By Surbhi JainReviewed by Susha Cheriyedath, M.Sc.Sep 14 2022
In an article recently published in the journal Additive Manufacturing, researchers discussed the rapid sintering of ceramic components fabricated through high-strength lithography-based additive fabrication.
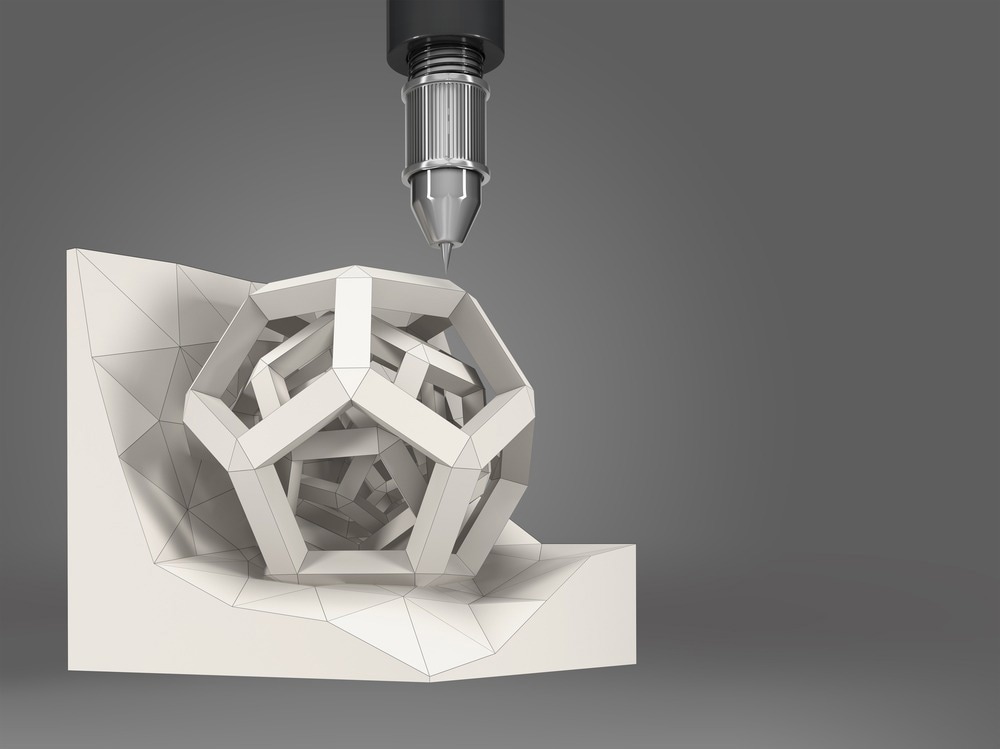
Study: High-strength lithography-based additive manufacturing of ceramic components with rapid sintering. Image Credit: Iaremenko Sergii/Shutterstock.com
Background
With the introduction of ceramic additive manufacturing (AM), there is a possibility for wholly new or significantly enhanced solutions to be revealed for cutting-edge automotive, environmental, aerospace, and biological applications. Of all the available AM processes, lithography-based ceramic manufacture (LCM) is currently one of the most well-known.
The entire densification of ceramics requires sintering following AM, in contrast to the final, fully consolidated output of the AM process for metals and polymers. Sintering requires a lot of time and effort. Up until this point, the process of densifying AM ceramic parts has primarily been carried out in conventional furnaces under typical sintering conditions. It is, therefore, still difficult to manufacture pore-free, fine-grained ceramics, especially when using traditional slow sintering methods.
Advanced sintering procedures have come under scrutiny as a means of reducing sintering time and temperature while promoting quick densification with less total energy usage. Recently, a method known as ultra-fast high-temperature sintering (UHS) was unveiled. The UHS approach has only been used on small and extremely thin specimens because of the substantial heat gradients involved and related structural issues.
Radiation-aided sintering (RAS) is a promising technique that could be used to sinter AM components. Recent findings have demonstrated how RAS can facilitate the sintering of lead-free, sub-micrometer-sized piezoelectric functional ceramics with better dielectric characteristics or zirconia nanoceramics. Yet no attempt has been made to quickly consolidate 3D-printed parts using the RAS approach.
About the Study
In this study, the authors described a method for quick sintering of ceramic components with complicated forms at 300-450°C/min using lithography-based additive manufacturing of alumina ceramics. Rapid radiation heat transfer was used to control densification and limit grain formation to create highly dense, fine-grained microstructures. In comparison to traditionally sintered reference parts, the high mechanical strength of 810 MPa and toughness of 4.3 MPa m1/2 of additively generated alumina sintered at 1600 °C within two minutes was superior.
The team showed that the radiation-assisted RAS method could successfully sinter lithography-based additively created alumina ceramics in a matter of minutes as opposed to hours. A spark plasma sintering (SPS) setup was modified to enable the sintering of complex geometries, such as a turbocharger engine rotor, without the need for direct pressure or current on the ceramic sample. This sintering process also produced fine-grained microstructures of 1 μm size with densities of 99% and the ability to quickly sinter complicated 3D printed items with an energy input of 1 MJ as opposed to 25 MJ for traditional sintering.
The researchers looked at how the maximum sintering temperature and time for rapid sintering processing affect the characteristics and microstructural evolution of 3D-printed ceramics. The quick sintering of 3D ceramic components with regulated microstructure and characteristics was made possible by the employment of strong radiation as a special source of the thermal transfer mechanism.
Observations
To print the alumina components, the used photosensitive suspensions needed a polymer binder that was 50% by volume. Upon the removal of the binder at around 430 °C, a green density of about 60% was attained. With a dwell time of two minutes, the ceramic turbocharger engine rotor solidified at a maximum temperature of 1600 °C. The achieved relative density was approximately 97%. For the RS1 and CS samples, toughness measurements of 3.8 MPa m1/2 and 4.3 MPa m1/2, respectively, were made. Between 1300 and 1400 °C, grains were reorganized due to enhanced volume diffusion and a low dihedral angle.
The relative density increased to greater than 99% at higher temperatures of 1600 °C and dwell periods of four and eight min, with an average tiny particle size of 1.5 μm. Longer dwell periods resulted in an increase in relative density from 68% to 82%. While the relative density increased from two to eight minutes of dwell time, the hardness marginally declined from 23 to 21 GPa. The grain size varied between 600 nm and 1.5 μm between the smallest dwell times of two minutes and the greatest stay times of eight minutes. In this case, the influence of grain size outweighed the hardly noticeable disparity in densities between the two microstructures.
According to the Griffith hypothesis of brittle fracture, the strength increased significantly as grain size decreased.
Conclusions
In conclusion, this study showed that RAS is a practical technique for accelerating the consolidation of complex-shaped ceramics produced through 3D printing. The team mentioned that RAS offered enhanced engineering of dense and robust ceramic architectures for cutting-edge applications made from commercial feedstocks when paired with 3D printing. The ability to densify and sinter 3D-printed alumina components while maintaining their fine-grained, homogenous, and dense microstructure with grain size less than 500 nm was demonstrated. This was an order of magnitude finer than their traditionally sintered ceramic counterparts with grain sizes of 5.3 μm.
The authors stated that this discovery paves the way for the quick sintering of highly dense, intricately structured ceramic structures with customized microstructures and characteristics. They believe that this approach can be used with a variety of material systems, including electroceramics, optical materials, magnetic materials, thin films, catalytic (porous) materials, and biomedical materials.
More from AZoM: What are Biopolymer-Based Hydrogel Electrolytes?
References
Hofer, A-K., Kocjan, A., Bermejo, R., et al. High-strength lithography-based additive manufacturing of ceramic components with rapid sintering. Additive Manufacturing, 103141 (2022). https://www.sciencedirect.com/science/article/pii/S2214860422005309
Disclaimer: The views expressed here are those of the author expressed in their private capacity and do not necessarily represent the views of AZoM.com Limited T/A AZoNetwork the owner and operator of this website. This disclaimer forms part of the Terms and conditions of use of this website.