Harper has a client which supplies uranium and produces uranium fuel bundles. This client provides uranium products to CANDU nuclear energy plants for production of clean energy both safely and reliably. It is licensed to produce 1,200 tons of uranium as finished fuel every year.
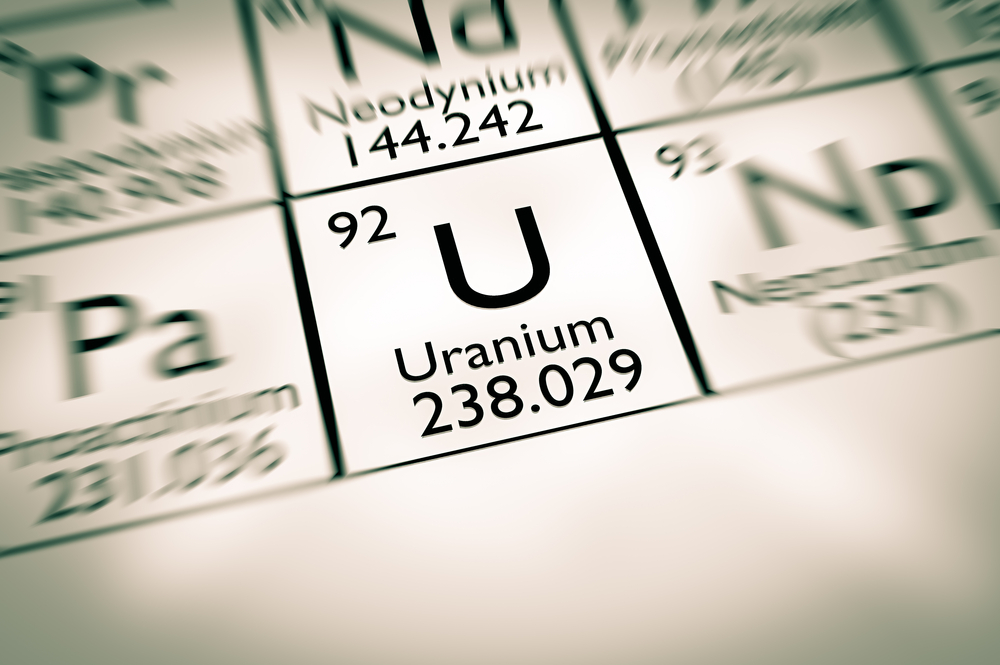
Image Credit: Shutterstock/Antoine2K
Objective
Maintaining safe, consistent and effective operation and delivering superior quality products are the key objectives of this uranium producer. To achieve operational reliability, this client along with Harper launched a support program by setting short-term and long-term objectives. Short-term goals set included: rebuilding two production lines, assessing strategic parts inventory, customizing training program for site personnel and qualifying three new production line installations.
Long-term objectives set included: the continuation of projected rebuild schedule, implementation of strategic parts program, data analysis for predictive maintenance and documentation of best practices for ongoing training.
Assessment of Equipment Condition
The client's facility used Harper’s equipment which included a range from the latest as well as equipment which dated back to the early 1980s. Root causes were identified during the initial rebuild through inspection that showed deterioration of key parts, which had a direct impact on the product quality and measured consistency. The list of parts affected are found below:
- Material buildup along hearth plates at high temperature zones on the tow path
- Furnace’s pressure control
- Elevated amperage conditions in high temperature zones (tuning SCR’s)
- Deposition of production material on the pusher plate’s bottom stack, resulting in a jack-knife effect within the furnace
- Banking (idling) the furnace to balance throughput
- Humidifier system operation (lack of knowledge on the significance of dew point control)
Implementation
As part of the program, a dedicated team was formed by Harper and the client in order to determine the actual operating conditions of key equipment components and to establish a supply scheme during each rebuild. The team determined that flow, internal pressure and atmosphere were the key factors affecting the operational reliability.
Refining process controls to define best practices and enabling documentation improvements to address the issue of staff change due to promotion or retirement were also part of the effort.
After successfully implementing the short-term objectives, Harper’s PulseTM group initiated long-term objectives with the help of its experienced staff comprising Technical Support Engineers, Service Technicians, and Process Technology Specialists (Figure 1).
.jpg)
Figure 1. Harper’s comprehensive Pulse™ team service helps clients achieve manufacturing excellence
Process Technology
The misalignment of the nitrogen curtain was corrected to restore pressure control. This misalignment formed a negative pressure region and allowed an air flow which deteriorated the internal refractory components. A steady internal profile was maintained by tuning the controls to throttle pressure when the furnace door is opened and closed.
Maintenance Training
The sintering process requires a very efficient control over the dew point. Moisture needs to be introduced into the gas stream to allow changing the mechanical properties of the material corresponding to the temperature. One of the findings was the improper use of the humidifier system. Hence, Harper documented the necessity to operate the humidifier system properly and conveyed the information during site training.
Operational Support
A long heating and cooling cycle is required for high temperature furnaces. The idling temperature can be lowered by banking the furnace when there is a change in the production demand without the need to completely cycle the furnace. Banking the furnace is not always recommended but it may be required when there is a change in the requirements of customers. Harper’s engineering group recorded the recommended protocol for banking the furnace.
Conclusion
A new level of timely aftermarket service is required to achieve superior quality, reliability, performance, stringent delivery schedules and minimal downtime in both domestic and international markets. Harper’s comprehensive Pulse™ team service provides a quick-turnaround replacement of genuine parts, proactive preventative maintenance programs, domestic and international field service, engineered solutions, and one-call technical support to address the service and maintenance requirements of customers.
About Harper International
Harper International is a global leader in complete thermal processing solutions and technical services essential for the production of advanced materials. From concept to commercialization, from research scale to full production line operations, Harper is perpetually on the cutting edge of the most innovative furnace and oven designs in the world. For decades, they have pioneered some of the most unique, customized systems available, with a focus on processing materials at high temperatures up to 3000°C and in non-ambient atmospheres.
Harper serves advanced, cutting-edge material markets including Fibers & Filaments, Powders, Metal Oxides, Technical Ceramics, Rare Earths, Graphene, Energy Device Materials and Nuclear Materials. Their support to these emerging industries begins in early stages of research and development, whether at corporate R&D centers, universities, government institutions, or start- ups. Harper is a partner through the entire development process assisting in the scale up and commercialization of advanced materials that will change our everyday lives.
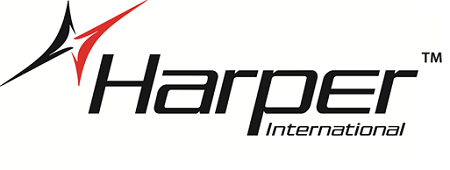
This information has been sourced, reviewed and adapted from materials provided by Harper International.
For more information on this source, please visit Harper International.