The significance of lightweight construction materials, especially carbon fiber reinforced plastics (CFRP), has gained popularity over the past few years. The material’s structural constitution is critical for its quality and using ZEN2 core software and light microscopy key micro-structural features can be quantitatively determined. The instance of CFRP cross-sections show the benefits of using ZEN 2 core software for such investigations.
ZEN 2 core is designed for light microscopic applications and efficient quantitative structural analysis of micrographs. An example includes a CFRP cross-section obtained using ZEN 2 core combined with the ZEISS Axio Zoom and V16 light microscope. CFRP components are mostly edited through machining and at that juncture, the quality of the components are significantly affected by the structural constitution.
ZEN 2 core can determine the key structural features that are significant for their ease of machining, two of which among others are the porosity and individual layer thickness. It is possible to report the analysis results using the previously layered out templates. In addition to that, the users can record the investigation as a ‘job template’ for repeated analyses. Hence, ZEN 2 core provides reproducible output data without wasting time.
Creation of Tile Overview Image
A CFRP component micrograph with 100 times magnification was chosen as a tile image. The image is set up using the ‘tiles interactive’ tool. The user should select magnification prior to the determination of corners as shown in Figure 1a.
The tile pattern is automatically interpreted using the ZEN 2 core software as shown in Figure 1b. The generated and stitched output micrograph is shown in Figure 1c, which can be used for further studies.
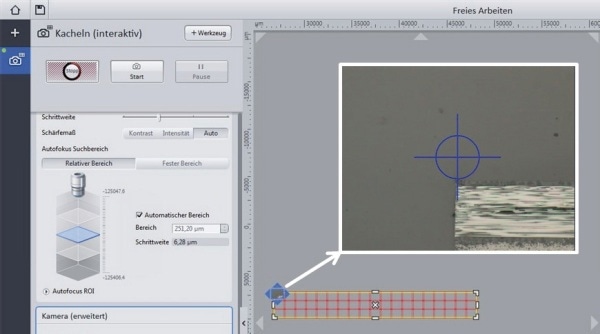
Figure 1a. Setup of the tile image using the tool ‘tiles interactive’, definition of the corner
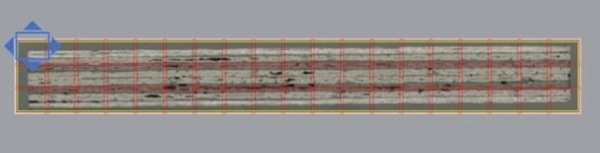
Figure 1b. Tile pattern

Figure 1c. Stitched overview tile image of the CFRP cross-section, 100×, coaxial light
Determination of Individual Layer Thicknesses and Component Measures
The tile image is used to quantify the thickness of the individual layer of the CFRP as shown in Figure 2a and its dimension in cross-section as shown in Figure 2b. The individual layer thickness measurement is performed at magnified regions of the tile micrograph.
Lengths and distances are measured using the ‘interactive measurement’ tool. The starting points must be considered to achieve appropriate results. The results are stored in a measurement table.
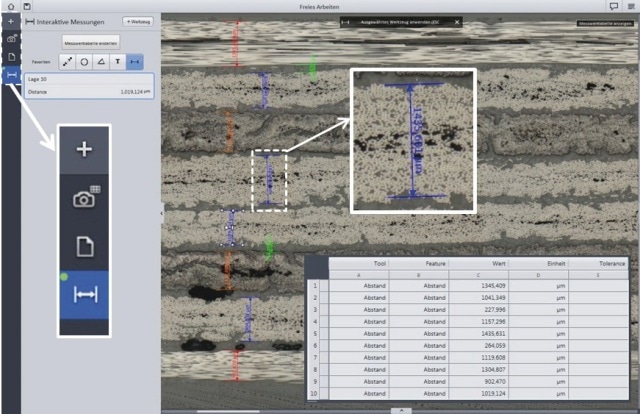
Figure 2a. Measurement of the individual layer thicknesses using the ‘interactive measurement’ tool

Figure 2b. Measurement of the component length and height, using the ‘interactive measurement’ tool
Porosity Measurement Using Image Analysis Wizard
Based on the tile micrograph of the CFRP cross-section, porosity measurements are carried out with quantitative structural analysis. The image analysis wizard is used for performing threshold analysis where the pores are segmented.
Figure 3a shows the automatic measurement tool - image analysis wizard. The measurement is initiated by defining the object and individual classes, selecting the favored measurement features and adapting the threshold value as shown in Figure 3b. Figure 3b shows the output image displaying the segmented porosity. Measurement tables having the selected parameters can be saved.
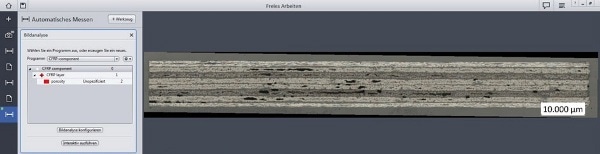
Figure 3a. Setup of image analysis wizard
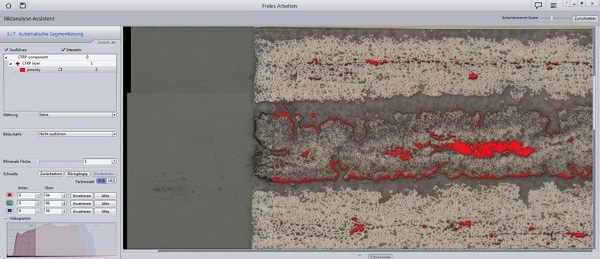
Figure 3b. Adapting the threshold value
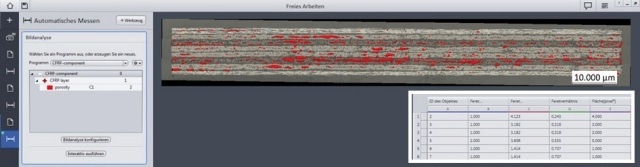
Figure 3c. Output image showing the segmented porosity (red) and output data table
Reporting Results
The results of the study can be precisely and efficiently documented using the ZEN 2 core software. The results such as the tables, micrographs, etc can be saved in previously layered out templates through MS Word.
The options for choosing the desired templates are shown in Figure 4a. The results are filled in the individual place holders for tables, micrographs, etc in the chosen template through clicking, as shown in Figure 4b.
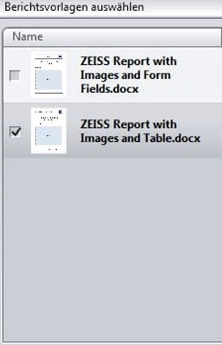
Figure 4a. Selection of favored template
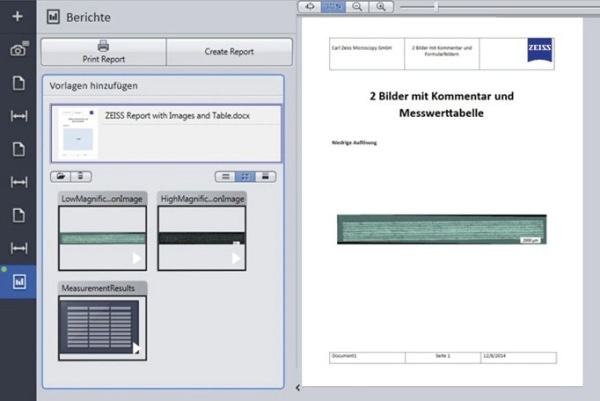
Figure 4b. Load up of investigation results
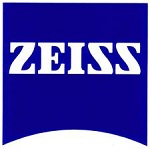
This information has been sourced, reviewed and adapted from materials provided by Carl Zeiss Microscopy GmbH.
For more information on this source, please visit Carl Zeiss Microscopy GmbH.