The Cetex brand of thermoplastic unitapes and laminates from Toray are used in a wide range of aircraft structures, ranging from floor panels, keel beams, luggage bins, and galleys.
Thermoplastics offer very low FST properties, can be formed easily, and offer productivity savings with short mold cycles, high quality finishes off tool, excellent moisture resistance, and durability. Figure 1 shows fire retardant structural materials for aircraft interiors.
.jpg)
Figure 1. Fire retardant structural materials for aircraft interiors.
Toray Cetex Products
These include the following:
- Toray Cetex TC925 FST is a polycarbonate resin version that offers a new low-cost alternative with less than 25/25 OSU performance.
- Thermoplastic fasteners can be friction-welded to minimize core fill and lighten the panel weight.
- Toray Cetex thermoplastic laminates are used as a lightweight option on current commercial aircraft.
- Toray Cetex thermoplastic laminates are used in diverse applications from flooring and seating, to galleys and luggage bins. They offer OEM's the highest FST resistance in a durable and long-lasting composite structure.
- For additional interiors composite solutions, low FST bulk molding compounds allow users to design complex parts to replace metal while maintaining the lightweight, high strength of composites.
These are shown in Figures 2, 3 and 4
.jpg)
Figure 2. Toray Cetex thermoplastic laminates.
.jpg)
Figure 3. Toray Cetex RTL.
.jpg)
Figure 4. Thermoplastic fasteners.
Materials Selection Guide: Interiors
The materials selection guide for interiors is shown in Table 1.
Table 1. Materials selection guide for interiors
Product Name |
Resin Type |
Tg |
Cure Temp/ Cure Time |
Description |
Key Resin Characteristics |
Prepregs* |
Toray Cetex®TC925FST NEW |
Polycarbonate (PC) |
307°F/153°C |
• Process temp* - 437°F/225°C |
• Value orientated solution
• Good FST performance (OSU < 25/25)
• Translucent laminate provides good chemical performance
• Ideal for flooring, seating and small parts |
See the datasheet for details. |
Toray Cetex® TC1000 premium |
Polyethermide (PEI) |
419°F/215°C |
• Process temp - 600°F/315°C |
• Qualified and certified to OEM specifications
• Excellent FST performance (OSU < 15/15)
• Industry-leading mechanical performance
• Good solvent resistance
• Ideal for interior applications ranging from floor panels to seat plinths to luggage bins |
See the datasheet for details. |
Toray Cetex® TC1000 design |
Polyethermide (PEI) |
419°F/215°C |
• Process temp - 600°F/315°C |
• RTL for customer design programs
• Excellent FST performance (OSU <15/15)
• Range of colors and textures available
• Significant weight reduction in metal replacement programs |
See the datasheet for details. |
Toray Cetex® TC1100 |
Polyphenylene Sulfide (PPS) |
194°F/90°C |
• Process temp* - 625°F/330°C |
• Offered on either glass or carbon exhibits moderate temperature capability and features:
- High impact resistance
- Low flammability
- Low moisture absorption of 0.02%
• Ideal for leading edges, structural aircraft parts including interior beams and floor panels |
See the datasheet for details. |
Toray Cetex® TC1200 |
Polyetheretherketone (PEEK) |
290°F/143°C |
• Process temp* - 725°F/385°C |
• Thermoplastic unitapes and fabrics either glass, carbon or aramid with PEEK resin
- Outstanding solvent resistance
- Low flammability |
See the datasheet for details. |
TC264 |
FR Epoxy |
266°F/130°C |
• Cure temp - 260°F/127°C |
• Ideal for use in applications where flame retardancy is needed such as air management system ducting, decorative enclosures, and fire retardent composite panel assemblies |
See the datasheet for details. |
TC550 |
FR Epoxy |
246°F/119°C |
• 75 minutes at 280°F/138°C |
• Low FST prepreg for interior ducts, meets 12-second vertical burn |
See the datasheet for details. |
Ancillary Materials* |
Bostik sharnet 4275 |
Polyester |
N/A |
Melt temp - 230°F/110°C |
• Lightweight
• High peel strength |
Call for details. |
Aluminium Honeycomb |
N/A |
N/A |
See datasheet |
• Aerospace grade available in corrosion-resistant 5052 and 5056 alloys either in honeycomb ell or Flex-Core® configuration |
See page 25 for details. |
Nomex® Honeycomb |
N/A |
N/A |
Service temperature up to 365°F/180°C |
• Excellent fire-resistant and self-extinguishing properties for FAR 25.583 |
See page 25 for details. |
TC263 NEW |
Epoxy |
230°F/110°C |
120 minutes at 250°F/12rC |
• Toughened firm adhesive |
See page 25 for details. |
* Thermoplastic composites do not cure, instead we show the processing temperature used to form parts. Nomex® is a registered trademark of DuPont.
Thermoform Processes
The thermoforming process in shown in Figure 5.
.jpg)
Figure 5. Thermoforming process.
The steps of the thermoforming process are:
- Use pre-assembled panel or assemble panel
- Move to press/IR Heating
- Remove and place in form
- Form under high pressure or vaccum bag
- Cool and remove
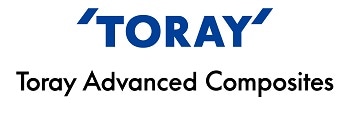
This information has been sourced, reviewed and adapted from materials provided by Toray Advanced Composites.
For more information on this source, please visit Toray Advanced Composites.