German scientists have collaborated on a new paper in Polymer Testing investigating the use of epoxy resin films to manufacture prepregs for use in the aerospace industry.
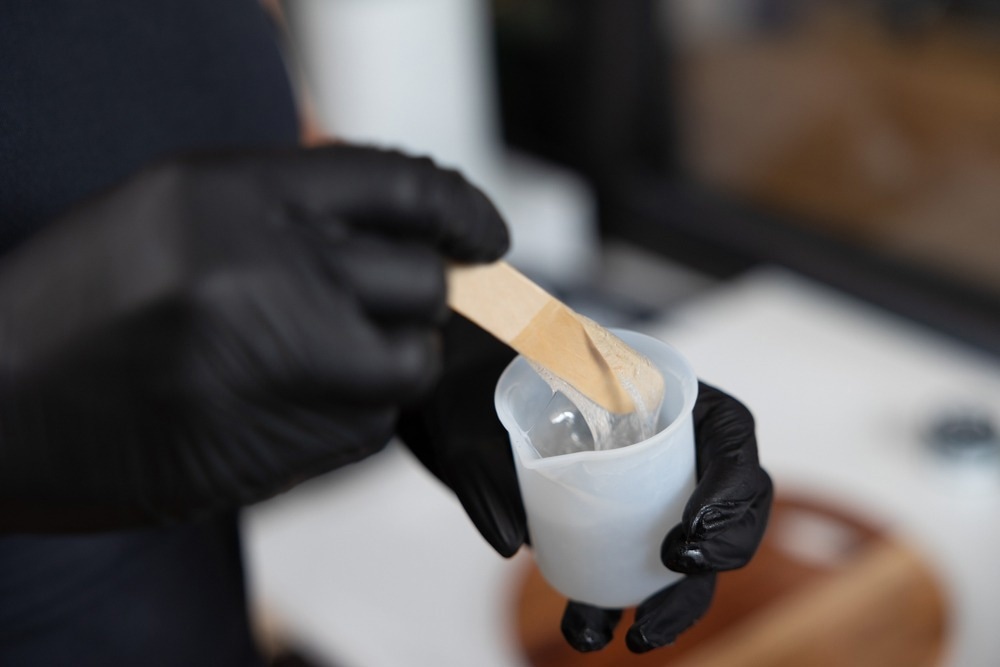
Study: Tack of epoxy resin films for aerospace-grade prepregs: Influence of resin formulation, B-staging and toughening. Image Credit: Eric fdo/Shutterstock.com
Manufacturing Composites for the Aerospace Industry
The aerospace sector is a key 21st-century industry that has highly specific and rigorous requirements for components to meet performance and safety standards. Amongst these requirements, thermomechanical performance is a critical concern as during the service life of an airplane it is subject to demanding environmental conditions.
To meet these demands, materials must possess characteristics such as a high modulus and high strength to ensure safe and optimal performance over the lifecycle of an airplane. These requirements limit the amount of suitable polymeric materials and stringent testing is required before a component or material can be approved for commercial use.
Different aerospace components have varying demands, with wings and fuselages subject to intense environmental pressures. The research and development of aerospace prepregs is a key area of study in the aerospace industry as any catastrophic failure in these parts can lead to loss of life and increased maintenance costs as well as fleets being grounded, causing economic damage to airlines.
Epoxy Resin-based Prepregs
Epoxy resin-based composites combined with carbon fiber reinforcements have proven to be beneficial materials for this purpose in recent decades. These composite materials possess high strength-weight ratios, superior processibility, and adequate thermal resistance. They have become the predominant material for constructing aerospace prepregs.
Multifunctional epoxy prepolymers are used in the manufacture of prepregs as they possess good glass transition properties at high temperatures after curing. Several curing agents have been explored for epoxy resin-based prepregs in recent years, with different processing requirements and post-curing properties.
A critical requirement of prepregs is their fatigue and crack resistance, as these can cause catastrophic equipment failure and potential danger to the lives of crews and passengers. To overcome this issue, materials such as high molecular weight PES or PEI are added to resin composites. The induction of a two-phase morphology during curing confers significant fracture resistance in parts.
In addition to material considerations in the post-curing stage, the processing of prepregs during automated lay-up processes such as automated tape-laying requires certain material properties. Resin flow, drape, and tack are critical factors that must be considered by engineers if the final product is to be fit for service.
What is Tack?
Tack ensures the optimal positioning of materials during laminate lay-up and prevents any sliding during this stage of prepreg manufacture. Whilst there have been some important studies published on the experimental characterization of tack which can be directly translated into the production process, manufacturers tend to keep their resin formulations a secret. This means that it is difficult to correlate tack and chemical composition.
A few studies have investigated how resin formulation influences tack, with some notable success. However, tack is a complex phenomenon, and currently, there is a lack of a standardized approach in studies which hinders research in this area of aerospace engineering.
The Study
The new paper explores how resin formulation affects prepreg tack. Three parameters were selected by the authors to evaluate this relationship: epoxy prepolymers, the content of PES toughener, and the B-staging level. Three monomers were evaluated by the researchers: TGAP, TGMDA, and DGEBA. DDS was used as the curing agent in all three resin formulations.
PES toughener content was varied, with 0, 10, 20, and 30 wt% content used in samples. Different curing was used in the B-stage, with 10, 20, and 30% evaluated by the authors.
Defined isothermal heat treatment was used on the epoxy resin to achieve the B-stage. A probe tack test was used to measure tack, with complementary analysis performed on all samples to reveal the differences in rheological and thermal behavior which influence tack.
Results and Summary
Material analysis and categorization results demonstrated that all resin samples in the research exceeded conventional commercial prepreg systems. A three-to-fourfold improvement was achieved at low temperatures. A loss of tackiness produced prepregs with higher pre-curing properties and toughness. A 30 wt% incorporation of PES caused a significant reduction in tack.
20% B-stage and 10 wt% PES yielded a medium tack which is comparable to commercially available prepreg systems. Overall, the paper has demonstrated a highly efficient and reliable method for tailoring and improving the pre-cure properties of epoxy-resin-based aerospace prepreg using automated fiber placement methods.
More from AZoM: Reflection Electron Microscopy for Crystal Analysis
Further Reading
Budelmann, D et al. (2022) Tack of epoxy resin films for aerospace-grade prepregs: Influence of resin formulation, B-staging and toughening Polymer Testing 114 107709 [online] sciencedirect.com. Available at: https://doi.org/10.1016/j.polymertesting.2022.107709
Disclaimer: The views expressed here are those of the author expressed in their private capacity and do not necessarily represent the views of AZoM.com Limited T/A AZoNetwork the owner and operator of this website. This disclaimer forms part of the Terms and conditions of use of this website.