A team from the University of Naples Federico II in Italy has demonstrated the use of carbon dioxide to 3D print microfoamed strands. Their work has appeared online in the journal Polymers.
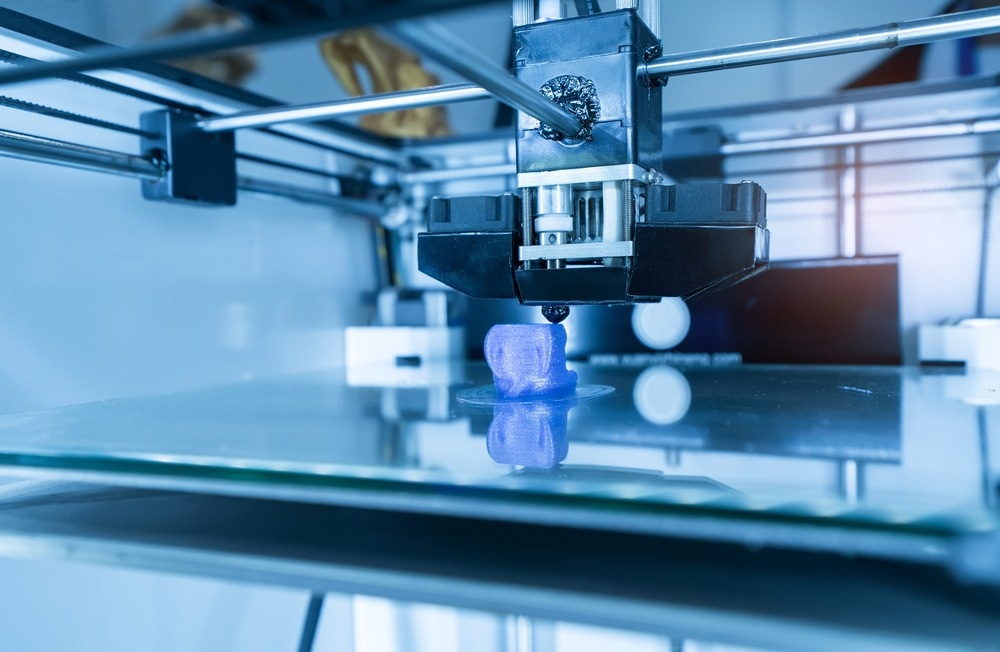
Study: Microfoamed Strands by 3D Foam Printing. Image Credit: asharkyu/Shutterstock.com
Polymeric Microfoams: Innovative Engineering Materials Inspired by Nature
Research fields including aerospace, nautical, biomedical, and sports have taken advantage of innovative, advanced materials in recent years. Amongst the many novel materials which have been developed recently, polymeric foams have proven beneficial due to their favorable mechanical and physical properties.
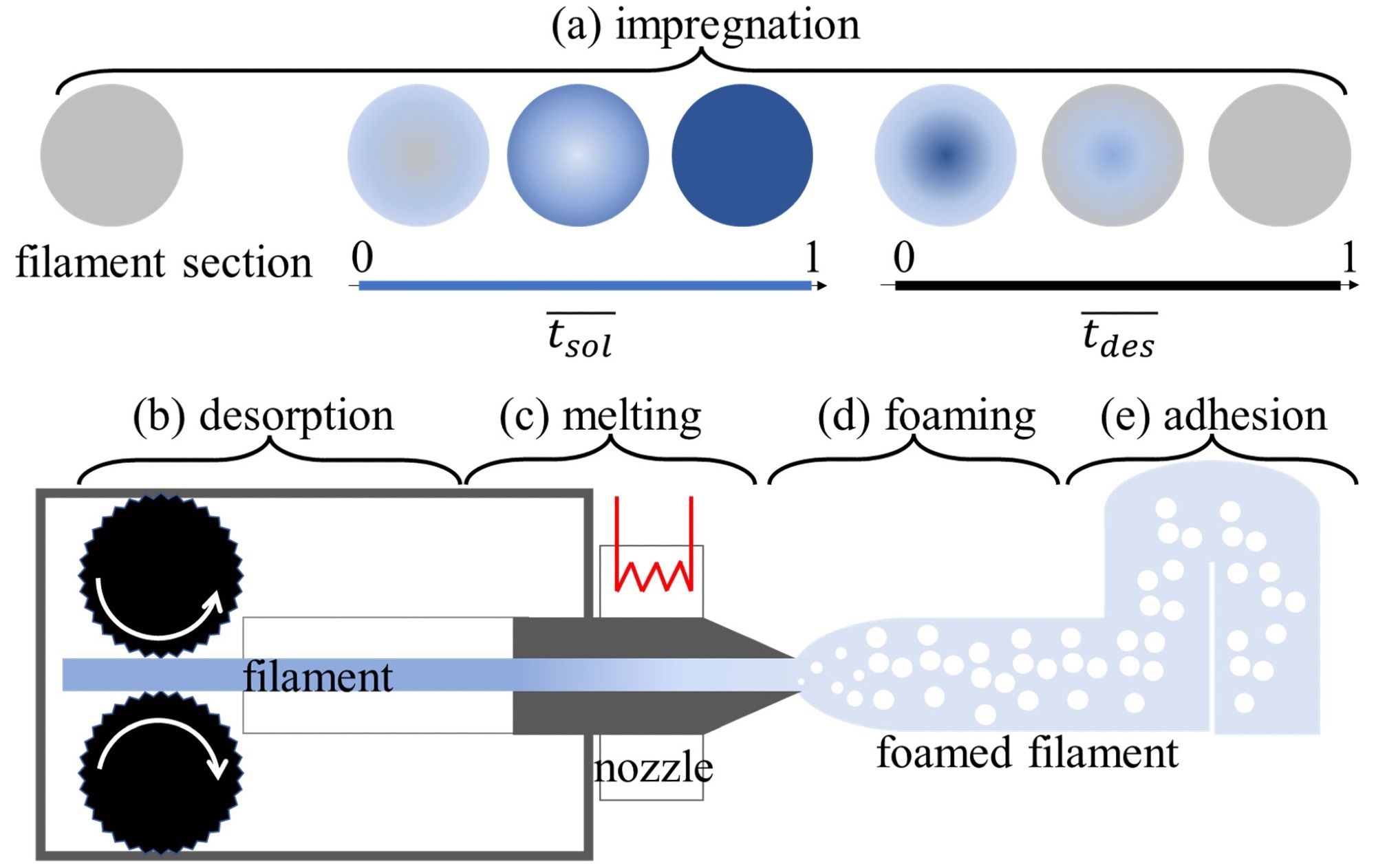
Schematic representation of the 5 steps to print foamed strands: (a) impregnation, (b) desorption, (c) melting, (d) foaming and (e) adhesion among the strands. Image Credit: Tammaro, D et al., Polymers
These novel materials possess hierarchical porous internal structures which govern their structure-property relationships. In comparison to non-hierarchical structures, these materials possess enhanced mechanical behavior and increased numbers of accessible active surfaces.
In nature, numerous examples of organic structures with hierarchical internal organization exist. In these structures, optimal efficiency and performance are achieved with minimal material requirements. Examples include honeycombs, bones, and bamboo. Natural structures have properties such as high stiffness-to-weight ratios, good energy reflection, and low thermal conductivity, which make them attractive to scientists.
3D Printing Polymeric Microfoams
Manufacturing 3D polymeric microfoams is a focus of research currently. 3D printing has been widely proposed as a technological solution for this purpose, with several advantages over conventional manufacturing techniques.
Several efforts have been made by researchers to form a hierarchical mesh and foam structures from polymers. Software is used to print filamentary struts with macro- and micro-scale pores between them. Limitations in terms of the density of extruded struts and inter-strand porosity have been encountered in current research due to printing resolution restrictions.
There have been attempts at improving this process by foaming each single strand to produce foams with high intra- and inter-strand porous structures. A two-stage approach wherein structures are printed with inter-strand pores, and then the material is batch-foamed or free-dried to produce intra-strand pores.
![(a) Comparison between the expansion ratios achieved with CO2 (this work) and acetone [2]. SEM images of the cross section of a strand foamed with CO2 (b) and acetone (c).](https://www.azom.com/images/news/ImageForNews_59741_16600366518943831.jpg)
(a) Comparison between the expansion ratios achieved with CO2 (this work) and acetone [2]. SEM images of the cross section of a strand foamed with CO2 (b) and acetone (c). Image Credit: Tammaro, D et al., Polymers
Another approach that has been recently proposed is to use discontinuous or inline solubilization of blowing agents in a one-step process. However, designing 3D polymer microfoams with innovative and fine-tuned morphologies is still problematic due to current limitations in technologies and processes.
3D foam printing itself is a recent technological innovation in the field of additive manufacturing, which is still poorly understood with several technical challenges before it can reach full commercialization. Foaming mechanisms in the printer’s nozzle are not properly understood, and difficulties exist in controlling the process.
Designing polymeric microfoams with finely controlled morphologies and pore structures is key to their commercial application in multiple cutting-edge fields of research and engineering. Achieving this will help scientists to fully exploit the rich potential of hierarchical structures, which offer a wide design space for materials scientists.
The Study
The authors have reported the green synthesis of porous, hierarchical 3D polymer microfoams using carbon dioxide to produce materials with ad-hoc bubble morphologies. The design, production, and characterization of the materials have been explored in-depth in the study. The relationship between bubble morphology and process parameters, namely CO2 concentration and temperature, are highlighted.
Microfoams were produced using bio-degradable and sustainable polymers and PLA. These polymers were then blown with carbon dioxide, creating a green and sustainable synthesis process. CO2 at 15 wt.% produces a low-density foam (40 kg/m3) with micro- and macro-scale porosities. Crystallinity content of the produced foams ranged from 5% to 45% depending on CO2 concentration, demonstrating a linear relationship.
The authors observed that the elastic modulus of foamed strands was strongly influenced by crystallinity content. The authors proposed a corrected Egli’s equation and thus explained the relationship between mechanical properties and foam density. Thus, an innovative model which demonstrated the interplay of crystallinity and properties was demonstrated in the research.
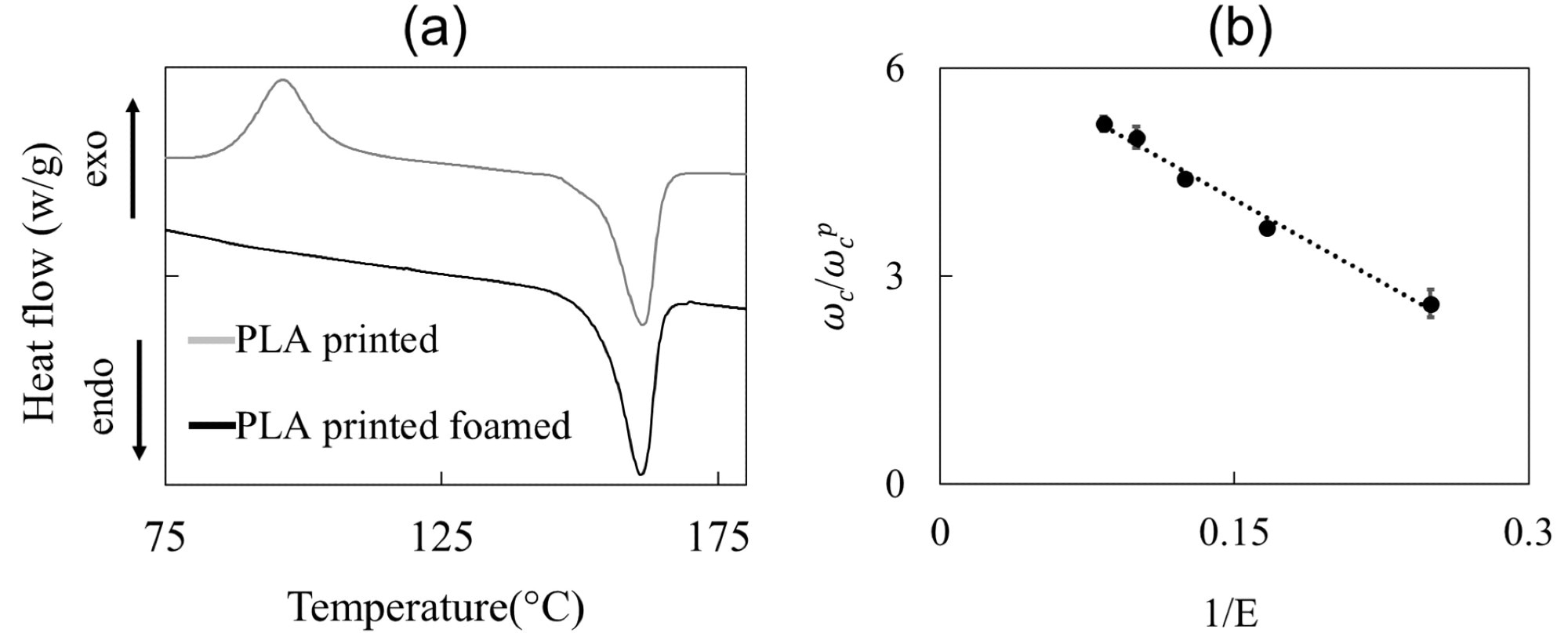
(a) DSC curves for a printed and foamed/printed PLA strand; (b) effect of expansion ratio on the crystallinity content—the dashed line is a guide for the eye. Image Credit: Tammaro, D et al., Polymers
Adiabatic cooling was discovered to be the main setting mechanism of the polymer strands. This cooling is due to rapid adiabatic expansion during the formation of the polymer microfoams. The authors proposed that understanding this effect will help to tune the process’s operating parameters to optimize final foam density.
In Summary
Polymeric microfoams are innovative bio-inspired materials that offer a wealth of benefits for industries such as biomedicine, aerospace, and textiles. Their complex, porous, hierarchical internal morphologies outperform conventional non-hierarchical materials.
To produce these materials, there is growing interest in applying 3D printing methodologies, but the field is still in its infancy and poorly understood, with processes difficult to control. The new study in Polymers has demonstrated a facile, green synthesis route that could revolutionize the field of 3D printed polymer microfoams. Whilst many challenges still exist, the field is an exciting one.
Further Reading
Tammaro, D., Villone, M.M. & Maffettone, P.L (2022) Microfoamed Strands by 3D Foam Printing Polymers 14(15) 3214 [online] mdpi.com. Available at: https://www.mdpi.com/2073-4360/14/15/3214
Disclaimer: The views expressed here are those of the author expressed in their private capacity and do not necessarily represent the views of AZoM.com Limited T/A AZoNetwork the owner and operator of this website. This disclaimer forms part of the Terms and conditions of use of this website.