Near infrared spectroscopy has been used widely in the polymer industry. Compared to traditional methods such as wet chemistry and chromatographic methods, NIR spectroscopy provides considerable advantages in process and quality control applications through fundamental benefits such as low to no cost of consumables for instance solvents, columns, reagents; real time analysis - generally less than 10 seconds’ measurement time; multiple components per analysis; elimination of sample preparation time; and elimination of many sources of systematic error.
This article will present three FT-NIR polymer applications: 1) at line polyether polyols' hydroxyl value analysis; 2) real time isocyanate number monitoring during a polyurethane reaction; and 3) off-line quality control of percentage styrene in styrene copolymers.
Introduction
Polyurethane polymers are most commonly formed by reacting a di- or poly-isocyanate with a polyol. Both the isocyanates and polyols used to make polyurethanes typically contain two or more functional groups per molecule. Different types of polyols and isocyanates can form different polyurethane products with dissimilar properties and end uses. The hydroxyl value of polyols and the isocyanate number of isocyanates are not only very important QC parameters for incoming raw material but also very important reaction control parameters. Traditional analytical methods for both hydroxyl value and isocyanate number are titration methods, which are very time consuming. Thus they cannot be used for real time process monitoring and adjustment. They also involve environmentally unfriendly solvents and reagents. In contrast, the near infrared (NIR) spectroscopy method is rapid, non-destructive, has no sample preparation, and can be applied to off-line, at line or on-line measurements.
Styrene butadiene copolymers (SBC) and their blends have been used widely in our daily life, e.g. clear disposable drinking cups, wrapping films, and toys. The ratio of styrene/butadiene or the styrene concentration in SBC affects its properties and final use. The styrene concentration in copolymers can be measured by an NMR method or chromatographic method. Although, these methods provide valuable information, they are time consuming and high cost. Compared to those methods, the NIR method is fast and easy to execute. A technician with no knowledge of spectroscopy can perform the analysis.
In this article, the focus is on Fourier transform near infrared (FT-NIR) analysis of hydroxyl value in polyether polyols, isocyanate number during polyurethane reaction and styrene concentration in SBC pellets
Materials and Methods
Materials and Reference Values
Polyether polyol samples were obtained from a manufacturing plant QC lab and analyzed using a titration method.
Polyurethane samples were pulled out of a reaction tank periodically and samples from several batches were collected and analyzed using the traditional titration method.
Pellets of styrene butadiene copolymers (SBC) with different styrene concentrations were obtained from a customer and the reference values for the styrene concentration were obtained using an NMR method.
Sample Measurement
FT-NIR spectra of polyether polyol samples were collected using a QuasIR™ 4500 (Galaxy Scientific, Nashua, NH, USA) (Figure 1.) equipped with temperature controlled sample compartment. Samples were measured in 8mm disposable glass vials at 70°C using a resolution of 8cm-1 and 32 scans.
FT-NIR spectra of polyurethane samples were collected on-line using a QuasIR™ 2000 (Galaxy Scientific, Nashua, NH, USA) (Figure 2.) coupled with a process transmission probe (5mm pathlength) over the range of 4000–10000cm-1 at a resolution of 8cm-1 and 20 scans. The spectra were recorded at regular intervals and named after the recording time.
FT-NIR spectra of SBC pellets were collected using a QuasIR™ 3000 (Galaxy Scientific, Nashua, NH, USA) equipped with a sample spinner accessory. Samples were placed into a 98mm cup with low OH quartz window and then loaded onto the sample spinner, which is mounted off-center on the 2mm sample window of the integrating sphere. This increases the quantity of sample measured and is suitable for inhomogeneous samples. Each sample was measured three times with 8cm-1 resolution and 64 scans. Samples were reloaded between measurements.
Data Processing
Spectral Sage™ software was used for data collection and the Spectral Sage™PLS package was used for calibration development.
.jpg)
Figure 1. Galaxy Scientific QuasIR™4000 Fourier transform infrared spectrometer with temperature controlled (optional) sample compartment and integrating sphere channels.
.jpg)
Figure 2. Galaxy Scientific QuasIR™2000 Fourier transform infrared spectrometer with standard SMA connectors.
.jpg)
Figure 3. Galaxy Scientific QuasIR™3000 Fourier transform infrared spectrometer with integrating sphere and optional sample spinner.
Results and Discussion
Polyether Polyol
Polyether polyol resin samples were gathered at one customer’s QC lab. The hydroxyl values were distributed around two levels, low at around 38mg KOH/g and high around 56mg KOH/g. To avoid any temperature influence on the OH bands all sample spectra were measured at 70°C. Figure 4 shows the vector normalized spectra of polyether polyols. An apparent difference can be observed for high and low OH value samples, at 7000cm-1, the first overtone of O-H stretch.
.jpg)
Figure 4. Normalized FT-NIR spectra of polyether polyol samples.
In total, 55 samples were used to develop the partial least square (PLS) OH value calibration using the Spectral Sage™PLS package. The spectra were preprocessed using first derivative and the calibration was developed using two spectral regions: 4575-5060cm-1 and 6100-9000cm-1. The PLS OH calibration was developed using 3 factors and the accuracy of the calibration expressed as the root-mean-square error of estimation (RMSEE) is about 0.28mg KOH/g (Figure 5).
Leave-one-out cross-validation was used to evaluate the calibration and the accuracy expressed as the root-mean-square error of cross-validation (RMSECV) is about 0.32mg KOH/g (Figure 6).
.jpg)
Figure 5. PLS calibration curve of OH value. R2= 99.91, RMSEE = 0.28 mg KOH/g.
.jpg)
Figure 6. Cross validation result of polyether polyol samples. R2= 99.88, RMSECV = 0.32 mg KOH/g.
Polyurethane
Polyurethane samples were pulled out of the reaction tank and analyzed by a titration method. Five spectra collected around the sampling time were averaged and used to develop the calibration. In total, 81 samples from 10 batches, with remaining isocyanate number in the range of 5.5% to 11.5% were used to develop the partial least square (PLS) calibration model.
Figure 7 presents 5 normalized polyurethane spectra with different isocyanate numbers (NCO). The spectra were vector normalized to remove baseline variation. Apparent spectral variation observed around 7000cm-1 is linked to the first overtone of the O-H stretch. As the reaction progresses more isocyanate and polyols are consumed.
.jpg)
Figure 7. Normalized FT-NIR spectra of polyurethane samples with various remaining NCO concentrations.
.jpg)
Figure 8. Validation result of samples from 3 independent batches. RMSEP = 0.14%.
.jpg)
Figure 9. Normalized FT-NIR spectra of styrene butadiene copolymer samples with various styrene concentrations.
.jpg)
Figure 10. PLS calibration curve of styrene content in SBC pellets. R2= 99.62, RMSEE = 0.25%.
The spectra were vector normalized and the PLS calibration was developed using the spectral range of 4800cm-1 to 9000cm-1. Leave-one-out cross-validation was used to evaluate the calibration. NIR spectra have a high correlation with isocyanate number (R2= 98.36) and the accuracy expressed as root-mean-square error of cross-validation (RMSECV) is about 0.19%.
12 samples from another 3 batches were used as an independent test set to validate the calibration, and the root-mean-square error of prediction is about 0.14% (Figure 8), which is consistent with the RMSECV result.
Styrene Butadiene Copolymer
30 bags of SBC pellets were obtained from a customer with styrene concentration ranging from 65% to 82%. Vector normalized spectra are shown in Figure 6. The shoulder band around 8700cm-1 changes according to styrene concentration. Since only 30 pellet samples were available, all of them were used as calibration samples. The calibration was developed using the spectral range of 6090-9000cm-1, and first derivative and multiplicative scatter correction were used as data pre-processing methods. The resulting FT-NIR spectra show high correlation with styrene content (R2= 99.62), and the accuracy expressed as root-mean-square error of estimation (RMSEE) is about 0.25% (Figure 10).
Leave-one-out cross-validation was used to evaluate the calibration, and the accuracy expressed as root-mean-square error of cross-validation (RMSECV) is about 0.29% (Figure 11).
.jpg)
Figure 11. Cross validation result of SBC pellets. RMSECV = 0.29%.
Conclusion
This study demonstrates that FT-NIR can be used as an at-line, on-line or off-line quality control tool for polymer products. Results can be obtained in seconds, with no need for an experienced operator.
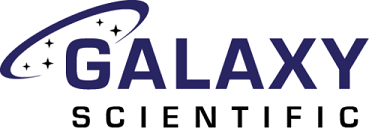
This information has been sourced, reviewed and adapted from materials provided by Galaxy Scientific Inc.
For more information on this source, please visit Galaxy Scientific Inc.