FePt films hold promise in the field of heat assisted magnetic recording (HAMR). These films need high bulk magnetocrystalline anisotropy energy constant and isolated grains with a uniform size below 6 nm. The preparation of FePt thin films is carried out by performing RF sputtering on a silicon substrate from a multi-layer, multi-target sputtering system.
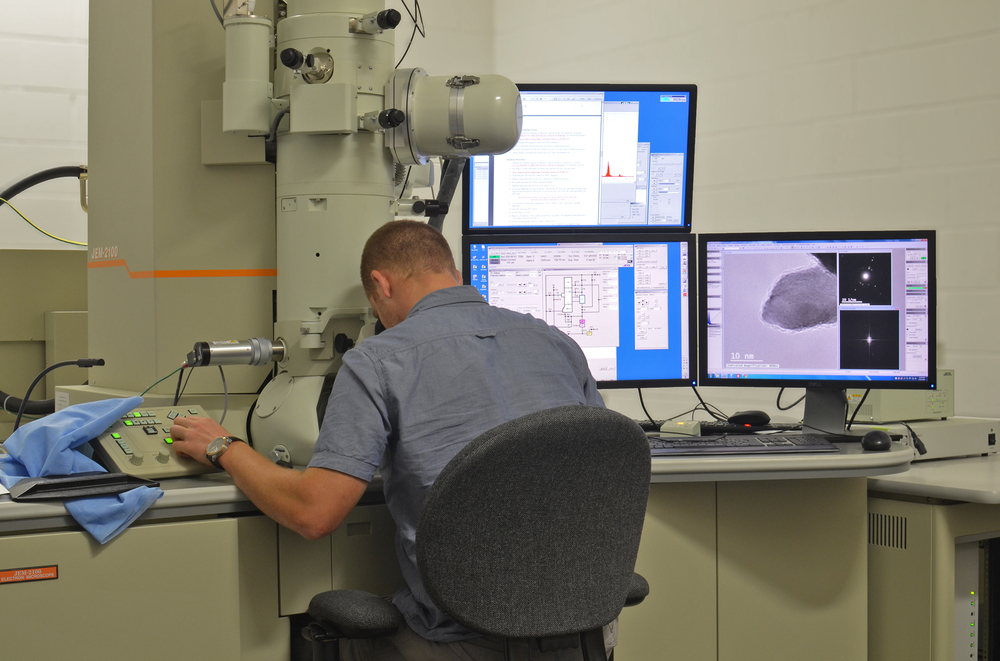
Image Credit: Shutterstock/Rui Serra Maia
The in situ heating temperature, sputtering power and argon gas pressure are all parameters, which may impact the magnetic properties, microstructure and applicability of these materials for HAMR. Hence, it is important to evaluate the impact of each of these processing parameters by preparing multiple samples and modifying one parameter at a time.
As statistical data is needed, transmission electron microscopy (TEM) and a method for producing a large electron transparent area is required. This article covers the specimen preparation procedure for enabling observation using the TEM.
Specimen Preparation Procedure
To reach a valid conclusion when comparing thin film samples, it is important to significantly reduce differences that may occur during preparation by using the right preparation procedure. Before observing the specimens in a TEM, they are prepared using a number of mechanical polishing steps, and after that, Ar+ ion milling. Both ion and mechanical thinning can induce artifacts in the specimen. Hence, to compare the microstructure of various samples with differing process parameters using TEM, preparation to electron transparency must be the same for all the specimens.
A diamond scribe was used to cut 3 mm plan view specimens from each type of material. The specimens were then mechanically polished flat from the silicon substrate side to below 100 µm, then further thinned to below 15 µm in the dimpled area using a Gatan dimple grinder. The specimen was then mounted on a clamp type DuoPost (dimple side up) and inserted in Gatan's Precision Ion Polishing System (PIPS™) II. The dimpled area can be centered with respect to the center of rotation and, and it is possible to center the Ar ion beams to an accuracy of a few micrometers.
It has been observed from the TEM study of specimens, previously made using an older model PIPS™, that polishing till perforation results in the areas surrounding the hole to curl, making it impossible or difficult to image the area of interest in the TEM. To prevent this from taking place, it is important to control and stop Ar milling prior to perforation. Using the PIPS™ II allows continuous monitoring of the remaining thickness and reliable halting of milling at the correct point. Optical image capturing was performed with the digital camera in the PIPS™ II, which is capable of capturing and storing high resolution images from each rotation of the specimen during milling.
While developing the preparation technique, test specimens were positioned in the PIPS™ II and milling was carried out until perforation. After milling, these image sets were checked in a 3D stack in order to study how the milled area appearance changed in PIPS™ II with both thickness and time.
Observations and Inferences
As milling began, the specimen was thinned and white light fringes developed at the centre of the milled area before continuing to grow towards the outside. (Figure 1a)
Two deep purple fringes were observed, then a yellow fringe was seen before the center area became black or gray. After studying a number of specimens, it was concluded that perforation takes place just after the fringes stop being seen in the center and this region becomes black or gray (Figure 1c). From the rear side of these specimens, ion milling was performed. Most of the Si substrate was removed by the milling, and the only FePt thin film was left.
.jpg)
.jpg)
.jpg)
Figure 1. PIPS™ II camera images. (a) early stages of milling, white light fringes start to appear. (b) mid stages of milling, white light fringes grow from inside the milling area toward the outside. (c) right before perforation: fringes stop growing and milling area starts turning dark gray/black.
Both guns were adjusted to mill at 9° Top and 3.5 kV energy based on these observations. Double beam modulation was employed during the milling to avoid sputtering of DuoPost® clamp material on the specimen.
Milling continued until white light fringes were seen in the PIPS™ II camera image (Live Mode). Beam energy and milling angle were then reduced to 2.5 kV and 7° Top respectively, and milling resumed until the first deep purple fringe could be observed. Next, the beam energy and milling angle were reduced to 1.0 kV and 6° Top respectively, and milling continued until the second deep purple fringe was seen. Milling then continued at 0.1 - 0.5 and 6° Top until most of the Si substrate was removed and the milling area began changing color to dark gray or black. PIPS™ II camera images of two other specimens, immediately after stopping milling, are shown in Figure 2.
.jpg)
Figure 2. Milling was stopped as soon as white light fringes stopped appearing and the center of milling area turned dark gray/black.
The samples were taken out of the PIPS™ II and imaged in TEM (Figure 3). After observing specimens from different samples prepared as mentioned, the effect of temperature, power and pressure was characterized on FePt thin film [Granz and Kryder 2012; Granz, Barmak and Kryder 2012].
.jpg)
.jpg)
Figure 3. TEM micrographs of two different growth conditions of FePt thin films. Specimens prepared in PIPS™ II and imaged in a JEOL 2000 EX TEM.
Conclusion
To conclude, a number of features in the Gatan PIPS™ II were used for making identical preparation route of several specimens, explained here:
- X-Y stage movement helped in bringing the dimple area of each specimen to the center of rotation with accuracy of a few microns.
- The automated gas flow control helped to operate the ion guns at optimized conditions and to reliably repeat identical conditions from specimen to specimen.
- Low energy milling (0.1 kV to 0.5 kV) helped to mill most of the Si substrate without perforation, whilst maintaining an electron transparent region with repeatable results.
- Being able to observe previous 3D image stacks of specimens helped the understanding of milling characteristics of the material (change in white light fringes and perforation).
- Being able to observce the specimen in PIPS™ II camera Live Mode, and knowing its milling characteristics, allowed the milling to be stopped immediately before perforation.
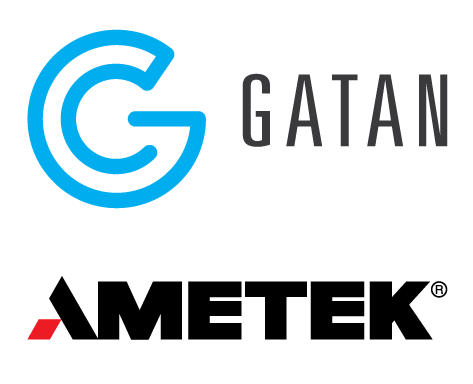
This information has been sourced, reviewed and adapted from materials provided by Gatan Inc.
For more information on this source, please visit Gatan Inc.