A recent article in Polymer investigated the impact of high-frequency curing on aqueous polymer isocyanate (API) containing an oxidized starch/styrene-butadiene rubber (SBR) system as the main component.
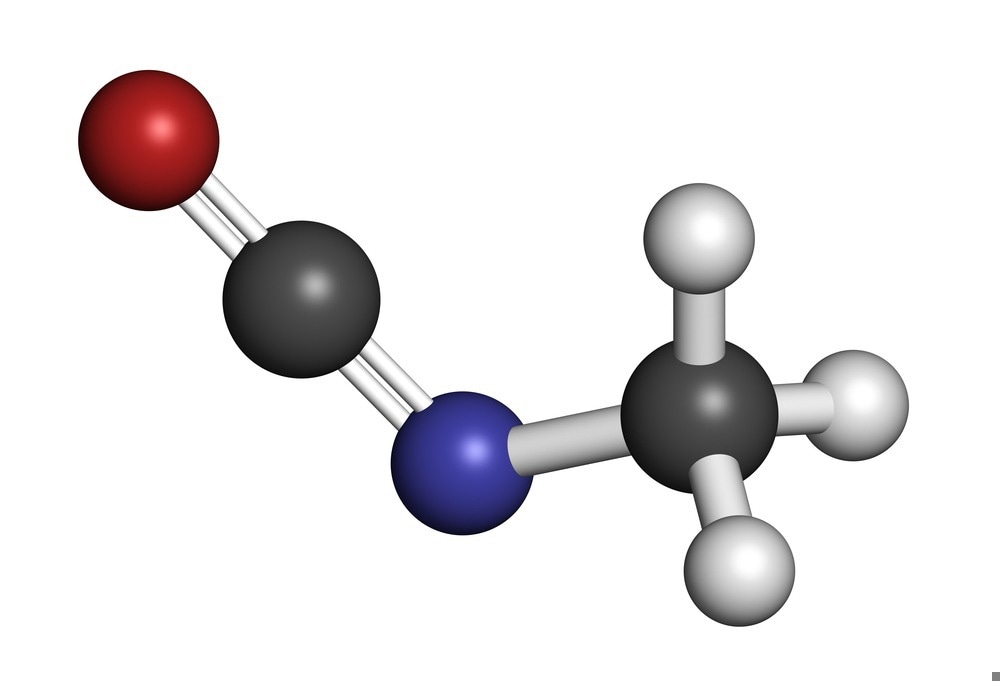
Image Credit: StudioMolekuul/Shutterstock.com
Background
API consists of isocyanate and a main component (MC), which includes aqueous polymers with active hydrogen, organic/inorganic fillers, and additives. Due to its excellent bonding characteristics, API is extensively used in load-bearing structures.
Despite its widespread use, API has several issues, primarily the high cost of its main raw materials (MC and cross-linking agent) and thermal curing process. High-frequency curing has emerged as a popular solution due to its numerous advantages, including fast and uniform heating, controllable temperature, high energy efficiency, and low cost, making it highly promising for adhesive curing.
Compared to conventional processes, curing with high-frequency electromagnetic fields can provide equivalent or better mechanical properties and bonding performance of the adhesive in shorter curing times.
Researchers selected an oxidized SBR system for its strong electromagnetic energy absorption to evaluate the effect of oxidized starch content on API high-frequency curing performance.
Methods
The MC was prepared using oxidized starch, hydroxyethyl cellulose, sodium tetraborate solution, SBR emulsion, and calcium carbonate. The API adhesive was then obtained by mixing an isocyanate cross-linking agent with this MC at a mass ratio of 15:100.
API-bonded wood specimens were fabricated using smooth-surfaced blocks of rubberwood (Brazilian rubber tree) with dimensions of 30×25×10 mm3 and a bonding area of 25×25 mm2. The API amount used was 200-300 mg/cm2, with the fiber direction parallel to the axial loading direction.
These specimens were cured in a high-frequency microwave generator (2.45 GHz, 700 kW) at 1 MPa for 10 minutes. For comparison, specimens were also prepared using the standard ambient temperature curing procedure.
Cured API films were placed in the high-frequency generator for 10 minutes, while another part was cured at 25 °C and 30 % relative humidity for 72 hours. The dried film had a thickness of 140 μm.
API dielectric loss and emulsion ionic conductivity were measured using an electrochemical workstation. Tensile and compression shear tests were performed on API adhesives under room temperature and boiling water aging conditions and quasi-static tensile tests were conducted on API propriety films.
Dielectric testing and differential scanning calorimetry were conducted to evaluate the dielectric loss and specific heat capacity of API adhesives, respectively. Fourier transform infrared spectral analysis and scanning electron microscopy were used to assess the microstructure of API adhesives.
Results and Discussion
The variations in specific heat capacity with temperature were minimal; thus, API-specific heat capacity in the range of 25-60 °C was used to represent the heat capacity during the high-frequency curing process to exclude the effect of API phase change.
Oxidized starch significantly increased the dielectric loss of API, enhancing its ability to convert electromagnetic energy into thermal energy and accelerating reactions between isocyanate, MC hydroxyl, and other reactive groups. This formed more solid cross-linking structures and reduced the isocyanate group's residue, decreasing defects in the API body.
API's bonding and mechanical characteristics with high-frequency curing initially increased and then decreased with increasing oxidized starch content. The optimum bonding and mechanical characteristics were observed at 15 wt.% oxidized starch content at room temperature, while the best bonding property after boiling water curing was at 10 wt.% oxidized starch content.
Higher oxidized starch content enhanced the effect of high-frequency curing on API’s bonding properties, increasing the improvement from 18 % and 17.3 % to 25.1 % and 26.3 % at room temperature and post-boiling water curing, respectively.
Young’s modulus and tensile strength of the API significantly improved after high-frequency curing compared with ambient curing, although its fracture elongation decreased. Thus, it was concluded that a higher oxidized starch content resulted in a more pronounced difference between high-frequency and ambient curing.
Conclusion
This study applied high-frequency curing to examine the effects of oxidized starch content on the bonding and intrinsic mechanical properties of API. Various thermodynamic tests and material characterization methods revealed the underlying physical and chemical mechanisms.
The addition of oxidized starch improved the mechanical properties of API after high-frequency curing, with greater improvements observed with higher oxidized starch content. The potential enhancement mechanism was attributed to the increased dielectric loss of API due to oxidized starch, which converted more electromagnetic energy into thermal energy, creating more cross-linked structures.
Journal Reference
Li, Y., et al. (2024). Oxidized Starch-Reinforced Aqueous Polymer Isocyanate Cured with High-Frequency Heating. Polymers. doi.org/10.3390/polym16111609,
Disclaimer: The views expressed here are those of the author expressed in their private capacity and do not necessarily represent the views of AZoM.com Limited T/A AZoNetwork the owner and operator of this website. This disclaimer forms part of the Terms and conditions of use of this website.