By Surbhi JainReviewed by Susha Cheriyedath, M.Sc.Nov 17 2022
In an article recently published in the journal Advanced Engineering Materials, researchers discussed the multi-inks 3D extrusion for sinter-based additive manufacturing of graded porous titanium scaffolds.
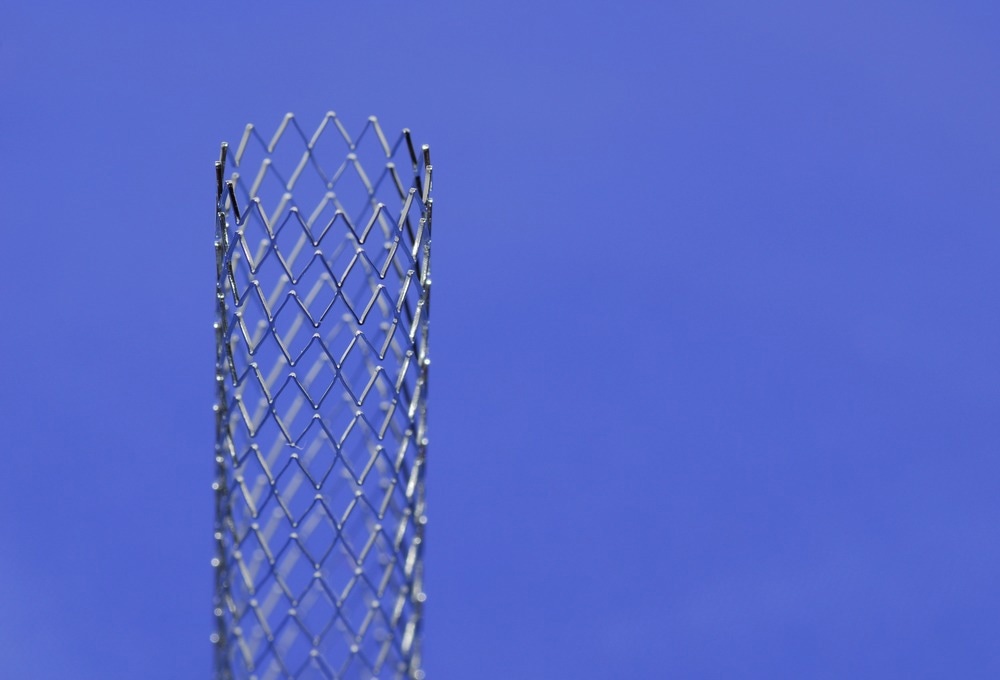
Study: Sinter-Based Additive Manufacturing of Graded Porous Titanium Scaffolds by Multi-Inks 3D Extrusion. Image Credit: Floris Slooff/Shutterstock.com
Background
For many purposes, it is highly desirable to customize a metallic object's porous structure and surface area. In the medical field, adding porosity is a strategy to reduce the stiffness of orthopedic implants while simultaneously enhancing their biological attachment. Titanium alloys cause bone loss surrounding the implant. Attempts are being made to create implants with regulated porosity to counteract this effect. Additionally, functionally graded scaffolds are gaining popularity as a way to more accurately mimic the gradient of mechanical properties found in bone.
Powder bed fusion processes, such as laser fusion (L-PBF) or electron beam (EB-PBF), have shown the ability to create parts with lattice structures, setting the standard. EB-PBF or L-PBF sections can exhibit an interconnected porosity network that is sufficiently large to permit vascularization.
It would be interesting to examine the qualities that may be achieved by inserting a gradient of pores within a scaffold. However, using PBF approaches, it appears to be challenging to realize such a structure. Feedstocks with a wider range of characteristics can be processed using 3D printing techniques that involve material extrusions, such as direct-ink writing (DIW) or fused-filament fabrication (FFF).
Using these methods, the filament created by feeding a feedstock via a fine needle is deposited following the digital model of the printed component. The ultimate pore size distribution is influenced by the particle size and green density during sintering. As a result, tailor-made porosity scaffolds might be created by material extrusion by adjusting the feedstocks for the materials.
About the Study
In this study, the authors used high-resolution X-ray tomography and electron microscopy to determine the fraction and size of macropores with a diameter greater than 100 μm, designed by computer-aided design (CAD), and micropores of diameter less than 10 μm, which remained after sintering. Their roughness, and microstructure, were correlated to the initial powder size. It was demonstrated that experimenting with the starting powder size enabled the construction of various pore architectures, from linked micropores to completely packed filaments. To create architectured structures with graded microporosity, these phenomena were integrated with a multi-inks DIW method.
The team observed that the proposed innovative approach could manufacture useful materials with adjustable strength, stiffness, and osseointegration, such as biomedical implants or scaffolds. Additionally, the micropores might contain active compounds and be positioned to meet release requirements. An innovative method was proposed for the creation of various binder/powder blends as feedstocks for the 3D extrusion using varied sizes of atomized Ti-6Al-4V powders.
The researchers created graded materials using the proposed additive manufacturing technology's flexible multi-material printing by picking the ink to print on each layer. They demonstrated how the starting powder affected the roughness, microstructure, and mechanical properties of the resulting parts, as well as the pore size distribution after sintering. This was used to create a graded porous scaffold. Any sinterable metallic material could be processed using the proposed innovative method to create well-controlled, functionally graded metallic pieces.
Observations
For stresses between 5% and 10%, a crack that propagated at 45° to the direction of compression manifested in samples containing fine powder. In samples that only contained coarse powder, a crack could start in one corner but could not spread throughout the entire sample. The increase from 265 MPa for scaffolds made of coarse powder to 425 MPa for scaffolds built of only fine powder demonstrated the anticipated improvement in yield stress with density. This value increased from 28 to 30 GPa for scaffolds composed of coarse powder to 35 to 45 GPa for scaffolds constructed using a batch of mixed powder, and finally to 55 GPa for scaffolds made entirely of fine powder.
Young's moduli for filaments with 12–13% porosity were around 62 GPa. The final amount of carbon uptake was preserved at 0.1 wt% because no significant effects of the powder size on the uptake of carbon were seen. A preliminary estimate of the oxygen uptake throughout the entire process was given as 8500 ppm for the fine powder and 1000 ppm for the coarse. Samples manufactured entirely of coarse powder only had a final oxygen content of 0.220 wt.% as opposed to 1.2-1.3 wt.% for samples made entirely of fine powder. The remaining porosity within filaments could be reduced from 12.5% to 0.025% by reducing the mean particle diameter from 23 to 4.3 μm.
From the roughness range of L-PBF to an average roughness of around 2 μm, the roughness could be reduced almost five times, which could be of importance for fatigue attributes. With just one set of sintering parameters, filaments that exhibited an open and connected porosity network could be transformed into filaments that were virtually completely dense. As a result, mechanical qualities could be adjusted in terms of both hardness and yield stress, with scaffold Young's modulus only moderately affected.
Conclusions
In conclusion, this study demonstrated the development of scaffold structures with a gradient of porosity at the micron scale by adjusting the size of the extruded powder. The different powders could not achieve the same densification stage for the same sintering treatment since this parameter affected the sintering kinetics.
The authors mentioned that the osseointegration of metallic implants or scaffolds might be adjustable using this processing method. They believe that it might also be possible to load these scaffolds with active molecules by selecting the site of the microporosity where it is needed.
More from AZoM: How are Bioplastics Made?
Reference
Coffigniez, M., Gremillard, L., Boulnat, X., Sinter-Based Additive Manufacturing of Graded Porous Titanium Scaffolds by Multi-Inks 3D Extrusion. Advanced Engineering Materials (2022).
Disclaimer: The views expressed here are those of the author expressed in their private capacity and do not necessarily represent the views of AZoM.com Limited T/A AZoNetwork the owner and operator of this website. This disclaimer forms part of the Terms and conditions of use of this website.