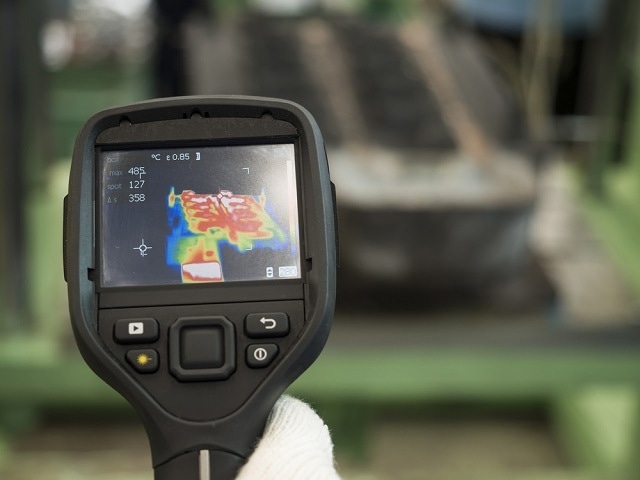
Image Credit: Aumm graphixphoto | Shutterstock.com
Thermal analysis is an important part of understanding and shaping a variety of plastics for a range of applications, including transportation or packaging. For example, polyethylene terephthalate is considered a low-weight and adaptable polymer to manufacture household items, including furniture and drink containers.
Applying heat to this type of polymer allows scientists to understand its characteristics, enabling them to discover how they should be manufactured and to improve their qualities.
Thermal Analysis Techniques
The most common thermal analysis techniques for polymers are: differential scanning calorimetry (DSC), thermogravimetric analysis (TGA), thermomechanical analysis (TMA), and dynamic mechanical analysis (DMA).
In DSC a sample is heated, cooled, or held at a constant temperature as heat flows to and from the sample. The reference material is measured as a function of temperature. The measurement is the amount of energy absorbed and released by the sample in milliwatts.
The sample is heated, cooled, or held isothermally in a defined atmosphere, and its mass is weighed in TGA.
In TMA a sample is measured as a function of temperature in terms of its abilities to deform or change as it is being subjected to a constant force, an increasing force, or a modulated force.
DMA requires the sample to be subjected to a periodically oscillating force, and its mechanical properties are assessed. Specifically, its force amplitude, displacement (deformation) amplitude, and phase shift are determined as a function of temperature or frequency.
Of these major thermal analysis techniques, DSC is seen as the most versatile in the evaluation of various aspects of materials whether the criteria is heat capacity, melting qualities including melting point, vaporization, crystallization, temperature stability, elasticity, glass transitioning qualities, or oxidative degradation.
Thermal Analysis in Practice
Polymer Solutions
Testing company Polymer Solutions conducted thermal analysis experiments to discover why a client’s polyacrylonitrile butadiene styrene (ABS) parts were breaking, and researchers used TGA analysis to both decompose and vaporize the parts to document their polymer and filler content.
Comparing normal and abnormal parts with the technique, researchers found that both sets had the required level of 30% glass filler, and therefore the filler was not the source of failure. Then, using optical microscopy the researchers discovered the filler for the good sample was half fiber and half powder whereas the filler for the bad sample was all powder, meaning the failing parts lacked the reinforcing glass fiber filler necessary for the plastic to be adequately strong.
University of Illinois
Researchers at the University of Illinois at Urbana-Champaign led by William King of the College of Engineering Bliss Professor in the Department of Mechanical Science and Engineering used AFM to conduct nanoscale thermal analysis on stiff materials like epoxies and filled composites, which was previously thought only possible on soft polymers.
They were able to measure temperature and frequency-dependent properties at the sub-100 nanometer scale, by passing a current around a self-heating AFM cantilever within a magnetic field to allow the tip-sample force to be modulated right near the tip of the AFM. The end result was the never-before ability to analyze polymers at the nanoscale. In one experiment, researchers were able to measure and map glass transitions and melting transitions on sub-100 nm polymer thin films.
Private company Anasys Instruments, Inc. worked with the University of Illinois as a co-investigator on its nanoscale thermal analysis in 2012, and now has incorporated the findings into techniques it continues to refine to, like other companies, offer it as another service to clients.
National Institute of Standards and Technology
Complementary research to the nanoscale thermal analysis has been going on for some time. By 2007 the National Institute of Standards and Technology (NIST) had already developed an imaging system that quickly maps the mechanical properties of mixed nanoscale materials, such as polymer composites or thin-film structures.
Its nanomechanical mapper uses custom software and electronics to process data acquired by a conventional AFM so that within minutes the AFM’s topographical maps of surfaces are turned into two-dimensional representations of mechanical properties near the surface.
Scientists were then able to see variations in elasticity, adhesion or friction. In one experiment, the NIST system revealed that glass fibers were stiffer than a surrounding polymer matrix but sometimes softer at their cores.
References and Further Reading
Injection Molded Components
Magnetic Actuation Enables Nanoscale Thermal Analysis
Solving Mysteries of Conductivity in Polymers
Thermal Analysis of Polymers and Plastics
Thermal Analysis of Polymers
NIST Imaging System Maps Nanomechanical Properties
Disclaimer: The views expressed here are those of the author expressed in their private capacity and do not necessarily represent the views of AZoM.com Limited T/A AZoNetwork the owner and operator of this website. This disclaimer forms part of the Terms and conditions of use of this website.