Damage that is inflicted on industrial parts is costly, leads to delays, and could put plant workers at risk. However, researchers from Japan have now replicated fracture initiation in materials that share a specific physical feature and are extensively utilized throughout industrial, scientific, and domestic applications.
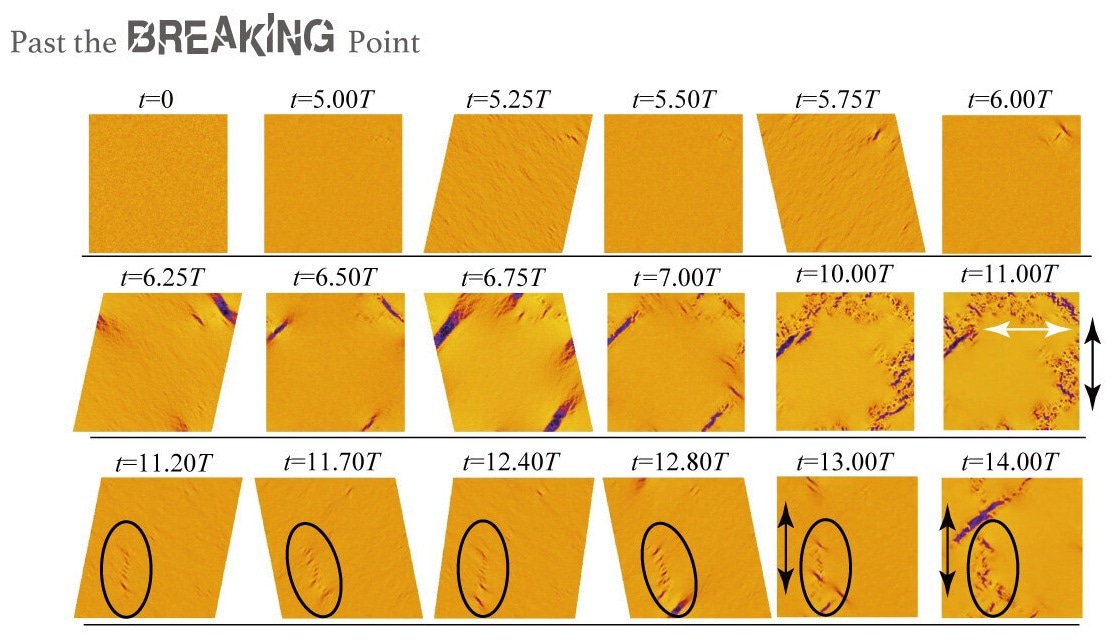
Image Credit: University of Tokyo
Their work revealed amazing results that might aid in preventing the damage of industrial parts.
If someone has ever been bored in a meeting and attempted to occupy themselves with a metal paperclip to pass the time, they may have observed something astounding. Even though the paperclip may initially seem flexible and reverts back to its initial shape, after a sufficient number of cycles, the paperclip, more often than not, tends to suddenly snap.
This is an instance of “fatigue,” where defects and cracks develop as an object is subjected to cyclic loading and unloading of stress. In several industrial applications, material fatigue is a prime concern, particularly for airplane or machine parts that go through several cycles of stress but for which an abrupt failure can be disastrous.
Correspondingly, getting a better comprehension of the fundamental process of material fatigue can have considerable advantages, particularly for non-crystalline materials.
At present, a group of scientists at the Institute of Industrial Science at the University of Tokyo has analyzed the physical mechanisms of low-cycle fatigue fracture with regard to amorphous solids, like plastics or glass, with the use of computer simulations.
It has been revealed that for crystalline materials, pre-existing defects and grain boundaries can start a fracture due to fatigue. Nevertheless, the equivalent mechanism in amorphous materials is not well understood.
The stress required for a fracture to occur is considered to be much smaller for cyclic stresses compared with constant stress; however, this was not what the scientists discovered.
Contrary to the common belief, we showed that the critical strain in disorder materials that corresponds with the onset of irreversible deformation is the same for both fatigue and monotonic fractures.
Yuji Kurotani, Study Co-author, University of Tokyo
This is because the higher density results in improved elasticity and slower dynamics for ordinary amorphous systems. This density dependence of mechanical properties combines the shear deformation with density fluctuations. The cyclic shear can then amplify density fluctuations until the sample breaks via cavitation, where voids are produced.
This situation is like a crowded train. Dynamic and elastic asymmetries with respect to density changes can lead to a link between shear deformation and density fluctuations.
Hajime Tanaka, Study Co-author, University of Tokyo
The researchers state that these outcomes need to be verified with experiments, which would also aid material scientists in better comprehending the initiation of fractures.
Journal Reference:
Kurotani, Y., and Tanaka, H., (2022) Fatigue fracture mechanism of amorphous materials from a density-based coarse-grained model. Communication Materials. doi.org/10.1038/s43246-022-00293-9.