By Surbhi JainReviewed by Susha Cheriyedath, M.Sc.Aug 2 2022
In an article recently published in the journal Additive Manufacturing, researchers discussed the controlling of the anisotropic behavior of 3D printed ceramic cores from the intralayer particle distribution to the interlayer pore growth.
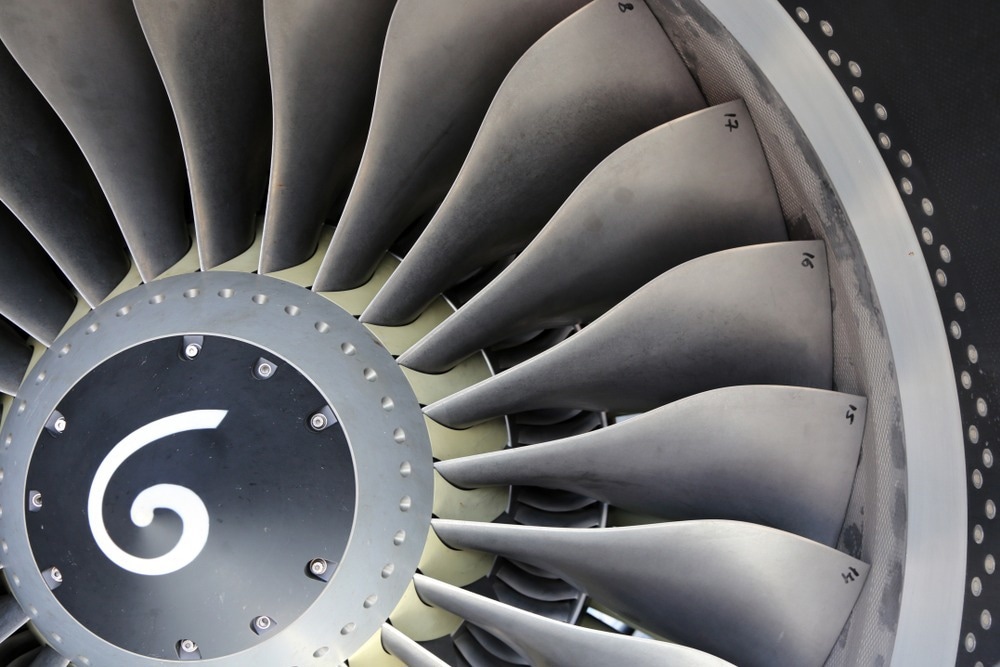
Study: Controlling the anisotropy behaviour of 3D printed ceramic cores: From intralayer particle distribution to interlayer pore evolution. Image Credit: Fasttailwind/Shutterstock.com
Background
A hollow turbine blade is a critical part of an aero-engine. The ceramic core is essential for creating a challenging cooling flow channel inside the blade during investment casting. Currently, a hot injection molding method is used to prepare ceramic cores. This method necessitates the development of numerous molds and has a considerable benefit in the manufacture of large quantities and standard simple structural cores. However, when the core structure becomes more intricate, the hot injection molding process's tooling cost and production cycle both considerably rise, limiting the amount of complicated structural cores that can be produced.
A long-running research topic, vat photopolymerization 3D printing ceramic core technology offers a fresh, cost-effective method for creating ceramic cores with intricate geometries. Researchers in related domains have made significant research in order to satisfy the necessary performance standards. Understanding the creation mechanism of layered structures and examining the impact of microstructure on anisotropy are essential steps in precisely managing the precision and attributes of vat photopolymerisation 3D printed ceramic cores.
About the Study
In this study, the authors discussed the development of ceramic core samples from the X, Y, and Z directions using vat photopolymerization 3D printing technology, and the corresponding anisotropic behavior was extensively investigated. Using a finite element simulation of the slurry which was spread during the printing process, the mechanism of core delamination was investigated.
The central layer of the slurry spread more quickly than the higher and lower surfaces, and tiny particles tended to collect more readily on the lower and upper surfaces. Fine particles made up the interface between the layers. The pores were tiny, and the interfacial sintering was compact. Large, scattered pores were present throughout the lamellar structure's interior, which was made up of coarse particles.
Additionally, during the sintering process, an evolution rule was shown by the distribution of pores in the 3D printed core. The pores traveled toward the interface between the layers as the sintering temperature increased, became enriched, and combined to produce larger pores there.
The team demonstrated that the interfacial pores created a gradient line among the porous layers when they were sintered at high temperatures. Theoretical recommendations for the regulation of the anisotropy and layered structure of 3D printed cores were provided by the combination of finite element simulation and experimentation. This encouraged the use of ceramic 3D printing technologies in the industrial sector.
The researchers examined the element distribution, microstructure, and distribution of ceramic particles in the layered structure of the ceramic core samples used in this study. The formation mechanism of the laminar structure in the printing process was illustrated using finite element simulation, and the influence law of pore distribution evolution on core anisotropy in the sintering process was described. The evolution law of pore distribution in the sintering process was also studied. The findings offered a theoretical framework for managing the accuracy and characteristics of ceramic cores produced using vat photopolymerization 3D printing. This encouraged the expansion of the industrial use of vat photopolymerization 3D printing technology.
Observations
Large pores were released from the sample when the sintering temperature was above 1300 °C, which created a porous interlayer gradient line at the interface. The small pores consolidated to the interlamellar contact when the sintering temperature was raised to 1200–1300 °C, which resulted in big pores that were randomly dispersed on the interface.
It was likely that pore coalescence occurred while the temperature was lower than 1250 °C because of the creation of the large-sized pores. No discernible changes in the pore size of the core sample sintered at 1200 °C were found in comparison to the core sample sintered at 1150 °C, and the pore size was modest. At 1500 °C, the flexural strength was greater than it was at 25 °C.
The core of the 3D-printed object had a lamellar structure. Small ceramic particles, compact interfacial sintering, and tiny pores made up the interface between the layers. Large ceramic particles with large, scattered pores were found inside the lamellar structure. Anisotropy in the core's porosity evolution, sintering shrinkage, and bending strength all come from the production of a lamellar structure.
Fine particles were more easily collected on the top and lower surfaces during the slurry spreading process because the intermediate layer of the slurry flowed more quickly than the higher and lower surfaces. During the sintering process, the distribution of pores within the 3D printed core revealed an evolution law. The holes traveled toward the interface between the layers, where they were enriched and consolidated to create huge pores as the sintering temperature rose.
The pores at the interface generated a porous gradient line between the layers when sintered at high temperatures. Theoretical recommendations for the regulation of the layered structure and anisotropy of 3D printed cores were provided by the combination of finite element simulation and experimentation.
Conclusions
In conclusion, this study used a vat photopolymerization 3D printing method to create ceramic core samples from the X, Y, and Z directions. The anisotropic behavior of these samples was extensively investigated. It was discussed how the layer structure was created and how this affected the mechanical properties. With the aid of a finite element modeling of slurry spreading throughout the curing process, the mechanism of core delamination was examined.
More from AZoM: Auger Electron Spectroscopy in the Semiconductor Industry
Disclaimer: The views expressed here are those of the author expressed in their private capacity and do not necessarily represent the views of AZoM.com Limited T/A AZoNetwork the owner and operator of this website. This disclaimer forms part of the Terms and conditions of use of this website.
Source:
Li, Q., Hou, W., Liang, J., et al. Controlling the anisotropy behaviour of 3D printed ceramic cores: From intralayer particle distribution to interlayer pore evolution. Additive Manufacturing 103055 (2022). https://www.sciencedirect.com/science/article/abs/pii/S221486042200447X