Chemicals like ethylene are frequently utilized as feedstock to make industrial chemicals and polymers. By reacting methane with oxygen, a process known as oxidative coupling of methane (OCM) offers a viable and energy-efficient method of producing ethylene from natural gas. Nonetheless, there are drawbacks to the approach. Since too much oxygen turns ethylene into carbon dioxide, it can lower product yields.
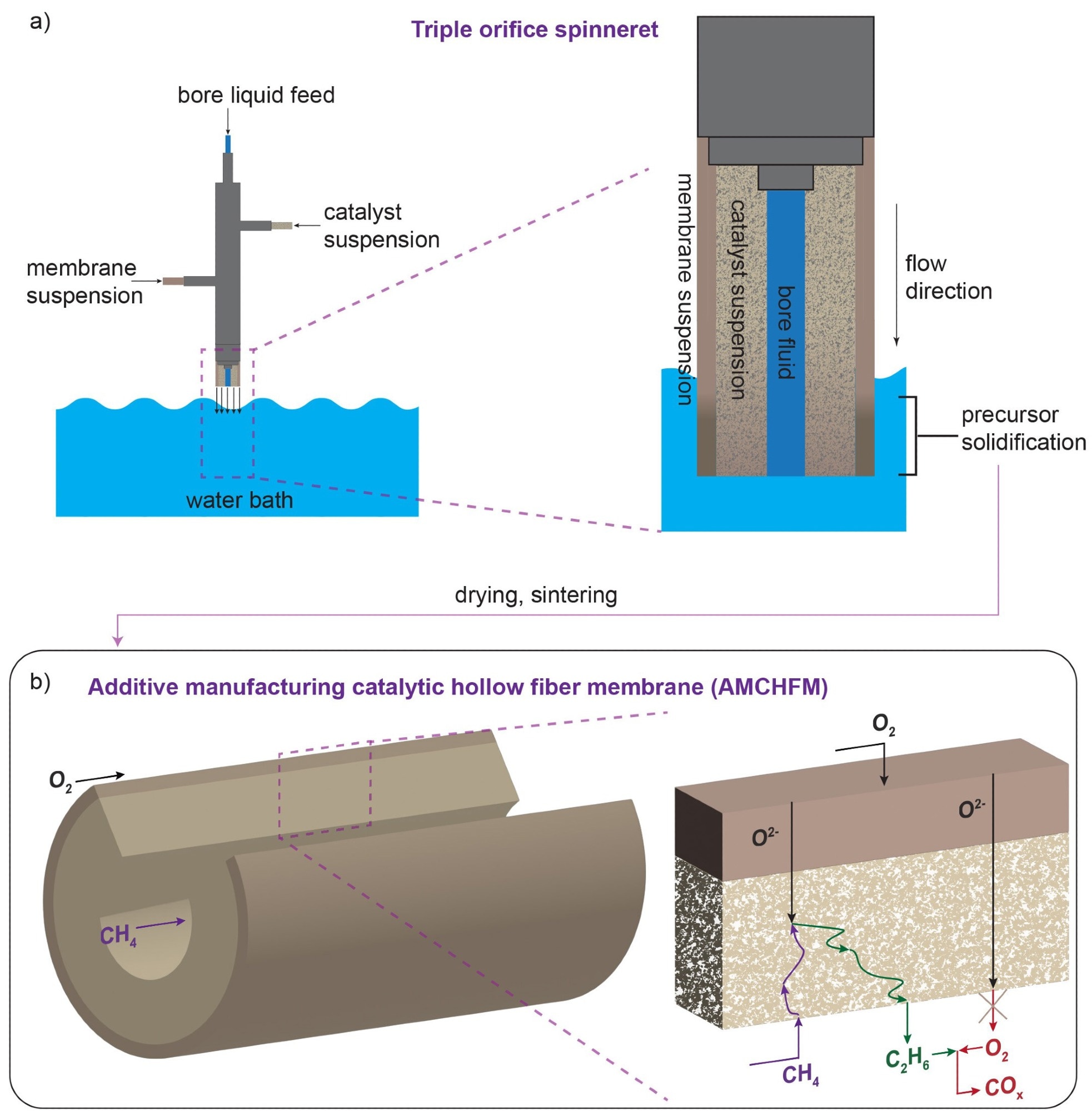
The membrane reactor manufacturing method. Membrane and catalyst layer suspensions are extruded through a triple-orifice spinneret. When the membrane precursor touches water, it forms asymmetric, hollow fibers with a porous, inner catalyst layer. b) The synthesis approach allows for the tuning of the catalyst and membrane layers of the reactor so that reactions between ethylene products and oxygen are minimized. Image Credit: Linic Lab, University of Michigan
Reactor designs that gradually add oxygen to the methane stream, limiting the amount of time the desired chemical products are exposed to oxygen, are being considered by some engineers as a solution to this issue. Nevertheless, these methods are more costly and intricate than a traditional reactor, where methane and oxygen are only delivered as gas-phase reactants over a catalyst material.
For a more sustainable future, we need to push the envelope in the design of chemical conversion processes. Introducing tools of additive manufacturing can be helpful in realizing more complex designs.
Suljo Linic, Study Corresponding Author and Martin Lewis Perl Collegiate Professor of Chemical Engineering, University of Michigan
A multifunctional membrane-catalyst reactor that minimizes oxygen-ethylene reactions while retaining high methane oxidation rates has been devised by researchers at the University of Michigan. By resolving the yield concerns of earlier OCM membrane reactor designs, the new design can boost the economic viability of an energy-efficient process of creating products from natural gas.
A hollow fiber membrane catalyst device, with multiple layers of gadolinium-doped barium cerate catalyst, powers the team’s reactor. High volumetric ethylene generation is supported by the barium cerate fibers’ high surface-to-volume ratio. The co-extrusion of the catalyst and membrane allows additive manufacturing techniques to construct these multifunctional systems in a single step.
With this method, the researchers can generate thin membranes that are sandwiched between thicker, more porous catalyst layers to speed up the reaction between oxygen and methane. In addition, they can adjust the transport and reaction speeds to coincide with one another more widely.
Thicker membranes speed up the reaction between surface oxygen and methane, increasing the generation of ethylene. However, they can also allow more unwanted oxygen to build up and react with ethylene.
The researchers adjusted the reactor’s OCM-active site count so that the oxygen diffusion rate and methane-oxygen reaction rates matched exactly to overcome this issue. Due to this alteration, all of the oxygen that was added to the system is consumed by methane reactions before it has an opportunity to interact with ethylene.
Tuning the methane activation rate to the oxygen diffusion rate gave unexpectedly high ethylene yields compared to a conventional reactor composed of the same catalyst material.
James Wortman, Doctoral Student, University of Michigan
Wortman stated that reactors can be optimized for various desirable chemistries, such as fuel cells, electrolyzers, and partial oxidation processes, by simply adjusting the characteristics of both the membrane and catalyst layers.
Journal Reference
Wortman, J., et al. (2023) Optimizing hierarchical membrane/catalyst systems for oxidative coupling of methane using additive manufacturing. Nature Materials. doi:10.1038/s41563-023-01687-x