Distributed dielectric cure monitoring, or D-DEA for short, is a novel idea for applying dielectric analysis (DEA) in the manufacturing field.
Rather than using a single costly base instrument and several long extension cables, D-DEA uses multiple low-cost instruments connected along a single RS-485 communications line, as illustrated in Figure 1.
.jpg)
Figure 1. Distributed DEA compared to conventional DEA (wind turbine blade manufacture). Image Credit: Lambient Technologies.
For the first time, D-DEA enables the use of DEA to monitor several locations in very large structures, such as composite beams and wind turbine blades. D-DEA also prevents the tangle of extension cables used for monitoring parts that require multiple sensors such as spacecraft and aircraft components.
In contrast to traditional DEA instruments, D-DEA offers the following features:
- It is less costly
- Utilizes short sensor cables that maintain signals to D-DEA units
- Avoids the use of long sensor cables that diminish signals to a base instrument
- Enables up to 256 DEA channels to operate at the same time
- Combines DEA with a standard RS-485 process control network
- Allows process control and DEA monitoring of huge structures
- Expands the distance of DEA channels to 4000 ft (1890 m), which is the RS-485 distance limit
Dielectric cure monitoring involves making use of the same kinds of measurements and sensors for research, manufacturing, and quality control applications. DEA corresponds with laboratory tests like dynamic mechanical analysis (DMA) or differential scanning calorimetry (DSC).
Therefore, DEA can serve as the “go between” that brings data from the research laboratory to the manufacturing floor, and then from there to the manager who is responsible for product quality.
Distributed Dielectric Cure Monitoring with the LT-439
The LT-439 Dielectric Channel shown in Figure 2 is a compact, low-cost instrument developed for thermoset cure monitoring in research and development, manufacturing, and quality control or quality assurance.
.jpg)
Figure 2. LT-439 Dielectric Channel for Distributed DEA. Image Credit: Lambient Technologies.
When the LT-439 Dielectric Channel is used with either reusable or disposable conductivity/dielectric sensors, just like those illustrated in Figure 3, it allows D-DEA in all processing environments.
.jpg)
Figure 3. Disposable (left) and reusable (right) dielectric sensors. Image Credit: Lambient Technologies.
Measurements from the LT-439 Dielectric Channel can be interfaced with a control network via its optional RS-485 serial port or standard RS-232 serial port. Each LT-439 Dielectric Channel supports one thermocouple and one dielectric sensor.
Up to 256 separate dielectric channels can be linked to a single RS-485 line. This cost-effective flexibility avoids the need for complex cabling and enables concurrent, multi-channel monitoring of the state of cure at any point in a large part.
The typical LT-439 Dielectric Channel has excitation frequencies of 10 Hz, 100 Hz, 1 kHz, and 10 kHz.
A wider frequency option expands the range from 1 Hz to 10 kHz, with added frequencies for every 10 years.
A Convergence of Cure Monitoring Technologies
For highly crucial parts like spacecraft or aircraft components and composite wind turbine blades, each manufacturing step is documented—to record that the component is produced according to specification as well as for analysis in the event of failure.
At present, several manufacturers quantify only temperatures as a highly inaccurate and indirect way to deduce the progress of cure. However, DEA can directly indicate the state of cure. Dielectric cure monitoring is useful for documentation as no other method can view cure state in manufacturing and in real time.
The subsequent advance—DEA-based closed-loop control of massive composite structures—is about to become a reality. Two crucial technologies of a large-scale, closed-loop control heating system had existed for many years. These include dielectric cure monitoring that was marketed in the 1980s, and closed-loop molding control with dielectric cure monitoring that was demonstrated in 1992.1
The third critical technology was recently developed by Spirit AeroSystems of Wichita, Kansas. It was a smart, multi-zone heated tool and a substitute for an autoclave.2 The tool enables total control of the curing process with real-time monitoring as well as feedback, modifying cure time for each segment of a part—based on its thermal needs and geometry—and bringing down production costs, reducing cycle times, and minimizing the use of energy.
Although the tool from Spirit AeroSystems utilizes temperature for control information, it is just a small step to incorporate dielectric measurements for feedback about the state of the material.
The convergence of all these technologies occurs at a time when the development of an increasing number of wind turbine blades is essential for the rapid growth of the renewable energy sector. The wind turbine blades are usually more than 50 m long and are made in a mold. The blade’s thickness, the thermal environment, and the exotherm differ along its length.
Therefore, broadly spaced locations cure at different rates. Trial and error methods should be used by manufacturers to identify the maximum demold time. If a blade is removed too quickly, it can become damaged due to inadequate stiffness. If it is removed later than necessary, it would lead to a reduced throughput.
.jpg)
a. Dielectric cure monitoring (ca. 1980). Image Credit: Lambient Technologies.
.jpg)
b. DEA closed-loop feedback control (1992).2 Image Credit: Lambient Technologies.
.jpg)
c. Intelligent control of multi-zone heating (2018).3 Image Credit: Lambient Technologies.
Figure 4. Technologies for closed-loop control in the production of large structures. Image Credit: Lambient Technologies.
.jpg)
Figure 5. Distributed DEA for closed-loop process control (wind turbine blade manufacture). Image Credit: Lambient Technologies.
When dielectric sensors are installed in the mold at critical locations—for example, every 5 m along its length—they can determine when cure along the whole part has reached a preferred point. It is only at that time the wind turbine blade is removed from its mold.
By using distributed DEA instruments and independent heaters, as shown in Figure 5, dielectric measurements would enable a closed-loop control system to adjust the heating. This way, the entire structure cures at an even rate for optimum throughput. As an advantage, profitability increases if a factory reduces scrap by one blade a week, or ships even as little as one more blade a week.
References
1. Day, D.R. and Lee, H.L., “Analysis and Control of SMC Part to Part Variations,” Session 13-C of Proceedings of the 17th Annual Conference, Composites Institute, the Society of the Plastics Industry, Inc., Feb 3-6, 1992.
2. Spirit AeroSystems, “Spirit AeroSystems Develops New Composites Manufacturing Technology,” Press release, Dec 14, 2017. https://www.spiritaero.com/pages/article/spirit-develops-new-composite-manufacturing-technology
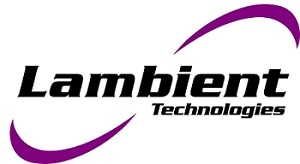
This information has been sourced, reviewed and adapted from materials provided by Lambient Technologies.
For more information on this source, please visit Lambient Technologies.