A recent article in Silicon explored the synthesis of Al/SiC cermet powders via attrition milling and their use as fillers in polycarbosilane (PCS) to create composite coatings that protect stainless steel (SS) from corrosion.
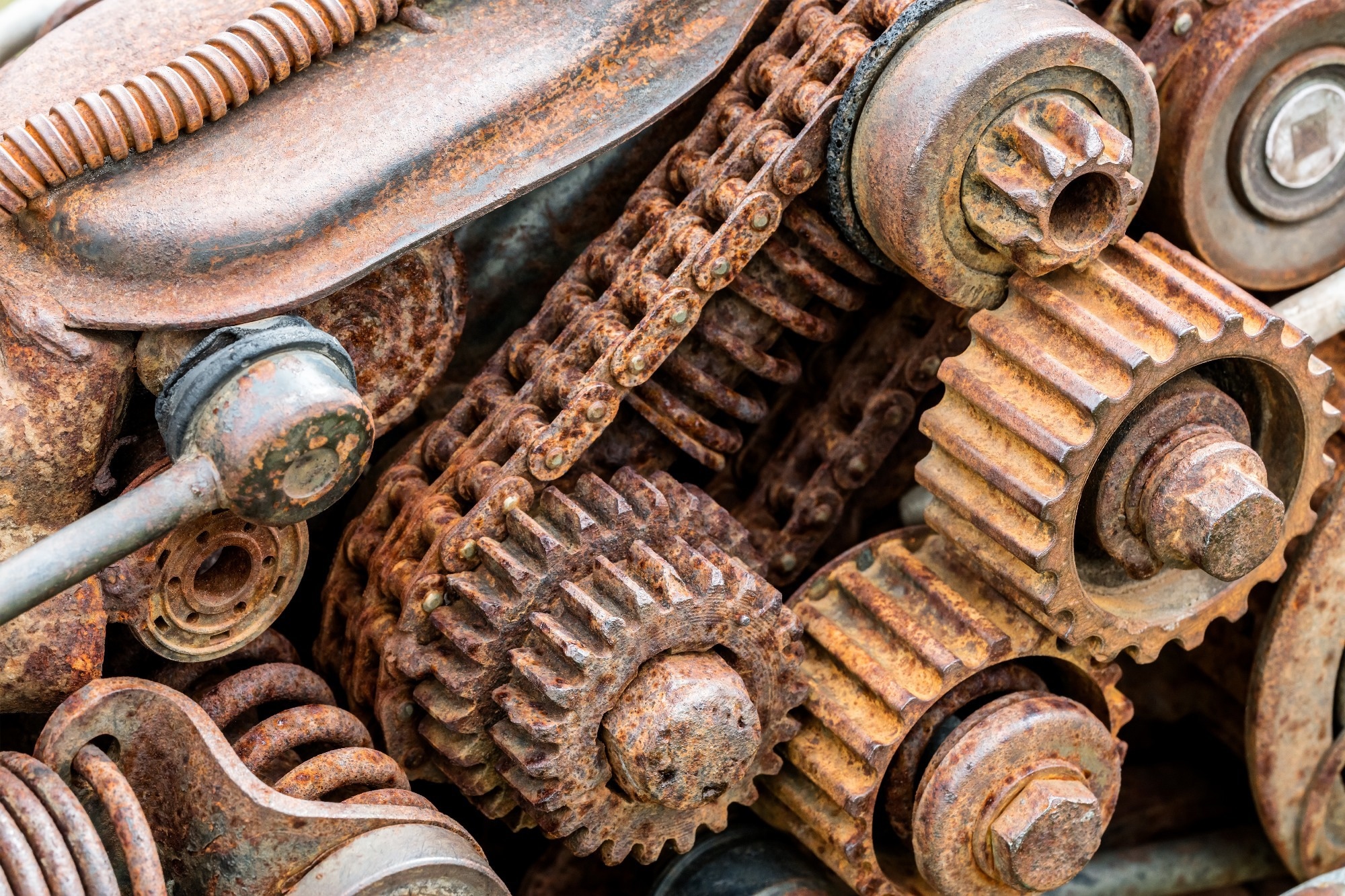
Image Credit: Mr Twister/Shutterstock.com
Background
SS is widely used in structural applications but is susceptible to corrosion, especially in highly corrosive environments like oceans and nuclear reactors. Preventing SS corrosion is crucial, particularly in energy-related applications.
Ceramic-metallic (cermet) coatings are promising for corrosion protection as they combine the high resistance of ceramics (against corrosion, wear, oxidation, and extreme temperatures) with the ductility and low thermal expansion of metals.
Polymer-derived PCS is a well-known precursor for SiC-based ceramics. However, these materials often undergo significant volume contraction during the transformation from organic to inorganic phases, leading to pores and cracks.
These issues can be mitigated by using passive or active fillers. This study proposed applying Al/SiC coatings on SS substrates by spraying suspensions of Al/SiC cermet powders and xylene in PCS.
Methods
Three composites were prepared by varying Al and SiC powder ratios in the initial mixtures: 80:20 % (ASP1), 70:30 % (ASP2), and 60:40 % (ASP3). These cermet powders were mechanically milled in a vertical attrition mill and mixed with xylene and PCS to prepare precursor suspensions.
The solutions were sprayed manually onto A304 SS substrates (2.5×2.5×0.3 cm3) at room temperature. The coated substrates were then cured at 200 °C in the ambient for 15 minutes and later annealed in a tubular furnace at 700 °C for one hour under argon gas flow. The coatings were labeled ASC1, ASC2, and ASC3, respectively, corresponding to ASP1, ASP2, and ASP3 cermet powders.
X-ray diffraction (XRD) was used to analyze the structure of the cermet powders and coatings, while scanning electron microscopy (SEM) provided morphological details. The roughness profiles of the coatings were examined with a digital optical microscope, and the sessile drop method determined the coatings' contact angle and wettability. Surface free energy was calculated using a normalized equation, and adhesion was tested with a universal testing instrument.
The corrosion resistance of the coated samples was evaluated using modified salt spray (fog) and acetic acid-salt spray tests, with corrosion rates determined by weight loss. A focused ion beam microscope was used to analyze the coating cross-sections before and after accelerated corrosion testing.
Results and Discussion
The XRD patterns of the milled cermet powders revealed the presence of a face-centered cubic (FCC) structure of Al, along with cubic 3C-SiC and hexagonal 6H-SiC phases. Some mixtures also showed ZrO2 diffraction peaks, indicating impurities from the grinding medium and vessel. The quantity of ZrO2 particles decreased in mixtures with higher Al-to-SiC ratios, where an Al layer formed on the surface of the vessel and medium, reducing wear from the rigid SiC particles.
The microstructures of the cermet powders consisted of round-shaped aggregates, measuring 14-20 µm, a result of the specific milling parameters that prevented cold-welding. This particle morphology was advantageous for producing uniform coatings when sprayed at room temperature.
The XRD patterns of the composite coatings before heat treatments (green samples) exhibited FCC Al, 3C-SiC, 6H-SiC, and ZrO2, which originated from the precursors. However, annealing at 700 °C in an argon atmosphere transformed the PCS into amorphous SiC.
The absence of diffraction peaks of the A304 SS substrates post-heat treatment validated the formation of dense Al/SiC coatings. SEM images also depicted the formation of dense homogeneous coatings for all Al:SiC ratios.
Among the coatings, ASC1 exhibited a higher roughness value and the lowest water contact angle compared to ASC2 and ASC3, likely due to more pronounced and spaced-out ridges on ASC1’s surface. As a result, the coatings reacted differently when exposed to a highly corrosive environment for 240 hours.
The untreated SS substrates experienced the highest level of corrosion, whereas the heat-treated coatings showed significantly lower corrosion rates. Even under severe conditions, such as exposure to acetic acid-salt fog, both green and heat-treated specimens exhibited no delamination or coating failure, reducing the SS corrosion rate by up to 87 %.
Conclusion
The researchers successfully synthesized Al/SiC cermet powders with a hemispherical morphology and maintained phase integrity. These powders were effectively used as fillers in PCS to create dense Al/SiC coatings.
The resulting coatings showed excellent stability, with no secondary phases forming after heat treatment at 700 °C. Additionally, the coatings demonstrated strong adhesion and effectively protected SS substrates from corrosion in harsh environments.
The researchers recommend further investigation into the use of cermet powders as active fillers to reduce pore formation in coatings, thereby enhancing their performance. Such coating systems could significantly extend the lifespan of marine equipment, reducing the need for costly maintenance.
Journal Reference
Valerio-Rodríguez, MF., González, LA., Mata-Padilla, JM., López-Honorato, E. (2024). Composite coatings from polycarbosilane derived SiC and Al/SiC cermet active fillers as protective barriers against steel corrosion. Silicon. DOI: 10.1007/s12633-024-03115-4, https://link.springer.com/article/10.1007/s12633-024-03115-4
Disclaimer: The views expressed here are those of the author expressed in their private capacity and do not necessarily represent the views of AZoM.com Limited T/A AZoNetwork the owner and operator of this website. This disclaimer forms part of the Terms and conditions of use of this website.