By Surbhi JainReviewed by Susha Cheriyedath, M.Sc.Oct 31 2022
In an article recently published in the journal Additive Manufacturing, researchers discussed the 3D-printed polymer behavior in monotonic torsion by using 15 different items in a database.
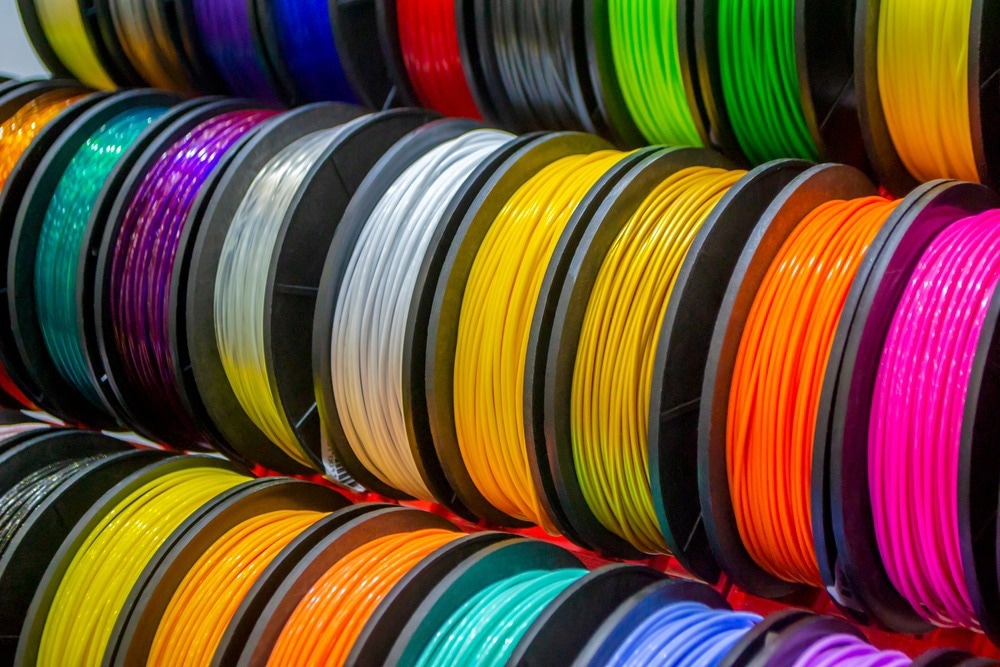
Study: Behavior of 3D-printed polymers under monotonic torsion- A database of 15 different materials. Image Credit: MarinaGrigorivna/Shutterstock.com
Background
Applications for 3D printing have multiplied dramatically over the past several years in a wide range of industries. The biomedical, automotive, food industry, education, aerospace, and civil engineering are a few of these sectors. In 2023, it is anticipated that the market for additive manufacturing will have a net worth of $23 billion. This quick development necessitates describing the performance of3D-printed samples to see how they performed under various mechanical loads and climatic conditions before being put to use. Examples of torsion in numerous fields include skewed reinforced concrete bridge piers, wind turbines, vehicle drive shafts, ships, etc. However, compared to flexural, compressive, and tensile loads, investigations on torsional loads are few.
There are not many studies on the torsional behavior of 3D-printed polymers. When fracture strain was taken into account, different printing methods did not result in differing final strengths since the fusion deposition modeling (FDM) method produced less ductility. A comprehensive literature analysis finds a scarcity of studies on the torsional behavior of 3D-printed polymers.
About the Study
In this study, the authors thoroughly investigated the performance of several 3D-printed polymers under monotonic torsion. FDM was utilized to 3D print materials from fifteen different types in a flat orientation. Two raster angles, ±45°, and 0°/90° degrees were taken into consideration for each series.
The team subjected the circular specimens with a 10 mm diameter to a 0.2 mm/min torsional moment. The results revealed that specimens with a raster angle of ±45° performed better than their 0°/90° counterparts. Additionally, the specimens' shear moduli and linear energy absorption per unit volume were evaluated and compared.
The researchers demonstrated that the best overall performance was achieved by the specimen polyamide high temperature (PAHT) - carbon fiber (CF) with an average shear stress of 49.3 MPa. The failure of specimens, except thermoplastic polyurethane (TPU) and polypropylene (PPJET), was abrupt, brittle, and initiated between layers rather than inside layers.
The addition of carbon fiber could not improve torsional capacity or ductility. The numerical simulation of various 3D-printed polymers was then suggested using idealized multi-linear curves. The current study contributed to addressing this deficiency by examining the torsional behavior of 15 different polymers that were printed in the flat orientation using the FDM technology in two ±45° and 0°/90° raster angles. A comprehensive review of the literature revealed that there was a dearth of research on the torsional behavior of 3D-printed polymers.
Observations
With very few exceptions, specimens with a raster angle of ±45° consistently outperformed their 0°/90° counterparts in all of the examined criteria. Out of the 15 materials tested, the PAHT-CF specimen performed the best overall. The highest average shear stress was seen in PAHT-CF at a raster angle of ±45°, which was equal to 49.3 MPa. This wasn't the case for the 0°/90° raster angle, where the polylactic acid (PLA)-PRO1 revealed an average shear stress value of 29.3 MPa and a marginal difference value of 28.7 MPa that belonged to the PAHT-CF. Instead of increasing the torsional capacity, elastic materials like TPU and PPJET endured massive rotations. Except for PPJET and TPU, visual observations made during the experiment showed that the failure mode of every specimen was brittle.
The fractures between layers, as opposed to the layers themselves, cause failure in brittle materials. As the specimen experienced more rotations, filament fracture occasionally occurred with additional twisting. Failure in flexible materials manifested as the development of circular bundles that gradually increased in quantity and covered the specimen's surface until the specimen failed. The highest average shear modulus of 675.1 MPa was achieved for PA-CF with a raster angle of ±45°, in contrast to the pattern shown for the shear stress. The greatest average value of 598.1 MPa for the raster angle belonged to PAHT-CF.
One of the most popular 3D-printing materials, PLA-based materials, had stress values that ranged from 22.4 to 29.3 MPa for raster angles 0° and 90° and from 29.7 to 37.9 MPa for raster angles ±45°. Most of the time, adding carbon fibers will not always result in better performance in terms of ductility or torsional strength. PPJET had the highest average elastic energy absorption of 20.70 J/mm3 per unit value among specimens for the raster angles of ±45° and 0°/90°. The proposed curve's multipliers could be changed to obtain the response of 3D-printed polymers made of various materials. The numerical simulation of 3D-printed polymers could be aided by the curves.
Conclusions
In conclusion, this study conducted an experimental investigation to evaluate the torsional performance of several polymers 3D-printed using the FDM method. Along with the material type, other study variables were the specimens' shear moduli, strain and stress values, raster angles, and energy absorption per unit volume. Idealization curves that accurately represented the overall shear stress-shear strain response of test specimens were proposed.
The authors stressed that additional study is necessary to expand on the scant amount of material reviewed in this area, validate and extend the results of this investigation, and look into situations where the two raster angles clash. They also advised exploring the behavior of polymers that were 3D-printed under cyclic and reversed-cycle torsional loads in future works because this is the situation in many real-life instances due to the dearth of data on the behavior of polymers under torsional loadings.
More from AZoM: Papertronics - Disposable Electronics on a Single Sheet of Paper
References
Sadaghian, H., Khalilzadehtabrizi, S., Farzam, M., et al. Behavior of 3D-printed polymers under monotonic torsion- A database of 15 different materials. Additive Manufacturing, 103251 (2022). https://www.sciencedirect.com/science/article/abs/pii/S2214860422006406
Disclaimer: The views expressed here are those of the author expressed in their private capacity and do not necessarily represent the views of AZoM.com Limited T/A AZoNetwork the owner and operator of this website. This disclaimer forms part of the Terms and conditions of use of this website.