Plastics are being used in almost all aspects of our lives. Such materials are affordable to make and extremely stable. The issue arises after plastic is used—it can continue to stay in the environment for years. After a while, plastic will break down into tinier fragments, known as microplastics, posing considerable health and environmental problems.
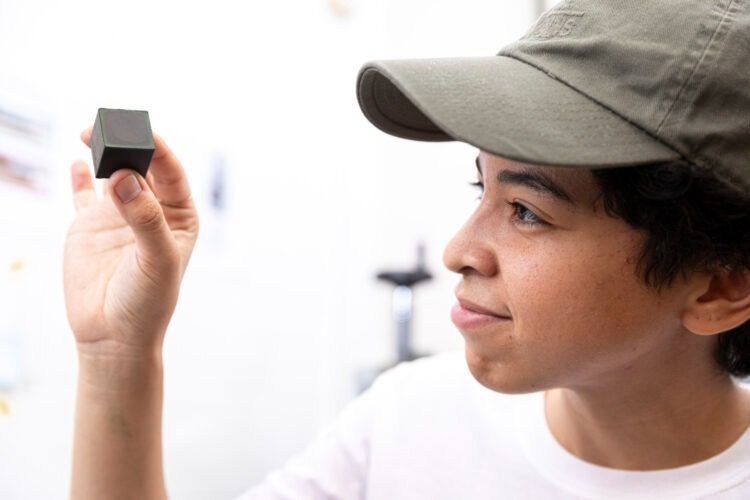
A team led by researchers at the University of Washington has developed new bioplastics that are made from powdered blue-green cyanobacteria cells, otherwise known as spirulina. Here Mallory Parker, UW materials science and engineering doctoral student, holds up a bioplastic cube made from spirulina. Image Credit: Mark Stone/University of Washington
The best-scenario solution would be to employ bio-based plastics that biodegrade; however, a majority of those bioplastics are not developed to decompose in backyard composting conditions. They must be handled in commercial composting environments, which are not available in all parts of a country.
A group headed by scientists at the University of Washington has built new bioplastics that degrade in the same period as a banana peel in a backyard compost bin. Such bioplastics are made completely from powdered blue-green cyanobacteria cells, otherwise called spirulina. The research group employed pressure and heat to produce the spirulina powder into different shapes, which is the same processing method employed to make traditional plastics. The bioplastics of the UW team possess mechanical properties that are comparable to common single-use plastics.
The research group published these results on June 20th, 2023, in Advanced Functional Materials.
We were motivated to create bioplastics that are both bio-derived and biodegradable in our backyards, while also being processable, scalable, and recyclable. The bioplastics we have developed, using only spirulina, not only have a degradation profile similar to organic waste, but also are on average 10 times stronger and stiffer than previously reported spirulina bioplastics. These properties open up new possibilities for the practical application of spirulina-based plastics in various industries, including disposable food packaging or household plastics, such as bottles or trays.
Eleftheria Roumeli, Study Senior Author and Assistant Professor, Materials Science and Engineering, University of Washington
The scientists chose to employ spirulina to produce their bioplastics for several reasons. Firstly, it can be harvested on large scales as people already employ it for different cosmetics and foods. Also, spirulina cells confiscate CO2 as they develop, creating this biomass a carbon-neutral, or likely carbon-negative, feedstock for plastics.
Spirulina also has unique fire-resistant properties. When exposed to fire, it instantly self-extinguishes, unlike many traditional plastics that either combust or melt. This fire-resistant characteristic makes spirulina-based plastics advantageous for applications where traditional plastics may not be suitable due to their flammability. One example could be plastic racks in data centers because the systems that are used to keep the servers cool can get very hot.
Hareesh Iyer, Study Lead Author, Doctoral Student, Materials Science and Engineering, University of Washington
Producing plastic products usually involves a method that employs pressure and heat to modify the plastic into an anticipated shape. The UW team took an identical method using their bioplastics.
This means that we would not have to redesign manufacturing lines from scratch if we wanted to use our materials at industrial scales. We’ve removed one of the common barriers between the lab and scaling up to meet industrial demand. For example, many bioplastics are made from molecules that are extracted from biomass, such as seaweed, and mixed with performance modifiers before being cast into films. This process requires the materials to be in the form of a solution prior to casting, and this is not scalable.
Eleftheria Roumeli, Study Senior Author and Assistant Professor, Materials Science and Engineering, University of Washington
Other scientists have employed spirulina to make bioplastics, but the bioplastics of the UW researchers are much sturdier and firmer than earlier attempts. The UW team regulated bonding and microstructure within these bioplastics by modifying their processing settings—like pressure, temperature, and time in the hot press or extruder—and examining the consequent materials’ structural characteristics, including their stiffness, strength, and toughness.
Such bioplastics are not quite prepared to be scaled up for industrial applications. For instance, although these materials are sturdy, they are still quite brittle. Another difficulty is that they are sensitive to water.
“You wouldn’t want these materials to get rained on,” Iyer stated.
The team is addressing these issues and continuing to study the fundamental principles that dictate how these materials behave. The researchers hope to design for different situations by creating an assortment of bioplastics. This would be similar to the variety of existing petroleum-based plastics.
Also, the recently created materials are recyclable.
“Biodegradation is not our preferred end-of-life scenario. Our spirulina bioplastics are recyclable through mechanical recycling, which is very accessible. People don’t often recycle plastics, however, so it’s an added bonus that our bioplastics do degrade quickly in the environment,” Roumeli added.
Co-authors on this research are UW materials science and engineering doctoral students Ian Campbell and Mallory Parker; Paul Grandgeorge, a UW postdoctoral scholar in materials science and engineering; Andrew Jimenez, who completed this study as a UW postdoctoral scholar in materials science and engineering and is now at Intel; Michael Holden, a UW master’s student studying materials science and engineering; Mathangi Venkatesh, a UW undergraduate student studying chemical engineering; Marissa Nelsen, who finished this research as a UW undergraduate student studying biology; and Bichlien Nguyen, a key scientist at Microsoft. This study was financially supported by Microsoft, Meta, and the National Science Foundation.
Journal Reference
Iyer, H., et al. (2023) Fabricating Strong and Stiff Bioplastics from Whole Spirulina Cells. Advanced Functional Materials. https://doi.org/10.1002/adfm.202302067.