Reviewed by Mila PereraOct 27 2022
When creating an alloy out of multiple metals, structural instability and defects can occur in the material.
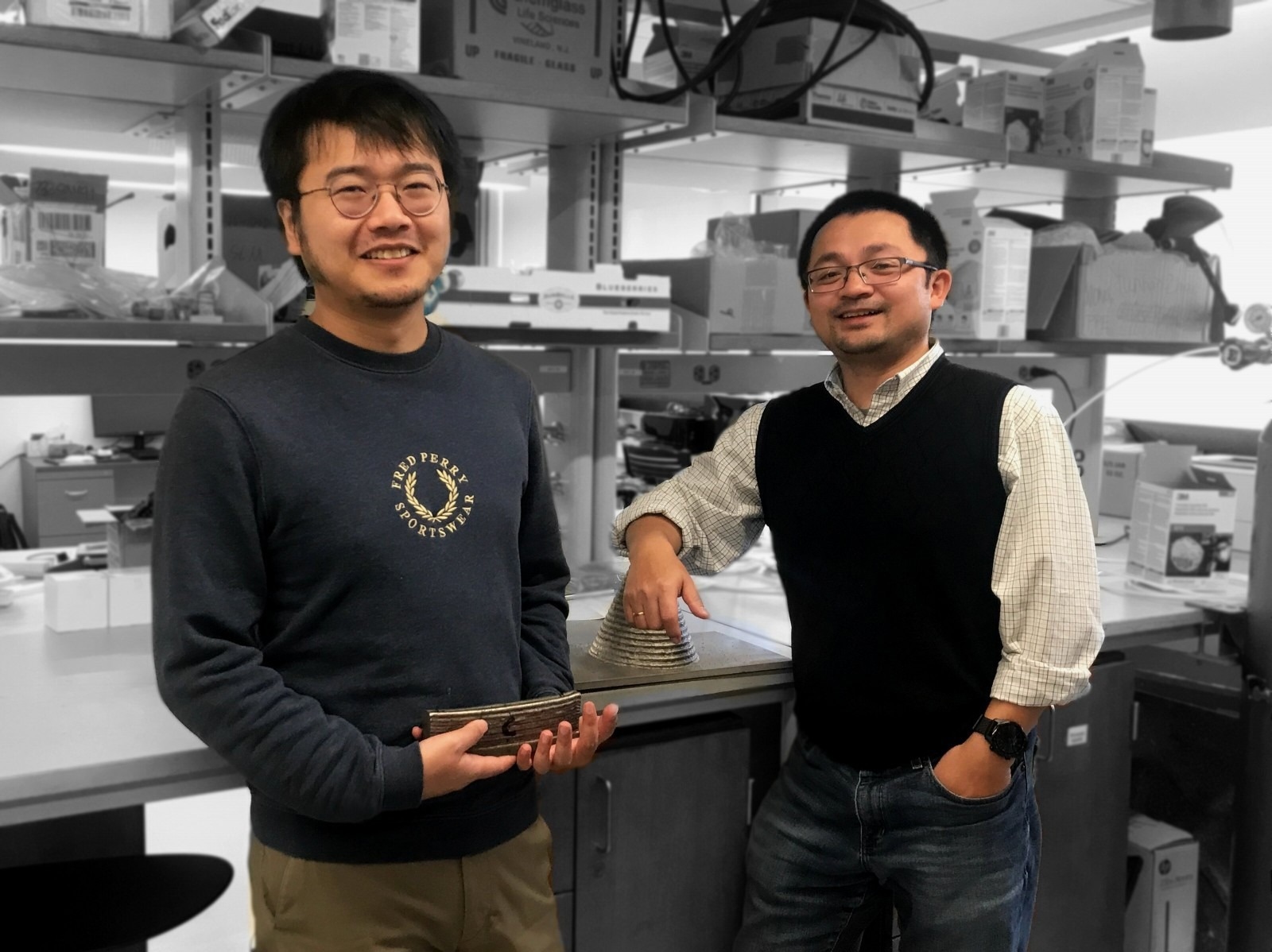
Xin Wang (left) and Wei Xiong hold samples of the alloys in the lab. Image Credit: PITT Swanson Engineering
Currently, scientists at the University of Pittsburgh Swanson School of Engineering are using those flaws to strengthen the material while keeping its flexibility intact.
The investigators are hoping to create metastable alloys that have the potential to overcome the trade-off between ductility and strength, revealing a strategy that could make alloys suited to various applications.
Our work is showing how we can include intentional flaws in an alloy to make it stronger while retaining the ductility, or flexibility, of the material.
Wei Xiong, Associate Professor, Mechanical Engineering and Materials Science, Swanson School of Engineering, University of Pittsburgh
Xiong added, “The techniques we are developing can be used to make materials fit for earthquake construction, naval ships, aerospace, nuclear energy, or even transportation for oil or hydrogen—all applications where a strong but flexible material is crucial.”
Xiong’s Physical Metallurgy and Materials Design Laboratory headed the study.
This study observes two mechanisms for metastability engineering that could be utilized to make powerful and ductile alloys: twinning-induced plasticity (TWIP) and transformation-induced plasticity (TRIP).
TRIP and TWIP use changes in the microstructure that occur under pressure, causing some defects in the material, to develop intentional defects that enhance the strength.
You can think of the strength and ductility of a material like plastic versus glass. Plastic is much more ductile and flexible: It is not as strong, but you can bend it with your hands.
Wei Xiong, Associate Professor, Mechanical Engineering and Materials Science, Swanson School of Engineering, University of Pittsburgh
“Glass is stronger than plastic, but it’s also much less flexible and will break if you try to bend it. This is the trade-off that we are trying to overcome with alloys—something that has both strength and ductility.”
To perform this research, Xiong collaborated with lead author Xin Wang, Ph.D. candidate in the Physical Metallurgy and Materials Design Laboratory, and scientists at the Illinois Institute of Technology and Northwestern University.
The team's CALPHAD modeling, aided by density functional theory calculations, offers fundamental knowledge that could be employed to develop metastable alloys with the help of TRIP or TWIP for improved strength-ductility synergy. Furthermore, it can be employed in concentrated alloys, such as nickel and steel.
We want to understand the unstable microstructure so we can predict the instability, and then we can use the defects to further increase strength and elongation. The resulting material is then self-strengthening—deform it, and it actually gets stronger.
Xin Wang, Study Lead Author and PhD Candidate, Physical Metallurgy and Materials Design Laboratory, Swanson School of Engineering, University of Pittsburgh
Journal Reference
Wang, X., et al. (2022) Design metastability in high-entropy alloys by tailoring unstable fault energies. Science Advances. https://doi.org/10.1126/sciadv.abo7333.