A paper recently published in the journal Polymers reviewed the feasibility of using tannin-based polymeric foams as a greener alternative to non-renewable rigid polymeric cellular foams, specifically for building insulation.
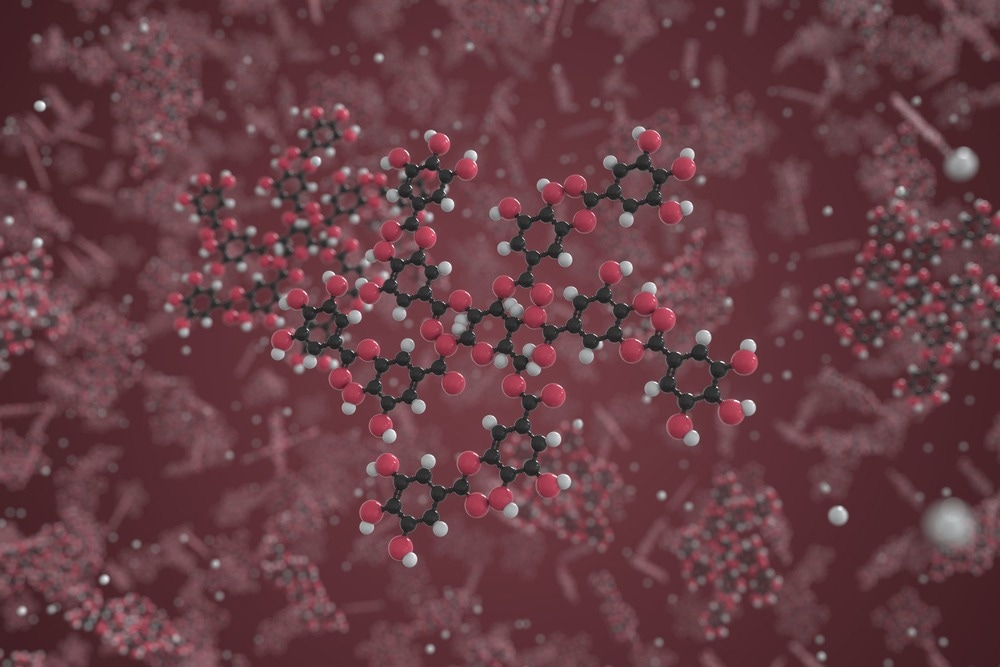
Study: A Review of Rigid Polymeric Cellular Foams and Their Greener Tannin-Based Alternatives. Image Credit: Irina Anosova/Shutterstock.com
Background
Polymeric foams, both rigid and flexible, are composed of several macromolecules, such as polystyrene, ethylene-vinyl acetate, polyimide, melamine–formaldehyde, phenol-formaldehyde (PF), polyvinyl chloride, polyethylene, polypropylene, and polyurethane (PUR). These foams are used in different applications based on the limitations of weight and price and chemical and physical compatibility.
Among these polymeric foams, cellular PUR and phenolic materials are commonly utilized for building insulation. However, rising environmental concerns regarding the use of these polymeric foams have necessitated the identification of bio-based alternatives.
Tannin-based bio-sourced foams are increasingly considered a suitable alternative to cellular PUR and phenolic foams. The design and production of tannin-based foams have gained considerable attention in recent years.
In this paper, the authors reviewed the different polymeric foams used for building insulation purposes and evaluated the feasibility of using tannin-based foams as an alternative to the existing non-renewable options.
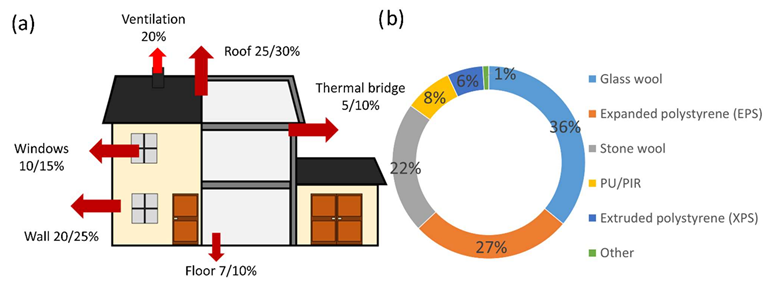
(a) Heat losses for a standard building in France, (b) European insulation market in 2019. Image Credit: Marie, Z et al., Polymers
Rigid Polymeric Foams
Polyurethanes
The rigid cellular material production is dominated by polymers derived from N=C=O functional group-based isocyanate chemistry, such as PURs. PURs constitute a family of polymers obtained by polyaddition of urethane units.
The primary PUR polymerization reaction occurs between polyols, such as polyether polyols, and isocyanates, such as toluene diisocyanate and methylene diphenyl diisocyanate (MDI).
Catalysts can be used to control specific foaming properties, retard the reaction for certain applications, or enhance less reactive reactions while foaming agents can be used for the expansion of the polymer matrix.
Crosslinking agents, flame retardants, and surfactants are the commonly used additives in PUR formulations. Additionally, additives such as fibers are explicitly used to increase the dimensional stability and strength of the matrix.
PUR foams possess an extensive range of fire resistance, water absorption, and thermal and mechanical properties due to the diversity of the PUR formulations. These foams are used in insulating materials for heaters, buildings, and automotive parts.
Polyureas (PUAs)
PUA foams are composed of urea units and are cheaper compared to polyisocyanurate (PIR) and PUR foams. Carbonates, imides, amides, polyisocyanurates, and urethanes are also used in PUA foams. PUA foams can also be based on isocyanate chemistry, including polymeric MDI (pMDI) or MDI.
PUA foams possess an extremely low density, higher conductivity than PUR foams, and good insulating properties. Additives such as fibrous fillers and fire retardants can be added to harden the polymer network and ensure fire resistance, respectively. PUAs are used in blocks or sprayed for building insulation.
Water-based formulations were developed for rigid or semi-rigid insulation boards or sprayed insulation devices, which is a less expensive method to expand the foam compared to using a foaming agent.
Polyisocyanurates (PIRs)
PIR foams are formed through the cyclotrimerization reaction between high-index isocyanates in a ring configuration. Foaming agents used for PUR chemistry can also be used in PIR formulations. Additionally, catalysts such as quaternary ammonium salts and tertiary amines, fillers, flame retardants, and surfactants can be incorporated into PIR formulations.
PIR foams are lightweight and possess good strength, rigidity, thermal behavior, and fire resistance. These foams can be used for heating systems and thermal insulation. However, PIR foams release hydrogen cyanide upon combustion, which is toxic to human health.
Phenolic-Based Formulations
PF or polyphenolic foams are obtained through the polymerization of phenolic monomers with aldehydes, specifically formaldehyde. Initially, the crosslinking reaction occurs between aldehydes and phenolic compounds, followed by the foaming of the polymer mixture.
Epoxy resins or bioresources can be added to PF formulations to improve the properties of PF foams. However, acidic vapors released by PF foams over time can corrode adjacent metals, which has limited their use in practical applications.
PF foams possess better thermal conductivity compared to PUR foams and exceptional fire resistance. These foams are primarily used as insulators in heating installations and refrigeration. Although PFs are brittle in nature, their mechanical performance can be improved by adding fillers such as fibers.
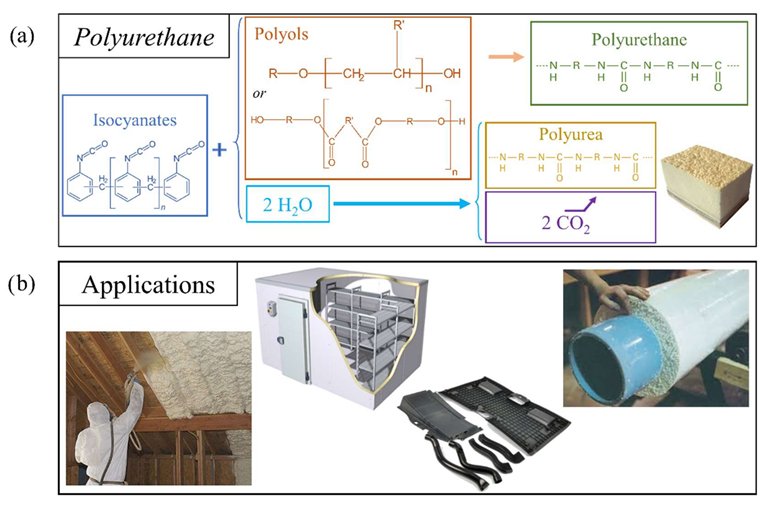
(a) Reaction diagram for PUR and PUA systems, containing (from left to right) the isocyanate precursors, some examples of polyols for the formation of PUR, and, in the presence of water, the formation of PUA and the consequent liberation of CO2; (b) examples of PUR foam applications, such as the thermal insulation of buildings, different polymeric devices, and thermal insulation of pipes. Image Credit: Marie, Z et al., Polymers
Use of Bio-based Reagents in Polymeric Foams
Several biosourced PUR foams were developed by replacing petroleum-based reagents. For instance, vegetable oils such as sunflower oil, soybean oil, palm oil, and lignin-derived compounds were used as alternative polyols.
Similarly, plant-based fibers and fillers were used as additives. Lignin can be incorporated in PF or PUR blends as it is also considered a phenol source. Additionally, tannins, another plant-based phenol source, can be used as substitutes for PF resins and foams.
The final foam quality primarily relies on the foam's rheological, thermal, and mechanical properties, which depend on crosslinker and precursor selection. Moreover, the selection of proper processing methods, gas, and foaming method, including physical foaming, mechanical foaming, and chemical foaming, is also essential to obtain a final material with satisfactory properties.
End of Life and Recycling
Waste generated due to polymeric foams is conventionally disposed of using two major waste management methods including landfill and incineration. Heat and ash generated during incineration can be used to generate electricity and as fillers in concrete, respectively.
In landfills, polyester-based PUR is more susceptible to decomposition compared to polyether-based PUR in an aerobic environment as polyether possesses a decomposition-resistant chemical structure.
However, waste disposal using these methods has increased concerns regarding soil and groundwater pollution and greenhouse gas production, which has increased the importance of biodegradation mechanisms and polymer matrix removal during recycling for second-life applications.
Recycling and Reuse
Chemical recycling and physical recycling are more efficient methods in the long term for the disposal of polymer foams. Thermal or mechanical processes are used to treat the PUR and PIR polymers in physical recycling. Although chemical recycling is the most efficient recycling method, the technology is extremely complex for commercial implementation.
Catalytic hydrogenation of PUR is another recycling strategy developed in recent years. Biodegradation by biochemical and genetic pathways has gained considerable attention to recover depolymerized chemicals, which can be reused as polyols during the formulation of new materials.
Tannin–Furanic Foams (TFFs)
TFFs are primarily bio-based formulations in which the initial mixture reacts and self-organizes into a three-dimensional (3D) polymer chain network through cross-linking. Eventually, the rigid foam is obtained when the polymerization is completed after the curing step.
Wood tannins, furfuryl alcohol, formaldehyde, catalyst, and foaming agent are used in the tannin-based foam manufacturing process. Tannins are primarily phenolic compounds obtained from different plant tissues, specifically the bark and wood of trees.
Condensed tannins have gained significant attention as an alternative to phenolic constituents in PUR or PF resins. These tannins can be obtained from several trees, including larch, spruce, and mimosa.
Tannins react with aldehydes to form a polymer through catalysts or under proper pH conditions. Tannins can self-condense to form complex polymer networks. Additionally, tannins react with added furfuryl alcohol to generate heat for the physical blowing process.
Aldehydes, such as formaldehyde, are added as curing agents for crosslinking reactions. Diethyl ether is utilized as a physical blowing agent in standard tannin-based foam formulations owing to its lack of reactivity with other components and low boiling point.
Different alkaline and acidic catalysts are added to facilitate the polymerization reaction under proper pH conditions based on the formulation. Moreover, several additives, such as isocyanates, fillers, and plasticizers, can be used to enhance specific properties. For instance, glycerol can be added to improve the elasticity of the TFFs, while hexamine can be used to improve rigidity.
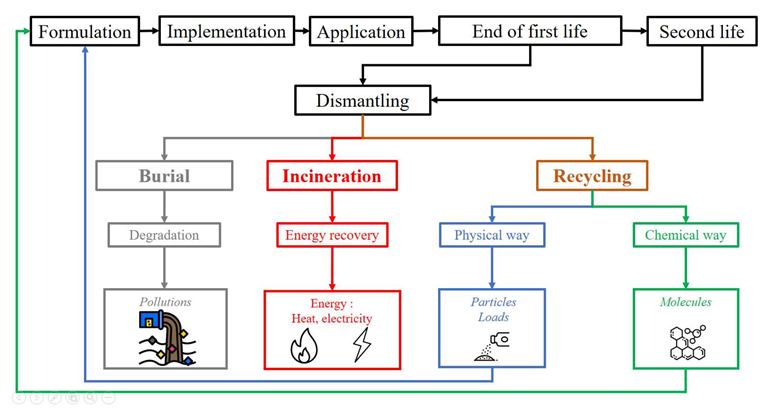
Life cycle of rigid cellular materials. Image Credit: Marie, Z et al., Polymers
Physical Properties of TFFs
TFFs are lightweight, and their typical density ranges from 0.055 to 0.075 g cm−3. The density of the foams can be controlled by varying the amount of foaming agents, such as diethyl ether, added to the formulation.
Additionally, tannin foams demonstrate exceptional insulation properties with an extremely low thermal conductivity between 0.032–0.050 W ·m−1 ·K−1. However, the thermal properties of TFFs depend on the structure homogeneity.
The polymerization degree of the matrix and the internal organization of cells influence the mechanical properties of TFFs. TFFs are rigid materials with more than 0.08 MPa compressive strength.
The addition of plasticizers or hardeners can change the mechanical behavior of the foam. Moreover, TFFs display extremely good fire resistance without the addition of flame retardants. These properties make them a suitable alternative for building insulation.
Conclusion
To summarize, TFFs showed a better or similar performance compared to commonly used polymeric foams based on petrochemical feedstocks, including PF, PIR, PUA, and PUR, in terms of density, thermal conductivity, compressive strength, and fire resistance.
However, the high friability of TFFs is one of the major challenges of using these foams for engineering applications. Additionally, more research is required to investigate the recycling and dismantling of tannin-based foams.
Disclaimer: The views expressed here are those of the author expressed in their private capacity and do not necessarily represent the views of AZoM.com Limited T/A AZoNetwork the owner and operator of this website. This disclaimer forms part of the Terms and conditions of use of this website.
Source:
Marie, Z., Celzard, A., Fierro, V. et al. A Review of Rigid Polymeric Cellular Foams and Their Greener Tannin-Based Alternatives. Polymers 2022. https://doi.org/10.3390/polym14193974.