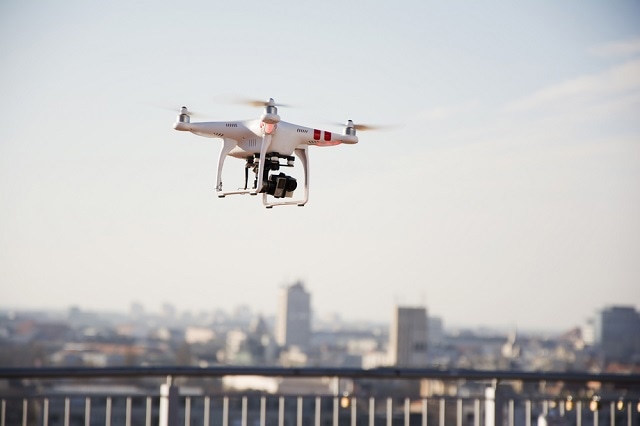
Image Credits: Newnow/shutterstock.com
Since the early beginnings of aviation, one of the projects of engineers have been working on is the development of Unmanned Aerial Vehicles (UAVs) to carry out military operations without the risk of human loss.
From Military to Civilian Use
One of the first uses of these machines was during the first Italian War of Independence in 1849, when the Austrian Army used unmanned balloons armed with bombs controlled by time fuses.
Although modern armies around the world have a vast range of military applications for these UAVs, ranging from intelligence to operations in conflict zones, 166 years after the bombardment of Venice ‘drones’ have migrated from military to civilian use.
Currently these systems are used by governments, private companies and individuals around the world for surveillance and law enforcement, to improve logistics and even to take breath taking pictures or videos.
Reducing the Weight of UAVs
The development of technologies, such as heavier-than-air aircraft, radio control and video have help us construct iconic aircraft such as the MQ-1 Predator or the DJI Phantom drone and have increased the public interest in UAVs. Currently drones have an increasingly important role in the future of aviation, especially in military applications.
However, as drones tend to be smaller than conventional aircraft and with a limited fuel capacity, their flight times tend to be significant lower than those of their manned counterparts. The issue becomes even greater when considering the payload of the vehicle, which can range from a set of hellfire missiles to a small camera for civilian use.
In order to improve this, a reduction of weight in the aircraft is paramount and the use of conventional aerospace materials such as Aluminum 6061-T6 might not be a feasible design option in the construction of UAVs. As a result, composite materials take a central role in the design and manufacture of drones.
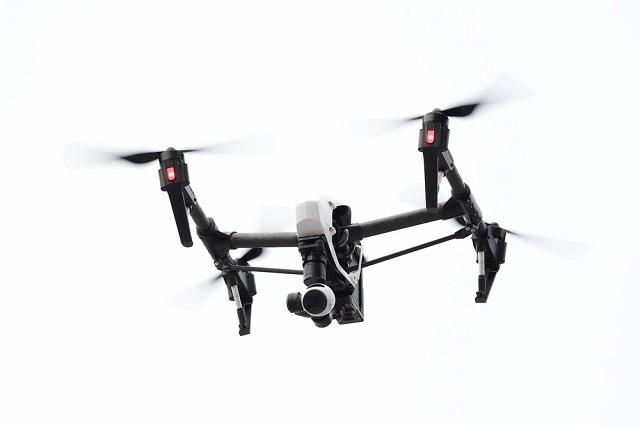
Image Credits: fluke samed/shutterstock.com
Composite Materials
A composites are materials made of two (a matrix or binder and a reinforcer) or more constituents with different physical or chemical properties. When these materials are combined, the new material has different characteristics from the individual components.
Usually the load is carried out by the fiber (from 70-90% of the load) and the rigidity and shape is provided by the matrix, which transfers the load to the fibers and stops or slows the propagation of cracks by isolating the fibers so that individual elements can act separately.
However, one of the most import characteristics to take into consideration when working with composites is that their mechanical properties, such as strength, usually depend upon the direction of the applied load. These materials have been used for thousands of years in the form of concrete and mud bricks, as well as wood and bones being natural composites.
The History of Composites in the Aerospace Industry
Composite materials are not a stranger to the aerospace industry and as early as the 1940s, glass fiber reinforced polymers (GFRP) began to find their way into the maritime industry. In 1944 the first aircraft with composites in its fuselage was flown in the US, an experimentally modified Vultee BT-15.
In the early 1960, composites were used in the form of ‘pre-pegs’, which consist of a series of fibre-reinforced plastics (FRP) pre-impregnated with an epoxy resin. Examples can be seen in the wings and forward fuselage of the AV-8B Harrier and the tail of the A-320, as well as other military aircraft such as the Eurofighter 2000.
Recently, Airbus increased its use of composites from 25% in the iconic A380 to 53% in the new A350 XWB. Boeing did the same: 12% of the structure of the 777 is made of composites and now their newest aircraft, the 787, is comprised in a 50% of composites. This produced a reduction in weight of 20% in the 787 and reduced scheduled and non-routine maintenance due to a reduced risk of corrosion and fatigue.
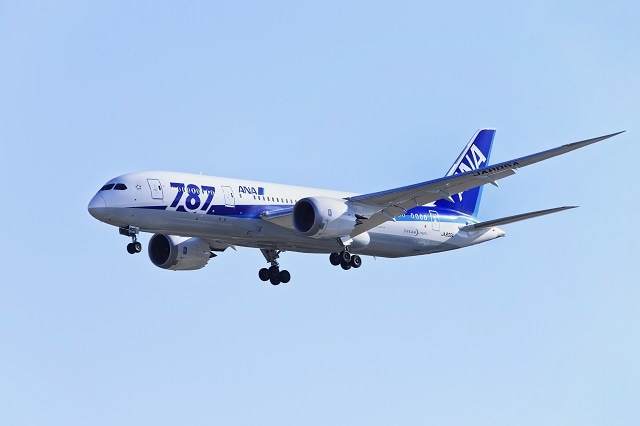
Image Credits: TonyV3112/shutterstock.com
Designing UVAs Using Composite Materials
This use of composites is reflected in the UAV industry. In 2009, a survey of 200 models by composite world found that all of the models have composites components and a number of cases reported the use of carbon fiber for the construction of airframes.
However, the increased demand for payload capacity and drone performance made the industry switch to another composite for the construction of the drone structure: carbon fiber-reinforced polymers (CFRP) which is now the primary material used in the construction of the UAV airframes.
In general, CFRP composites use thermosetting resin, which cures when heated, in combination with carbon fiber as the primary structural component. This makes the material lighter than GFRP composites as well as stronger, even when compared to metals.
For example, a structure made of steel will weight approximately 5 times more than a structure of the same strength made from CFRP. However, their high cost (5 to 25 times more expensive than glass fiber) has inhibited the use of this material in the industry. In addition, the material is electrically conductive which make it unsuitable for certain applications.
Kevlar/epoxy composites have been used in propeller construction, as it is lighter than CFRP. Considering that several designs of UAVs consist of 4 or more propellers, the advantage of using this material for such applications is considerable. The reduced inertia of the propeller, which in turn reduces the vibration, helps to make the UAV more stable during flight.
Drones Sacrificed for Spectacular Volcano Video | National Geographic
Drones Sacrificed for Spectacular Volcano Video - National Geographic/YouTube.com
The Future of UAV Design
According to composite world, in 2007 and 2008, 231 and 247 metric tons of composites were produced to support UAVs and the market is expected to produce 738 metric tons of airframe structure by the year 2018.
As the market share of drones increases in civil and military applications, the demand for more maneuverable, pay-load effective UAVs is going to increase with composite materials playing a vital role in the development of these new aircraft.
The use of additive manufacturing techniques such as Fused Deposition Modeling (FDM) and Laser Sintering (LS) in conjunction with composite materials is going to permit the development of more effective drones for security and military purposes.
Sources and Further Reading
Disclaimer: The views expressed here are those of the author expressed in their private capacity and do not necessarily represent the views of AZoM.com Limited T/A AZoNetwork the owner and operator of this website. This disclaimer forms part of the Terms and conditions of use of this website.