Chrysler's latest concept car (figure 1)might look like your average urban runabout, but even just a cursory tap on the bodywork will tell you that this vehicle is something different. For although the design breaks little new ground, the Composite Concept Vehicle (CCV) is made from radically different materials to the norm, with the body being built almost entirely from plastic. Chrysler hopes the CCV will herald a new generation of lightweight, fully recyclable plastic cars that are cheap to run and extremely fuel efficient. 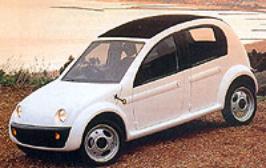 | Figure 1. The Chrysler CCV. | Advances Making the CCV Possible The CCV has been made possible by two key advances: • Continuing development of a breakthrough PET polymer from Ticona, the engineering polymers subsidiary of Hoescht • New advanced moulding technologies that allow large panels such as those needed for vehicle bodies to be produced without warpage. The CCV outer body is constructed from four of the largest mouldings ever used in an automobile. These body panels are adhesively bonded to one another and then to a steel chassis, which strengthens the entire structure and supports the power train and suspension. Design Advantages Chrysler and its team of collaborators has designed the CCV to be most successful in emerging countries. Thanks to reduced manufacturing costs, the vehicle will sell for about US$6000 - half the cost of its competitors. The vehicle is also virtually 100% recyclable - the plastic can be collected at the end of the vehicle's life for reprocessing. Thanks to the new technology developed by the team, the CCV can be assembled in about 6.5 hours, compared to 19 hours for a conventional compact car. The four large body panel mouldings are part of a general design aimed at cutting the number of parts by a quarter. Overall, instead of the 80 steel components that make up a traditional chassis, the CCV only needs six plastic parts. This design should reduce manufacturing costs by as much as 80%, and plant space required for assembly could be only one sixth of that for a conventional vehicle. Weight and Strength The plastic body of the CCV also helps keep the vehicle light. It has a 1200lb curb weight, which is approximately 50% lighter than a steel equivalent. The four body panels by themselves weigh just 2101bs in total, saving more than 400lbs compared to a metal body. Despite this reduced weight, the CCV is safe and strong. Its performance in cyclic load tests exceeded expectations - the body panels were expected to survive 1800 cycles, equivalent to 100,000 road miles at full vehicle weight. The test body passed 3600 cycles without significant failures. `[We have] proved that the big panels could be moulded and that a car body made of the right thermoplastic resin can perform safely after years of rigorous testing,' says Bernard Robinson, Chrysler's vice president of engineering technologies. Material Choices The CCV's balance of physical properties and good performance in road simulations partly stems from the use of Ticona's Impet PET resin, which was specially developed for the vehicle. The resin gives good impact strength, ductility, dimensional stability and mouldability that the company says has never been achieved before in a thermoplastic. Conventional PET resins have limited impact strength and fracture into many pieces upon impact. In comparison, Ticona's patent-pending material has triple the impact strength and benign failure modes. Material Developments The resin underwent six phases of development over a period of 18 months. The first three phases added the essential elements of ductility and impact resistance to the starting PET material without reducing its strength and dimensional stability. The final three stages then addressed mouldability and retention of properties - which is difficult because the resin spends a very long time in the melt stage during the moulding process. ‘Because of the weight of the parts and the shot size, the resin must be held in the melt stage for more than half an hour, yet retain its end-use mechanical properties,’ says Tom Sinner, Ticona Project Engineer on the moulding team. ‘At the same time it [must not] discolour. Given the requirements for end-use ductility, mechanical properties and dimensional stability, that is an unprecedented challenge for a PET resin.’ The resulting Impet material is a 15% glass-filled, impact-modified PET resin with good processability and surface appearance. ‘Total additive loading is not any higher than in other PET formulations, but the total number of different additives certainly is higher,’ says Sinner. ‘That number could well increase this year, as we start to explore additional colours.’ All the cars produced so far are off-white, and the main focus for further development is to produce body parts in a variety of moulded colours, and also to improve processing consistency. ‘It is a matter of learning to make consistent parts in a production setting,’ says Steve Leyrer, Ticona Programme Director. Material Cost The low price of the CCV - which Chrysler intends to be an ‘affordable world car’ - is partly thanks to the resin, which is less expensive than composites used in other car bodies. It costs just $1.50 per pound compared to carbon fibre at $10 per pound, SMC at $5 per pound and SRIM at $6 per pound. Ticona is building on the success of this specially-produced resin, developing a new product line called Impet Hi. The first material, Impet Hi 430, was introduced at SAE 1998. It has the same easy moulding properties as the CCV resin, and a notched impact strength 40% greater than that of comparable glass reinforced PET. It is also far tougher than ordinary polyesters. Some properties are shown in table 1. Table 1. Properties of Impet Hi 430 compared to a conventional 15% glass-filled PET material. | Impact Strength (kJ.m-2) | 18 | 5.0 | Tensile Strength (MN.m-2) | 73 | 100 | Flexural Modulus (MN.m-2) | 4200 | 5200 | Moulding Developments in moulding technology are key to the production of the CCV, as well as Ticona's new resin. The moulded panels, which are three times bigger than any plastic moulding used in a production automobile, are produced accurately enough to meet automotive body-fit standards. Two 70lb inner shells and two 351b outer shells make up the finished car body (figure 2). They are moulded in a three minute moulding cycle with a 10-15 second fill time - extremely short for such a large shot. To achieve proper filling, Sinner worked with Cascade Engineering and the mould makers to develop very large gates. A moulding sequence to vary the wall thickness of the finished part was also developed. ‘The variations of wall thickness in the finished part are there to ensure proper mould filling, to reduce distortion and for end-use structural strength,’ says Fred Keller, President of Cascade. 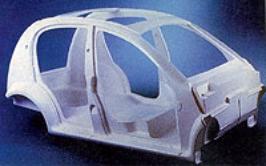 | Figure 2. The four section polymer body of the Chrysler CCV. | Component Distortion Controlling distortion well enough to meet car body fit-check standards was key in producing such large mouldings. ‘Much of the processability stems for the resin itself, which is quite remarkable,’ says Keller. ‘Beyond that, from a mould-fill standpoint, we treated a single large part as several smaller parts, each with its own melt-flow and material distribution requirements.' Component Tolerances The team particularly focused its design efforts to maintain the closest tolerances in the door opening and mating surfaces, where accuracy matters most. ‘We capitalised on latitude available in the non-mating areas to make sure the parts fit together where they meet and that the door openings are exactly right,’ says Sinner. This strategy is borrowed from forming and assembly of steel body panels. The Next Stages of Development With the concept proven by the development of the CCV, the outlook is bright for plastic cars. ‘Our next task will be to identify what has made the CCV prototypes work so well so far, and to scale up to production status,’ says Leyrer. ‘It will require identifying every parameter in the moulding of a large part that affects the consistency of dimensions and material properties.’ Further resin development work will be key to the process. This will involve optimising the moulding process and determining how wide the moulding window can be while ensuring consistency and producing high quality parts. Leyrer’s team will also explore the possibilities of moulded-in colour, and develop an understanding of the tolerances associated with large parts for high volume assembly and finished body fit. Project Success ‘The balance of properties and economies we have achieved has obvious appeal in a variety of automotive parts of all sizes,’ says Leyrer. ‘We know an entire body can be made of PET and can survive in service - it has been done at the prototyping stage. We also know the body performs in service. The proof is in the crash and road test results to date. ‘Several test cars have been made that can successfully navigate the rutted back roads in places like Africa and Brazil,’ Keller adds. ‘End use performance aside, the CCV project provides 210 pounds per car of new proof that you can mould large automotive body parts to close tolerances with an affordable resin. It can provide automotive manufacturers with a solution for dramatically simplifying production and taking cost and weight out of their mainstream vehicles.’ The Future The team is bullish about its achievements. Regardless of how the CCV itself fares in world markets, the project has provided a thermoplastic and a technology for metal replacement in the large, functional components in automobiles. Two other vehicle studies are already underway with an Impet PET body. The Chrysler Dodge ESX2 car, figure 3, is using a PET body reinforced with aluminium structural parts. The other Chrysler prototype is the Plymouth Pronto Spyder, figure 4. The body is again made from the same material as the CCV - although the stylish two-seater design is pitching plastic cars into entirely new markets. 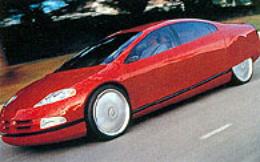 | Figure 3. The Dodge ESX2, built with Impet Hi, reinforced with aluminium structural parts. | 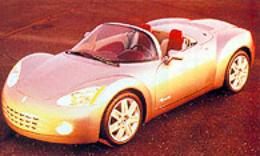 | Figure 4. The Plymouth Pronto Spyder, also featuring a Impet Hi polymer body. | |