Toray Advanced Composites provides advanced thermoplastic and thermoset materials for aerospace and industrial applications. The company supplies its thermoset-based advanced composite prepregs in fabric and unidirectional (UD) tape form.
It controls resin content and the degree of impregnation using both direct impregnation and film impregnation in order to address the processing and handling requirements specific to each customer. A range of proprietary resin systems including high-temperature cyanate esters, BMIs, and toughened epoxies and a variety of reinforcement materials such as aramid, glass, and carbon-based reinforcements are used by Toray Advanced Composites.
Motorsport
Toray Advanced Composites offers a myriad of composite material solutions to meet each specific application within the high-end motorsport and Formula 1 market (Figure 1). Since the company has made a continuous investment in product development, it has developed a comprehensive line of high-performance thermoset materials for a broad range of motorsport applications, such as chassis, suspension parts, gear box, crash structures, body parts, nose cone, side-impact protection, and a floor panel (Figure 2).
.jpg)
.jpg)
Figure 1. Toray Advanced Composites have a broad range of composite material solutions to suit a diverse range of applications within the Formula 1 and high-end motorsport market.
.jpg)
Figure 2. Motorsport product applications of Toray Advanced Composites materials.
Toray's Thermoset Composites
The composite material solutions offered by Toray Advanced Composites are lightweight, energy-absorbing materials with a high strength-to-weight ratio, superior stiffness, fracture toughness, good material handleability, outstanding cosmetic finish, and good impact resistance. They are also bondable to a honeycomb core. The motorsport industry uses the complete line of Toray Advanced Composites products, ranging from low temperature to high temperature curing prepregs. Low temperature curing epoxies are ideal products for use in wind tunnel testing and prototyping (Table 1).
Table 1. Low temperature curing prepregs.
Product name |
Resin type |
Tg |
Typical cure time/cure temp |
Description of properties |
Application examples |
Reinforcement type |
Fabric |
UD |
Toray E644 |
Epoxy |
124 °C
(255 °F) |
3.5 hours
at 70 °C (158 °F) |
Excellent surface finish |
Wind tunnel prototyping |
Ο |
|
Toray E650 |
Epoxy |
121 °C
(250 °F) |
3.5 hours
at 70 °C (158 °F) |
Medium tack level,
easier lamination |
Wind tunnel prototyping |
Ο |
|
Mid temperature curing epoxies are most suitable for structural components (Table 2). Cyanate esters exhibit high-temperature resistance and durability in extreme conditions. Toray also offers its thermoset materials with glass or carbon in woven or unidirectional reinforcements. Table 3 lists the high service temperature products offered by Toray.
Table 2. Mid temperature curing prepregs.
Product name |
Resin type |
Tg |
Typical cure time/cure temp |
Description of properties |
Application examples |
Reinforcement type |
Fabric |
UD |
Toray E760
NEW |
Epoxy |
204 °C
(399 °F) |
2 hours
at 180 °C (356 °F) |
High-temperature resistance
and high mechanical performance |
High temperature e.g. rear suspension |
Ο |
Ο |
Toray TC350-1 |
Epoxy |
191 °C
(376 °F) |
2 hours
at 177 °C (350 °F) |
High compression after impact |
High impact areas e.g. chassis |
Ο |
Ο |
Toray E750
NEW |
Epoxy |
148 °C
(298 °F) |
60 minutes
at 135 °C (275 °F) |
Variable temperature
cure, starting at 80 °C (176 °F) |
High impact areas, bodywork |
Ο |
Ο |
Toray E731
NEW |
Epoxy |
140 °C
(284 °F) |
60 minutes
at 125 °C (257 °F) |
High cosmetic clarity |
E.g. center console |
Ο |
Ο |
Toray E721-FR |
FR Epoxy |
120 °C
(248 °F) |
60 minutes
at 120 °C (248 °F) |
Fire retardant version of E720 |
Internal bodywork |
Ο |
Ο |
Toray E722 |
Epoxy |
120 °C
(248 °F) |
60 minutes
at 120 °C (248 °F) |
Excellent drapability
Greater rigidity |
Monolithic parts |
Ο |
Ο |
Toray E745
NEW |
Epoxy |
118 °C
(244 °F) |
60 minutes
at 135 °C (275 °F) |
High toughness and
impact properties |
Side-impact structures,
F1 nose cones |
Ο |
Ο |
Toray E720 |
Epoxy |
110 °C
(230 °F) |
60 minutes
at 120 °C (248 °F) |
Honeycomb bondable |
Ambient structural |
Ο |
Ο |
Full mechanical data is available please call us at Toray Advanced Composites (UK) to discuss your requirements.
Table 3. High service temperature.
Product name |
Resin type |
Tg |
Typical cure time/cure temp |
Description of properties |
Aplication examples |
Reinforcement type |
Fabric |
UD |
Toray C640 |
Cyanate ester |
335 °C (635 °F) |
10 hours at 80 °C (176 °F) followed by 300 °C (572 °F) postcure |
High-temperature resistance and variable temperature cure |
Brake ducts |
Ο |
|
Toray C740 |
Cyanate ester |
325 °C (617 °F) |
60 minutes at 135°C (275 °F) followed by 300 °C (572°F) postcure |
High-temperature resistance and longer out life for larger parts |
Pipework and ducting, exhaust area |
Ο |
|
Toray TC420 |
Cyanate ester |
321 °C (610 °F) |
3 hours at 177 °C (350 °F), followed by 260 °C (500 °F) post cure |
Excellent thermal stability, resistance to microcracking |
Gearbox |
Ο |
|
Toray RS-8HT |
BMI |
255 °C (545 °F) |
2 hours at 204 °C (400 °F), followed by post cure of 6 hours at 230 °C (450 °F) |
Thermal stability, moderate toughness with good moisture resistance, available in RTM resin form |
Rear structural components |
Ο |
|
Toray AmberTool® Composite Tooling Solutions
The Toray AmberTool® range of composite tooling solutions (Figure 3) has been used in the high-performance motorsport industry for more than two decades. The range includes the HX and TC series and is marketed worldwide by an established tooling expert team. The extensive range of tooling solutions offered by Toray provides customers with complete tool design options. The company is able to provide complete technical support thanks to its proven processing procedures, full tooling construction guidance, life-cycle maintenance control, and expertise in surface treatments, and advanced in-mold heating applications.
.jpg)
Figure 3. The Toray AmberTool® range of composite tooling solutions.
The Toray AmberTool® range of prepregs is listed in Table 4.
Table 4. The Toray AmberTool® prepregs.
Product
name |
Tg (DMTA)
following post-cure |
Min cure temp |
Tack life |
End-use temp |
Storage life |
Benefits |
HX42 |
Onset: 200 °C (392 °F)
Peak Tan δ: 220 °C (428 °F) |
50 °C (122 °F) |
5 days |
190 °C (374 °F) |
12 months |
Excellent surface finish at
high temperatures |
HX50 |
Onset: 190 °C (374 °F)
Peak Tan δ: 220 °C (428 °F) |
40 °C (104 °F) |
60 hours |
180 °C (356 °F) |
6 months |
Fast cure, excellent surface
finish |
HXR56
NEW |
Onset: 185 °C (365 °F)
Peak Tan δ: 209 °C (408 °F) |
40 °C (104 °F) |
50 hours |
180 °C (356 °F) |
6 months |
Two-layer product for rapid
lamination |
TC40* |
Onset: 213 °C (415 °F) |
182 °C (360 °F) |
14 days |
199 °C (390 °F) |
12 months |
Ultra-high use temp BMI |
*Toray AmberTool® TC40 country of shipment is North America
The complete service support provided by Toray facilitates a single supplier approach to address each and every composite tooling requirement. This ranges from material and master to technical support. With Toray product solutions, a high degree of precision and accuracy can be achieved for all machined and molded applications.
The master and surface coat package comprises a high-performance epoxy block, EC85 surface coating technology, and various combinations of specialist sealing and releases agents from Chem-Trend. Toray Advanced Composites (UK) serves as a distributor for Chem-Trend, supplying mold cleaners, release agents, and sealers. The company also provides full tooling delivery solutions, such as:
- Carbon and glass backing structures
- Machinable
- Fast delivery solutions for standard materials
Honeycomb and Core Materials
Toray supplies composite tooling materials that are compatible with superior quality epoxy tooling boards such as Rampf WB-0700. These materials are supplied with density matched adhesive and repair paste for no witness lines. Toray Advanced Composites (UK) owns the largest independent core processing facility in Europe. Flex-Core®, aluminum, and Nomex® honeycomb materials are supplied by the company. Tables 5 and 6 summarize the honeycomb core and syntactic core materials.
Table 5. Honeycomb core.
Product name |
Configurations |
Description |
Aluminium Honeycomb - Aerospace Grade |
3.1-1/8-07N-5052
4.5-1/8-10N-5052
5.2-1/4-25N-5052
8.1-1/8-20N-5052 |
4.5-1/8-10N-5056
6.1-1/8-15N-5056*
8.1-1/8-20N-5056* |
- High strength-to-weight properties at relatively low cost
- Structural aerospace-grade aluminum honeycomb available in 5052 and 5056 alloy
- Sheet size 1250 x 2500 mm except *1220 x 2440 mm
|
Nomex® Honeycomb - Aerospace Grade |
ANA-3.2-29 3.2mm 29kg/m3
ANA-3.2-48 3.2mm 48kg/m3
ANA-3.2-64 3.2mm 64kg/m3*
ANA-4.8-48(OX) 4.8mm 48kg/m3 |
- Nomex® paper sheets are coated and bonded together with a high modulus phenolic resin
- Fire-resistant and self-extinguishing
- High-temperature strength up to 180 °C (356 °F)
- Sheet size 1250 x 2500 mm except *1220x 2440 mm
|
Nomex® Honeycomb - Commercial Grade |
ANC-3.2-48 3.2mm 48kg/m3
ANC-4.8-32 4.8mm 32kg/m3
ANC-4.8-48 4.8mm 48kg/m3
ANC-4.8-48(OX) 4.8mm 48kg/m3 |
- Fire-resistant and self-extinguishing
- Good thermal and electrical insulating properties
- High strength-to-weight ratio and easily formable to shape
- Sheet size 1250 x 2500mm
|
Aluminium Flex-Core® |
5052/F80 - .0013N Density 4.3
5052/F80 - .0024N Density 8.0
5056/F80 - .0014N Density 4.3 |
- Made from either 5052 or 5056 aluminum alloy foil and is available in two cell sizes <
- Unique cell configurations that permit small radii of curvature without deformation of the cell walls or loss of mechanical properties
- For leading edges, flaps, nacelles, fairings, doors and access covers, and other parabolic, spherical and cylindrical shapes
|
Additional grades can be sourced on request, subject to minimum order quantities and extended lead times.
Flex-Core® is a registered trademark of Hexcel. Nomex® is a registered trademark of E.I du Pont de Nemours and Company.
Table 6. Syntactic core.
Product name |
Resin type |
Tg (onset) |
Cure temp |
Description |
Toray Amlite LT64 |
Epoxy |
130 °C (266 °F) |
50-80 °C (122-176 °F) |
- Low temperature curing, low density, non expanding
- Co-compatible with Toray E600 series
|
Toray Amlite SC8020A |
Epoxy |
106 °C (223 °F) |
80 °C (176 °F) |
- Low density, non expanding with flexible cure temperatures from 70-130 °C (158-266 °F)
|
Toray Amlite SC72A |
Epoxy |
106 °C (223 °F) |
120 °C (248 °F) |
- Mid temperature curing, non expanding, ideal for sandwich structure under 3 mm (0.11”)
- Excellent for edge close outs
|
Toray Amspand ES72A-2 |
Epoxy |
114 °C (237 °F) |
125 °C (257 °F) |
- Expanding epoxy resin film
- Varying density by tailoring cure pressure and / or volume
|
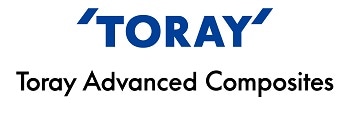
This information has been sourced, reviewed and adapted from materials provided by Toray Advanced Composites.
For more information on this source, please visit Toray Advanced Composites.