The fourth industrial revolution is underway, scored by an expanding network of connectivity and automation. What this means for materials and device testing platforms is the development of systems with the capacity to perform a test automatically as the data flow is transmitted to wherever it needs to be in an instant.
This improves productivity and increases the number of tests that can be performed in short time periods exponentially. Efficient automation allows a company to apply its valuable personnel resources much more effectively. However, the question is, how do you approach establishing the appropriate setup for your needs?
For a well-established production process, being aware of how and where to allocate time, energy and manpower are key factors. Part of that is determining the right framework to apply to your own manufacturing process.
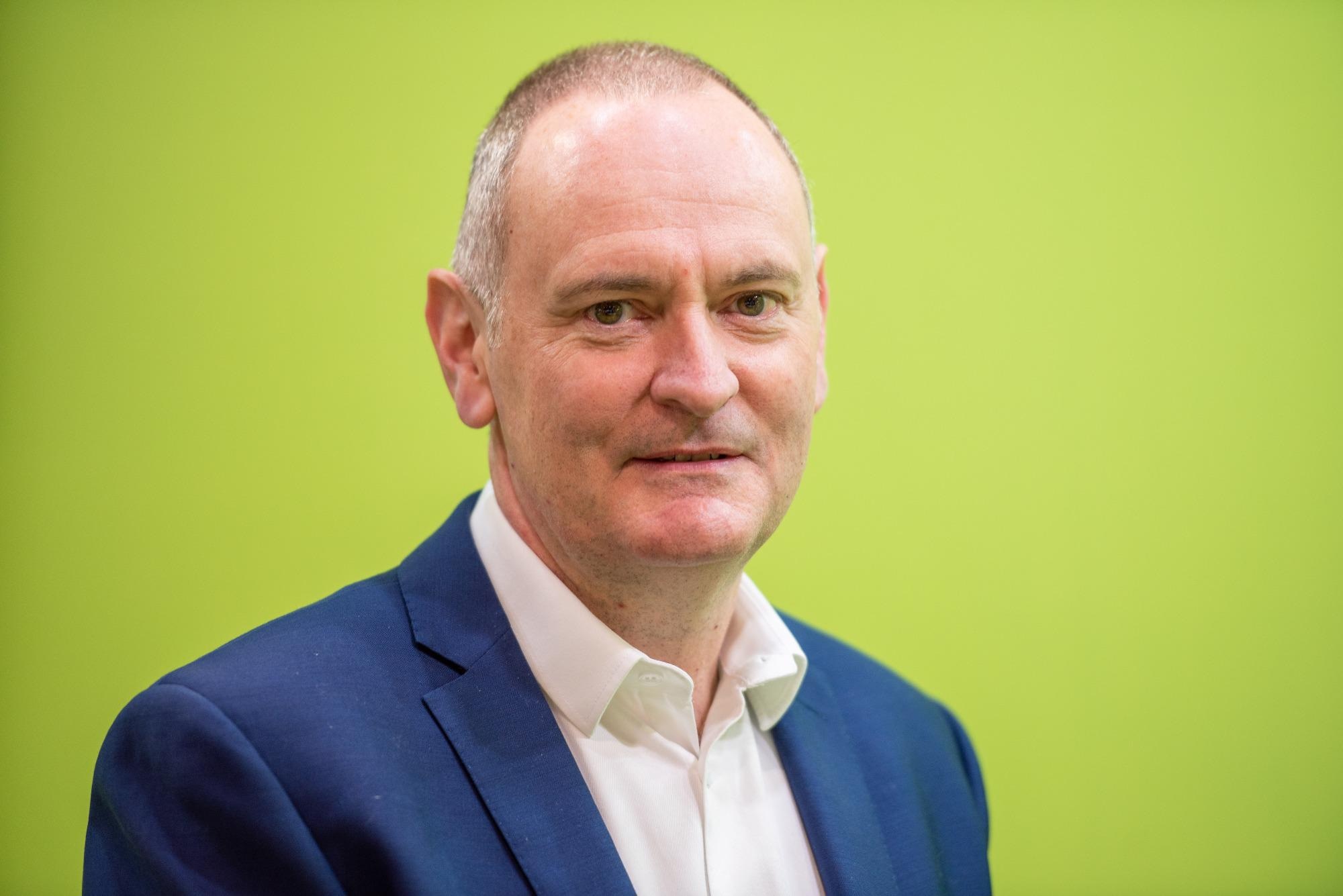
Image Credit: Tinius Olsen
At times this may be using fully automated systems, but that may not always be necessary. Evolving developments in automation technology mean that only certain elements of an automation process need to be introduced into the materials or device testing infrastructure, yet still allow substantial gains to be made.
Tinius Olsen discusses automation needs directly with its clients to gain a deep understanding of which one of the three classifications meets technology expectations as well as ROI. These classifications are created to work in-house as standard but can be broadly applied to most situations and can be modified or expanded upon.
Classification 1; “No Walking Paper”
The automation of processes within a materials testing station/platform – while an operator still enters and extracts the test specimen, everything else is automated.
This replaces older processes where users traditionally had to push buttons on basic machines and testers as well as fit and set up sensors for each test and so on.
At this technology level, the operator’s presence is still required during a test as they pick and place the specimen into the tester, but then they simply speak “Start test” or click the mouse once to initiate the process. Everything else is automated, including test pass/fail, alert notifications, and digital data flow that is fed into the user’s process.
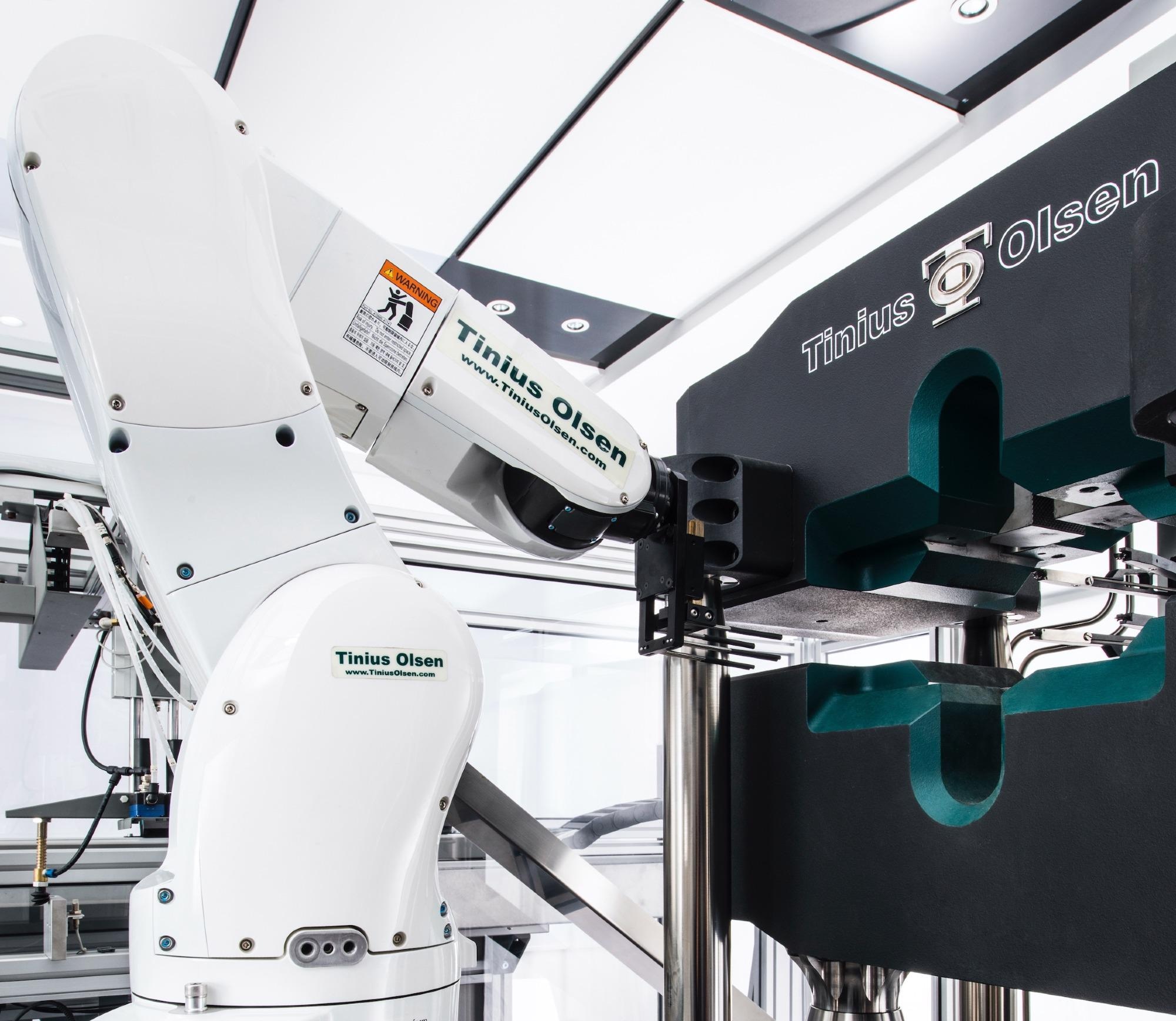
Image Credit: Tinius Olsen
Classification 2; “Lights Out Working”
Automation, including the pick and entry of test specimen and extraction of the specimen. Here integration with the user’s process, as with classification (1), takes the form of data flow in (specimen information) and the results data fed out supplemented this information.
This level of automation necessitates minimal unskilled operator intervention restricted to loading test specimens for a “shift” into a feeding rack system on the automated testing cell’s edge.
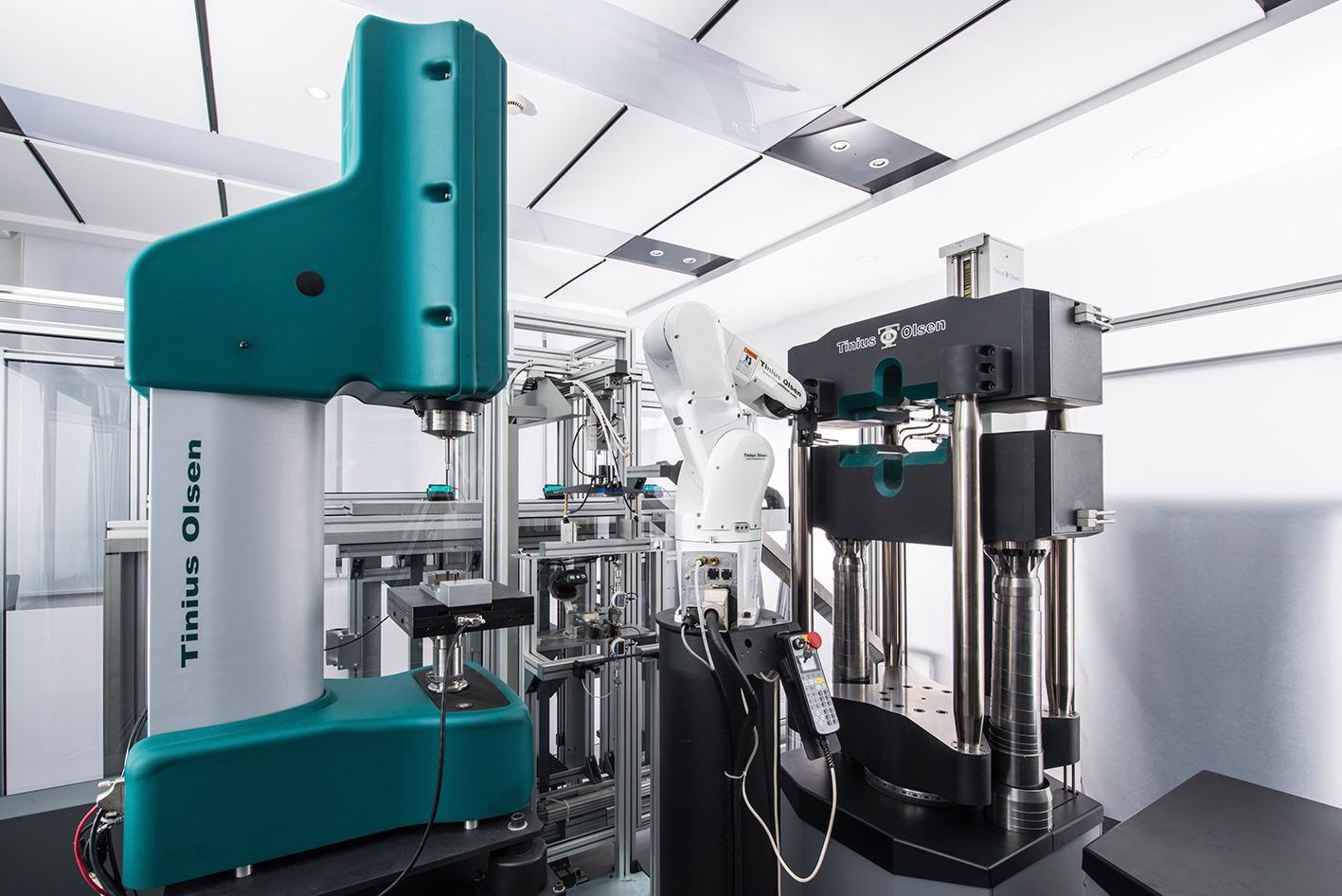
Image Credit: Tinius Olsen
Classification 3; “Total Process Automation”
Full automation via “intimate” integration with the user’s broad-scale process, accomplished by either the user themselves or their contracted developer and integrated process provider.
As part of the Tinius Olsen solution, the company provides a remote interface for automation developers, i.e., an API (Application Programming Interface), which the automation/integration development team used to integrate the Tinius Olsen system into the broad-scale process that requires implementation.
This level of automation is operator free - test specimens can be transported from production to the Tinius Olsen system by AGV (Automated Ground Vehicles), and the specimen handling (robotics) makes up part of the developer’s solution.
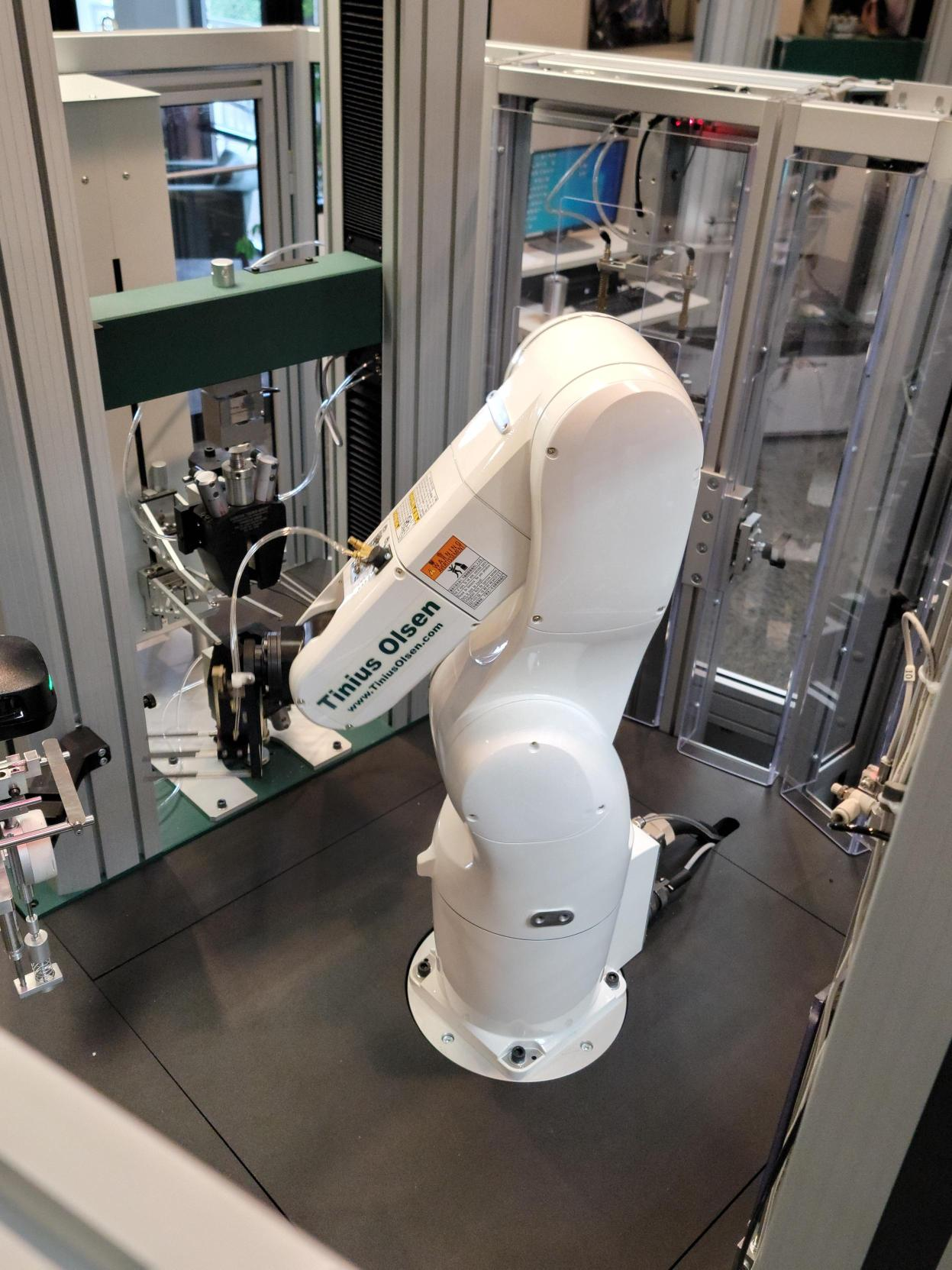
Image Credit: Tinius Olsen
Here is a prime example of an automated tensile ASTM D 638 and flexural ASTM D790 solution that Tinius Olsen recently delivered under the need classification (2):
A global manufacturer of polymer matrix composites that uses glass, carbon and fibers in its composites required a method that would allow minimal operator interference and monitoring of tensile and flexural tests on its glass-filled composite materials.
As the director of quality and testing explained, they have to able to “hit go and walk away. We have no time to sit, watch and shepherd a materials testing process.”
While the company tests only a limited number of batches a day, those it does test must meet strict monitoring procedures to ensure the quality of the final product meets and complies with industry standards, including ASTM D638 tensile and ASTM D790 flexural.
With space a precious commodity in the lab facility, Tinius Olsen uses its standard technology building blocks approach to offer a single “automated test cell” that includes two materials testing machine frames.
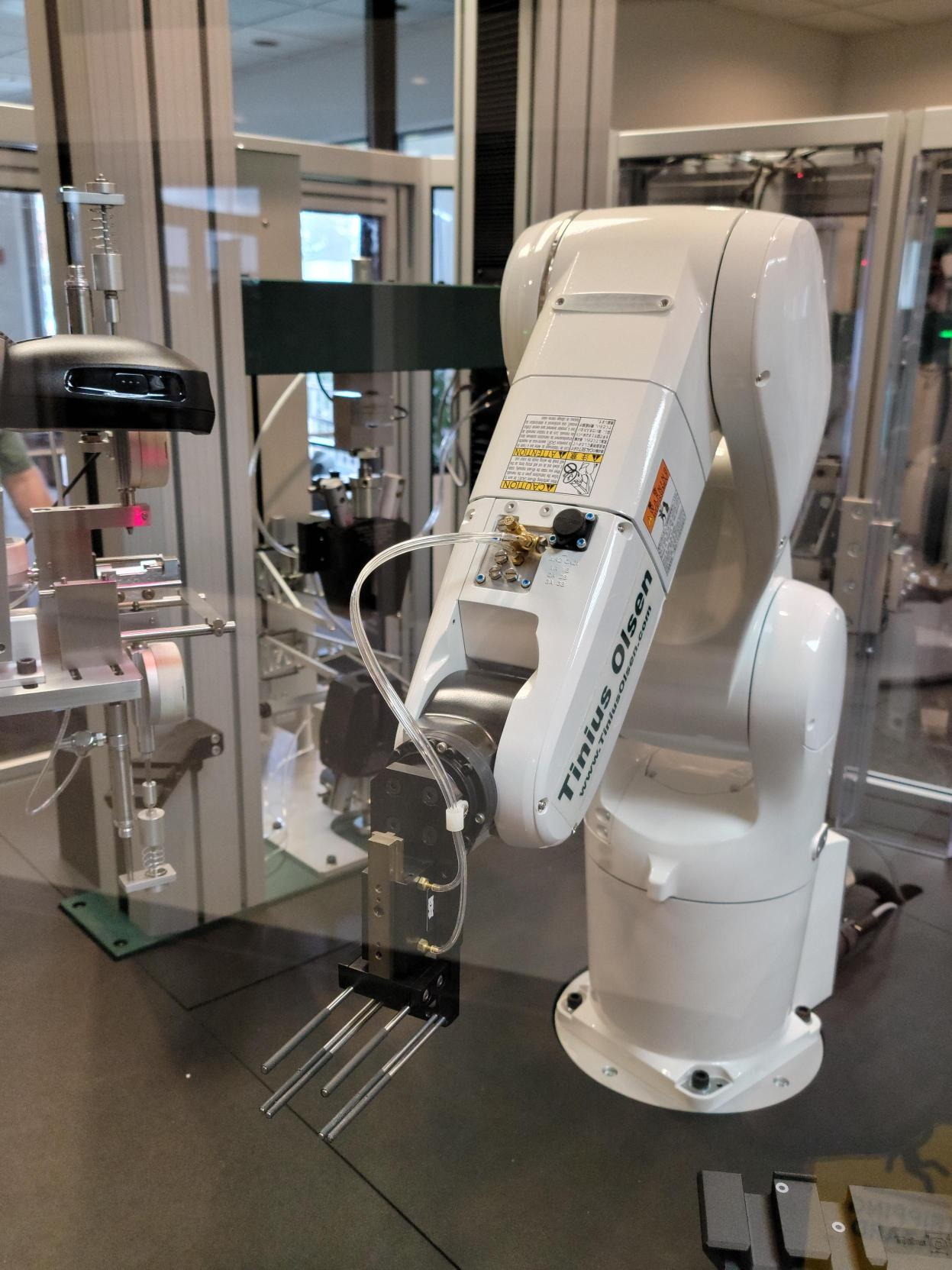
Image Credit: Tinius Olsen
One of the testing machine frames is for tensile tests and the other is for flexural tests - where both specimen types are accommodated by the test specimen feed and handling system, specimen measurement, and barcode-led data flow.
From the client’s perspective, data integration is seamless, with data and specimens going in and spent specimens and data coming out.
What happens inside that testing cell - like the data determining the history of the incoming test specimen passed digitally from the client’s process to the testing cell, supplemented with the results data and pass/fail status post-test, and then returned digitally to the client’s process, where it is immediately accessible by the manufacturing process team - appears as a simple a block on the client’s process flow chart with a verified calibration status.
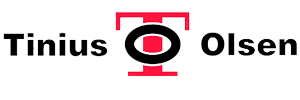
This information has been sourced, reviewed and adapted from materials provided by Tinius Olsen.
For more information on this source, please visit Tinius Olsen.