Introduction New high temperature materials are required to increase energy conversion efficiency of thermal cycles such as gas turbine engines. Functionally graded materials (referred to as FGMs) and nano-composites consisting of oxide ceramics and metals have received an attention as next generation of high temperature materials. Since at high temperatures oxygen can pass through oxide matrix, dispersed metal particles are oxidized in the matrix. The metallic dispersion expands due to oxidation and gives rise to stress in the matrix. Finally the composite is fractured. To apply FGMs and nano-composites at high temperatures, oxidation/corrosion resistance is very important. Nanko et al. [1] reported high temperature oxidation of partially stabilized zirconia (PSZ) composites with Ni particle dispersion (Ni/PSZ). Due to oxidation of Ni dispersion, a PSZ matrix was cracked. The cracked region grew proportional to oxidation time. High temperature oxidation of Al2O3 matrix composites with Ni particle dispersion (Ni/Al2O3) was also reported [2,3]. Nanko et al. [2] described that since Al2O3 has excellent mechanical properties and low diffusivities of ions, Al2O3 composites dispersed with metallic Ni particles (Ni/Al2O3) have higher oxidation resistance than the Ni/PSZ. Oxidized layer of Ni/Al2O3 consisted of Al2O3 matrix and NiAl2O4 as an oxidation product. Growth of the oxidized zone followed the parabolic law, which meant that mass transport in the oxidized layer was rate-controlled. The oxidized zone was not cracked, however, included voids, which were formed by outward diffusion of cation during oxidation of Ni. Wang et al. [3] reported oxidation of Ni/Al2O3 at temperatures from 1000 to 1300ºC. They studied oxidation behavior of the composites with finer Ni particles (2-5 µm) than our previous work (10 µm) [2]. Oxidation behavior obeys the parabolic law. Oxidation rate increases with increasing Ni volume fraction. To understand oxidation of oxide composites dispersed with metallic particles, diffusion properties of matrix should be discussed. Since PSZ is a typical oxide ion conductor, Ni/PSZ is oxidized by the inward oxygen diffusion. Oxidation of Ni/Al2O3 occurs due to inward diffusion of oxide ion and outward diffusion of cation. Magnesium oxide has faster diffusion coefficient of cation than the oxide ion. In this paper, high temperature oxidation of MgO-based composites with Ni particle dispersion (referred to as Ni/MgO) is investigated in order to understand oxidation behavior of metal dispersed oxide that has faster cation diffusion than oxide ions. Experimental Preparation of Sample The commercial MgO powder (average particle size: 0.5 μm, purity: 99.99%) with 5 vol% of Ni powder (average particle size: 10 μm, purity: 99%) were mixed in ethanol for 30 min with a mortar. After drying, the powder mixture was consolidated by a pulsed current pressure-sintering technique at 1350˚C in die temperature under 29 MPa in die pressure for 30 min of holding time in vacuum. The sintered samples attained a density of at least 99 % of theoretical value. Sample surface was ground by #1500 SiC-abrasive papers and then polished by 4 μm-diamond slurry. Oxidation of Sample The sample was put on the alumina balls (3 mm in diameter) in an alumina crucible and oxidized at temperatures of 1200 and 1300˚C in air. The heating rate in the oxidation experiments was 400 K/h. Phase identification of the samples was carried out by X-ray diffraction (XRD). Microstructure of sample was observed by scanning electron microscopy (SEM) and electron probe microanalysis (EPMA). Thickness of oxidized zone was determined as the average of the value measured in 10 different areas. Results and Discussion Figure 1 shows XRD pattern of (a) as-sintered sample and (b) oxidized one at 1300˚C for 1 day. As-sintered sample consists of MgO and Ni. After oxidation, peaks of Ni in the XRD pattern disappear. This fact means that the oxidation reaction of Ni particles in the MgO matrix form the solid solution, as follows: (1) 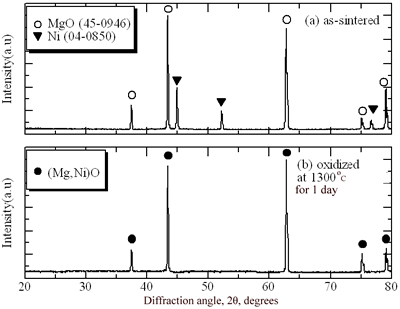 | Figure 1. XRD pattern of sample surface of Ni/MgO. (a) as-sintered sample and (b) oxidized one at 1300˚C for 1 day. | According to the binary phase-diagram [4], the NiO-MgO system shows the complete solid solution. Figure 2 shows the SEM photograph of the sample oxidized at 1300˚C for 1 day. There are no Ni particles in the region in the depth of 70 μm. Ni particles dispersed in the MgO matrix are oxidized completely in this zone. The region below the completely oxidized zone includes partially oxidized Ni particles. The MgO composite is not fractured by oxidation of dispersed Ni particles. Voids are observed in the oxidized zone, as similar to Ni/Al2O3 [2]. The voids are formed by the outward diffusion of cations during high temperature oxidation. In this study, the depth of oxidized zone is defined as a distance from free surface to the position where partially oxidized Ni particles are observed. 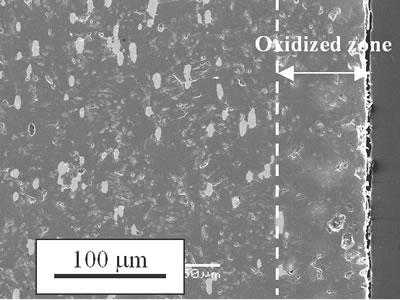 | Figure 2. Cross-sectional view of Ni/MgO after oxidation at 1300˚C for 1 day. | Figure 3 shows the EPMA results of the sample oxidized at 1300˚C for 1 day. In oxidized zone, distribution of Ni and Mg is not homogeneous even around the free surface. 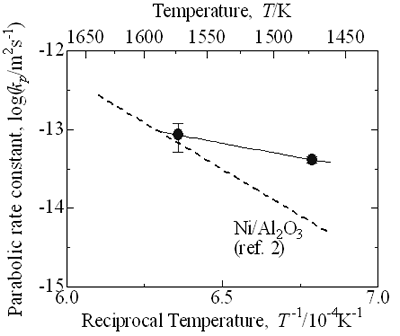 | Figure 3. EPMA results of Ni/MgO oxidized at 1300˚C for 1 day in air. BEI means back scattered electron image. | This means that interdiffusion of Mg and Ni in the oxidized zone is not completed to form homogeneous (Mg,Ni)O solid solution during high temperature oxidation. By increasing oxidation time, the oxidized zone near the surface should be homogeneous. Figure 4 represents the depth of the oxidized zone, x, as a function of oxidation time, t, on the high temperature oxidation of Ni/MgO at elevated temperatures. Growth rate decreases with increasing oxidation time. Growth of the oxidized zone follows the parabolic law: (2) where kp is the parabolic rate constant. Because the oxidized zone is dense as shown in Figure 2, mass transport through the oxidized zone is the dominant of the growth process of the oxidized zone. 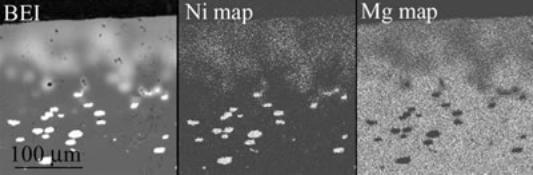 | Figure 4. Depth of oxidized zone, x, as a function of time, t, on high temperature oxidation of Ni/MgO. | Figure 5 shows comparison of the parabolic rate constant of Ni/MgO and Ni/Al2O3. At temperatures lower than 1600 K, the values of kp of Ni/MgO are lower than Ni/Al2O3 reported previously [2]. The apparent activation energy is 139 kJ.mol-1. Freer [5] listed reported data of diffusion coefficients of many oxides. The values of apparent activation energy of diffusion of Mg and Ni in MgO range from 150 to 350 kJ.mol-1 and for O from 250 to 400 kJ.mol-1. In particular, the extrinsic diffusion coefficient of Mg in MgO is equal to 151 kJ.mol-1 and for Ni it is 154 kJ.mol-1 in MgO. Their activation energies of cation diffusion agree with that of high temperature oxidation of Ni/MgO reported in this work. The predominant process of oxidation of Ni/MgO is diffusion of cation passing through oxidized (Mg,Ni)O zone. 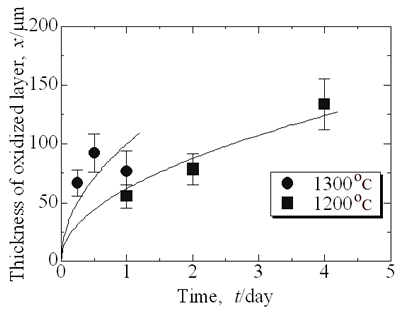 | Figure 5. Temperature dependence of parabolic rate constant and high temperature oxidation of Ni/MgO. | Average molar fraction of NiO in the oxidized zone can be calculated as 8 mol% from 5 vol%Ni. By doping NiO in MgO, hole concentration should be increased as follows: (3) Diffusion process on the growth of oxidized zone should be dominated by Mg or Ni diffusion and electronically compensated by hole conduction. Figure 6 illustrates a speculation of growth mechanism of oxidized zone of Ni/MgO. Cations of Mg or Ni diffuse toward the outside. Metallic Ni particles are oxidized by oxide ions generated by decomposition of the MgO matrix at the interface. The specific volume change per Ni particle of this reaction, ΔV/VNi, is calculated by: (4) where nNi is the molar amount of Ni and vi is molar volume of species i. When oxidizing 1 molar of Ni to form 1 molar of NiO, 1 molar of MgO must be decomposed. The value of ΔV/VNi is equal to –1.1, i.e. voids with almost same volume of Ni particle are formed. As shown in Figure 2, large voids with almost same size of dispersed Ni particle are observed in the oxidized zone. This observation is in agreement with the calculation result of volume change. 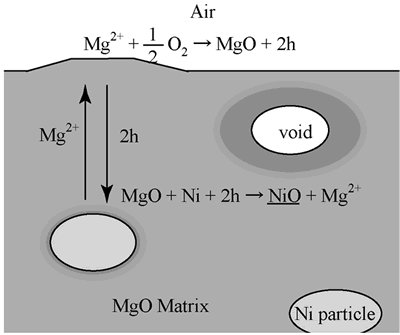 | Figure 6. Mechanism of oxidized zone growth of Ni/MgO at elevated temperatures. | Conclusions Oxidation behavior of MgO-based composites with 5 vol% Ni particle dispersion was investigated at high temperatures in air. Oxidized zone consisted of (Mg,Ni)O solid solution. Growth of the oxidized region followed the parabolic law, which meant that mass transport in the oxidized zone was rate-controlled. The apparent activation energy of parabolic rate constant agrees with those of extrinsic diffusion coefficients of cation in MgO. Because of outward diffusion of cation during high temperature oxidation, voids form in the oxidized zone. Acknowledgement The authors wish to express their gratitude to the Saneyoshi Scholarship Foundation for partially supporting the present work. References 1. M. Nanko, M. Yoshimura and T. Maruyama, “High Temperature Oxidation of Y2O3 Partially-Stabilized ZrO2 Composites Dispersed with Ni Particles”, Mater. Trans., 44 (2003) 736-742. 2. M. Nanko, T. Nguyen Dang, K. Matsumaru and K. Ishizaki, “High Temperature Oxidation of Al2O3-Based Composites with Ni Particle Dispersion”, J. Ceram Proc. Res., 3 (2002) 132-135. 3. T. C. Wang, R. Z. Chen and W. H. Tuan, “Oxidation Resistance of Ni-Toughened Al2O3”, J. Euro. Ceram. Soc., 23 (2003) 927-934. 4. E. M. Levin, C. R. Robbins and H. F. McMurdie, Phase Diagrams for Ceramists, The American Ceramic Society, OH, p110 (1979). 5. R. Freer, “Bibliography, Self-Diffusion and Impurity Diffusion in Oxides”, J. Mater. Sci., 15 (1980) 803-824. Contact Details |