementitious material, the latter system utilizes a gas-releasing ingredient (Al powder, Silica fume, and H2O2) into the concrete mixture, which creates pores in the concrete.
The pre-foaming process is the easiest and more efficient of the two because it provides excellent control of the ultimate viscosity and porosity characteristics of the generated aerated concrete.
Advantages of Foam Concrete
Foam concrete offers several benefits over other lightweight concrete manufacturing technologies, including the ability to achieve ultra-low density (less than 300 kg/m3), good insulation qualities, auditory and fire resistance capabilities, and cost-effectiveness. As a result, the use of this concrete mixture is becoming more common in current building technologies such as façade architecture, boundary panels, ceilings, and exterior sheathing.
Challenges
The fundamental difficulty in 3D printing traditional concrete mixture is the low yield stress in the pristine condition, which results in poor form preservation and manufacturability. In typical foam concrete, such low yield stress is required to minimize bubble disintegration and failure during the blending process.
Due to the high shear stress during the blending, the high yield stress of the base mix (the mix before blending with froth) can cause severe disintegration of bubbles. As a result, it is clear that the rheological qualities of concrete mixture, especially at low density, continue to pose a significant problem for 3DCP applications.
A proposed solution to the conflicting needs of low density and yield stress is to substitute sand in 3D printed mixtures with cementitious materials. To achieve the same density, the compact aggregates would significantly lower the quantity of foam concentration.
Research Findings
Two foam concrete blends with granular sand as constituents (M1 and M2) and three mixes using EP instead of fine sand (M3, M4, and M5) were developed. In the sand-based group, the initial density of M1 improves from 1244 to 1253 kg/m3 during extraction and approaches 1267 kg/m3 after 20 minutes, representing an overall increase of 1.8 percent in 20 minutes.
The dispersion dimension of the M1 was 213.5 mm, whereas the spreading width of the M2 mix with increased foam concentration was 226.6 mm. The spread diameters of the EP groups' M3, M4, and M5 blends were 167.5 mm, 193.5 mm, and 201.5 mm, correspondingly. The foam content in the various mixtures was 2.5 percent, 5%, and 7.5 percent of the concrete mixtures, respectively.
The mechanical properties of the EP group 3D printed concrete were superior in all three tested orientations when contrasted to the sand group samples.
In brief, using EP as a substitute for fine aggregates (i.e. sand) in 3D printing foam concrete significantly lowered the foam percentage required to achieve the same density while improving the strength and durability qualities.
More from AZoM: What is Glow Discharge Optical Emission Spectrometry
Further Reading
Pasupathy K. et. al. (2022). Enhancing the properties of foam concrete 3D printing using porous aggregate, Cement and Concrete Composites. https://doi.org/10.1016/j.cemconcomp.2022.104687
Disclaimer: The views expressed here are those of the author expressed in their private capacity and do not necessarily represent the views of AZoM.com Limited T/A AZoNetwork the owner and operator of this website. This disclaimer forms part of the Terms and conditions of use of this website.