Ulm-Einsingen – based Zwick started the manufacture of testing machines back in 1938 and grew, in the ensuing decades, to become one of the world’s leading manufacturers of machines for materials testing.
The company's product range encompasses materials testing machines for tensile, compression and bending tests on material specimens, work pieces and components. To enable the testing systems to work 24/7 and with consistent accuracy, Zwick automate specimen handling using robots from KUKA.
The fact that cell phones and remote control units are comfortable and pleasing to hold is due to extensive advancements in the field of materials research. The properties of the materials that are used in production must be defined by steel and plastic manufacturers.
In a large number of cases, several trials are required before the desired material properties are achieved.
Safe Handling of Specimens by Robot
Zwick uses KUKA robots for specimen handling and moveing the test objects from A to B. Specimens range from strips of metal to parts for medical devices such as insulin pens. Testing of steel bars measuring up to 700mm in length and weighing up to 15kgs can also be achieved.
According to Robert Kaifler, Automation Product Manager at Zwick, in almost 80 to 90% of the cases, a specimen is destroyed. The resulting control parameters are subsequently fed into the production system to optimize it. The principle is the same whether the system is a steel rolling mill, an injection molding machine or a machine for manufacturing insulin pens. Figure 1 shows the robotic test system for automatic metals testing.
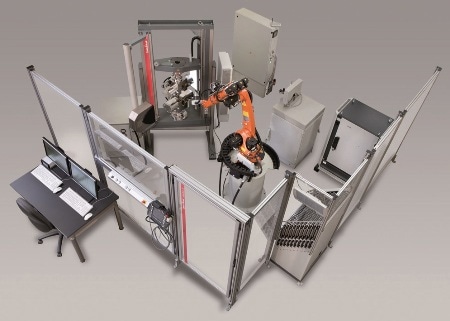
Figure 1. Robotic test system for automatic metals testing
Utmost Precision for Highly Accurate Measurements
Materials testing requires the highest possible accuracy - even a very small deviation in motion can cause a change in the material characteristics. Hence Zwick has been automating its materials testing machines with KUKA robots for over 10 years. This robotic testing system aims at reducing deviations to a minimum.
The key task of the KUKA robot is the exact loading and positioning of the material to be tested. It is only with a robotic system that material testing has a reproducible process without loss of value, as the cycles are fixed. Figure 2 shows the automatic testing of insulin pens.
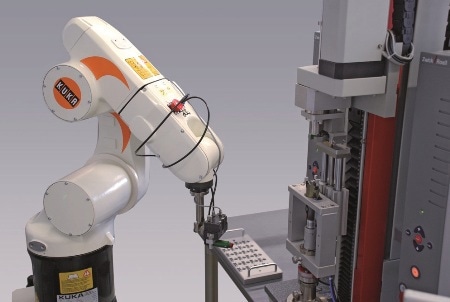
Figure 2. Automatic testing of insulin pens
There has been a considerable rise in testing volumes in recent years, but the number of employees in the laboratory is constantly decreasing, meaning the available employees can only be used for value-adding work. Monotonous tasks and repetitive procedures that nonetheless require maximum accuracy are reliably performed by the KUKA robot, around the clock if necessary.
Safe Movement of Specimen
Temperature plays a decisive role when materials are tested in the plastics industry. For instance, if a specimen is touched by hand, there is a change in material characteristics because of body temperature.
One way of attempting to filter out this negative effect is to use a robotic hand at room temperature. A normal test takes between one and three minutes. Figure 3 shows the specimen feeding system for composites testing.
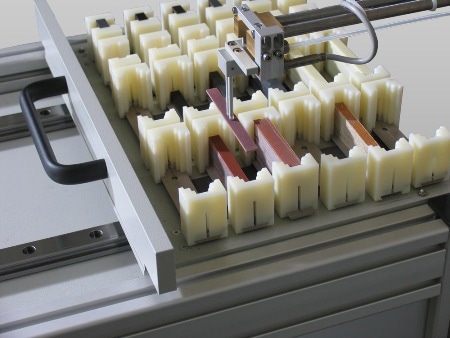
Figure 3. Specimen feeding system for composites testing
Automated Testing Systems – in Operation Worldwide
Standard tests are mostly conducted by Zwick customers and cost reduction is the primary objective according to Robert Kaifler. 80% of applications for KUKA robots with the Zwick testing systems involve destructive testing, while 20% are accounted for by non-destructive materials testing. The most commonly used robot types are the KR6, KR30 and KR60 and Zwick has installed at least 100 automated systems in operation worldwide.
Plannable and Traceable Sequences in Medical Technology
While testing medical products, reproducibility of test results is indispensable. Hence Zwick developed a fully-automatic system for testing insulin pens. A zwicki-line materials testing machine with integrated torsion drive, combined with a KR 5 from KUKA, ensures exact and cost-effective testing.
Zwick has been more actively involved in the field of medical technology for some years. The testing machine measures the dosage setting and triggering force and calculates the administered dose in one continuous process. Test methods on the two test axes can be modified and combined as needed.
An automated specimen feed is carried out using the robotic handling system, so changes to the test results caused by operator influence is eliminated.
The test process is considerably more efficient by the increased specimen throughput, while testing can also be performed manually at any time if required.
The automated Zwick testing systems can also be used to test the force required to unroll gauze bandages, the material properties of dental syringes or the child-proof caps of medicine containers.
Using KUKA’s powerful and open control concept, Zwick can adapt the testing systems to the specific requirements of the end customers. Furthermore, there is a wide range of expansion options available, making it easy to adapt the robot to changing requirements or new tasks.
About Zwick
Zwick is one of the top-ranking manufacturers of static and dynamic materials testing systems worldwide. With our extensive portfolio of testing machines, systems, and software we supply customized solutions for almost all test tasks required in the area of modern mechanical materials testing.
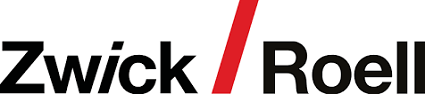
This information has been sourced, reviewed and adapted from materials provided by ZwickRoell GmbH Co. KG.
For more information on this source, please visit ZwickRoell GmbH Co. KG.