Decarburization refers to a loss of carbon from a metal surface, particularly cast irons and steels, and occurs due to heating in a medium, which in turn reacts with the carbon atoms. Case hardening is defined as a process where the top layer of iron-based alloys is considerably harder than that of the interior. However, during decarburization the opposite takes place.
The decarburized steel surface is relatively softer than the core, leading to low fatigue life and poor wear-resistance. It is often necessary to measure the level of decarburization. Figure 1 shows fastener threads sowing decarburization.
.jpg)
Figure 1. Fastener threads exhibiting decarburization (100X).
Sampling and Specimen Preparation
The following sampling and specimen preparation were used.
Sample identification: Heat treated steel fastener
Sectioning: |
|
Saw |
MSX255M2 |
Blade |
12” x 0.062”, Rubber Bonded, Aluminum Oxide (811-089-010) |
Mounting: |
|
Press |
PR-36 with 1.5" Mold Assembly |
Media |
Black Epoxy (811-645) |
Grinding/Polishing
GRINDING
SS-1000 Grinder/Polisher
(8" Wheel) |
Time (Minutes: Seconds) |
Head Direction |
Head Pressure (Pounds) |
Wheel Direction |
Wheel Speed (FPM) |
Platinum #1
812-341 / Water |
2:00 |
CW |
40 |
CCW |
300 |
PRE-POLISHING
FAS Magnetic System
8" (812-381) |
Time (Minutes: Seconds) |
Head Direction |
Head Pressure (Pounds) |
Wheel Direction |
Wheel Speed (FPM) |
Silver Disk, 6 µm Cameo Suspension, Microid Extender, 812-344, 812-356, 811-003 |
2:00 |
CW |
40 |
CCW |
200 |
POLISHING |
Time (Minutes:Seconds) |
Head Direction |
Head Pressure (Pounds) |
Wheel Direction |
Wheel Speed (FPM) |
3 µm Diamond Paste, Ultra Silk, Microid Extender, 810-872, 812-437, 811-003 |
3:00 |
CW |
40 |
CCW |
200 |
1 µ Diamond Paste, Red Felt, Microid Extender, 810-870, 810-647, 811-003 |
1:00 |
CW |
35 |
CCW |
200 |
Etching: 2% Nital solution approximately 15s
Hardness Tester Calibration Samples
A certified microindentation hardness standard from NIST, LECO or another suitable source is used to verify the tester. The same load and indenter type, like sample analysis, should be used to certify the hardness standard, which should have a hardness value near to that of the material under analysis.
Application Parameters – Single "Vector"/Pattern
In order to locate a suitable hardness test location, the AMH55 software can be used to automatically perform an auto-trace. A Panoptic image is produced, similar to that shown in Figure 2. A vector containing 10 equally spaced Knoop indentations is produced and pulled to the tip of one of the threads, as shown in Figure 3.
.jpg)
Figure 2. Panoptic view
.jpg)
Figure 3. A vector in place
Indentations are made and automatically determined, producing the following data:
.jpg)
Figure 4. Analysis of decarburized fastener
At the surface (the lowest carbon content) the hardness is lowest and slowly increases toward the core. In certain cases, a hardness limit is measured depending on the hardness values of a core and surface, and is applied to define the decarburized layer depth (Figure 4).
In this example, the limitation of the decarburized layer is referred to the point where the hardness increases to 75% of the total core value. 197 HK was the core hardness and 137 HK was the surface hardness; 45 is 75% of the difference (60). The limit is measured as 182 HK (137 + 45), providing a decarburized layer of about 110 µm (0.11 mm). A custom report can be generated by exporting the data obtained from the AMH55 to a spreadsheet (Figure 5).
.jpg)
Figure 5. Hardness profile
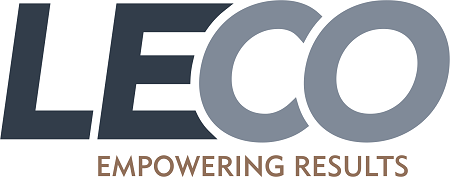
This information has been sourced, reviewed and adapted from materials provided by LECO Corporation.
For more information on this source, please visit LECO Corporation.