Waterborne coatings do not have a priori, the same advantageous rheological properties as solvent-based coatings. If not formulated correctly, they display inferior characteristics with regard to flow properties, leveling, application properties, film build, etc. The performance of waterborne paints can be improved through the addition of thickeners and rheological modifiers. The addition of traditional thickeners such as inorganic clays and high molecular weight polymers improves the viscosity during application, but delivers inferior spatter resistance and leveling to the paint.
Associative thickeners such as low molecular weight, water soluble polymers improve the overall performance of waterborne coatings. Associative thickeners reduce viscosity at high rates, thus providing low roller spatter and good film build. Furthermore, they maintain a low viscosity at low rates, thereby improving flow, gloss and leveling. The disadvantage is the instability of these systems (phase separation) and the strong pH dependence, which influences the ionization of the carboxyl groups of the latex surfactants.
Rheological Characterization of Water-based Coatings
The rheological characterization of coatings is generally carried at low shear viscosity (LSV) 0.001 to 1s-1, medium shear viscosity (MSV) 1-1000s-1, and high shear viscosity (HSV) 103 to 106s-1 (Figure 1). The consistency of a coating (i.e., appearance, pouring and mixing behavior) is defined by MSV. ASTM D562 (Stormer viscosity), ASTM D2196 (Brookfield spindles), and DIN53019 are typical test standards.
.jpg)
Figure 1. Viscosity of structural coatings
The HSV correlates to coating application conditions like brushing, rolling, etc. The cone/ plate viscosity test at 104s-1 is the standard test method (ASTM D4287-88). Typical paints are adjusted to 50–150 mPas for low drag during application. The LSV correlates to all low rate processes like leveling, sagging, settling, etc. The LSV is usually determined at 0.3s-1. Leveling will be improved if the viscosity range is 25-100Pas. Sagging will occur if the viscosity is below 10Pas.
Yield stress measurement is also performed for the characterization of the paint in the low rate region. A profile for a good thin film water-based coating is given in Table 1:
Table 1. Profile of a thin film waterborne paint
Coating Process |
Rate (1/s) |
Viscosity (Pas) |
Yield Stress (Pa) |
Storage |
0,1 |
>50 |
>1 |
Transfer to brush w/o dripping |
0 |
>2.5 |
>1 |
Transfer to substrate with good film build and w/o excessive brush drag |
104 |
0.1 to 0.3 |
>0.25 |
Drying with good levelling and minimum sag |
1 |
5 to 10 |
>0.25 |
A yield stress τ y larger than 1 Pa and a LSV above 50 Pas (at rest, before mixing) are typical values to prevent settling during storage. Good leveling and flow is obtained if τ y is smaller than 0.25 Pa after high shear mixing. Table 1 shows a table with typical values for the viscosity and yield stress at different rates, giving a profile for good thin film water-based coating. It is necessary to maintain a low elongation viscosity and elasticity for a paint to avoid spatter and stringing.
Application Examples
Storage Stability and Shelf Life
The LSV correlates to the storage stability of paint. However the LSV is a single point measurement and does not provide adequate data to understand the complex settling mechanisms under gravity and their effect on the long-term shelf life of a product. Measuring the rheological behavior, yield stress, and yield point is crucial for formulation of coatings with the desired long-term stability.
The long-term stability of coatings can be predicted using the knowledge about the network structure and its ability to resist internal (Brownian motion) or external forces (gravity, vibrations) less than the yield stress. Yield stress can be directly measured from the viscosity maximum during a stress ramp (Figure 2). However, careful control of the test parameters is essential due to their influence over the yield stress value.
.jpg)
Figure 2. Yield point from a stress ramp experiment for a latex paint
Yield stress and yield point from the on-set (critical strain) of nonlinear behavior can be determined with the dynamic strain sweep (Figure 3). The material structure data can be obtained from a frequency sweep at strain amplitude less than the critical strain (Figure 4). A key parameter is the tan δ, the ratio of energy dissipation and storage mechanisms down to low frequency. If tan δ is in the range of 1-1.5, the material exhibits optimum storage stability.
.jpg)
Figure 3. Strain sweep to determine yield stress and yield point
.jpg)
Figure 4. Frequency sweep to characterize the material’s structure
High tan δ values mean that the flow is predominantly viscous and there is only weak association between the particles. As a result, under gravity, sedimentation cannot be prevented by the inter- particle forces. Low tan δ values will occur because of strong interparticle interaction (higher elasticity). Low tan δ values result in coalescence and the generation of large aggregates, which also settle with time.
Leveling and Brush Marks
Brush mark leveling involves two opposing forces (surface tension and viscous force) for a drive to equilibrium and smooth surface (Figure 5). As the surface tension σ, the film height h, and the wavelength of the brush marks λ do not change much, the depth of the brush marks relies predominantly on the leveling stress τ.
.jpg)
Figure 5. Leveling of brush marks
Leveling ends when τ becomes equal to the yield stress τy, it is then possible to calculate d from the yield stress. The viscosity increase must be rapid to avoid sagging, but needs to be slow enough at the same time to allow leveling to take place (Figure 6). Figure 7 shows the determination of the thixotropic index from the thixotropic loop test. There is no good correlation between the thixotropic index and the application behavior under all conditions.
.jpg)
Figure 6. Recovery of structure
.jpg)
Figure 7. Thixotropic loop test
Rheology During Roller Application
Slender strings or thin fibers are formed if coatings have high elongation viscosity. They lengthen and eventually break during application, snapping back onto the roller and the substrate and producing spatter by forming small air-borne paint droplets due to the release of energy stored in the elongated fibers. Coating tracks or surface patterns are also created on the substrate by the same mechanism.
The elongation viscosity for some dispersion with various levels of spatter resistance is shown in Figure 8. The elongation viscosity does not increase with the addition of associative thickeners as they form a structure breaking at high rate and therefore no energy can be stored during deformation to cause spatter.
.jpg)
Figure 8. Elongation viscosity of conventional thickeners with different molecular weight
Film Build During Drying
The Mooney equation can describe the viscosity during the film formation of a latex dispersion (Figure 9). During solvent evaporation, the viscosity increases and so the particle volume fraction increases. Capillary forces dominate the particle-particle repulsion forces when the particles approach each other, causing coalescence into a solid film. The polymer latex is plasticized by less volatile solvent during the final stage of evaporation to aid film coalescence.
.jpg)
Figure 9. Viscosity increase during drying
The solid content of the coating greatly affects the film building, providing poor sagging behavior during application over vertical surfaces when the solid content is high. The viscosity becomes a minimum for high solid content coatings during drying and curing at high temperatures (Figure 10), influencing the film thickness and the sagging performance.
.jpg)
Figure 10. Viscosity during drying and curing of two coatings with different solid loading
Heating rate also affects the viscosity during cure. Faster curing is achieved when the temperature increase is rapid, but the viscosity minimum is lower (Figure 11). For low heating rate, the viscosity minimum is higher, but the total cure time is longer.
.jpg)
Figure 11. Cure profile as a function of heating rate
Performance of the Coating Film
The performance properties of the final coat are correlated with the glass transition of coating film. The Tg (crosslinking density) is higher when the curing temperature is higher. The glass transition is measured by observing the drop in modulus as a function of temperature (Figure 12).
.jpg)
Figure 12. Tg as a function of the cure temperature
Impact resistance is a key parameter for automotive coatings. Impact times for gravel are typically in the order of 10ms. The DMA traces, modulus and tan δ as a function of temperature must be shifted to a reference time of 10ms or a reference frequency of 105s-1 for predicting impact performance (Figures 13 and 14).
.jpg)
Figure 13. DMA trace of an automotive clear coat
.jpg)
Figure 14. Correlation of the impact resistance with the DMA trace referred to a frequency of 105s- 1
In Figure 15, no significant change in the Tg and the modulus is observed in the glassy state and the rubbery state for a crosslinked polyacrylate film pigmented with TiO2 rutile for concentrations up to 40% by volume. However, the temperature dependence of the modulus varies significantly at a critical pigment concentration, above the glass transition in particular. The rubber region disappears above the pigment concentration of 45% due to the reduced segmental mobility of the binder and the contributions of the modulus of the rigid particles.
.jpg)
Figure 15. Pigment (TiO2) concentration on Tg
Conclusions
Characterization of paints and coatings using rheology provides information about material flow during processing as well as the performance of the coating during application and of the final coating. Rheology is an important tool for formulation engineers to create paints and coatings with better application properties.
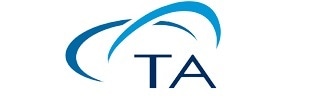
This information has been sourced, reviewed and adapted from materials provided by TA Instruments.
For more information on this source, please visit TA Instruments.