Many different fabrication processes are available to make advanced composite structures. However, the available options begin to narrow if highly intricate components with superior performance need to be produced at higher volume production rates. Compression molding with long chopped fiber thermoplastics is one of the methods that can fulfill these requirements.
Compression Molding
Compression molding involves forming of complex shaped components by molding of a charge of fiber reinforced prepreg bulk molding compound (BMC) under heat and high pressures. Unidirectional fiber reinforced thermoplastic tape is cut into long lengths of 6.4-50.8mm to create the BMCs (Figure 1).
Then, an exact amount of these loose chips or strands is weighed out to fill the volume of a specific tool located in a matched metal mold. The subsequent heating and compression of the material to pressures makes the fibers to flow and reach every complex feature in the mold cavity before cooling.
.jpg)
Figure 1. Bulk molding compound. Image Credit: Toray Advanced Composites
Thermoplastic BMC Compression Molding
Thermoset compression molding generally does not require a degree of mold temperature control. However, it is essential in the case of thermoplastic BMC compression molding.
Xpress is the tooling concept used by Toray Advanced Composites/CCS to achieve a tight control over the mold temperature in zones above the surface of the component.
This Xpress process has been used to mold a carbon fiber/thermoplastic bracket with intricate features and flat plates. Molding and testing of structural test coupons will be carried out to characterize strength and stiffness. Components can be designed using these BMC materials with the help of sophisticated design and analysis routines.
Thermoplastic Bulk Molding Compounds
Since the 1990s, long, discontinuous fiber, thermoplastic composites have been used to make compression molding components. Materials such as polypropylene and fiberglass were used in some automotive applications. Thermoset based sheet molding compounds (SMC) had been in use before this period and are still used.
For the past several years, SMCs have been used by the aerospace industry to make secondary structures such as covers. SMCs are different from BMCs, which are composed of chips, chopped flakes, or lengths of prepreg fibers instead of a continuous sheet of material consisting of continuous or discontinuous fibers.
The high strength and stiffness characteristics of carbon fiber make it suitable for the aerospace industry. Aircraft structures, as shown in Figure 2, have been fabricated using carbon fiber thermoset BMCs.
.jpg)
Figure 2. V-22 access door. Image Credit: Toray Advanced Composites
Thermoplastic BMCs are considered as an alternative material solution to thermoset SMCs/BMCs in areas demanding faster part production times, inherently low flame-smoke- toxicity (PST), and better durability.
Processing of thermoplastic BMCs needs to be carried out at temperatures higher than that of many thermosets. During cool down, a higher degree of temperature control is required in order to maintain the crystallinity of the polymer and to achieve an even cooling profile throughout the component.
A range of BMCs has been developed by Toray/CCS, containing the four major aerospace grade thermoplastic polymers such as PEKK, PEI, PPS, and PEEK with many different types of fibers. The XPress process allows molding of these compounds under consistent and rapid heating and cooling with monitoring of the tool surface, thus minimizing part warpage, internal and surface defects.
Advantages of Compression Molding
Plastic and composite materials are increasingly used in place of metallic structural components owing to characteristics such as lightweight, high strength, high stiffness and better resistance to corrosion.
Fast production time, cost savings, and the ability to incorporate complexity that is hard to machine with metals are the advantages of injected molded plastics over metallic fabrication processes. However, injected molded plastics are inferior to most metals in terms of strength and stiffness even if short fibers are added to them.
Continuous fiber composites such as woven fabric prepregs and unidirectional prepregs fabricate structures with strength and stiffness better than the metal components they substitute.
However, they have limitations in the fabrication of complex geometries.
These shortcomings can be addressed with long, chopped, discontinuous fiber, thermoplastic composites, which have strength and stiffness comparable to or better than some metals. Furthermore, they can be used to fabricate parts with very complex geometries.
Conclusion
A range of BMCs is used in the fabrication of long, chopped fiber, thermoplastic, compression molded composite parts. The XPress process with multi heating zone tooling solves the problem of temperature control at different points within a component being molded.
Thermoplastic BMCs are mainly used as an alternative material solution to metallic components with complex geometries and provide advantages such as lighter weight, corrosion resistance, and high specific strength and modulus. Inherent FST characteristics, superior toughness, and high production throughput are the additional benefits of Thermoplastic BMCs over thermosets. The availability of sophisticated software tools alleviates the difficulties involved in the design and analysis of these BMC materials.
For additional technical information, please contact Toray by email at [email protected].
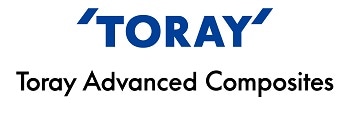
This information has been sourced, reviewed and adapted from materials provided by Toray Advanced Composites.
For more information on this source, please visit Toray Advanced Composites.