Toray Advanced Composites specializes in developing and producing next-generation thermoplastic and thermoset materials for aerospace and performance applications.
The company offers advanced composite prepregs that are based on thermoset and are available in two forms: unidirectional (UD) tape and fabric. Toray meets customers’ special handling and processing needs by using methods like direct impregnation and film impregnation. These methods help regulate the resin content and control the extent of impregnation. The company is capable of working on aramid, glass, and carbon-based reinforcements and different types of proprietary resin systems, spanning from high-temperature BMIs to low-cost epoxies.
With more than three decades of experience, Toray CFRT® and Toray Cetex® bring a new dimension to engineered and high-quality thermoplastic composite materials. Toray has the required know-how in semi-crystalline and amorphous thermoplastics that range from PMMA, PA6, and PP through to PEKK, PEEK, and PEI. They can also customize polymers to meet the unique application needs of customers.
Toray Cetex® thermoplastic materials come in a wide range of fabric-based laminates and UD tapes or prepregs that ease the component design and production processes. Toray CFRT is a continuous fiber-reinforced thermoplastic material that can be pre-consolidated and tailored to meet customers’ demands for parts.
Medical Applications
Toray offers different types of composite materials that are suitable for a wide range of applications within the medical sector. The company continually invests in product development and offers a complete set of thermoplastic and thermoset materials. These materials have been exclusively designed for use in medical applications, such as components of MRI scanners and C scanners, X-ray couches, mammography plates, tables, surgical target tools, and devices. They can also be used in wheelchairs and walking aids, prosthetics such as springs and orthotics like an anterior foot, podiatric-correcting in-soles, and braces([R1] Figures 1, 2, 3, and 4).
.jpg)
Figure 1. C scanner arm manufactured from Toray E722 carbon fiber 500 gsm UD tape.
.jpg)
Figure 2. X-ray couch made with woven carbon with Toray E726 carbon fiber 205 gsm 2x2 twill and carbon 200 gsm UD tape.
.jpg)
Figure 3. Wheelchair and walking aids with Toray E722 carbon fiber 205 gsm 2x2 twill and 650 gsm 2x2 twill.
.jpg)
Figure 4. Orthotic foot inserts manufactured from Toray Cetex® TC951.
Toray’s materials offer the following properties:
- Excellent solvent resistance
- Heat resistance for steam sterilization
- X-ray transparency
- High strength to weight ratio
- Excellent cosmetic finish
- Excellent damping, resiliency, and shock attenuation
- Improved energy return (spring) and response
- Thin and lightweight design reduces weight, thus reducing stress and fatigue
- Customized properties with different degrees of stiffness
Thermoset Products
Toray offers medium temperature curing prepregs that are perfect for structural components. They are supplied in glass or carbon reinforcements in woven or UD tape format. Table 1 shows the properties and application of examples of thermoset products.
Table 1. Medium temperature curing prepregs.
Product name |
Resin type |
Tg |
Typical cure time / Cure temp |
Key product characteristics |
Application examples |
Reinforcement |
UD tape |
Fabric prepreg |
Toray E722 |
Epoxy |
120 °C (248 °F) |
60 minutes at 120 °C (248 °F) |
High rigidity |
Wheelchair frame, rims and mud guards |
Ο |
Ο |
Toray E720 |
Epoxy |
110 °C (230 °F) |
60 minutes at 120 °C (248 °F) |
Progressive flex, honeycomb bondable |
ARO (anterior foot orthoses), braces |
Ο |
Ο |
Toray E726 NEW |
Epoxy |
105 °C (221 °F) |
60 minutes at 120 °C (248 °F) |
X-ray transparent.
Higher degree of toughness.
Excellent drapability |
Prosthetic springs, X-ray couches, tables and mammography plates |
Ο |
Ο |
The company provides a kit cutting service as per customer specification for Toray thermoset products sold across Europe. Toray’s automatic cutting tool is employed in a well-controlled setting designed to improve the lifespan of materials. Different types of shapes can be cut. Customers can simply provide the size, a sample of the preferred shape, or a CAD file.
Thermoplastic Products
Toray Cetex® laminates have been specifically developed to meet the structural needs of high-volume applications, including orthosis. Table 2 shows the performance of thermoplastics, table 3 illustrates the size and dimension of Toray Cetex®, and table 4 shows the development of thermoplastics.
Table 2. Performance thermoplastics.
Toray Cetex® product |
Resin type |
Laminate |
Style |
Thickness (mm / in) |
Rigidity (N-cm2 / lb/in2) |
Modulus (GPa / Msi) |
Strength (MPa / ksi) |
TC951 |
PMMA |
TL-2100 |
Semi-Flex1 |
1.78 / 0.070 |
124 / 42.4 |
11.0 / 1.6 |
363 / 53 |
TC951 |
PMMA |
TL-2100 |
Semi-Rigid1 |
2.29 / 0.090 |
240 / 82.0 |
9.7 / 1.4 |
337 / 49 |
TC951 |
PMMA |
TL-2100 |
Rigid1 |
2.79 / 0.110 |
424 / 144.9 |
9.0 / 1.3 |
282 / 41 |
TC951 |
PMMA |
TL-2100 |
Ultra1 |
2.92 / 0.115 |
468 / 159.9 |
10.3 / 1.5 |
302 / 44 |
TC951 |
PMMA |
TL-6000-2L |
3x1 twill weave2 |
2.20 / 0.087 |
365 / 124.7 |
17.2 / 2.5 |
376 / 55 |
TC951 |
PMMA |
TL-6000-MOD1 |
3x1 twill weave2 |
2.92 / 0.115 |
1600 / 546.7 |
29.0 / 4.2 |
329 / 48 |
TC951 |
PMMA |
TL-6000-3L |
3x1 twill weave2 |
2.95 / 0.116 |
1434 / 490.0 |
28.6 / 4.1 |
335 / 49 |
TC951 |
PMMA |
TL-6000-4L |
3x1 twill weave2 |
3.43 / 0.135 |
2487 / 849.8 |
28.3 / 4.1 |
454 / 66 |
RTL panels are available with 0.178mm films on the exterior, except for TC951 (TL-6000-MOD1).
1 Toray Cetex® TC951 (TL-2100) often comes in bags that are resistant to moisture and in dried pre-cut rectangular plates with a complete radius on one end to allow improved forming of heel cups, as well as to facilitate distribution to podiatry labs.
It is also supplied as 1220 x 910mm panels. Its custom-designed weave allows extra support, stability, and bio-mechanical rectification of the foot in the medial orthotic and lateral direction.
2Cut to customer specifications from 910 x 1220mm sheets, Toray Cetex® TC951 (TL-6000) woven carbon fiber laminates have high mechanical properties. Some application examples are lower limb orthoses like ankle and knee bracing.
Table 3. Toray Cetex® TC951 (TL-2100) dimensions.
Size |
Toray Cetex® TC951 (TL-2100) dimensions |
|
1 |
76.2 x 177.8 mm |
3.0 x 7.0 inches |
Sizes 1 and 3 are not available in the Ultra Strength grade |
3 |
88.9 x 190.5 mm |
3.5 x 7.5 inches |
4 |
101.6 x 203.2 mm |
4.0 x 8.0 inches |
Additional sheet sizes are available on a factory special order basis only |
5 |
101.6 x 215.9 mm |
4.0 x 8.5 inches |
6 |
127 x 228.6 mm |
5.0 x 9.0 inches |
Table 4. Engineering thermoplastics.
Toray Cetex® product |
Resin type |
Tg / Tm (for semicrystalline resins) |
Key product characteristics |
Application examples |
Product format |
UD tape |
Prepreg |
RTL |
TC1000 Design |
PEI |
217 °C (423 °F) |
High strength / stiffness
Heat resistant
Good chemical resistance |
Abdominal retractors, external fixators, surgical instruments |
|
Ο |
Ο |
TC1225 NEW |
PAEK |
147 °C (296 °F)
Tm 305 °C |
Low moisture absorption
Cost-effective |
X-ray, surgical target devices |
|
Ο |
Ο |
TC1200 |
PEEK |
143 °C (289 °F) Tm 343 °C |
Excellent strength / stiffness
Excellent solvent resistance |
X-ray, surgical target devices |
Ο |
Ο |
Ο |
The Material Edge
Toray Performance Composites specializes in delivering high performance, continuous fiber-reinforced thermoplastics for the medical sector. Mainly used for podiatric correction, the Toray CFRT® thermoplastic composites can be found under the feet of many patients. They are also utilized to provide high-performance braces in the orthopedic business.
The proprietary technology of Toray Advanced Composites offers a number of benefits when compared to other thermoplastic technologies available on the market. One primary benefit is the way the materials are developed, which results in better precision and consistency. It is possible to customize the Toray CFRT® thermoplastic materials to either boost or restrict the range of foot motion with resin mix, fiber replacement, and part design. The type of fiber, placement, and content can be considered to provide maximum mechanical properties in the required direction.
Toray CFRT® materials are similar to a continuous “bridge”, and offer customized strength from one component end to the other, thereby enabling designers to create an orthotic component that has different properties in the longitudinal and medial-lateral direction.
Sheet Manufacturing
By using vertically integrated manufacturing Toray Performance Composites ensures delivery of high-quality parts to clients on time. On-site processes comprise prepreg, resin formulation, and fabrication of laminates. Laminates make it possible to orient and consolidate various plies, and also enable fast thermoforming.
High Volume Component Manufacturing
Component parts are cut from the laminates in a fast and efficient manner, thanks to the latest waterjet technology and CAD/CAM programming. Also, material usage is improved and the costs of tooling are drastically reduced when compared to other cutting processes. The patterns of the waterjet-cut flat component are then produced quickly through low-cost tooling.
Thermoplastic Processing
Laminates that are completely consolidated are traditionally employed in secondary thermoforming operations to realize rapid part production. It is also possible to reform and recycle materials. Thermoplastic forming can be done quickly, allowing part fabrication at a reduced cost. Table 5 shows a comparison of materials and common composite fabrics, and table 6 shows the standard weave styles adopted for fabrics.
Table 5. Material comparisons and common composite fabrics.
Material vs. reinforcements |
Filament count |
Tensile strength |
Tensile modulus |
Density g/cc |
Steel |
N/A |
400 MPa / 58 ksi |
200 GPa / 29 Msi |
7.8 |
Aluminium |
N/A |
483 MPa / 70 ksi |
69 GPa / 10 Msi |
2.8 |
E-Glass3 |
N/A |
2,000 MPa / 290 ksi |
72 GPa / 10 Msi |
2.6 |
High Strength Carbon3 |
3k, 12k (also 18k, 24k, 48k) |
3,447 - 4,826 MPa / 500 - 700 ksi |
230 - 245 GPa / 33 - 36 Msi |
1.8 |
Intermediate Modulus Carbon |
6k, 12k |
~5,516 MPa / ~800 ksi |
275 - 304 GPa / 40 - 44 Msi |
1.9 |
High Modulus Carbon |
6k, 12k |
~3,965 MPa / ~575 ksi |
>340 GPa / >49 Msi |
1.8 |
Table 6. Standard weave styles for fabrics.
Table of standard weave styles for fabrics |
Areal weight (gsm / oz/yd2) |
Description |
E-Glass |
Plain Weave |
200 / 5.90 |
Lowest cost option |
Carbon |
Plain Weave 3k |
193 / 5.69 |
Good fabric stability, but less drapable |
2x2 twill 3k
2x2 twill 12k |
205 / 6.05
650 / 19.17 |
More drapability than PW, less stable |
4x4 twill 3k |
283 / 8.35 |
Flatter weave style than 2x2 twill, improved finish |
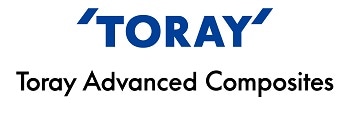
This information has been sourced, reviewed and adapted from materials provided by Toray Advanced Composites.
For more information on this source, please visit Toray Advanced Composites.