Duplex steels have a two-phase microstructure made up of austenite and ferrite. They also have better toughness than ferritic stainless alloys, and double the strength of both austenitic and ferritic stainless sheets of steel. Their corrosion resistance behavior is similar to that of common austenitic stainless grades.
Because of the lower alloying element requirements for duplex steels, they are often lower in cost than traditional stainless alloys and because of the higher strength, thinner sections of duplex steel may be used, reducing both cost and weight. However, duplex steels are prone to the precipitation of intermetallic phases because of their higher molybdenum and chromium content. More specifically, the sigma phase is a hard phase and has a negative impact on corrosion resistance and toughness. If an excess of the sigma phase is present, the alloy properties are reduced below values which are practical for use.
Analysis
Pegasus is the ideal tool to be paired with EDS-EBSD for the characterization of the duplex steel’s microstructure and for measuring phase fractions present to establish if a particular alloy and heat treatment method produce a useful duplex steel product.
In the analysis described in this application note, duplex steel alloy samples were subjected to heat treatments at one of three temperatures (800°C, 900°C, and 1000°C) for 2 hours then prepared for EBSD analysis. Pegasus was used to collect, manage, and analyze data from the three samples.
Pegasus Project
A Pegasus project was created for data collection. Austenite (face-centered cubic), Ferrite (body-centered cubic), and sigma (tetragonal) structures were chosen. Figure 1 shows the representative patterns. The APEXTM Software was used to image the area of interest, gathering the collective EDS-EBSD dataset and reviewing the data.
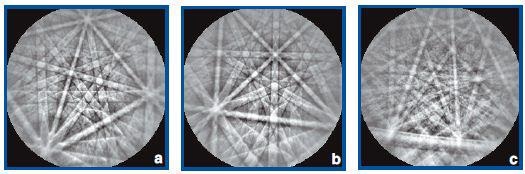
Figure 1. EBSD patterns from the a) ferrite, b) austenite, and c) sigma phases
While gathering a simultaneous APEX™ map, a key smart feature is the EBSD camera’s auto-optimization, which is content-sensitive. While acquiring point analysis data, EBSD patterns are improved for low noise and high resolution, and EDS spectra are collected for quantitative analysis.
The EDS count rate is used to establish a dwell time, which generates a statistically significant number of EDS counts per pixel during mapping data collection. The EBSD camera exposure is then automatically set to this dwell time by the software to improve the quality of the collection pattern. For EBSD-only mode, optimization modes are also available.
Here, a greyscale image quality (IQ) map is integrated with a colored phase map. However, there are other map versions available. For instance, Figure 2 illustrates a blended EDS map indicating the various processing temperatures, providing some indication of phase distribution.

Figure 2. Blended EDS maps for samples heat-treated at a) 800°C, b) 900°C, and c)1000°C where molybdenum is colored red, chromium is colored blue, and iron is colored green.
These maps can be compared to the EBSD structural phase maps depicted in Figure 3. In these maps, the colored phase data is yet again integrated with the greyscale EBSD image quality contrast to show the grain structure inside each phase.
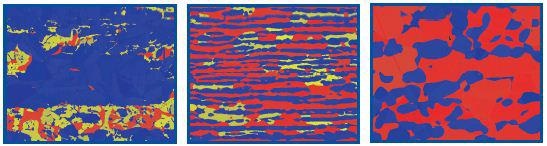
Figure 3. Colored phase maps combined with greyscale EBSD image quality for samples heat-treated at a) 800°C, b) 900°C, and c)1000°C where ferrite is colored blue, austenite is colored red, and sigma is colored yellow.
Results
The quantitative microstructural results are displayed in Table 1. When the annealing temperature was increased, the percentage of the sigma phase was reduced. This is in coincidence with an increase in the average size of the grain. It is known that when grain size increases, strength decreases, and therefore, the two competing mechanisms need to be controlled. In this particular case, the size of the grain is required to be small enough to offer strength high enough for a specific application, and at the same time, the sigma fraction has to remain low enough to offer sufficient corrosion resistance and toughness.
Table 1. Microstructural results vs. annealing temperature
Annealing Temperature |
% Sigma |
% Ferrite |
% Austenite |
Ave Grain Size (µm) |
800°C |
14 |
6 |
80 |
1.37 |
900°C |
9 |
38 |
53 |
1.85 |
1000°C |
0 |
57 |
43 |
4.82 |
Conclusion
Pegasus yields the characterization data required to understand and improve the heat-treating process so as to provide material appropriate for this application.
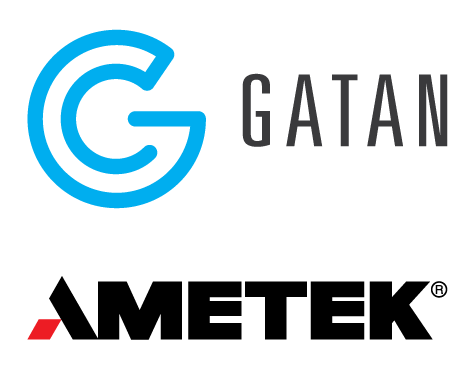
This information has been sourced, reviewed and adapted from materials provided by Gatan Inc.
For more information on this source, please visit Gatan Inc.