Writing in the journal Materials, a team of scientists from Imam Abdulrahman Bin Faisal University and King Fahd University of Petroleum & Minerals in Saudi Arabia has investigated the surface and physiomechanical properties of 3D-printed zirconia, a common ceramic material used in everyday applications.
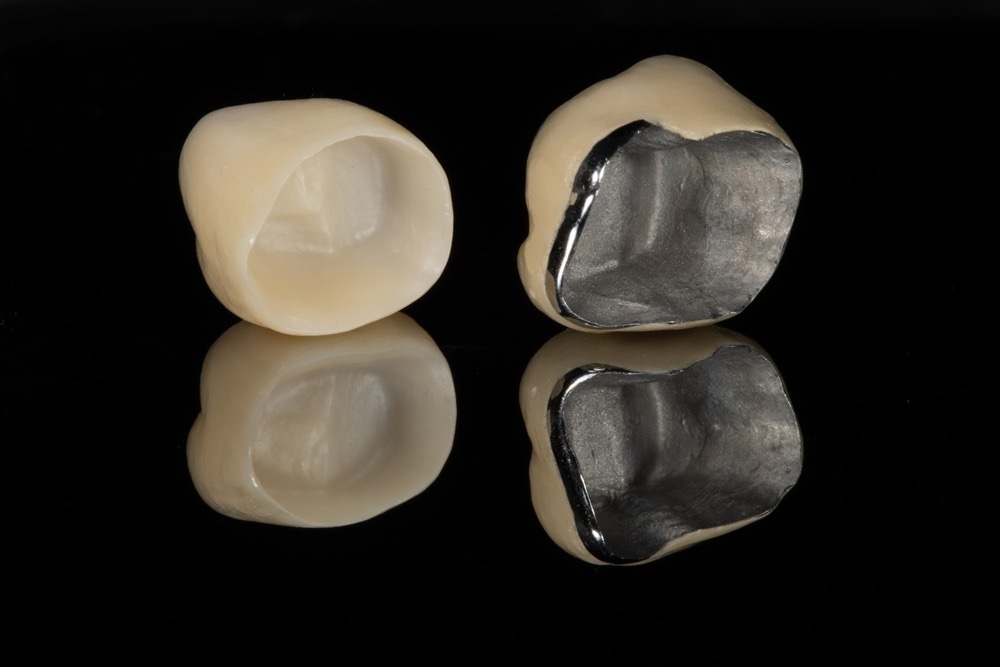
Study: Physiomechanical and Surface Characteristics of 3D-Printed Zirconia: An In Vitro Study. Image Credit: JH Lee/Shutterstock.com
Ceramics: A Class of Key Medical and Dental Materials
Ceramics have been widely applied in products such as dental implants, medical devices, and other key non-medical industries in the past few decades. Their growing use in the dental industry as implants, for instance, plays a key role in restoring lost functions and replacing damaged tissue, improving the quality of life of many patients across the world.
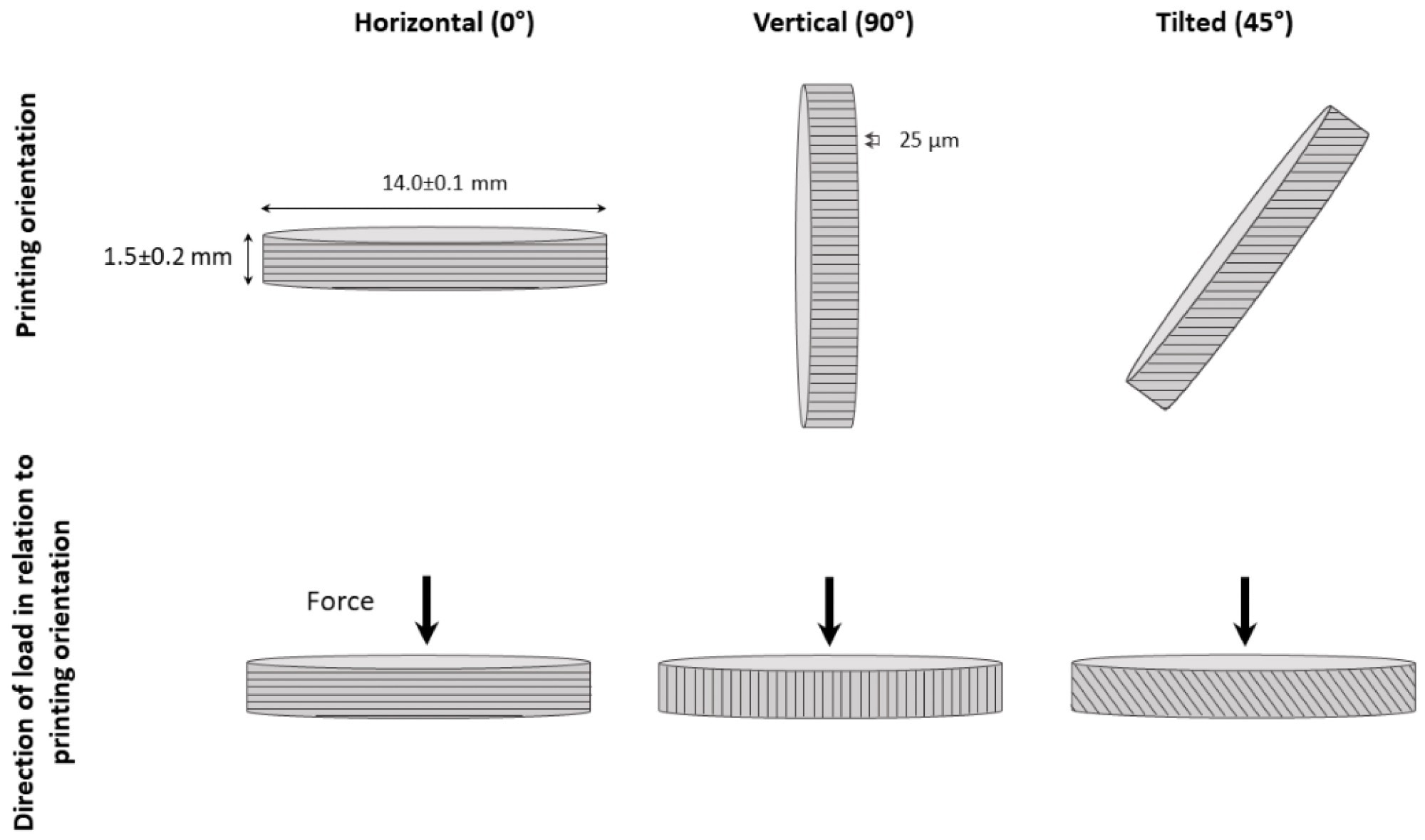
Schematic representation of the specimen printing orientation and relation to the applied load. Image Credit: Abdualsaud, R et al., Materials
Key benefits of dental ceramics are their outstanding biocompatibility, stability, excellent mechanical properties, and chemical resistance. Moreover, they possess similar optical properties to natural teeth, which gives ceramics a huge aesthetic appeal for patients.
Amongst the numerous ceramics that have been evaluated over the years for dental prostheses, dental zirconia has emerged as a suitable candidate. This is due to its advantageous qualities, such as good aesthetics, microbial adhesion resistance, superior mechanical properties, and adequate radiopathy. Zirconia is especially effective as a prosthetic in areas with a high occlusal load.
Dental zirconia is typically fabricated by adding yttrium oxide to produce 3Y-TZP. This polycrystalline-structured zirconia has a unique ability wherein it can undergo transformation toughening upon stress induction. This is achieved via phase changes from tetragonal to monoclinic phases. An increase in the crystal structure volume of the material aids this transformation and helps to stop crack propagation.
Additive Manufacturing: An Emergent Technology Which Can Aid Better Ceramic Design
The increasing demand for advanced dental ceramics such as zirconia has facilitated the need for new and improved production methods. Conventionally, subtractive manufacturing methods such as milling are used to produce these materials. As the word “subtractive” suggests, these methods involve the removal of material from a ceramic block with the aid of computer design software and hardware.
These conventional methods have serious limitations, however. Firstly, they produce significant amounts of waste materials that cannot be reused, and consequently, this increases the cost and energy demands during production. Additionally, traditional manufacturing methods cannot produce structures with complex internal geographies, which are increasingly in demand for multiple applications.
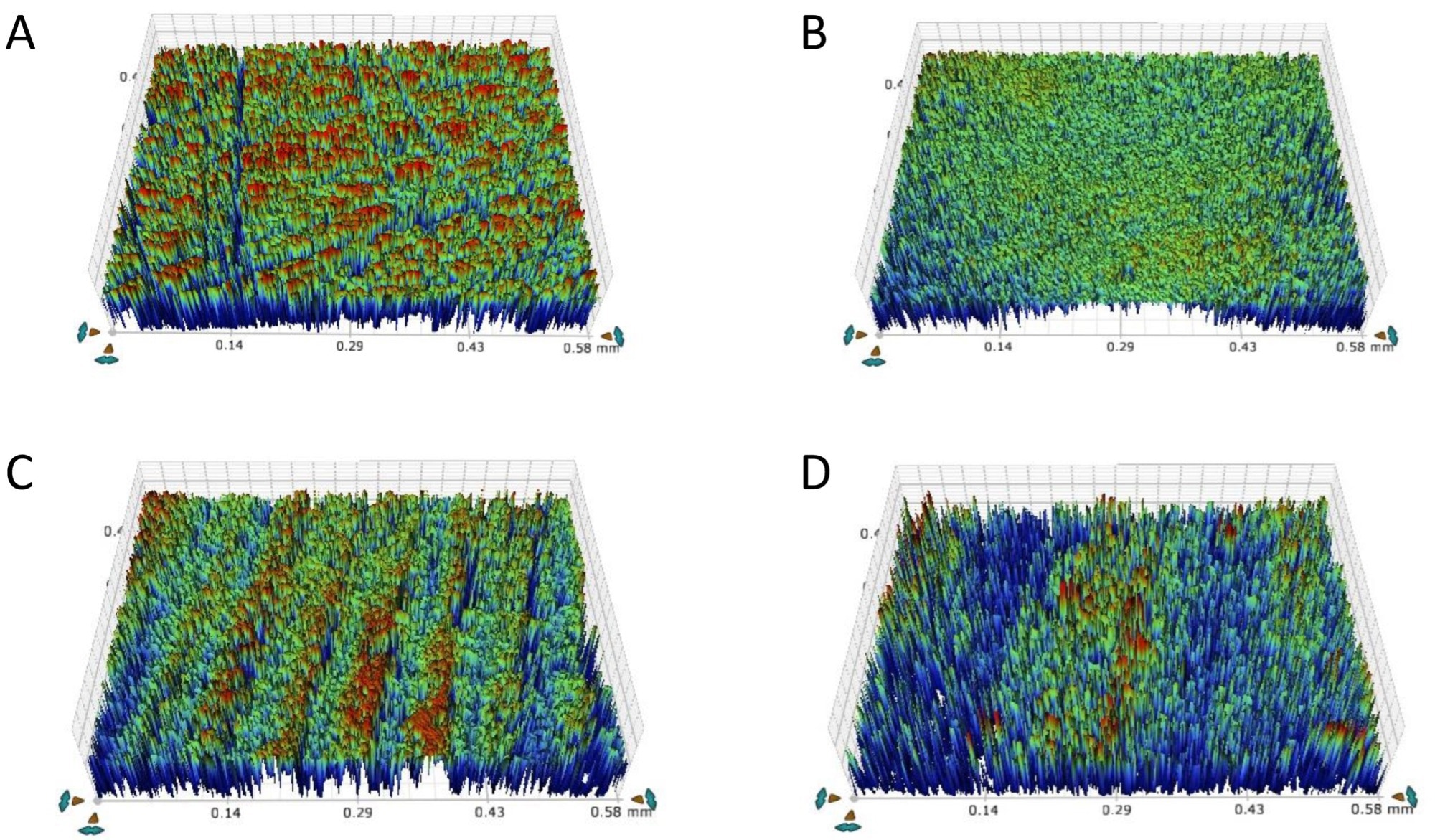
Images of surface roughness of specimens. (A) Milled, (B) horizontal, (C) vertical, and (D) tilted. Image Credit: Abdualsaud, R et al., Materials
Another key disadvantage of milling techniques is the progressive wear of products, which facilitates the need for periodic replacement of dental prosthetics. Consequently, the cost of dental treatment increases, and most importantly, this seriously impacts the patient’s quality of life.
Additive manufacturing is an emergent, disruptive technology that offers significant benefits for the design and manufacturing of dental zirconia prosthetics as well as numerous other key applications in nearly every industry. 3D printing methods reduce waste, enhance design freedom, and are more appropriate for the production of multi-material ceramics, metals, and polymer-based products.
Whilst the potential of additive manufacturing is clear, early reports on the fabrication of dental zirconia-based implants and prosthetics have demonstrated key challenges such as surface pores, uneven shrinkage, and microcrack formation. Parameters such as printing speed and orientation can impact the quality of final products. These challenges require intensive research on improving 3D printing techniques.
The Paper
The new paper in the journal Materials has reported the investigation of mechanical, surface, and physical properties of 3D-printed zirconia in order to improve additive manufacturing processes which could eventually completely replace conventional subtractive methods such as milling.
The study makes some null hypotheses. Firstly, the research proposes that differing printing orientations do not influence the tested properties (grain size, crystalline structure, porosity, density, wettability, surface roughness, biaxial flexural strength, and microhardness) of the 3D-printed zirconia. Secondly, the paper hypothesizes that specimens of 3D-printed zirconia will display comparable properties and behavior to milled zirconia specimens.
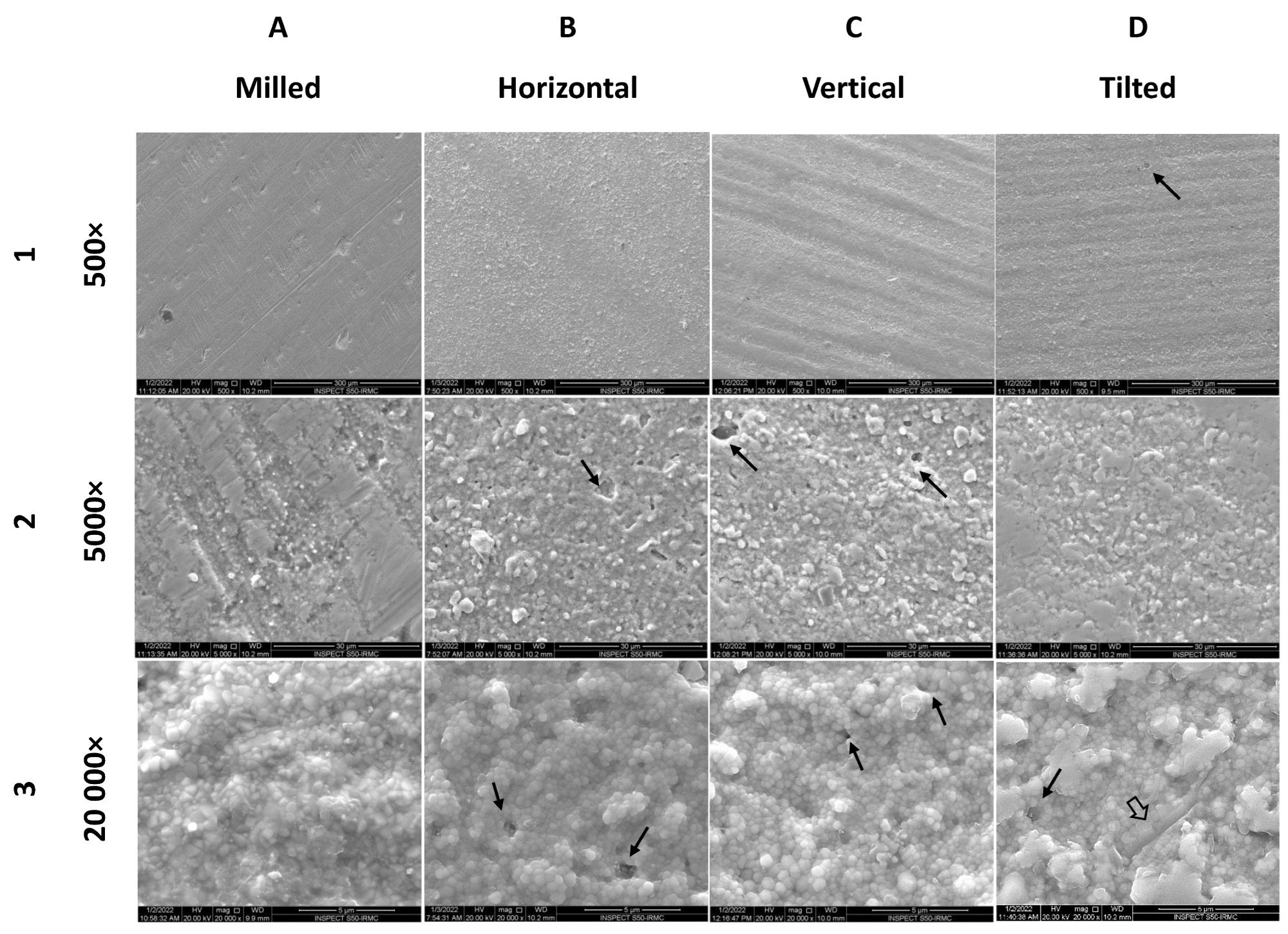
Surface characteristics of representative specimens from each group (1A–1D) at 500×, (2A–2D) at 5000×, and (3A–3D) at 20,000×. Image Credit: Abdualsaud, R et al., Materials
Three different printing orientations were analyzed, and the results were compared with milled zirconia. Eighty total specimens were produced for evaluation. Specimens were milled in the green stage and sintered according to manufacturer specifications. Analytical methods such as XRD and SEM were employed to characterize the specimens.
Study Conclusions
Experimental results and analysis revealed the properties of 3D-printed zirconia and the comparison of this material with milled zirconia. Printing orientation influences the biaxial flexural strength and wettability of 3D-printed specimens. However, in terms of the minimum strength required for substructure and monolithic restoration involving molars, the 3D-printed zirconia specimens satisfied this key dental requirement.
Microstructure, porosity, and density were comparable for all groups of zirconia, which is important for the quality and performance of dental implants and prosthetics. Furthermore, the study revealed that horizontally printed specimens display the lowest wettability whilst tilted specimens possess higher roughness values than milled zirconia samples.
In summary, the research has successfully characterized the properties of 3D-printed zirconia, which will have important implications for future research in the field of dental ceramic prosthetics. The study has recommended that future research focuses on areas such as evaluating a wider range of zirconia brands and tests aspects related to optical properties, bonding strength, and anti-microbial properties.
Further Reading
Abdualsaud, R et al. (2022) Physiomechanical and Surface Characteristics of 3D-Printed Zirconia: An In Vitro Study Materials 15(19) 6988 [online] mdpi.com. Available at: https://www.mdpi.com/1996-1944/15/19/6988
Disclaimer: The views expressed here are those of the author expressed in their private capacity and do not necessarily represent the views of AZoM.com Limited T/A AZoNetwork the owner and operator of this website. This disclaimer forms part of the Terms and conditions of use of this website.