By Surbhi JainReviewed by Susha Cheriyedath, M.Sc.Oct 3 2022
In an article recently published in the journal Additive Manufacturing, researchers discussed the building and finishing techniques for deconstructed parts scheduling in additive manufacturing (AM).
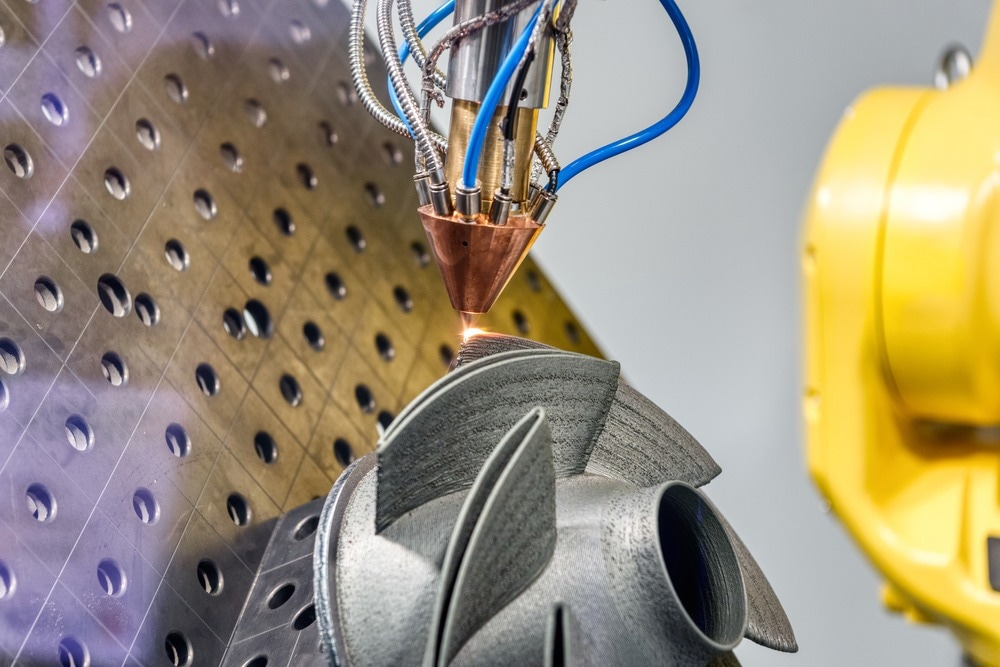
Study: Scheduling of build and post processes for decomposed parts in additive manufacturing. Image Credit: Nordroden/Shutterstock.com
Background
Different from traditional manufacturing, additive manufacturing (AM), also known as three-dimensional (3D) printing, is the joining of materials to create items from 3D model data, frequently layer by layer. AM has been used in a wide range of industries during the last few decades. By demonstrating the potential of highly customized and individualized products, AM has set the path for the future of manufacturing. The literature demonstrates that process engineering, product engineering, and production engineering have all worked on AM systems. Recent studies on AM have focused on revisiting and developing conventional methods for production planning, including scheduling.
A build process is a single cycle of processing during which one or more objects are assembled in the AM machine's process chamber. To ensure that the finished product has the appropriate attributes, post-processing is used as one or more process steps after the build phase. The build process is mostly taken into account while scheduling or planning production for AM. Although post-processing affects production stage performance in general, it has received little attention in AM literature. A thorough approach to production planning must take into account both the build process and post-processing.
About the Study
In this study, the authors discussed the AM systems based on flow-shop, including the build and post-processes. Coloring, cutting, and assembling procedures were studied under post-processing. Three scheduling policies, namely, one-for-one job, all-for-one job, and hybrid, were introduced. Throughout the same build process, many parts were simultaneously manufactured. The second policy required each part to be assigned to a certain job, which caused parts to be constructed one at a time during the build process. To reduce the makespan for each policy, the mixed-integer programming (MIP) paradigm was suggested.
The team applied the scheduling optimization for AM to a variety of applications in computational experiments using test models, including scheduling policies, numerous parts, and several AM machines. One of the key comparisons showed that the MIP model of hybrid policy, which shortened the makespan by 27.68%, was favored over the all-for-one-job policy.
The study quantitatively demonstrated that, when carefully taking into account build and post operations, packing was not a significant influence in lowering the makespan. A mathematical method was suggested for the optimization of the scheduling for AM. The mathematical method reduced the makespan of AM systems with many stages that covered the construction and post-operations.
The researchers offered typical scheduling policies and suggested the associated scheduling models. Production planning for complex products like toy figures could be done using the mathematical model for scheduling optimization. This study looked into whether component decomposition was necessary for conjunction with scheduling models in terms of cutting down on the AM systems' makespan.
Observations
The makespan of MIP1 was reduced by 36.35% when 3 machines were used for 6 pieces as opposed to using just one. The makespan of MIP1 was reduced by 53.02% when 3 machines were taken into account for 6 pieces as opposed to the worst scenario. However, when the number of AM machines was increased, the difference between MIP1 and MIP3 was quite small. When MIP1 and MIP3 were compared, M1's decrease rate differed by 5.1%, while M3's difference was only 0.6%. The makespan decrease rate was 25.92% for 2 parts and 42.48% for 6 parts. The assembly sequence diagram for the 10 disassembled parts had 230 nodes and 50,400 sequences. Regression models had R-squared values of 0.72 and 0.76, respectively.
While contrasting the three schedulers, MIP1 offered a better outcome than MIP2 and MIP3. When fully taking into account build and post operations, the results quantitatively demonstrated that packing was not a significant influence in lowering the makespan. The removal, coloring, and assembly procedures used in the MEX process were the first three exemplary post-processes. Meta-heuristics like the tabu search, evolutionary algorithm, and simulated annealing could be used to handle a high number of pieces in the scheduling optimization.
Conclusions
In conclusion, this study discussed scheduling optimization for build and post operations in AM. According to the hybrid, all-for-one, and one-for-one rules, three MIP schedules (MIP1, MIP2, and MIP3) were created. The scheduling optimization for AM was applied to a variety of instances in computational studies. In the depicted cases, the MIP schedulers were used to explore four test models. To shorten the makespan, it was desirable to fabricate several components as opposed to the full original part.
The authors mentioned that this study's primary contribution was to address the post-processing of AM in the improvement of scheduling.
More from AZoM: How Far Can Semiconductor Manufacturing Be Automated?
Further Reading
Oh, Y., Cho, Y., Scheduling of build and post processes for decomposed parts in additive manufacturing. Additive Manufacturing, 103164 (2022). https://www.sciencedirect.com/science/article/abs/pii/S221486042200553X
Disclaimer: The views expressed here are those of the author expressed in their private capacity and do not necessarily represent the views of AZoM.com Limited T/A AZoNetwork the owner and operator of this website. This disclaimer forms part of the Terms and conditions of use of this website.