Shayne Harrel, Application Development Scientist specializing in XRF for Olympus, talks to AZoM about the FOX-IQ factory on-line XRF spectrometer and the analytical power it offers manufacturers for precise quality control.
What is the FOX-IQ designed to do?
The Olympus FOX-IQ is a Factory On-line XRF spectrometer. Its purpose is to make quantitative or qualitative compositional measurements, usually for quality control. It uses x-ray fluorescence spectroscopy (XRF), a powerful and proven analytical technology capable of determining material chemistry that is widely used in the alloy world. The analyzer comes equipped with a miniaturized x-ray tube, filter wheel and silicon drift detector (SDD) for optimal analytical performance. Upward of 100 systems have been installed globally. By introducing the FOX-IQ into a manufacturing process, the customers’ quality management and productivity objectives under Industry 4.0 can be advanced.
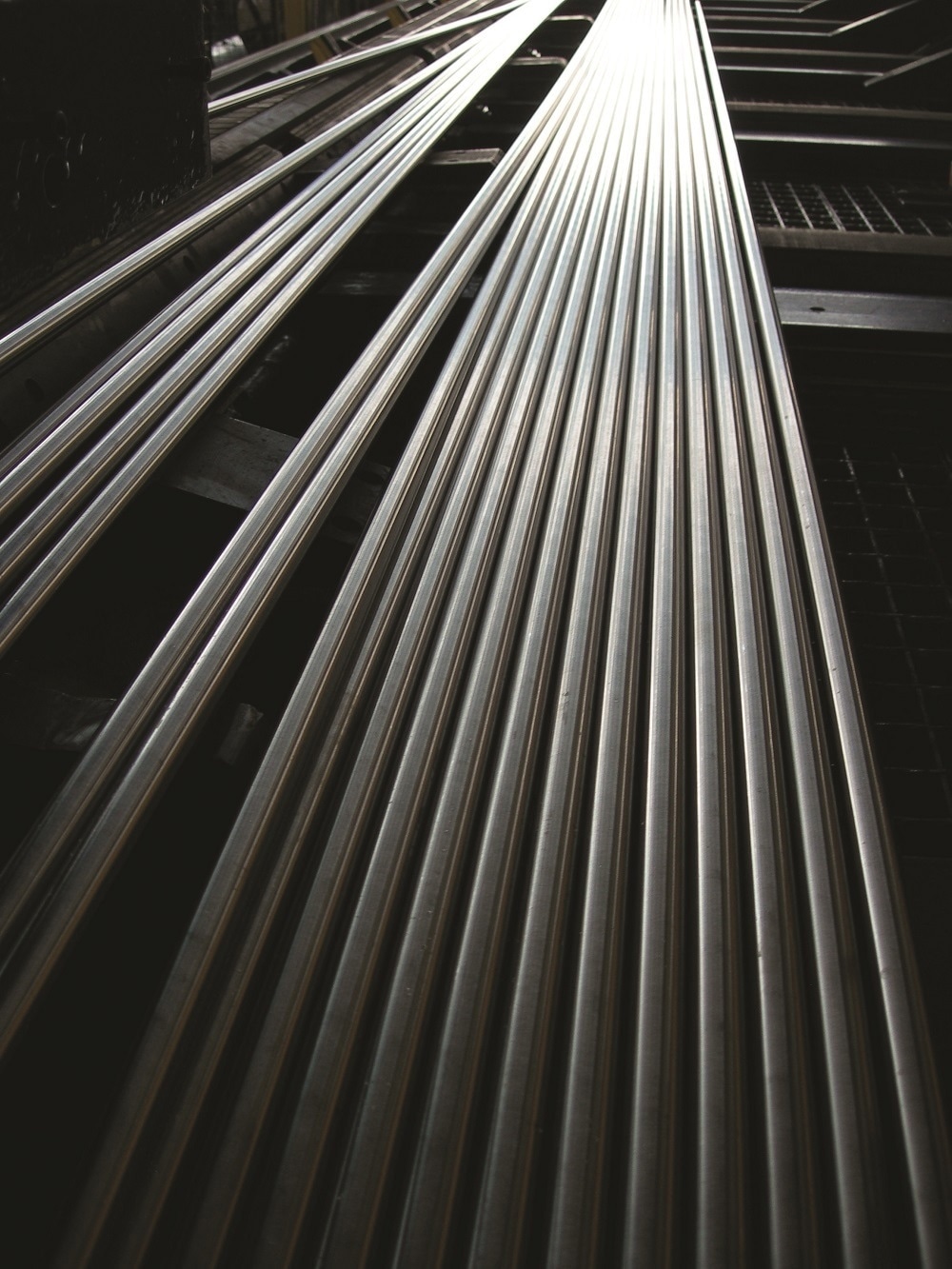
What capabilities does the FOX-IQ have compared to your handheld devices?
The FOX-IQ can do nearly anything the Olympus handheld analyzer can do. It has the ability to identify and verify alloy grades and material chemistry quickly and nondestructively. These results can be integrated in to a pass/fail criteria that can be automatically linked to a QC/QA reporting system.
How easy is it to install in applications that require on-line elemental analysis?
It easily integrates into any new or existing PLC-controlled processes. Our factory field service engineers provide guidance supporting the planning, preparation, physical installation and process control integration. We also provide a two-day on-site commissioning, training and start up session. Each system has a controller, a FOX-IQ analyzer (probe head), and a PC for setup, manual operation and data storage and exporting. The analyzer can be controlled via the Factory PC software, a customer supplied PLC, or a COM-API (Application Program Interface).
Do you have any case studies you’re particularly proud of?
I am especially proud of some custom applications that we were able to achieve. The FOX-IQ comes equipped with a factory alloy calibration that accommodates the needs of most customers. However, there are certain instances where we have to fine tune or develop a completely new calibration to satisfy a customer’s needs. This involves us working very closely with the customer, testing their samples and coming up with a solution that meets their analytical goals and objectives.
What elements can be measured with the FOX-IQ system?
Elements that can be analyzed with the FOX-IQ can be as heavy as Pu or as light as Ti. In special applications, such as determining the presence or absence of an analyte on a surface, lighter elements such as P have been measured. While LODs below 0.5 % are common, elements lighter than Ti (Z < 22) are less favorable to test. The limits of detection (LODs) depend on serval factors such as the material to be analyzed and other elements present (matrix effect), and test duration. A big factor to successful material analysis is sample presentation. Automated, precise sample movement to and from the FOX-IQ analysis window is required.
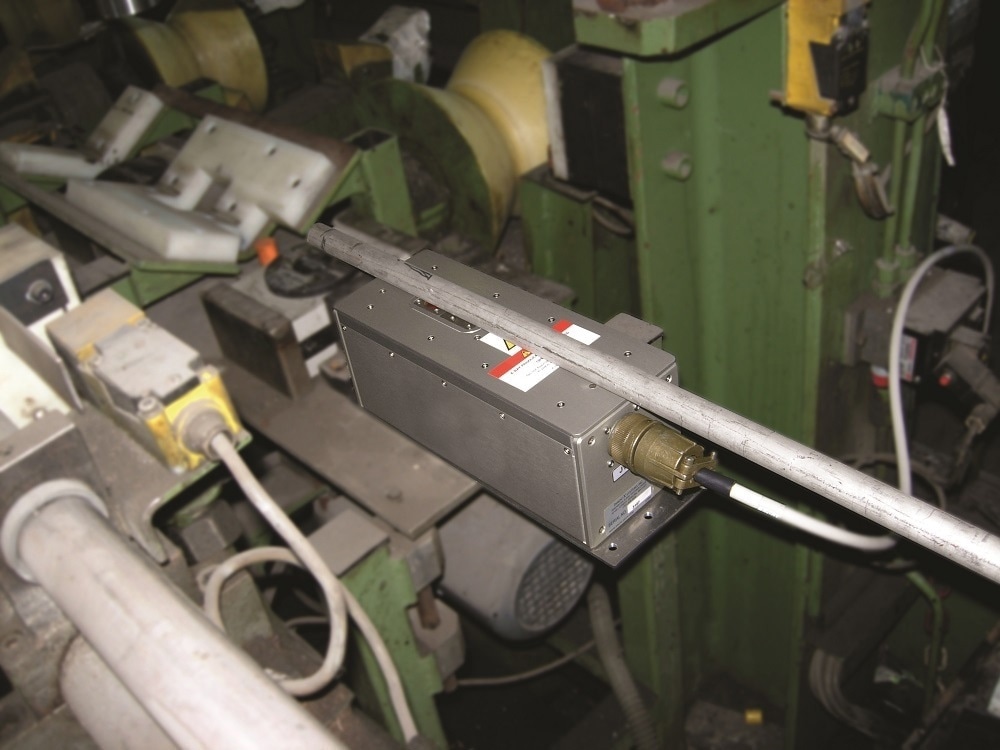
What are the most common applications for the FOX-IQ?
The most common FOX-IQ applications are for tube and rod manufacturing. It can provide automated testing for 6 to 10 samples per minute, or over 3000 tests per shift. The typical cost per test ranges from 1 to 3 cents, depending on the testing volume. Stainless steel tubing, Zr alloys, Ti alloys, low alloy steels and specialty aerospace alloys are all materials that can be analyzed using the FOX-IQ. Some other applications include testing surface coatings and thin film samples, such as precious metal coatings in solar panels, surface coatings for brake discs and material composition of filter paper. The FOX-IQ uses a Fundamental Parameter approach to generate analytical results. Keys to a successful measurement include precise sample delivery to the FOX-IQ analyzer window, sample homogeneity size and shape, and that the near surface (10 to 100 μm) is representative of the bulk sample.
How have you achieved an engineered system capable of running 24/7 operation and why was this important?
The system has been engineered to run 24/7 in an industrial environment. This is important because many of our customers have a 24/7 process. Our design had to account for this. The FOX-IQ probe head is made of high strength aluminum and incorporates a thick Kapton window for durability. It is resistant to vibration and can endure electromagnetic and acoustical noise. From a testing point of view, unlike our handheld where customers may make 200 measurements in one day, customers using the FOX-IQ may take up to 3000 measurements per day. In order to meet that requirement, we made changes to how we operate the tube and filter wheel in the FOX-IQ as opposed to our handheld. In the FOX-IQ, the tube maintained at a constant voltage and the filter wheel position remains fixed. This maximizes both tube and filter wheel life.
Where can our readers learn more?
Readers can visit http://www.olympus-ims.com/en/xrf-xrd/process-on-line-xrf/fox-iq/ to learn more.
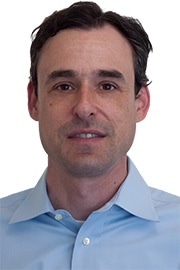
About Shayne Harrel
Shayne Harrel is an Application Development Scientist specializing in XRF for Olympus.
He has been at Olympus for over 3 years. Prior to joining Olympus, he studied analytical and radio chemistry at the US Food and Drug Administration.
Shayne holds a PhD in Physical Chemistry. During his graduate work, he helped pioneer the use of Terahertz emission spectroscopy (TES) to study dynamical processes in charge transfer systems, thin magnetic films and semiconductors.
Disclaimer: The views expressed here are those of the interviewee and do not necessarily represent the views of AZoM.com Limited (T/A) AZoNetwork, the owner and operator of this website. This disclaimer forms part of the Terms and Conditions of use of this website.