Around the world weather balloons are launched daily to collect atmospheric data such as humidity, temperature, pressure, and wind speed and direction. With approximately 800 different locations in some of the most remote areas of the world, meteorological organizations conducting upper air observation rely on gases such as hydrogen and helium to elevate weather balloons so they can capture data.
Recently, there has been much debate regarding the type of gas that should be used and what to do so that the gas is readily available when required.
The Hydrogen/Helium Debate
In the weather balloon market many organizations, from meteorological users, to civil government, to the military, often resort to using helium due to concerns regarding hydrogen's safety.
The introduction of Proton Exchange Membrane (PEM) technology has brought changes in the generation of hydrogen. This technology enables pure hydrogen to be produced on-site in a reliable, safe and cost-effective manner using only electricity and water.
The Proton Exchange Membrane electrolyzers that are sold all over the world are used in a wide range of applications outside the meteorological field, including gas chromatography, cooling of power plant turbine generator windings, electronics manufacturing, and heat treating. These electrolyzers have demonstrated high reliability in a variety of duty cycles and environments.
Several meteorological agencies, such as the US National Weather Service and Environment Canada, have been using helium for the past 40 years, and are now allowing some sites to fill their balloons with hydrogen. The two main reasons for this switch are availability and price.
As many sounding balloon sites are in remote locations, the delivery of gas to these areas is a difficult process. The delivery of either helium or hydrogen in high-pressure cylinders also has certain risks. The deployment of on-site hydrogen generation systems will allow the observations in remote locations to be made without the logistical difficulties and risks associated with the transportation and storage of these gases in high-pressure cylinders.
The availability of helium is limited but it is possible to produce hydrogen using only electricity and water anywhere and at any time. An unreliable supply of helium ties the hands of the organization in the balloon market, and also limits their ability to capture data.
Meteorological agencies, with their limited budgets, are not prepared to risk upper air data collection on an unreliable and expensive supply of helium.
Producing Safe, Affordable Hydrogen
These very same organizations recognize value in the price difference between helium and hydrogen. The limited availability of helium has increased the price of sourcing and makes it more difficult to obtain, two of the issues solved with on-site hydrogen generation.
Compared with helium, on-site hydrogen generation eliminates problems such as cost, delivery, and scarcity. Various cost-effective ways are available to generate hydrogen, including:
- On-site production via a chemical reaction like steam reforming - a process that generates hydrogen from natural gas or other hydrocarbon fossil fuels
- Via electrolysis with a solid polymer electrolyte (PEM)
- On-site production via electrolysis with a liquid potassium hydroxide (KOH) electrolyte
- Using calcium hydroxide cartridges
Solid is Better
On-site hydrogen generation from fossil fuels is unaffordable for meteorological weather balloons because of the complexity, fuel costs, and risks associated with the process.
Two main options are available for the generation systems that produce hydrogen gas from water and electricity: KOH electrolysis and PEM electrolysis. A solid polymer electrolyte is used in the PEM electrolysis.
Many differences exist between the PEM and KOH electrolysis, with the KOH systems posing more drawbacks and safety risks. For instance, KOH systems use hazardous caustic chemicals such as potassium hydroxide. Additionally, KOH systems generally use a balanced pressure design, which leads to an explosion/fire risk when oxygen and hydrogen gases mix.
Conversely, PEM systems do not require hazardous chemicals and they also use a differential pressure design, which eradicates the risks associated with the mixing of the two gases.
Additionally, PEM systems do not adversely impact the safety and health of the environment or the personnel as there is no need to handle or dispose of hazardous electrolyte chemicals.
PEM systems use a solid electrolyte to generate hydrogen from pure water and electricity. The latter can be generated by solar panels, making on-site hydrogen generation independent of local power grids and their limitations, which is a vital secondary benefit.
.jpg)
Ease of Maintenance
The maintenance needs also differ for KOH and PEM hydrogen generation systems. For instance, KOH system components corrode with every system start up and shut down. In addition, KOH systems generally require 40+ hours of maintenance every year. Conversely, PEM systems only require around four hours.
A much smaller operating footprint is required by the PEM systems. The components of these systems are self-contained in smaller cabinets than commercially available KOH systems. Separate explosion-proof rooms are not required by the PEM systems. Hydrogen generation systems with smaller operating footprints are attractive for meteorological teams working with limited budgets in remote areas.
As an increased number of upper air sites turn to on-site hydrogen generators, it is important to take into account the most practical option for production of the gas: Proton Exchange Membrane systems.
.jpg)
Nel Hydrogen’s S Series Hydrogen Generation System
.jpg)
Nel Hydrogen's S Series Hydrogen Generation System
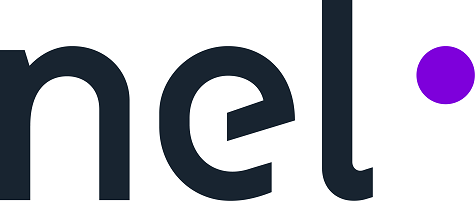
This information has been sourced, reviewed and adapted from materials provided by Nel Hydrogen.
For more information on this source, please visit Nel Hydrogen.